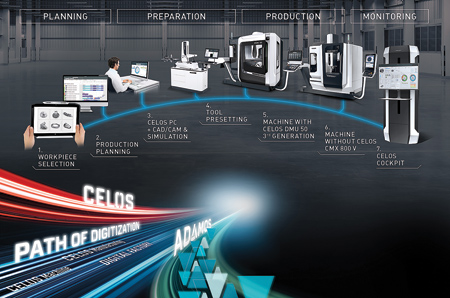
DMG MORI's current digitization initiatives are based on the vision of the digital factory.
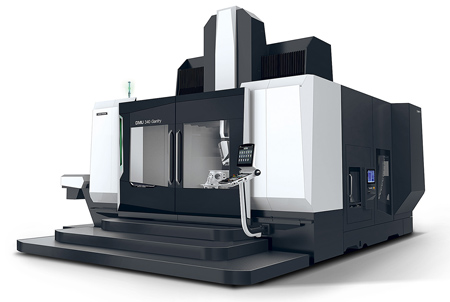
The DMU 340 Gantry is a dynamic and universally applicable XXL machining center.
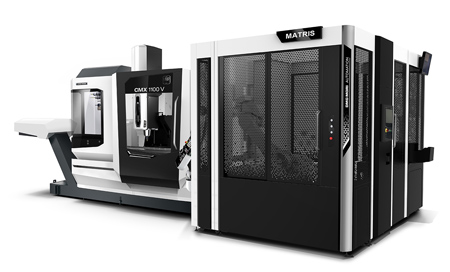
Produced in Davis, CA, the CMX 1100 V VMC will be shown at IMTS paired with the MATRIS modular robot automation.
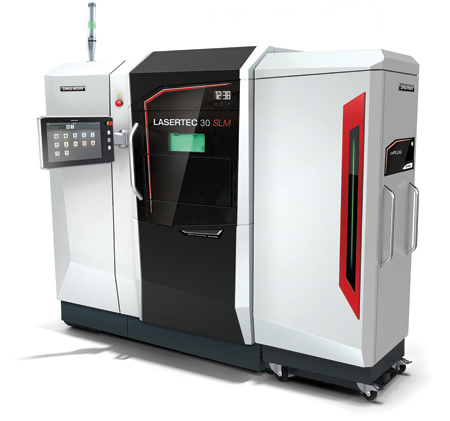
The LASERTEC 30 SLM can manufacture very small, highly complex parts by means of selective laser melting in its powder bed.
DMG MORI will present the "Path of Digitization," two U.S. machine tool premieres and other U.S. manufactured machines, automation solutions such as robotic and linear pallet pool systems and additive manufacturing (AM) solutions.
Integrated Digitization
DMG MORI has further developed its CELOS control and user interface to create an open and consistent ecosystem for digital production. Among other things, in the current CELOS version the focus is on digital workflows for adaptive production planning and integrated tool management. DMG MORI's current digitization initiatives are based on the vision of the digital factory, which is characterized by adaptive factory structures. The digital factory's key feature is the automatic, data-based adaptation of processes in production to changing framework conditions.
A new feature that CELOS offers is the CELOS COCKPIT, which allows users to view the entire production process at a glance. This technological feature heightens production transparency on all order statuses, bottlenecks, waiting times and causes. It provides flexible use in companies as a pure software solution by streamlining the production process in the production control console. Workflows and machining processes can now only be digitally mapped, controlled and optimized based on a consistent flow of data in the shop floor area.
XXL Machines-Two U.S. Premieres
DMG MORI will be premiering for the first time in the U.S. two XXL machines: the DMU 200 Gantry and DMU 340 Gantry. Gantry series machines have been developed for highly dynamic universal applications of large components. Both models offer 5-axis simultaneous machining within a large work area with small space requirement.
The DMU 200 Gantry combines the machining of large components and enhanced dynamics and improves user benefits in the aerospace and automotive industry as well as in moldmaking and the energy sector. With 5-axis machining of up to 30,000 RPM and optional ULTRASONIC or LASERTEC technology integration, more complex components weighing up to 22,046 lbs. made of aluminum or composites as well as welded components can be machined economically.
The work area of the DMU 340 Gantry measures 134 x 110 x 49" and provides expansion options to up to 236" in the X- and 59" in the Z-axis. Due to its gantry design, it also has compact dimensions.
Made in USA Machines
DMG MORI's North American manufacturing facility, located in Davis, CA, offers customers comprehensive local engineering and support for U.S. made machine tools. With a production capacity of up to 1,200 machines per year, the Davis location manufactures and assembles vertical machining centers (VMCs) such as the CMX 1100 V and horizontal machining centers (HMCs) such as the NHX 4000 3rd Generation and NHX 6300 2nd Generation.
The NHX 4000 3rd Generation machining center has a 21 RPP rotary pallet pool feature. It features spindle speeds of 20,000 RPM, power rating of 50 HP and maximum torque of 163 ft-lbs. A standard auto coupler hydraulic fixture interface enables the NHX 4000 3rd Generation to automate in a more efficient manner. This HMC handles workpieces up to 882 lbs.
The NHX 6300 2nd Generation is equipped with a standard 12,000 RPM, 75 HP powerMASTER spindle with maximum torque of 595 ft-lbs. An optional high-speed version from the powerMASTER spindle range has a maximum speed of 16,000 RPM and up to 1,042 ft-lbs. of torque for demanding heavy-duty machining. The NHX 6300 2nd Generation offers space for pallets up to 25 x 25", a workpiece height of 51" and maximum loading capacity of 3,307 lbs.
The CMX 1100 V VMC enables workpiece weights of up to 2,205 lbs. and provides a travel path up to 43.3 x 22 x 20.2". Rapid traverses are 1,417 IPM in X- and Y-axes, and 1,181 IPM in Z. The CMX 1100 V will be featured with a speedMASTER 20,000 RPM spindle with 50 HP and 163 ft-lbs. of torque paired with the MATRIS modular robot automation.
Automation
It is the aim of DMG MORI that every machine in its portfolio be equipped with an automation option in future. Intelligent linking of the machine tool and automation is a key focus at its production locations to ensure customers can receive automation solutions from a single source.
DMG MORI will present the PH 150 pallet handling system, LPP multi-layer pallet pool system, 21 RPP space-saving automation solution, as well as the newly developed flexible GX gantry loader in the new VERTICO design. Robo2Go 2nd Generation extends the portfolio as a mobile robotic automation system for a large number of turning machines. Integrated turn-key solutions that link any number of machines and process-supporting work steps complete the automation range from DMG MORI.
With its Robo2Go 2nd Generation, DMG MORI has a workpiece handling solution that can be put to flexible use on a number of universal turning machines, and is also easy to program with CELOS. This year, the CTX beta 800 will demonstrate its easy teach-in functions for different workpieces and flexible set-up at multiple turning machines.
DMG MORI also creates larger manufacturing cells comprising of several machines using linear pallet pools (LPPs) and robotic automation systems. The LPP feature provides flexible, multi-layer pallet pool systems with up to eight machines, 99 pallets and five set-up stations. The NHX 6300 2nd Generation automation solution demonstrates the handling of up to three different sizes of pallets possible in one system.
Additive Manufacturing (AM)
Highlighted this year is the LASERTEC 30 SLM. With the powder bed technique, very small, highly complex parts can be manufactured by means of selective laser melting. The LASERTEC 30 SLM enables the flexible use of different materials, while an intelligent powder module concept allows the change of material in under two hours. The closed powder circuit is designed for work safety and process autonomy. The ergonomic design of the machine simplifies workpiece handling and maintenance work through the arrangement of doors and flaps, while the new Stealth Design Control Panel keeps all important buttons and operating elements in direct view and control panel.
Holistic software solutions from the CAD file (RDesigner) to the process control (ROperator) enable the LASERTEC 30 SLM to create workpieces of various materials with high density and good mechanical behaviors. This selective laser melting machine produces 3-D parts with lattice and honeycomb structures not achievable with other machining methods. It has an integrated powder recycling center for more efficiency and improved powder handling in removable units.
For more information contact:
DMG MORI - Americas Headquarters
2400 Huntington Blvd.
Hoffman Estates, IL 60192
847-593-5400
Service Hotline: 855-DMG-MORI
www.us.dmgmori.com
IMTS 2018 Level 3, Booth S-338900