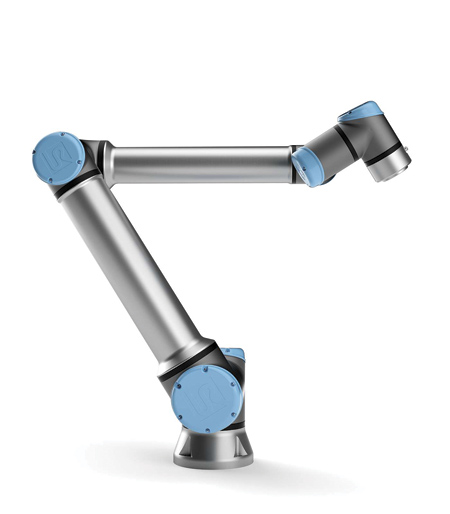
UR10e
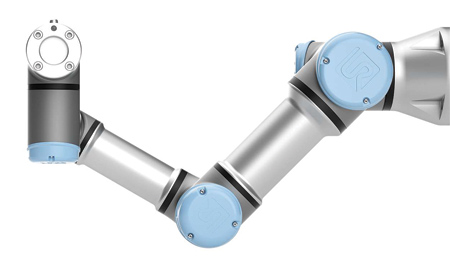
UR3e shown side-mounted
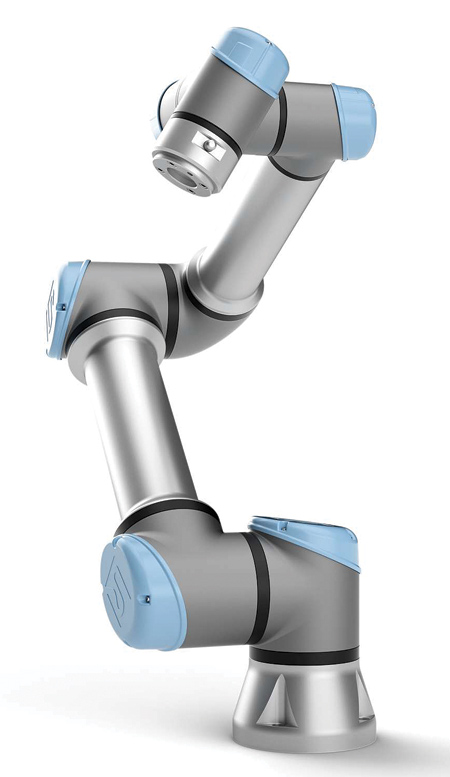
UR5e
Universal Robots is adding an "e" (for "evolution") to the UR robot model names in its new flagship series: the UR3e, the UR5e and the UR10e robot arms.
With a new built-in tool-centric force/torque sensor, the e-Series is designed for applications requiring force control right out of the box, such as assembly, sanding, buffing, polishing and deburring, where force feedback is paramount in order to obtain uniform results and repeatability. Additionally, the force/torque sensor can be used to measure mass and perform related inspection processes or precisely detect contact. A repeatability of 30 micron (0.03 mm) in the UR3e and UR5e models and 50 micron (0.05 mm) in the UR10e means the new cobots are suitable for very precise finishing, assembly and electronics tasks
A redesigned intuitive and responsive-touch user interface decreases cognitive load and expedites program development by simplifying programming flow while reducing programming to a few clicks on a new lightweight, wide-screen teach pendant. Advanced users can utilize the new externally accessible, 500 Hz system bus to implement more complex motion control algorithms or profiles.
"The e-Series offers unparalleled convenience; it takes just one hour to unpack the cobot, mount it and program the first task," said a company spokesperson. A new wrist-joint-tool communication interface reduces production line integration time and the hassle associated with routing cables between the end effector and control cabinet. All joints are field replaceable in under six minutes.
As the catalog and capability of UR+ end effectors has grown, so has the need for increased tool power consumption. To address this emerging need, the e-Series platform tool power supply now supports up to 2A of peak current. The new cobot line also adds four additional digital inputs with an associated interface for use with conveyor tracking.
The user interface now also includes programming stopping time and stopping distance for protective stops. This feature reduces the complexity and uncertainty involved in performing pre-deployment risk assessments. All 17 safety functions are certified by TÜV Nord and in compliance with the EN ISO 13849-1 and EN ISO 10218-1 machinery safety standards for unobstructed human-robot collaboration.
For more information contact:
Universal Robots USA
5430 Data Court, Suite 300
Ann Arbor, MI
844-462-6268
ur.na@universal-robots.com
www.universal-robots.com
IMTS 2018 Booth N-236861