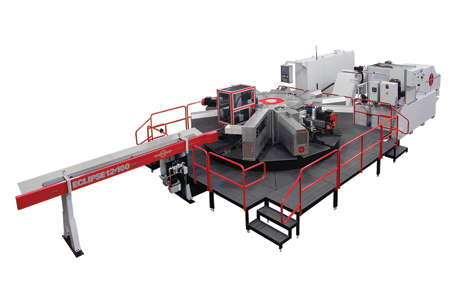
Hydromat Inc. will present the new Eclipse 12-100, a unique 12-station rotary transfer machine.
Hydromat Inc. will present the new Eclipse 12-100, a unique 12-station rotary transfer machine. The Eclipse is a ground up re-design of the Hydromat concept with all new components. The machine has a heavy casting mounted on a frame of sturdy, welded steel construction. The machine casting is 2 m in diameter, nearly twice as large as the traditional 12-station Hydromat machine. This new ductile iron casting is designed for the use of semi-permanent tool spindles, each having 3-axis capability as standard; eliminating the need to change tool spindle sizes for different cutting processes or adding 3-axis flanges for that capability. The new Eclipse features all electric servo spindles and slides. No hydraulics are needed for tool spindle motion as in previous Hydromat machines. These new technologies along with the beefier base yield better accuracy and repeatability.
The bar fed collet version of the Eclipse 12-100 has a maximum workpiece diameter of 65 mm (2.5") and features a maximum workpiece length of 180 mm (7") with 127 mm (5") of material outside the collet. The Eclipse will also be available in an indexing chuck version that will feature a table with vertical chucks capable of 360° rotation of the workpiece. This system is suitable for mid- to high-volume precision production of irregular-shaped castings or forgings and is designed with the flexibility to easily accommodate families of parts. The Eclipse indexing chuck machine will utilize hydraulically-actuated, self-centering two- or three-jaw chucks or custom clamp fixtures, to provide high accuracy and part clamping rigidity. Workpieces are mounted in the chucks by robotics or pneumatic loaders.
A new cut-off saw was designed by Hydromat Inc. engineers at its headquarters in St. Louis, MI. It features bar and workpiece spacing prior to saw blade retraction after the cut, moving both the saw blade away from the workpiece in the collet and the bar stock away from the blade, to eliminate the blade dragging during the saw's return to home position. A two-speed drive motor with belt reduction yields a highly accurate cut.
The saw utilizes standard size 360 mm diameter carbide brazed saw blades. The blades are flanked by replaceable guide supporting pads to dampen blade harmonics. A high pressure flush to clean the blade gullets of chips is standard.
A new CNC head, also designed by Hydromat, features an outside diameter of 160 mm with a radial stroke of 25 mm. The Eclipse features quick-change, presettable tool heads for easy changeovers.
The tool spindles are larger than previous Hydromat spindles to accommodate the heavier cuts and larger parts machined with this platform. They are designated as 55/200 units, referring to the 55 mm front bearing size and a 200 mm stroke at the Z-axis. The units utilize HSK 50 toolholders, and they are a stout design weighing in at 536 kg total mass. These units are direct drive powered by a FANUC ailT6/12000 HV motor with a KTR GS38 coupler. This motor continuous rating is 5.5 kW at 7.4 HP and a 30-minute rating at 7.5 kW at 10 HP. It has dual windings and offers 35 Nm at low speeds and 13.2 Nm at high speeds. The high resolution encoders and the latest servo and spindle HRV Control realize Nano Control Servo system with high speed, high precision and high efficiency. The ai series motors are best suited to large size machine tools because it has high power up to high speed, and has high torque at low speed, well suited to the milling axis of large machines and large lathes.
An optional 20,000 RPM tool spindle powered by the same FANUC aiIT2/20000 is also available. It features a proportionally lower cutting force related to the higher speed. The bearing configuration is the same as the 12,000 RPM version, but features a KTR GS28 coupler on this configuration. Both the 12,000 and 20,000 RPM Eclipse units are through spindle coolant capable.
The Eclipse 12-100 machine is the solution for the elimination of secondary operations by producing parts complete from barstock, castings, forgings or cold formed blanks. The new Eclipse machining platform eliminates secondary operations and reduces work in progress. Additional cost reduction occurs due to short remnants and thin cutoff for material saving.
This multi-station transfer technology enables load and unload processes on station one, and simultaneous machining on the other 11 stations, making the Eclipse suitable for medium to high production of complex workpieces requiring multiple operations, complex cuts and where tight tolerances are critical. The Hydromat Eclipse engineering team works closely with the customer to develop an innovative production solution.
For more information contact:
Kevin Shults
Hydromat, Inc.
11600 Adie Road
St. Louis, MO 63043
314-432-4644
kshults@hydromat.com
www.hydromat.com0
IMTS 2018 Level 3, Booth S-338348