
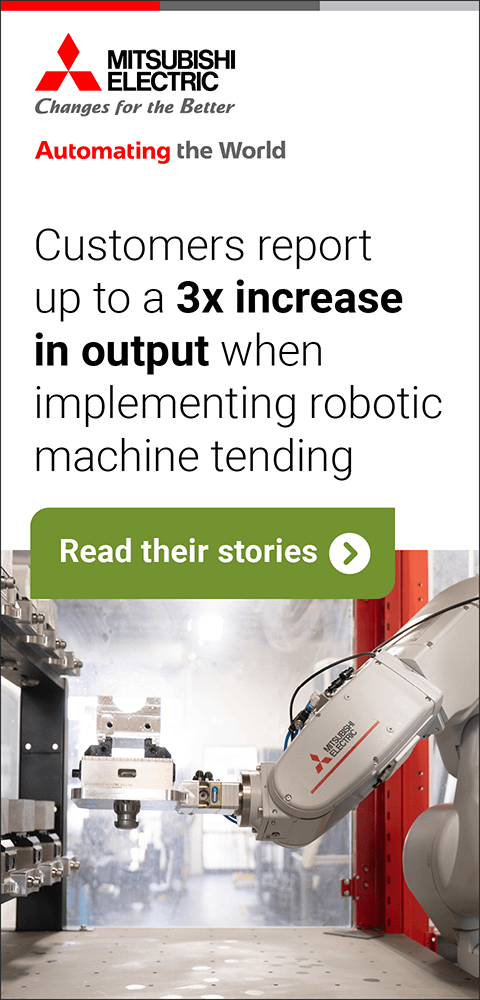
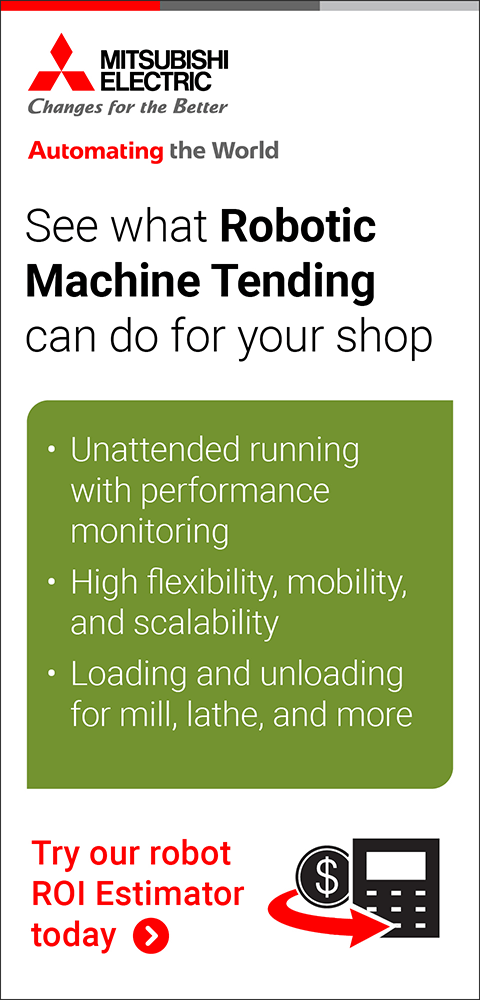
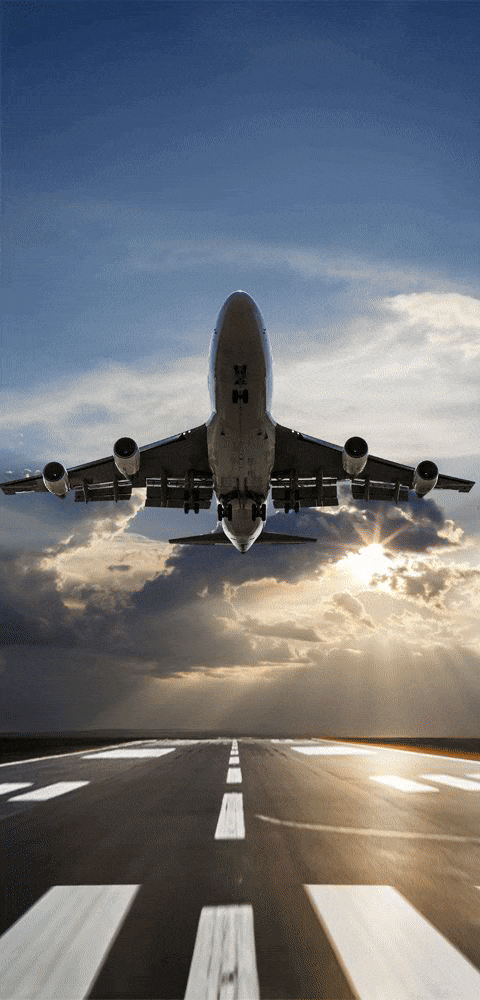
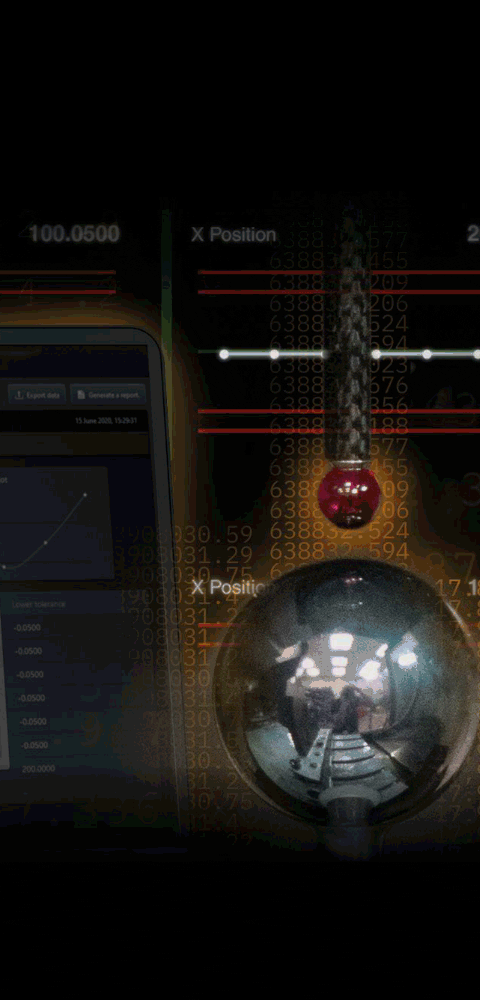
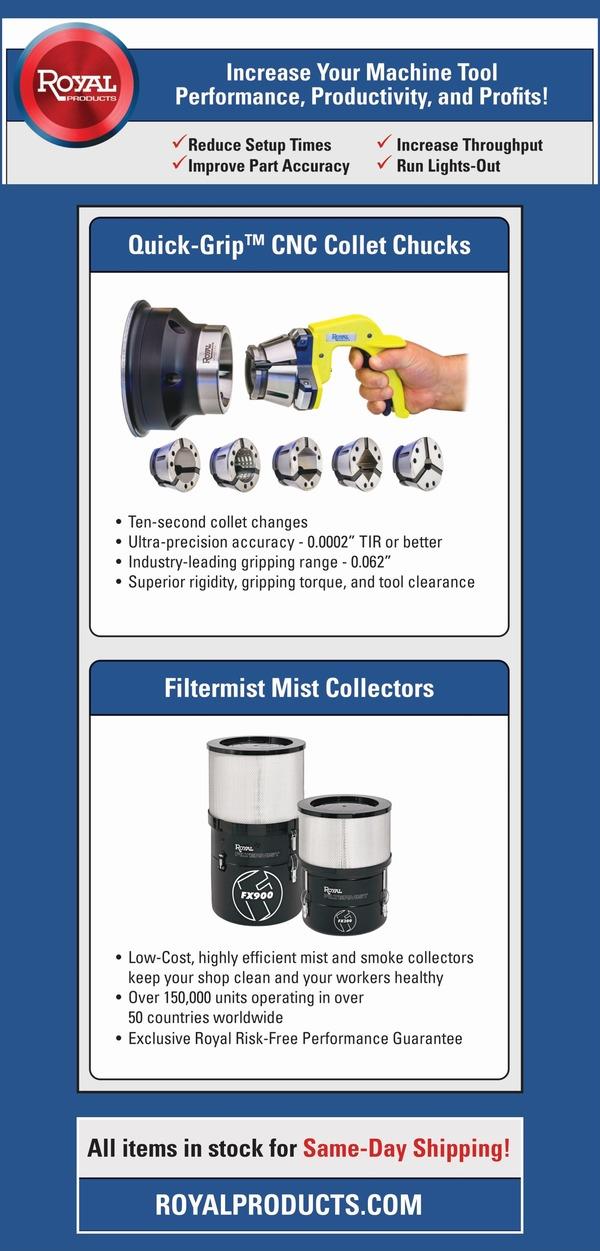
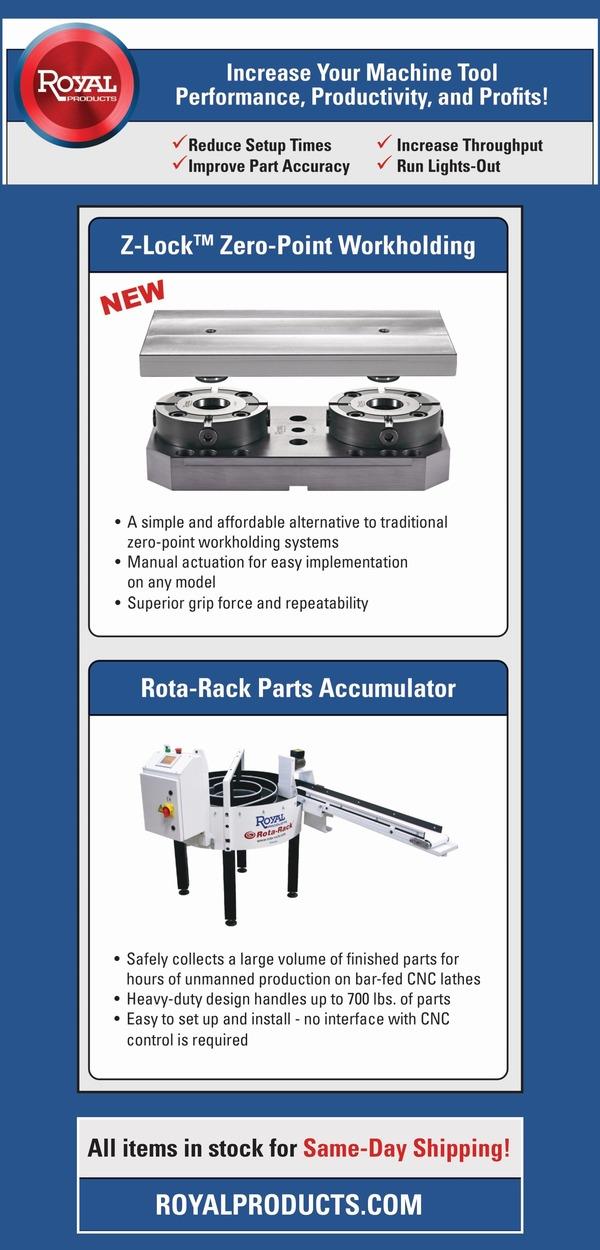

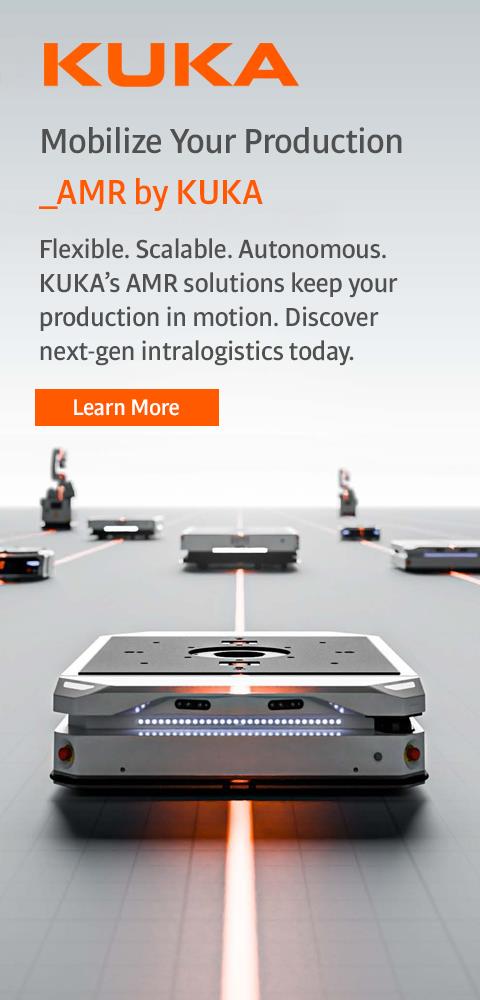
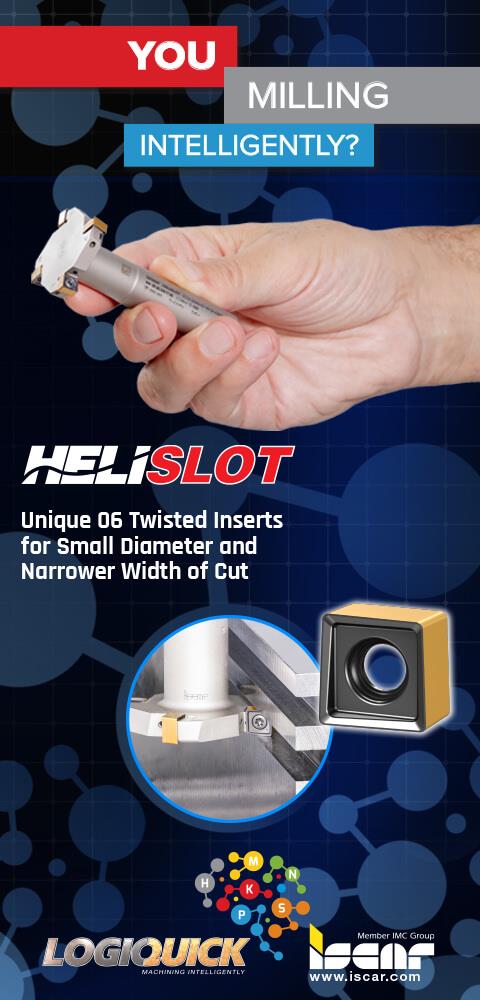
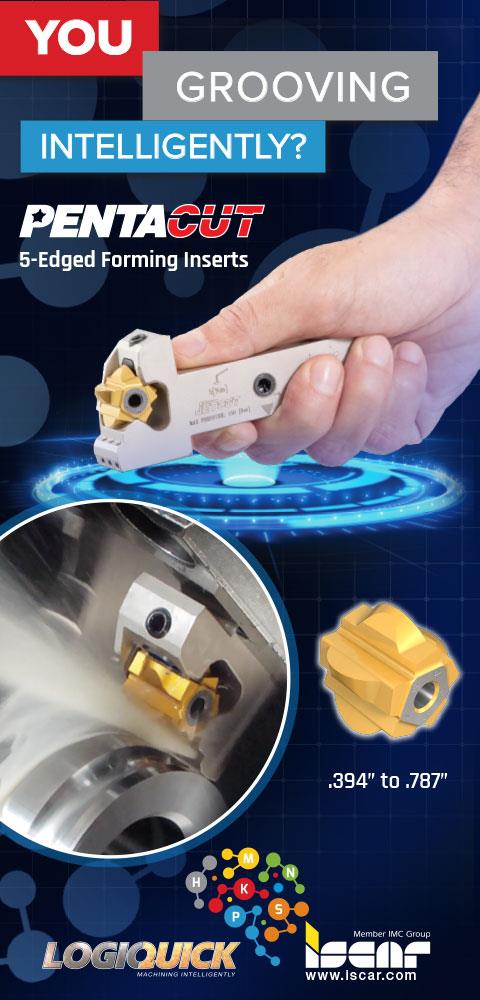
New Robots and Advanced Manufacturing Solutions
August 1, 2018
Yaskawa Motoman will feature the latest in advanced automation solutions at IMTS 2018. The demonstrations include several new robots, turn-key workcells, collaborative technology and innovative advancements designed to enhance manufacturing productivity for operations of varying sizes and industry sectors.
Highlights at the Yaskawa booth include:
- New MH900 robot: The heavy-duty, large reach MH900 robot is the latest addition to Yaskawa's MH-series line of material handling robots. Its parallel-link construction provides strength, rigidity and stabilization for high moment of inertia loads (2,200 kg/m2), and it easily accommodates a range of large, heavy components such as car frames and agricultural equipment. Designed and assembled in the U.S., the 6-axis MH900 features a 900 kg payload capacity, 4,683 mm horizontal reach and 6,209 mm vertical reach.
- New MotoMini robot: "The MotoMini is the industry's smallest and lightest 6-axis robot," said a Yaskawa Motoman spokesperson. Weighing only 7 kg, it is easy to carry and designed for tabletop-, floor-, ceiling- or wall-mount installations. Its compact footprint allows the MotoMini to be mounted close to workpieces and other machinery in existing lines or cells. Offering high acceleration speeds for a small-size robot, the MotoMini is suitable for a variety of applications, such as small component assembly or case packing. It is controlled by the a new, compact YRC1000micro robot controller.
- New YRC1000micro robot controller: "The ultra-compact and lightweight YRC1000micro is the smallest controller in its class," said the spokesperson. Its space-saving design enables installation in either a vertical or horizontal position, as well as within a 19" rack. The YRC1000micro features new functions to improve programming efficiency and robot operation. Yaskawa's standard teach pendant and the new Smart Pendant can be used for programming this controller.
- New HC10DT (direct teach) robot: Designed to work safely with or in close proximity to human workers, the 6-axis HC10DT collaborative robot features enhanced hand-guided teaching for fast deployment or redeployment on demand. Power and force limiting technology is used to protect the worker from potentially harmful contact situations. The HC10DT can be integrated with existing automation infrastructure. The robot offers a 10 kg payload and 1,200 mm reach, and it is built with the industrial strength to perform a broad range of material handling, machine tending or light assembly tasks.
- New Smart Pendant: An easy-to-use 10" touchscreen teach pendant provides simplified programming and fast implementation. It offers a simple learning curve, making it suitable for novice robot programmers. The built-in SMART Frame function allows the robot to adapt to the position of the programmer, which eliminates the use of conventional coordinate (XYZ) frames.
- ArcWorld 1200: This recently redesigned pre-engineered welding workcell features the new Motoman AR1440 arc welding robot equipped with AccuFast laser-based seam finding and ComArc LV (low voltage) seam tracking capability. The MSR-355 high-speed turntable offers a payload capacity of 355 kg per side. Its dual-station configuration facilitates easy loading and unloading of parts. A Miller Auto-Continuum power source with Insight Centerpoint arc data monitoring.
- New Yaskawa Cockpit: Yaskawa Cockpit is Industry 4.0 software that integrates robots and other factory level assets into a complete systems management and visualization solution. Yaskawa Cockpit provides insight into device information and production rates, identifies appropriate preventive maintenance, predicts the life span of components, and automatically distributes system alarms to the appropriate personnel.
- GP8 robot: Designed for high-speed assembly and handling applications, the GP8 robot's small footprint, slim-arm design minimizes interference with peripheral devices and enables close proximity placement to workpieces and other robots for high-density layouts. The GP8 has an 8 kg payload capacity, a 727 mm reach, and can be floor-, ceiling- and wall-mounted. Its IP67 washdown rating, with easy-to-clean surface, enables use in harsh environments.
- MotoSight 3D BinPick: The next generation of vision technology for bin picking applications, the MotoSight 3D BinPick system, uses a single 3-D camera with integrated lighting to quickly and easily recognize and pick parts that are randomly placed in bins.
- Spot welding: Scalable, integrated spot welding system featuring two Motoman spot welding robots. These workcells are customizable to suit application needs. Several new spot welding robots will be highlighted; they feature exceptionally fast axis speeds and acceleration to reduce air cut time and increase production output.
- New 3-D printer: A strong, rigid framework and Yaskawa servo control combine to deliver 3-D printing at 350 mm per second. A Yaskawa MP3300iec machine controller achieves this productivity with standard G-code, using an open source GUI for easy customizing of user controls. The new printer was developed in a cooperative effort with Titan Robotics, a manufacturer of high speed industrial 3-D printers.
For more information contact:
Yaskawa America, Inc.
Motoman Robotics Division
100 Automation Way
Miamisburg, OH 45342
937-847-6200
www.motoman.com
IMTS 2018 Level 3, Booth N-236601
< back