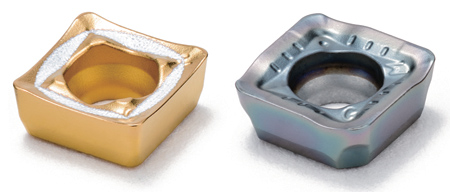
GM Inserts: GM chipbreakers are recommended for steel machining. These DRV Magic Drill inserts combine a CVD coated insert on the outside cutting edge (left) and a physical vapor PVD coated insert (right) on the inside cutting edge.
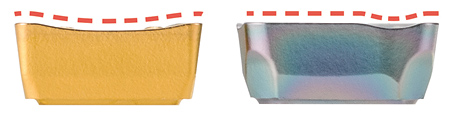
DRV Insert Edge: (l-r) The outside insert is U-shaped while the inside insert is spoon-shaped.
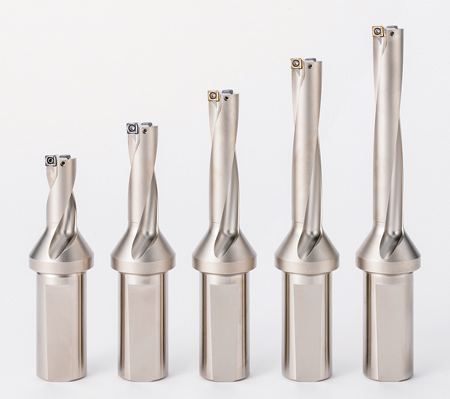
Magic Drill: DRV Magic Drill
Kyocera Corporation has developed a new line of indexable drills to be used mainly for holemaking. Suitable for the automotive, aerospace and medical device industries, the new DRV Magic Drills combine a chemical vapor deposition (CVD) coated insert on the outside cutting edge and a physical vapor deposition (PVD) coated insert on the inside cutting edge. This allows for high-speed machining and enhanced drilling precision.
The newly developed insert chipbreakers are designed to improve chip evacuation. The holder's thicker center core offers greater rigidity. The DRV magic drills can reach depths from 2xD up to 6xD.
"Reducing weight and providing greater functionality of components are current trends in the automotive, aerospace and medical device industries," said a company spokesperson. "This increases demand for products that can provide high-speed and high-efficiency drilling of different workpiece materials under various drilling conditions. With previous indexable drills, PVD coated inserts were used for both the outside and inside cutting edges. This created the disadvantage of increased wear and tear on the outside insert, which moves at a higher speed across the workpiece material than the inside insert. To solve this issue, the DRV Magic Drill uses a CVD coated insert with heat and wear resistance for the outside cutting edge and a PVD coated insert for the inside cutting edge. This creates stable machining even when higher cutting forces are applied to the inside cutting edge. By taking advantage of both CVD and PVD coatings, the drill maintains better stability and longer tool life."
Kyocera offers four chipbreaker designs to cover a range of machining applications: GM (general purpose); GH (tough edge); SM (for stainless steel); and XM (for soft steel and stainless). The inserts are designed with four usable cutting edges to reduce customers' machining costs.
The outside cutting edge has a U-shaped design that provides smooth chip evacuation and compact chips that prevent chip clogging. The inside cutting edge has a spoon-shaped design to reduce cutting forces for smoother chip evacuation, even at 6xD drilling depths. "With better chip flow, the holder body's flutes (grooves) were designed in a way that allows for a 33% larger web thickness when compared to competitors' products," said a Kyocera spokesperson. A high-rigidity holder body with low cutting resistance provides stable indexable drilling at up to 6xD depths.
For more information contact:
Kyocera Precision Tools
102 Industrial Park Road
Hendersonville, NC 28792
828-698-4113
www.kyoceraprecisiontools.com
IMTS 2018 Level 3, Booth W-432279