
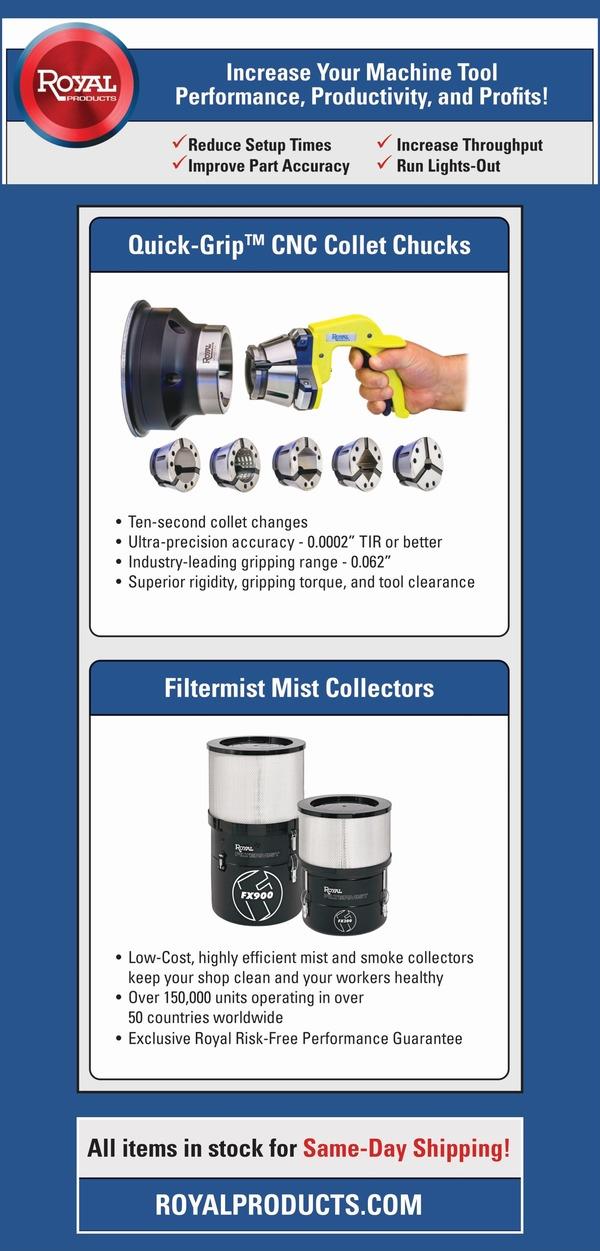
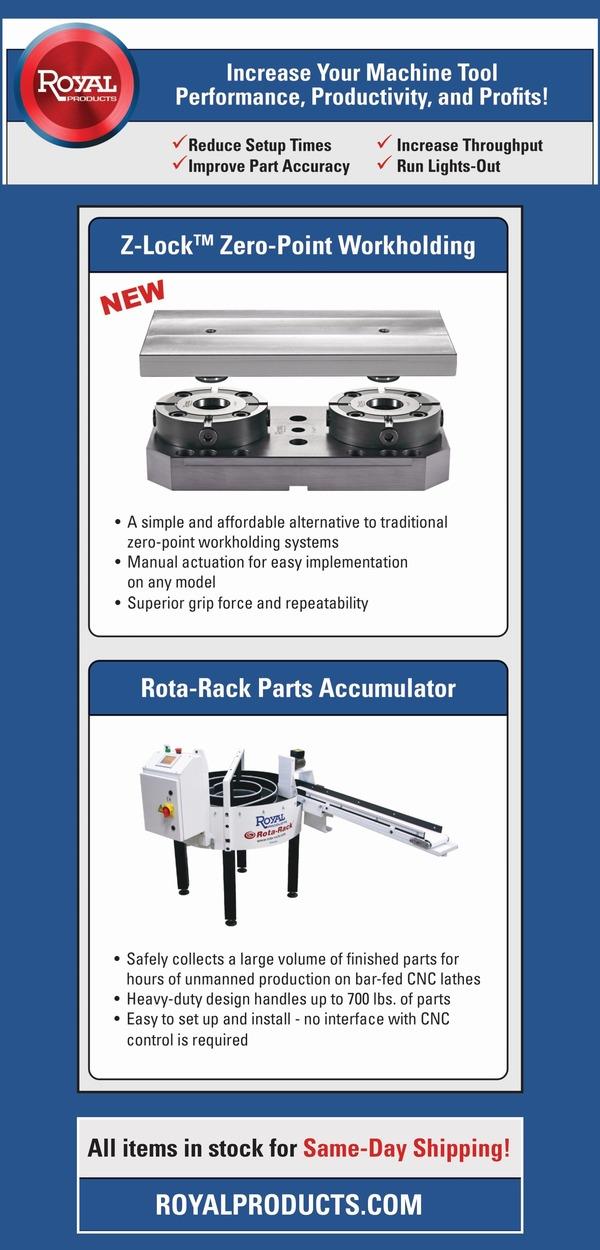

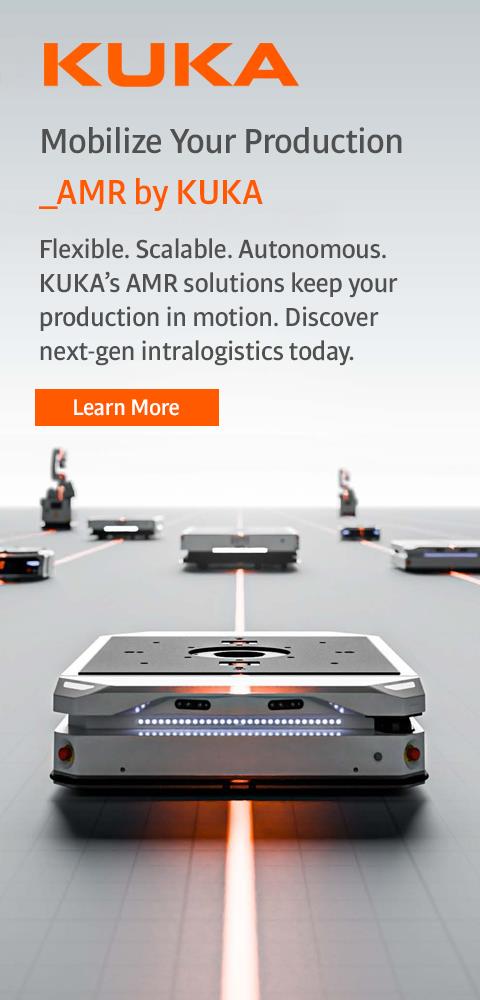
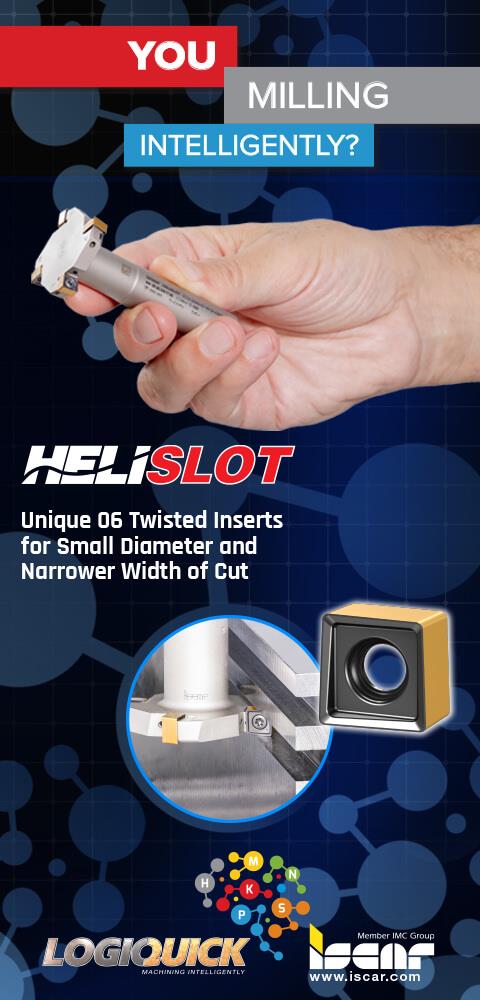
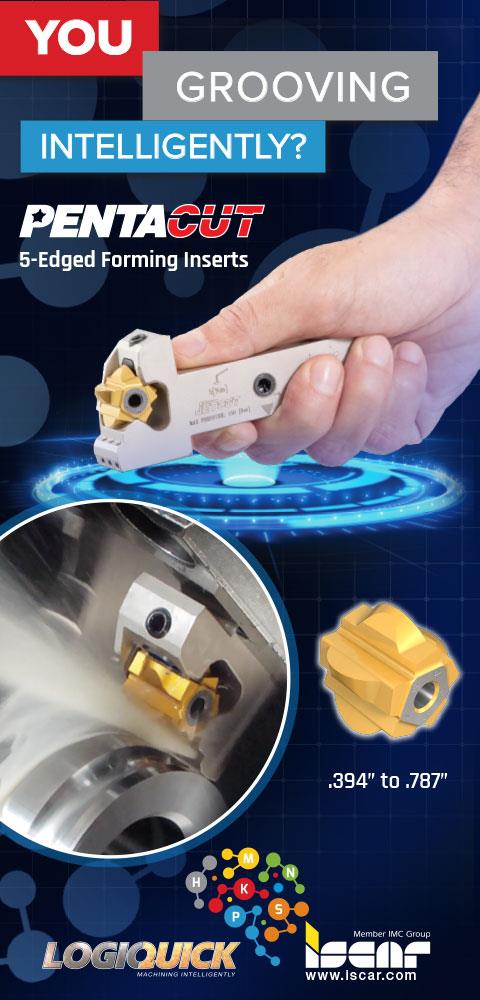
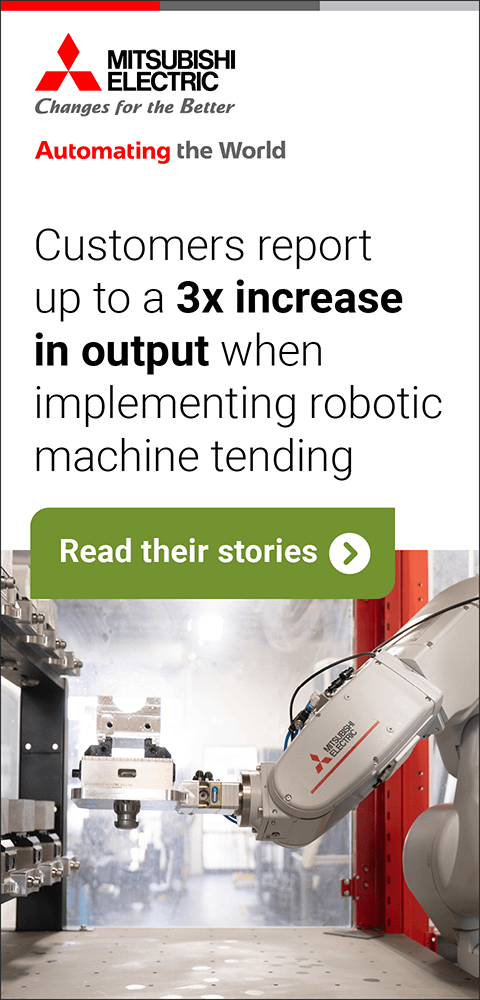
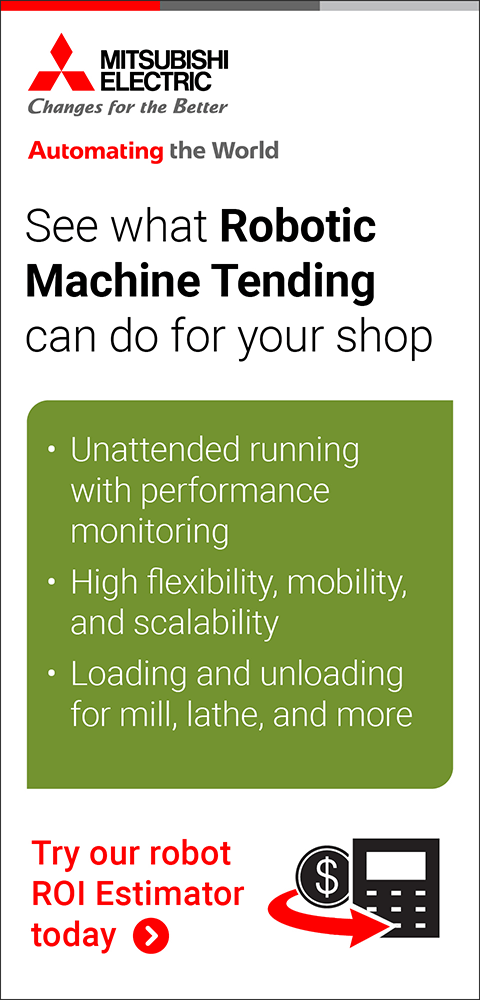
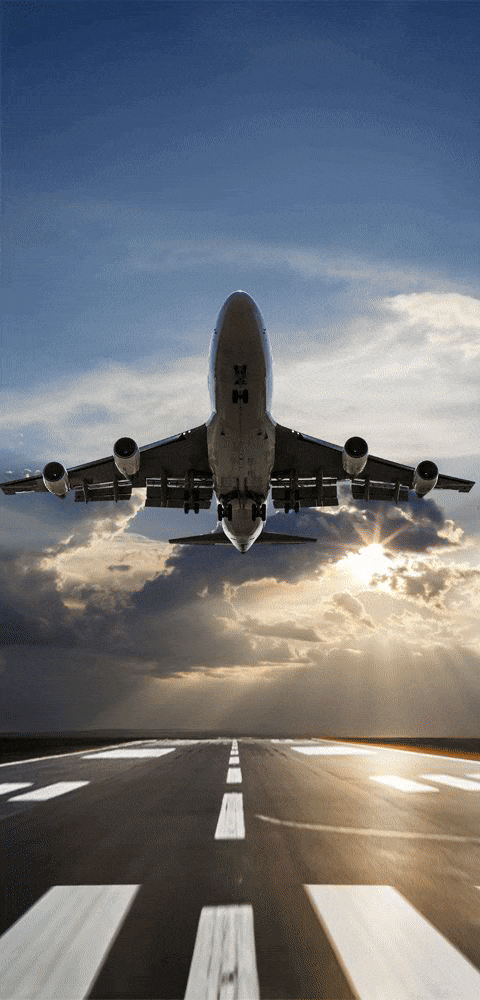
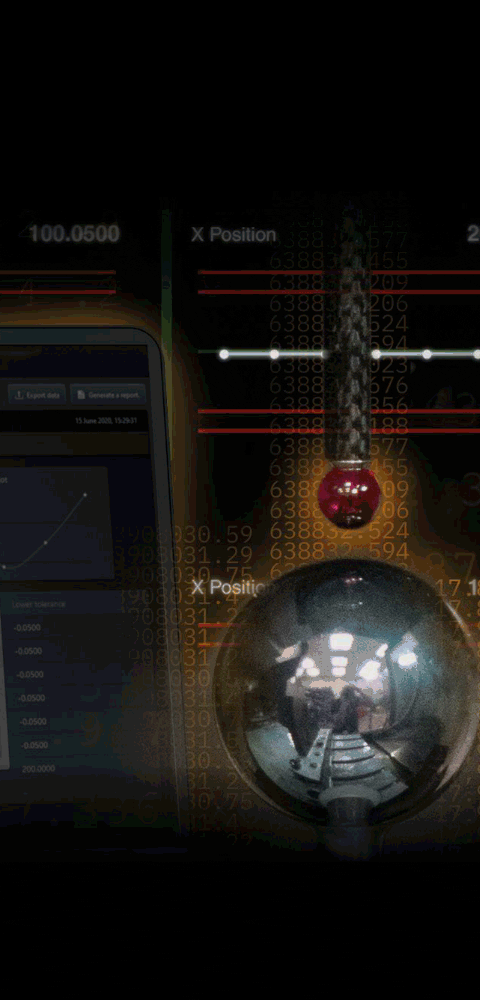
New Concepts in 5-Axis Blisk Machining
September 1, 2016
Autodesk and UK based cutting tool specialist Technicut have jointly developed new tooling concepts and toolpath strategies for machining blisks (bladed disks). Manufactured from titanium and nickel, these highly complex and critical components are becoming more common due to the advantages of weight, efficiency and through-life servicing.
This patent-pending process, which combines innovative tooling solutions and application strategies for the roughing, semi-finish and finish machining of all integrally bladed rotors, has provided a 51% time reduction to machine a blisk from start to finish.
"Through our Productivity Solutions, we are able to demonstrate significant reductions in machining cycle times and total production costs for either current or planned components, and deliver both optimized `mini-turnkey' and `green-button' packages for their complete manufacture," said a spokesperson.
The blisk machining strategies utilize Autodesk's PowerMill blade, blisk and impellor module. Technicut's optimized titanium roughing solutions use X-TREME shanks in combination with Nikken Kosakusho's X-TREME milling chuck for enhanced workpiece security. Features include:
- Heavy-duty cutting capability
- Accurate clamping technology
- Zero tool pull out and tool micro-creeping elimination
- No damages to workpiece or machine
"Our focus is to continually enhance our customers' competitiveness through the supply of optimized tooling and application methodologies," said the spokesperson.
Productivity solutions include:
For more information contact:
Mary Shaw
Autodesk
877-335-2261
mary.shaw@autodesk.com
www.autodesk.com/make
IMTS 2016 Booth E-3222
Technicut
www.technicut.ltd.uk
< back