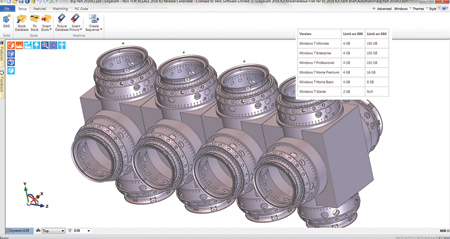
Edgecam 2016 R2
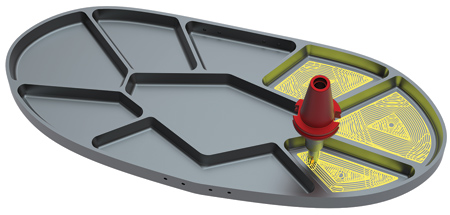
Surfcam Waveform Roughing
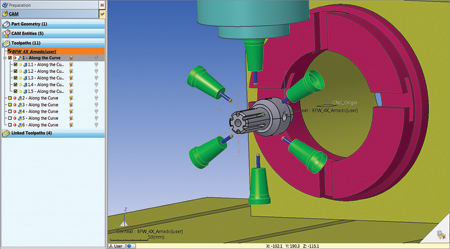
WorkNC
Vero Software will feature Edgecam 2016 R2, Surfcam and WorkNC at IMTS.
Edgecam
With the release of Edgecam 2016 R2, the software is now a 64-bit application that offers increased access to memory, which improves overall efficiency, especially when working with large files. The program is now able to load solid models up to 20x faster than the previous version.
Among the software's time-saving capabilities is the Waveform roughing strategy, a high-speed machining cycle that is available for milling and turning and delivers consistent tool engagement with the material, thereby maintaining constant tool cutting load. "By generating a smooth tool path to avoid sharp changes in direction, Edgecam Waveform maintains machine tool velocity while decreasing cycle time and increasing tool life," said a company spokesperson.
Edgecam's Rough Turn cycle now features a new Ramp Cut strategy, which is typically used for turning deep recesses with double-sided turning inserts, and extends tool life because the contact point on the insert is constantly changing, avoiding notching. The new strategy can be used with decreasing cut increments.
The latest version of Edgecam also offers extended collision detection and improved NC output for machining holes. Working in unison with the Update Fixture command, the Hole Cycle avoids collisions with fixtures by using clearance and retract values parameters.
Surfcam
The Surfcam CAM solution, by Vero Software, will also be presented. Surfcam Workflow offers a programming strategy designed to lower manufacturing costs, improve part quality and shorten lead times. Workflow understands the component topology and the required manufacturing environment, thereby accelerating tool path generation.
Available for both milling and turning operations, Workflow lowers programming time and, because it is simple to operate, the learning curve for new users is reduced. "Unlike many CAM systems for which the user must manually set the machining environment and use traditional commands to create data, Workflow automatically detects the machining environment and creates an interactively movable origin based on the user's preferences," said the spokesperson.
Also available in Surfcam is the Waveform Roughing strategy, a high-speed machining technique that maintains a constant tool cutting load by ensuring the tool engagement into the material is consistent. The tool path moves in a smooth path to avoid sharp changes in direction, which maintains the machine tool's velocity.
Waveform Roughing improves on standard roughing by ensuring a constant volume of material is removed. In addition, this opens up the way for use of high-speed machining, particularly for harder materials. Using as much of the flute length as possible distributes wear evenly along the entire cutting length, rather than just the tip. The radial cut depth is reduced to help ensure consistent cutting force, allowing cut material to escape from the flutes. Tool life is extended, since most of the heat is removed in the chip.
WorkNC
In addition to improvements to the user interface and collision-free machining, WorkNC now offers Waveform technology, which is designed to cut down on cycle time while extending tool life.
The Waveform strategy entails maintaining a constant load on the cutting tool by machining from the stock material towards the part geometry. This approach results in a reduced number of intermittent cutting movements, especially in the outer areas, meaning the tool stays engaged in the material for as long as possible and leads to fewer retracts and air-cutting periods.
"The stepover distance automatically adjusts in order to maintain a constant load on the cutter over the complete toolpath trajectory, making it possible to maintain optimal feedrates during the whole cycle, which can attain rates of up to five times faster than a traditional roughing strategy," said the spokesperson. Machining is performed over the full cutting length of the tool whenever possible, which distributes load evenly.
Additional improvements to WorkNC include the availability of its Auto 5 functionality as a standard module. With Auto 5, users can automatically generate 5-axis toolpaths using existing 3-axis or 3+2-axis toolpaths, while also taking into consideration the kinematics of the selected 5-axis machine. The intelligent toolpath is dynamically and automatically checked in order to avoid collisions and manage the linear and rotational limits of the machine.
Auto 5 technology allows the use of shorter, more rigid cutters, allowing most of the part to be finished in a single operation.
For more information contact:
Vero USA Inc.
2000 Town Center
Suite 1730
Southfield, MI 48075
248-351-9300
info@verosoftware.com
www.verosoftware.com
IMTS Booth E-3114