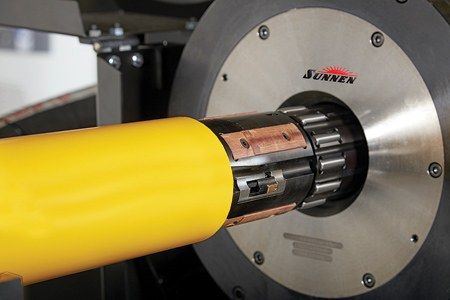
The new Sunnen SHD series bore-sizing machine incorporates the BTA Heller skiving and roller burnishing tooling.
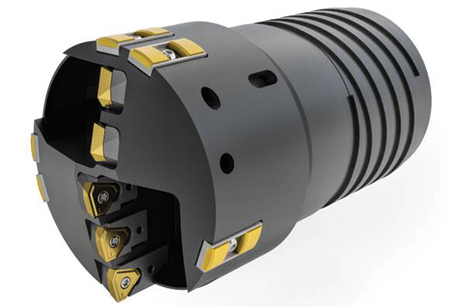
Sunnen/BTA Heller offers an indexable, adjustable drill head, the Hellerdex, for use in BTA-style deep hole drilling.
Sunnen Products Company's acquisition of BTA Heller Incorporated has created a unique solution for shops looking for complete bore drilling-to-finishing capabilities. Sunnen adds BTA's deep hole tooling and systems for primary hole generation as the companies build on natural synergies to offer single-source bore creation and finishing solutions. These new solutions will be on display at the Sunnen Products Company and BTA Heller booths.
Sunnen's core technical competencies include automated and manual honing systems, custom system development and integration, abrasives, tooling, cutting fluids and gauging. The acquisition expands Sunnen's honing expertise to include tooling for initial hole creation and other complementary bore sizing and finishing processes such as trepanning, counterboring and form boring. The BTA Heller product mix includes accessories for those processes including pressure heads, vibration dampeners and boring bars. Sunnen recently introduced the new SHD series skiving and roller burnishing system with tooling engineered and supplied by BTA Heller. Sunnen will also be entering the market with a deep hole drilling and boring machine with tooling engineered and supplied by BTA Heller.
"We have developed various tools and systems for creating intricate internal profiled deep hole drilling from 0.5 in. to 36 in. diameter," said Mark Sollich, Director of Sunnen's BTA Heller division. "To combine forces with Sunnen and its bore geometry expertise creates a company not found anywhere else in our industry. No one company can provide a total bore solution from the creation of the primary hole to the final bore finish specifications like we can."
As Sunnen enters the skiving/roller burnishing sector, it brings its unique approach of providing support to customers also using non-Sunnen equipment, a key advantage to shops using a variety of machine types and/or manufacturers for bore creation and finishing. "We are able to take an unbiased approach to achieving high-quality bores," said Miltenberger. "We offer solutions based on drilling, honing, skiving, roller burnishing, trepanning or any combination of those. With our increased product lines and capabilities, however holes need to be made, we can make them."
SHD Series Skiving and Roller Burnishing System
Sunnen streamlines the skiving and roller burnishing processes with the new SHD series system. "The system is 60 - 70% faster than traditional honing and engineered to deliver precise tolerances and quality surface finishes," said a company spokesperson.
The skiving and roller burnishing process may be used for a variety of part types and materials, and is especially suitable for high production hydraulic cylinder applications. Available in two standard models-the SHD 2400 for part lengths up to 2 meters and the SHD-4400 for part lengths up to 4 meters-the system is designed to finish the inside of diameter of workpieces in a single pass.
"Only Sunnen offers both honing and skiving/roller burnishing solutions, so we are able to provide completely objective consultation on the most cost-effective bore finishing process for each specific bore sizing application," said Phil Hanna, Sunnen Product Manager. "The SHD systems are easy to set up and use, providing superior finishes and dramatically reduced cycle times. Plus, we offer the complete solution with machines, tools, coolant systems, cutting fluids and chip management, all designed to work together."
The SHD is powered by a 57 kw (76 HP) Baldor spindle motor with ABB inverter drive for optimum power, and heavy-duty 55 mm (2.16") linear rails for maximum durability. Beckhoff servo driven 80 mm (3.15") heavy-duty ball screws handle tool feeding and part clamping. An automatic chip removal system eliminates waste from the skiving/roller burnishing process, and a heavy-duty tool-drive shaft vibration dampener ensures smooth operation.
Sunnen skiving/roller burnishing tooling accommodates bore diameters from 51 mm to 178 mm (2.0" to 7.0"), and a full range of individual or combined skiving/roller burnishing tool assemblies are available for use on non-Sunnen machines. Sunnen's SCO-885 cutting oil provides optimal lubricity and chip flushing for long tool life and enhanced surface finish.
For more information contact:
Sunnen Products Company
7910 Manchester Road
St. Louis, MO 63143
800-325-3670 / 314-781-2100
sales@sunnen.com
www.sunnen.com
IMTS 2018, Level 3
Booths N-237400 & W-432216