
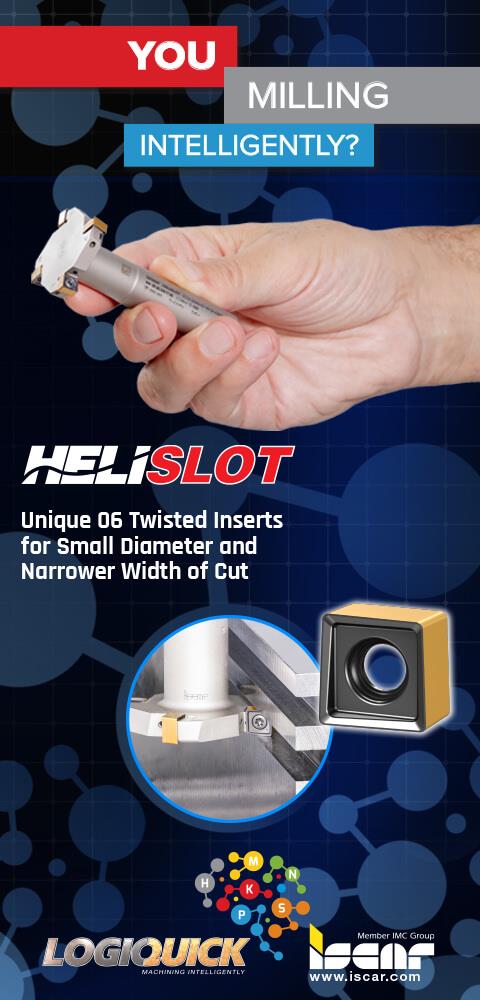
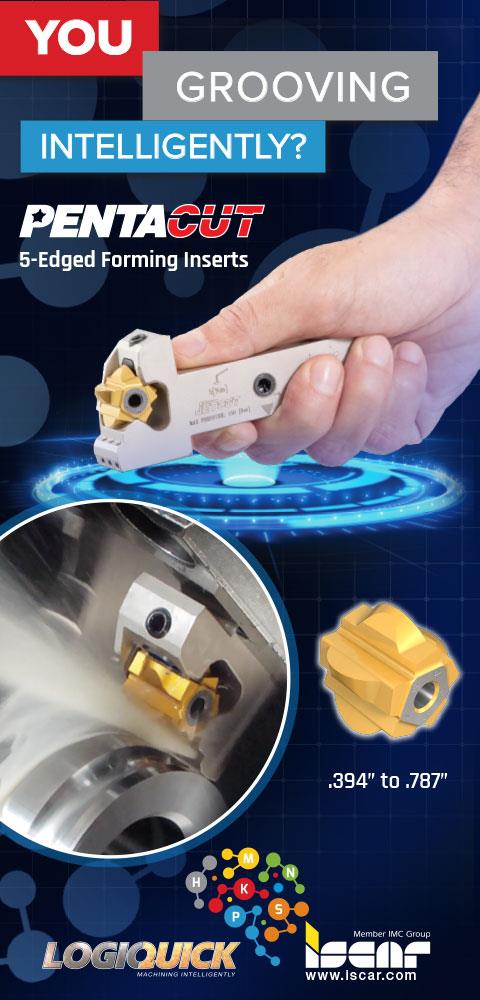
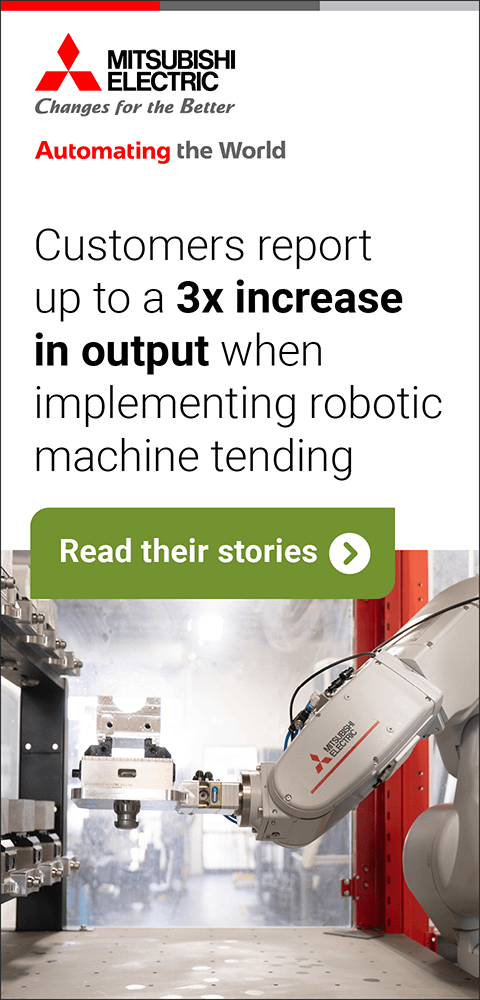
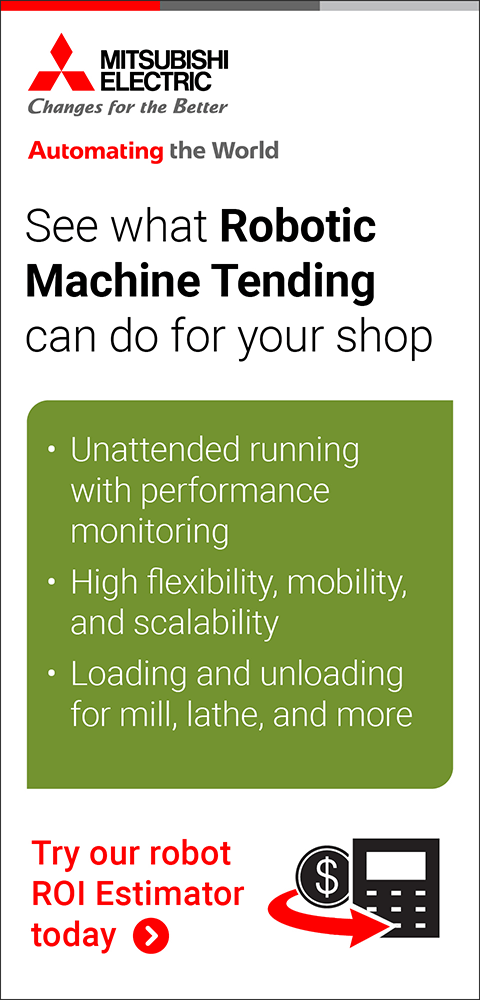
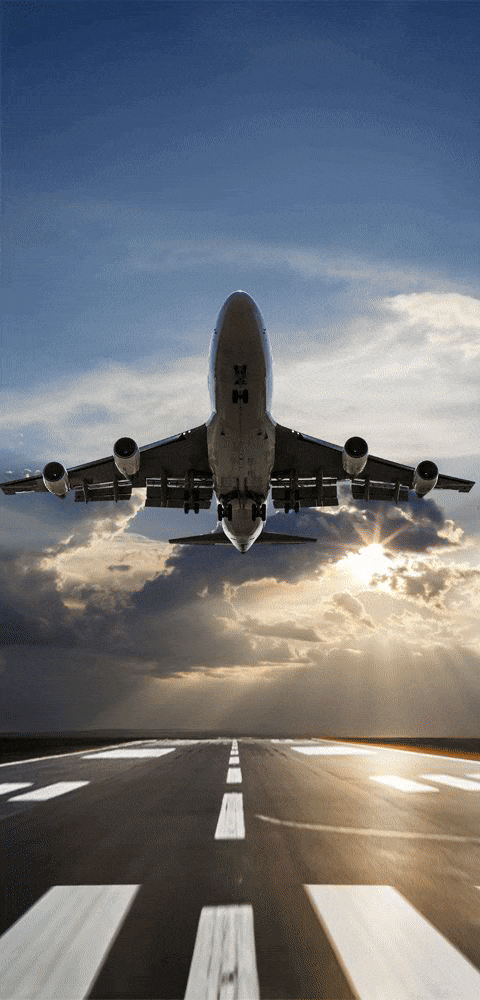
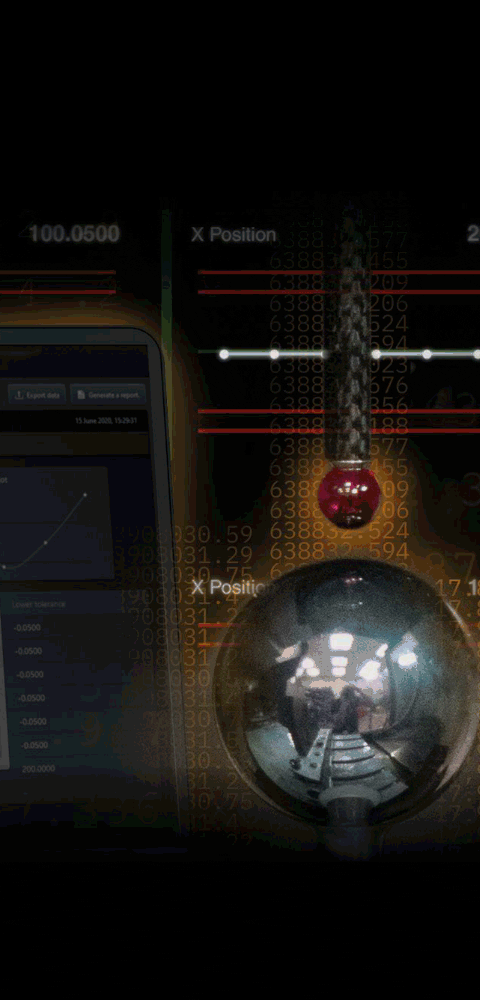
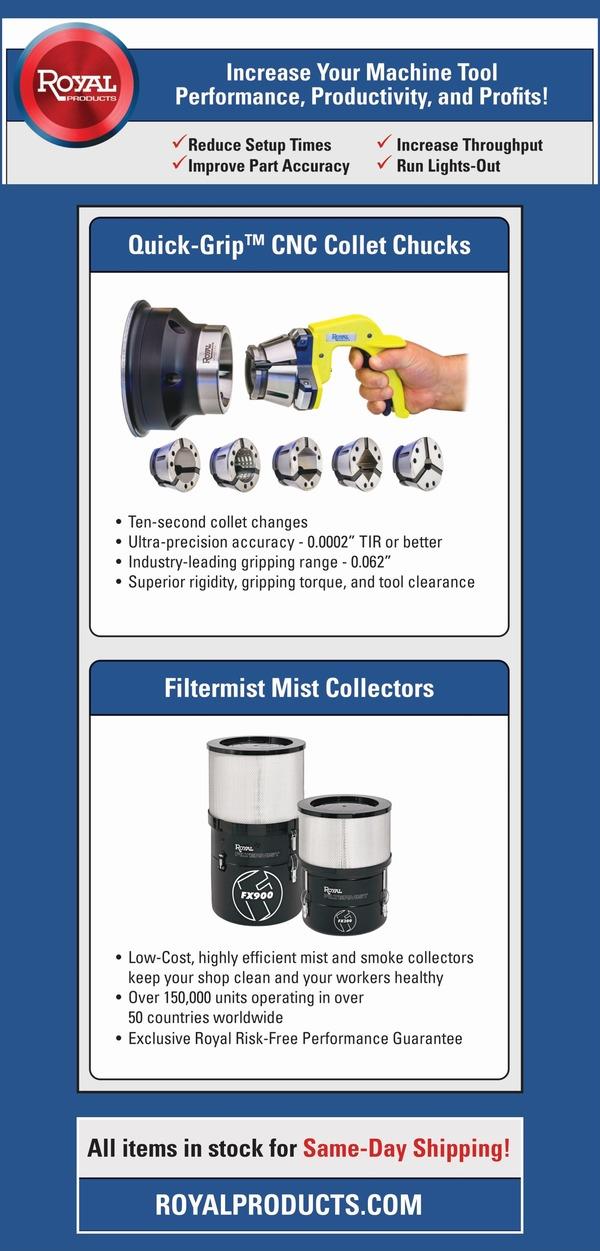
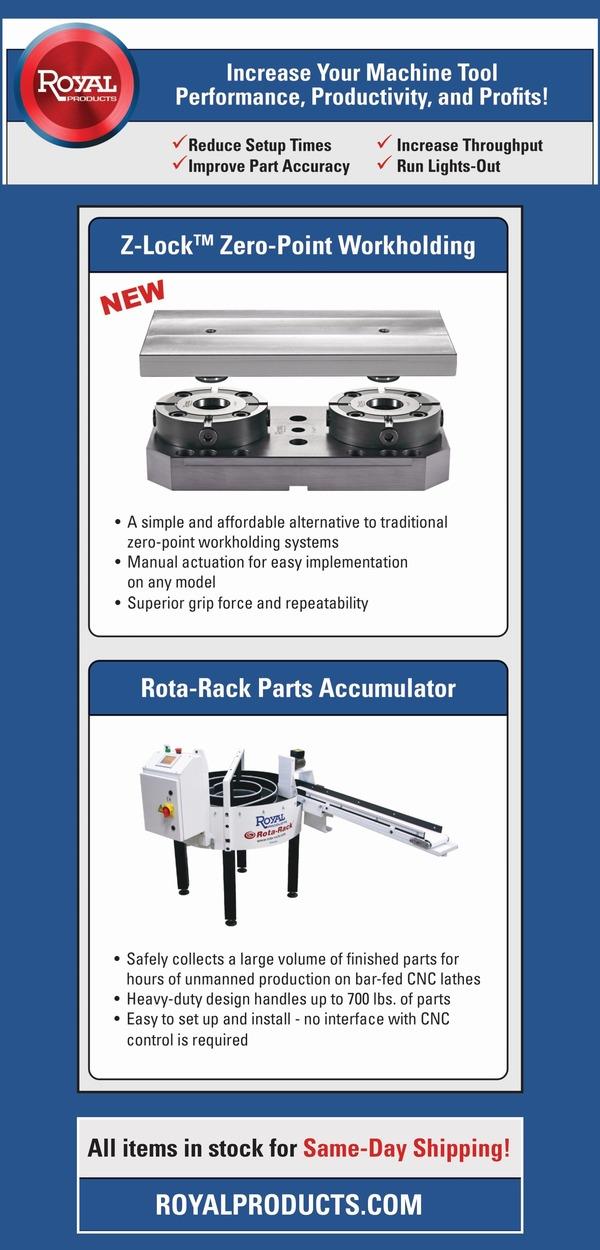

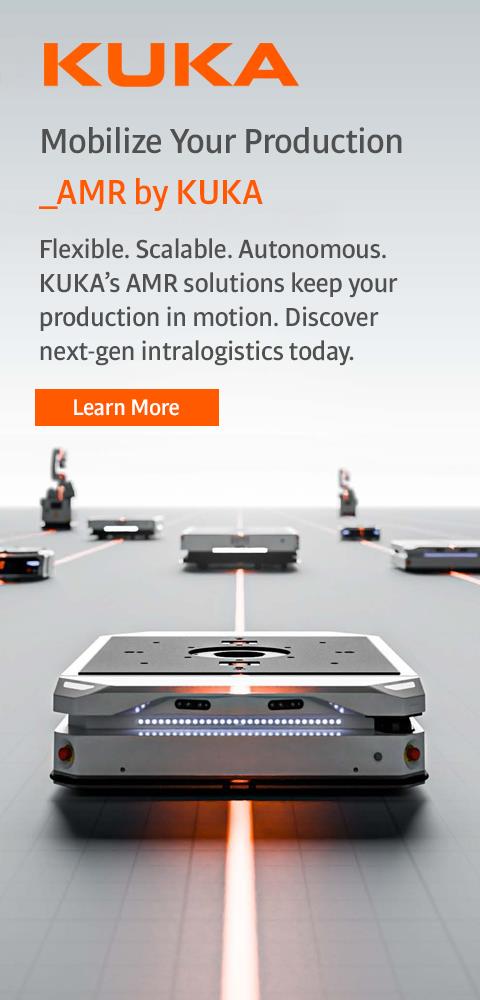
Products that Work Together to Optimize CNC Performance
August 1, 2018
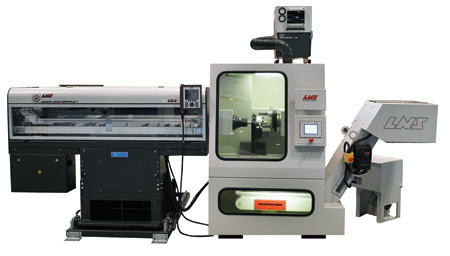
This work cell displays multiple LNS products that optimize CNC machine performance.
LNS will display a broad assortment of bar feeders along with chip conveyors, air filtration systems, workholding devices, coolant systems and the e-Connect Ethernet Communications System at IMTS 2018.
A centerpiece of the booth will be a simulated work cell displaying:
- Quick Load Servo S3 T spindle-length, automatic, magazine bar feeder for fixed or sliding headstock machines accommodates bar diameters from 1/4" to 4-3/4" and has an intuitive, touchscreen HMI that enables partial changeovers in 15 seconds or less and complete changeovers in 1 minute or less. The parts library stores part programs to simplify operator set-ups. Built-in e-Connect Ethernet communications capability makes this bar feeder suited for unattended and lights-out production.
- MH Series filtering chip conveyor filters coolant to 250 or 500 microns using continuously self-cleaning, patented filter boxes. It handles all chip types and sizes from stringy stainless steel to fine brass and aluminum while using no more floor space than a typical hinge belt conveyor. The chip conveyor fits most machine tools and uses an existing coolant tank in most cases. It is equipped with e-Connect Ethernet communications capability for sharing data with the CNC machine control.
- LNS Fox oil/coolant mist collectors are designed to exceed OSHA and NIOSH requirements while eliminating oil/coolant mist, smoke and other fine aerosols and particulates. They install easily on any CNC machine. The Fox mixt collector uses a patented 3-stage filtering system and long-life filters that are easy to replace in 15 minutes. An optional 4th stage HEPA filter removes 99.97% of contaminants. Five models are available with capacities from 170 to 1250 cfm for CNC machines using water soluble, synthetic or neat oil coolants.
- Steady rest-based workholding system designed for machining long workpieces needing extra support, and for performing secondary operations on the end of a workpiece without engaging a tailstock. It is available in a variety of models from .20" capacity to the size that fits largest applications. Each unit custom designed includes steady rests, brackets, manual and automatic clamp bases, valve packages, automatic oil lubrication, optional hose track assemblies and telescoping way covers.
- Blaze Air vacuum unloader automatically removes parts within 2 to 3 seconds through the back of the secondary spindle after both ends have been machined. This continuous, automatic unloading of parts substantially improves production efficiency and operator safety. Capable of unloading shafts up to 48" in length, Blaze Air is easily integrated into automated production cells. It is equipped with e-Connect Ethernet communications capability for sharing data with the CNC machine control.
- PhaSep waste oil removal system uses a floating pick-up to skim waste oil and coolant mix from the top of the machine sump. Oil droplets as small as 20 microns are separated from the coolant and rise to the top of the PhaSep unit. When the oil layer builds up sufficiently in the unit, it passes over a specially-designed weir, and is trapped away from the clean coolant. The oil can then be removed periodically through the waste oil drain. Coolant, cleaned of 99% of contaminated oil, is returned directly to the machine sump.
- e-Connect Ethernet communications system: LNS Systems Software and Control Manager will present live, in-booth and real-time remote monitoring demonstrations of the e-Connect Ethernet communications system that enables data sharing between CNC machines and key LNS peripherals to reduce material waste while improving workflow.
For more information contact:
LNS America, Inc.
4621 East Tech Drive
Cincinnati, OH 45245
513-528-5674
sales@lnsamerica.com
www.lns-america.com
IMTS 2018 Level 3, Booth S-338586
< back