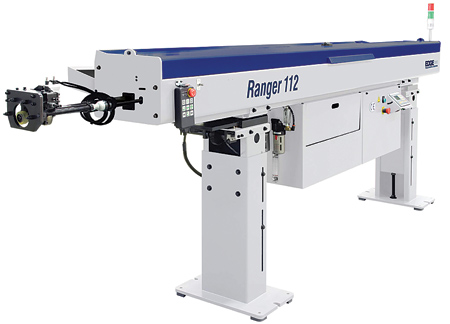
Edge Technologies' Ranger 112 is its newest, scroll-fed 12' magazine bar feeder. The Ranger 112 features a 1.5-15 mm diameter capacity, quick-change polyurethane guide channels, hand-held pendant and a Swiss synchronization device.
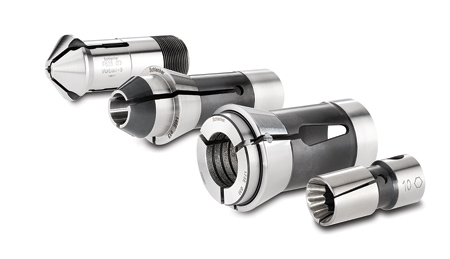
Schlenker collets and guide bushings
Edge Technologies will introduce the Ranger 112 with scroll feed as well as the latest collets and guide bushings from Schlenker.
Ranger 112 Scroll Feed Bar Feed
The Ranger 112 Scroll Feed magazine bar feeder is designed for feeding round, square and hexagonal bar stock in a diameter range of 1.5-15 mm and lengths up to 12' into CNC lathes. A two-pusher system reduces the overall length of the unit by as much as 4'. A short pusher pre-feeds the bar then retracts, and then a second full-length pusher lowers into position to continue the feeding process. The Ranger 112's double pusher system is propelled by a toothed belt for accuracy and smooth, quiet operation. Maximum adjustable feeding speed is 600 mm per second and maximum adjustable return speed is 1,000 mm per second. This feeder is compatible with all types of sliding or fixed, CNC or cam operated lathes.
The Scroll Feed bar device has a storage capacity of 16 bars. Small diameter bar stock, along with the accuracy of the Scroll Feed system, makes the Ranger 112 suited for the medical and electronics industries.
As a standard feature on the Ranger 112, the synchronization device for Swiss-style lathes employs an electro-magnetic coupling, mechanically linking the lathes headstock's Z-axis travel to the bar feeder's pusher, allowing synchronous movement and no loss of connection between the bar stock and pusher collet.
Dual anti-vibration devices stabilize the bar stock at two critical points between the guide channel and lathe spindle, maximizing RPM potential.
The Ranger 112 features a 1.5-15 mm bar diameter capacity with hydrodynamic quick-change polyurethane guide channels. The channel is flooded with oil to create a hydrodynamic effect to support the rotating bar, resulting in the ability to run at higher RPM with reduced noise and vibration. The top guide channel is profiled for all bar stock sizes. The "U" shaped bottom guide channel sections slide easily out of their base. To make the change for a new channel size, a new section is inserted, a screw is tightened and the Ranger 112 is ready to run a new bar stock diameter.
The Ranger 112 features a remote control pendant with a Mitsubishi control and servo drive that provides the Ranger's motion control and functionality. Functions include: manual and automatic operation, manual load/unload of bar stock for set-up and/or change over, movement of bar pusher and the emergency stop. The control is easy to program, yet flexible enough for all applications. Parameters are set through simple F functions. Alarms are well defined and displayed on the operator control panel, whichswings out for ease of use.
The Ranger 112's bar remnants are withdrawn to the back end of the magazine and a gripper extracts it out of the collet and deposits it in a remnant basket. The gripping device is used to both insert the new bar into the bar stock collet and to extract the remnant. It is not necessary to chamfer the bar if it is cleanly cut. No adjustment for bar size is necessary and it is completely self-centering. Bar pusher collet changes can be done less than two minutes.
Collets and Guide Bushings
Edge Technologies represents the full line of Schlenker collets and guide bushings, including an innovative selection of fully sealed collets.
The collets are made from steel specifically made for this intended use and are manufactured to accept polyurethane inserts that grip the bar stock rather than steel as in other collet designs. This allows the user to cut softer materials such as aluminum, brass, and synthetics without any marks being left on the outside dimension of the final product. These inserts can be manufactured to grip round, square, hex and profiled materials.
The collet slots are enclosed with a silicone material that serves as a barrier to keep chips and debris out of the openings. Once the bar is clamped in the polyurethane insert and the collet is in the closed position, it is entirely sealed against contamination.
"All of Schlenker collets and bushings have consistent clamping pressures that handle bar inaccuracies and fluctuations with ease," said an Edge Technologies spokesperson.
Edge Technologies became the sole importer and distributor of Schlenker products for the North American marketplace in 2011.
For more information contact:
Edge Technologies
11600 Adie Rd.
St. Louis, MO 63043
314-692-8388
www.edgetechnologies.com
IMTS 2018 Level 3, Booth S-338348