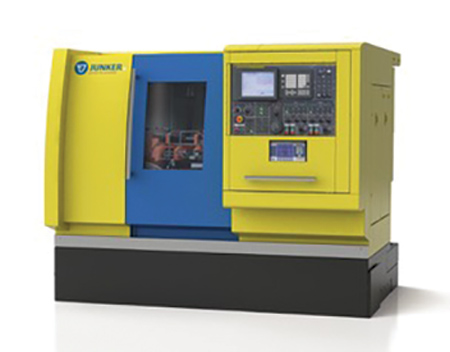
When manufacturing small components with a diameter of between 2 and 20 mm, the Grindstar grinding machine from Junker offers an economical alternative to turning.
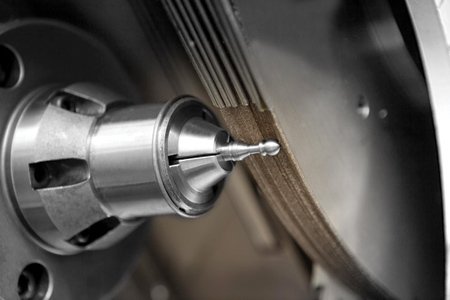
All work steps take place on one machine in a single clamping set-up. This enhances process reliability and minimizes machine downtime.
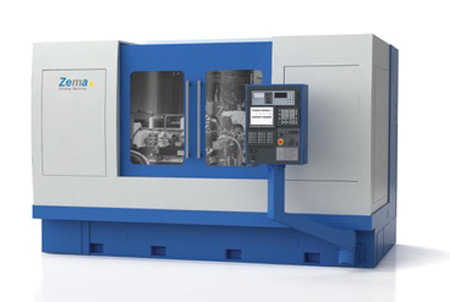
With its new Zema corundum grinding machines, JUNKER is now also offering efficient solutions for conventional grinding.
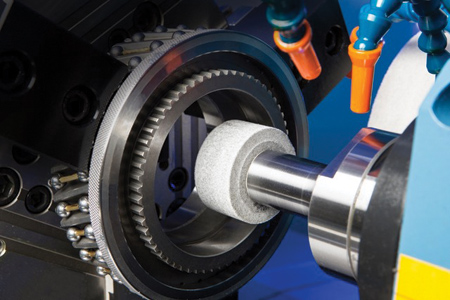
The corundum grinding machine Flexa solves up to three grinding assignments with precision: internal and external grinding as well as thread grinding.
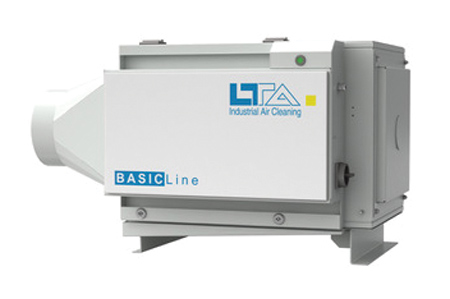
LTA-BASIC Line
The JUNKER Group will present grinding machines from JUNKER and ZEMA together with the latest in air filtration technology from LTA. As a complete supplier in the grinding sector, the JUNKER Group offers turn-key solutions to suit the customers' needs, from individual machines to complete production lines.
"We developed and relaunched the GRINDSTAR and NUMERIKA machine for the North American market," said a company spokesperson. "Customers and their processes benefit from our experience, advice and technology. We respond flexibly to specifications and optimize solutions until we have fulfilled requirements. The advantages for our customers are clear, we adapt our machines to suit customers' needs because we are willing and able to do so. This means that ultimately almost every machine tool is tailor-made."
Replace Turning with Grinding
Booth visitors can experience live grinding demonstrations daily on the GRINDSTAR. "The GRINDSTAR machine concept replaces turning through the use of dressing-free high-speed plunge-cut grinding. This can open up enormous potential for savings, in particular when working with large production volumes. The GRINDSTAR is an economical alternative to turning for any difficult-to-machine workpiece in high volume and complex outer contours," said a company spokesperson.
Highlights of the GRINDSTAR include:
- Minimal piece costs as a result of:
- Shorter manufacturing time due to contour plunge grinding
- Long grinding wheel life leading to minimal tooling cost
- Higher precision
- High process reliability
- Simultaneous grinding of entire part contour including ends
- Reduced downtimes
- Customer-specific process and technology configuration
- Grinding of difficult-to-machine, hard and soft materials possible
- Low-manned, 24/7 lights out production cost benefits due to grinding directly from bar stock
- No burrs and enhanced cut off face.
Cylindrical Grinding with the ZEMA NUMERIKA GH 1000
"Versatile, rugged, long-life - the cylindrical grinding machines of the Numerika series meet any requirements for the series production of a broad range of workpieces; in the largest version up to a length of 3.7 m," said the spokesperson. A torsion-resistant machine bed, hydrostatic guides and grinding spindles mounted on rolling or hydrostatic bearings provide for enhanced grinding results. The user-friendly control system offers all required input screens for grinding with corundum.
Highlights of the ZEMA NUMERIKA platforms:
- Hydrostatic guideways and spindles
- Workpieces ranging from small fuel injection components to 3.7 m long shafts
- In-process and/or post-process measurement.
Filtration Technology by LTA
Filtration solution specialist LTA will be presenting its compact oil and emulsion mist filter BASIC line.
Highlights of the BASIC line:
- Effective suction capacity: up to 1,200 cubic meter/hour
- Can be mounted directly to the machine
- Low energy requirement due to the use of fans in compliance with the ERP Directive.
In addition, LTA will be showing its oil and emulsion mist filter AC 2000 Solid, characterized by its service life and low-maintenance requirements.
Highlights of the AC 2000 solid:
- Solid matter filter with high filtration efficiency
- Effective suction capacity: up to 2,500 cubic meter/hour (capable of modular upgrading to 10,000 cubic meter/hour)
- Low-maintenance solution.
For more information contact:
Erwin Junker Machinery, Inc.
2541 Technology Drive, #410
Elgin, IL 60124
847-488-0406
sales@junker-usa.com
www.junker-usa.com
IMTS 2018 Level 3, Booth N-236839