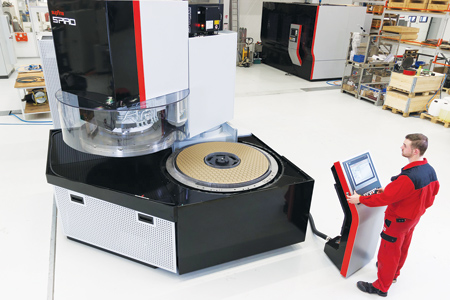
Supfina's Spiro F12 fine-grinding machine-the largest of the Spiro line-can achieve highly precise plane parallelism (≤ 1.0 µm) for precision bearings, pump gears, valve plates and more.
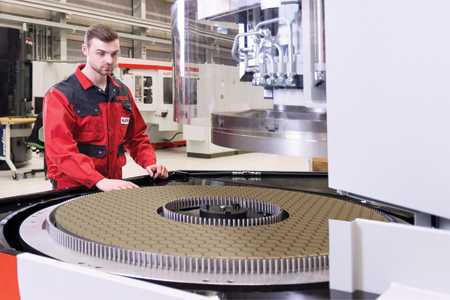
The Spiro F12's lower grinding wheel-which can accommodate parts with diameters of 6 mm to 420 mm and thicknesses of 1 mm to 100 mm-is accessed easily. That is because the upper grinding wheel swings well out of the way, facilitating loading and unloading as well as any maintenance tasks.
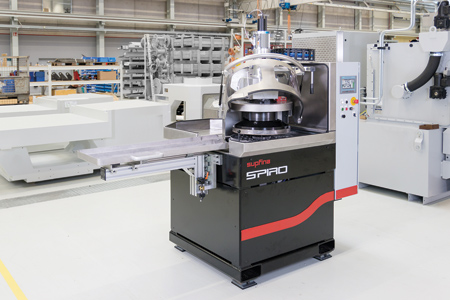
Smallest of the Spiro line, the F5 was designed to process parts with diameters of 4 mm to 150 mm and thicknesses of 0.3 mm to 50 mm while achieving precise plane parallelism (≤ 1.0 µm).
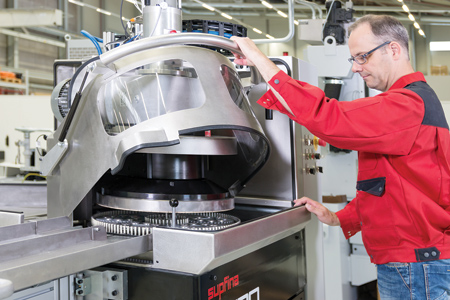
Like the other machines in the Spiro line, the F5's safety shield and upper grinding wheel are designed to swing well away from the work area, facilitating loading and unloading as well as any maintenance tasks.
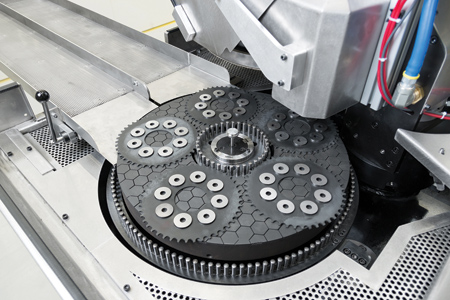
Parts to be finished are loosely placed in "carriers" that pins rotate in an orbiting manner. Machining takes place between two grinding wheels (diamond or CBN).
Supfina has expanded its line of fine-grinding machines to include the Spiro F5 and the Spiro F12, both of which will make their North American debut at IMTS. Along with the Spiro F7, the three machines provide customized solutions for batch mode processing of a wide range of parts.
"From aluminum to steel, soft plastics to hard ceramics-matter the material, the Spiro series can achieve highly precise plane parallelism (≤ 1.0 µm) for precision bearings, pump gears, valve plates and more," said a company spokesperson. "And because parts can be machined up to 20X faster than lapping and with more precision than double-disk grinding, costs per unit are reduced. Depending on the part's material, dimensions, starting surface finish and removal requirements, a single Spiro can fine-grind several thousand parts per hour."
For plane-parallel fine grinding on both sides, parts are loosely placed in carriers that have teeth on the outside diameter. An inner pin ring rotates the carriers as they shift on a stationary outer pin ring in an orbiting manner. Machining takes place between two rotating grinding wheels (lower and upper). The optimal machining force is applied by the upper wheel.
The smaller F5 can process parts with diameters of 4 mm to 150 mm and thicknesses of 0.3 mm to 50 mm, while the larger F12 can accommodate parts with diameters of 6 mm to 420 mm and thicknesses of 1 mm to 100 mm. The midsize F7 is suitable for parts with diameters and thicknesses of 5 mm to 220 mm and 0.6 mm to 80 mm, respectively.
Because the Spiro eliminates water from the cooling process, there is no chance of contamination-thus cutting costs (the coolant is also recycled). The machines' sturdy base keeps vibration to a minimum, reducing tool wear, while their modular, ergonomic design allows quick tooling changes and easy accessibility. For example, the upper part of the machine swivels completely out of the work area, allowing fast loading and unloading of parts as well as easy maintenance.
A high-precision, indirect measuring system (probe and anvil) is designed to provide optimal process results that can be duplicated from batch to batch, thus increasing yield. That is because such factors as coolant temperature and abrasive contamination do not affect the measuring system.
For each machine that it sells, Supfina assigns a dedicated senior project engineer who provides not only installation and training but also ongoing customer support.
For more information contact:
Supfina Machine Company, Inc.
181 Circuit Drive
North Kingstown, RI 02852-7439
401-294-6600
info@supfina.com
www.supfina.com
IMTS 2018 Level 3, Booth N-236949