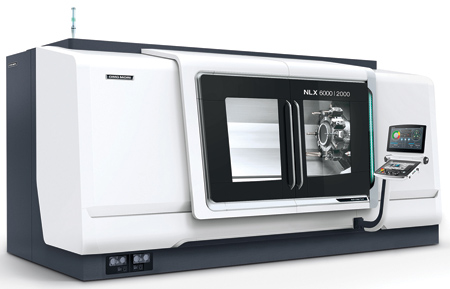
NLX 6000|2000
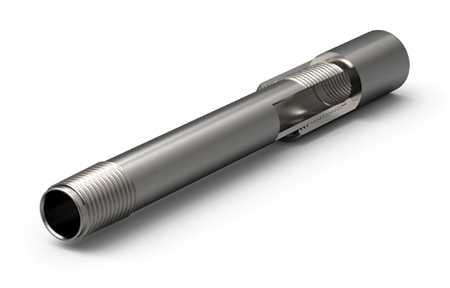
The oil drill pipe measuring o300 x 1,800 mm is made of stainless steel and is completely machined in approx. 2 h 30 min.
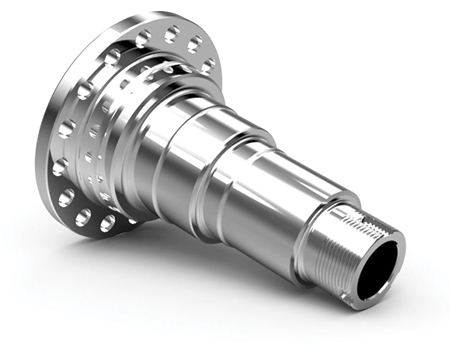
The flange used in shipbuilding (material: SCM440) takes approx. 1 h 30 min to machine.
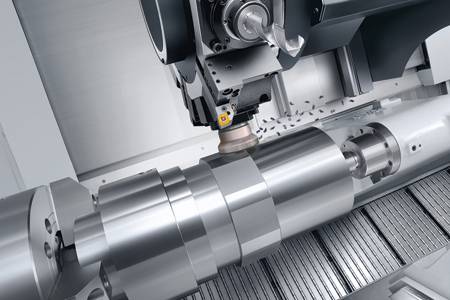
The NLX 6000|2000 offers stable process conditions due to its 180 mm wide flat guides.
DMG MORI has introduced the NLX 6000|2000 featuring Big Bore spindles of up to 12,000 Nm and o375 mm. Designed for energy technology, the oil industry and hydraulics and mechanical engineering, it offers a turning length of 2,000 mm, a Y-axis option with +/- 100 mm stroke, individual spindle variations, an optional BMT turret for demanding milling operations and the CELOS user interface.
The NLX 6000|2000 has a 45° slanted bed with flat guides of up to 180 mm in width in all axes for enhanced damping properties and dynamic rigidity. Ball screws with a diameter of 50 mm, a headstock with integrated motor spindle and a built-in tailstock provide additional stability during machining. With a maximum turning diameter of 920 mm and a turning length of up to 2,000 mm, this largest model in the NLX series is designed for turning applications reaching into the XXL range. It features XYZ travels of 485 mm x 200 mm (± 100 mm) x 2,150 mm. The maximum chuck size is 600 mm.
Like the work area, the available spindle bores are also largely dimensioned. The offer includes o185 mm (type B), o285 mm (type C) and o375 mm (type D). The Big Bore spindles achieve torques of around 7,000 Nm in the case of type B and up to 12,000 Nm for the two larger versions. The turret features an integrated drive motor with BMT technology and has a maximum speed of 4,000 RPM and a torque of 117 Nm. There is space for 12 powered tools.
The powder-coated housing is scratch-resistance to provide a higher service life. The door handles have been designed ergonomically and the view into the work area optimized. The clearly arranged 21.5" control panel with touchscreen and touch panel includes the future-orientated user interface CELOS with MAPPS V.
The new user interface, with its six window displays, provides access to a variety of information simultaneously. Features include a Tool Management System (TMS) for displaying all required tool information, Visual Programming System (VPS) that combines the input of the G- and M-code and predefined cycles that simulate the machining operation, as well as a 3-D interference check for automatic collision control that includes the spindles, workpieces, tool and clamping devices. Automatic inclusion of already machined areas to enable shorter travel paths also reduces machining times.
For more information contact:
DMG MORI - Americas Headquarters
2400 Huntington Blvd.
Hoffman Estates, IL 60192
847-593-5400
Service Hotline:
855-DMG-MORI (364-6674)
www.us.dmgmori.com