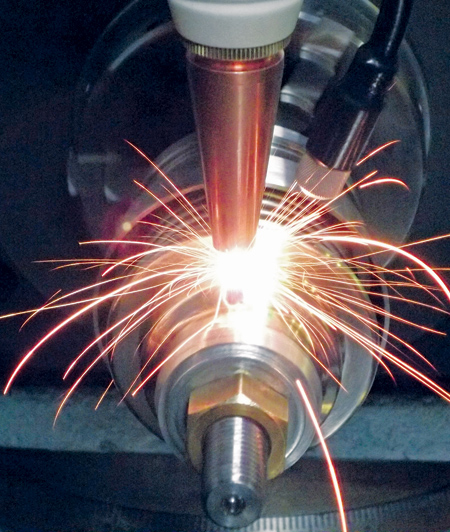
Welding nickel-based aerospace alloys is accomplished following guidelines established by Laserdyne applications engineers.
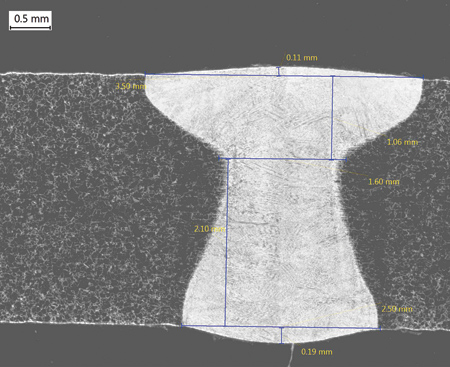
Hastelloy X, 3.2 mm thick, shows the desirable crown (convexity) of the weld
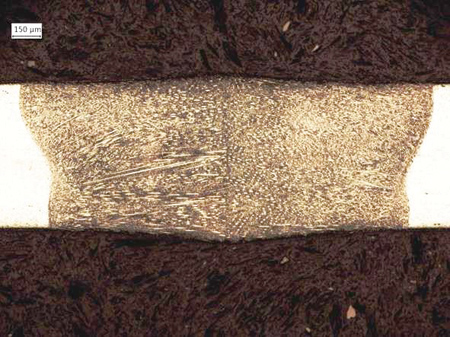
Inconel 625, 0.8 mm thick, shows the ability to control weld dimensions on both the top and bottom sides of the weld.
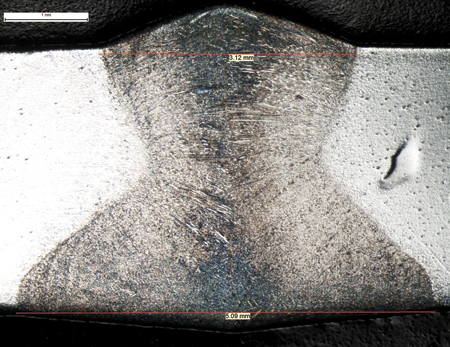
Inconel 625, 3.2 mm thick
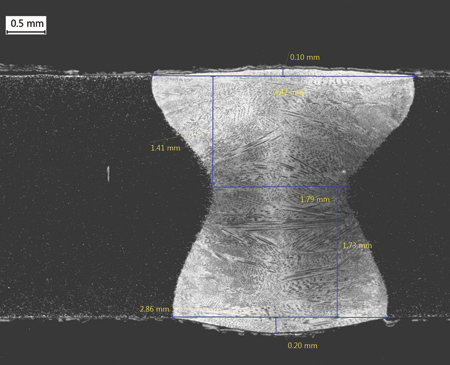
Haynes 230, 3.2 mm thick
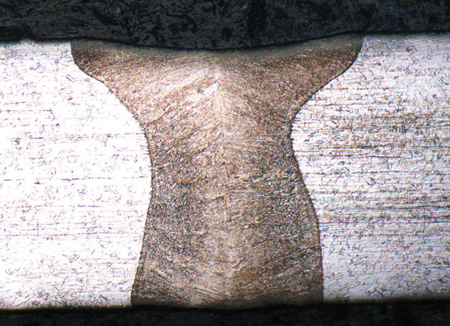
Laser welding with conventional end point ramp-down, gives excessive undercutting of the top bead.
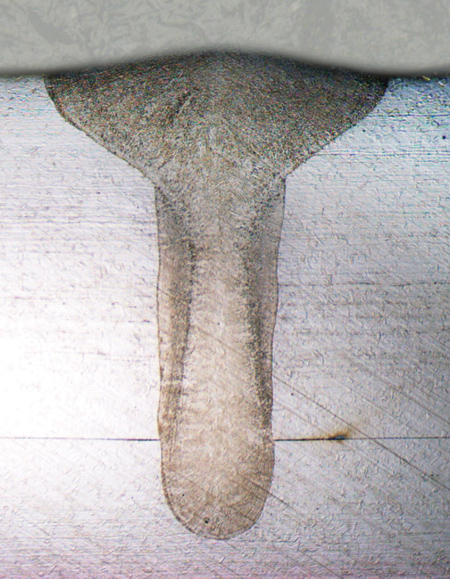
End point control with SmartRamp avoids top bead undercutting.
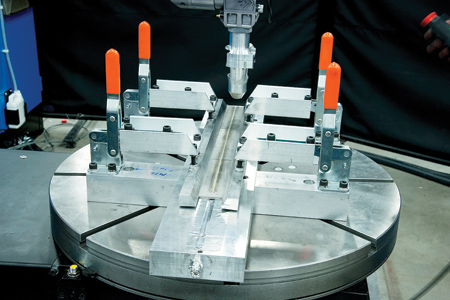
Laser welding fixture for butt and overlap welding of nickel-based plate and sheet for aerospace applications.
High quality butt and lap joint welds are possible and practical in a number of common nickel-based aerospace alloys, as established by Prima Power Laserdyne application engineers. These applications meet the exacting requirements of aerospace, both for airframe as well as for aero-engine applications.
Examples show the desirable crown (convexity) of the weld. Each example shows the ability to control weld dimensions on both the top and bottom sides of the weld with or without filler metal with no observable porosity within the weld fusion zone.
Using Prima Power Laserdyne's exclusive SmartRamp that makes use of LASERDYNE S94P exclusive laser and motion control, this desired profile is maintained even at the end of closed welds.
Integrated laser and motion control with the LASERDYNE S94P laser process control enables production of crack-free welds through use of laser process parameters that take into account the relatively large solidification temperature range of nickel base aerospace alloys and the fact that brittle phases can form when solidification rates are low.
Joint Cleaning Prior to Welding Nickel-Based Aerospace Alloys
It is necessary that weld contaminants be removed by thorough cleaning prior to welding. At high temperatures, nickel alloys are susceptible to embrittlement from sulfur, phosphorus, lead and other low-melting point substances that are often present in materials used in everyday manufacturing processes. For example, grease, oil, paint, cutting fluids, marking crayons and inks, processing chemicals, machine lubricants and temperature-indicating sticks, pellets and lacquers may be found on materials to be welded.
Oxides are especially harmful to the welding process. Those oxides visible on the surface of materials to be welded melt at temperatures significantly higher than the base metal. This causes weld porosity, lack of fusion and other weld defects.
To ensure a successful welding process, a good cleaning of the joints will help ensure a successful and strong weld joint.
Correct Fixturing to Control Thermal Expansion
The thermal expansion characteristics of nickel-based aerospace alloys are similar to those of carbon steel. When welding, the forces and distortion generated by both materials are similar and require component restraint by a properly designed holding fixture. The restraint provided by a properly designed fixture can be used to control stresses in the weld. For example, if an appropriate clamping force is used to restrain the material near the weld joint, the expansion created in the weld joint will lead to a compressive force in the weld. This compressive force will in turn lead to upsetting of the weld metal and corresponding reinforcement, or crown, of the top and bottom of the weld, even without filler metal.
In addition to proper clamping, the fixture must also provide proper shielding of the top and back sides of the weld. Shield gas is provided to the top of the weld using Laserdyne's SmartShield welding nozzle. Shield gas is provided to the back-side of the weld through a special groove in the fixture beneath the weld.
"In summary, the use of Laserdyne's SmartTechniques for laser welding together with proper joint cleaning and component fixturing produces successful welds of nickel-based aerospace alloys," said the spokesperson.
For more information contact:
Prima Power Laserdyne
8600 109th Ave. North, #400
Champlin, MN 55316
763-433-3700
lds.sales@primapower.com
www.primapower.com