

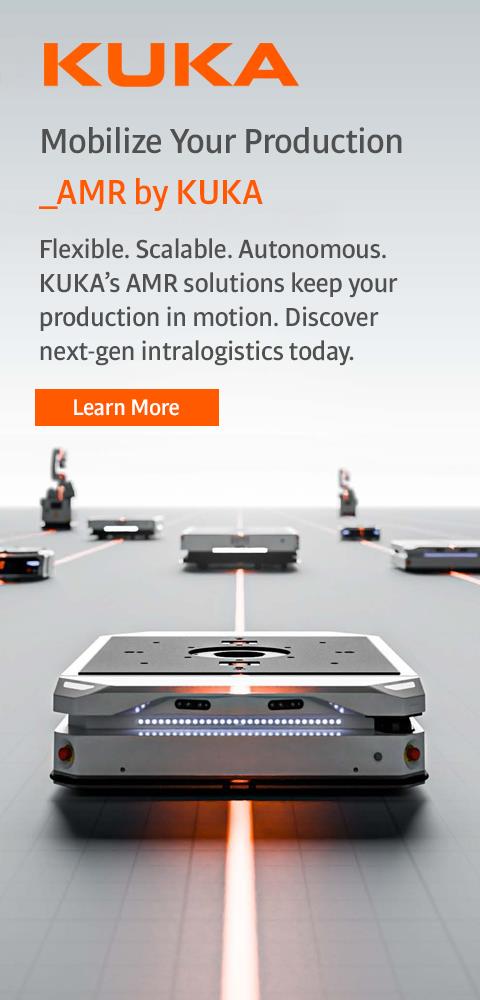
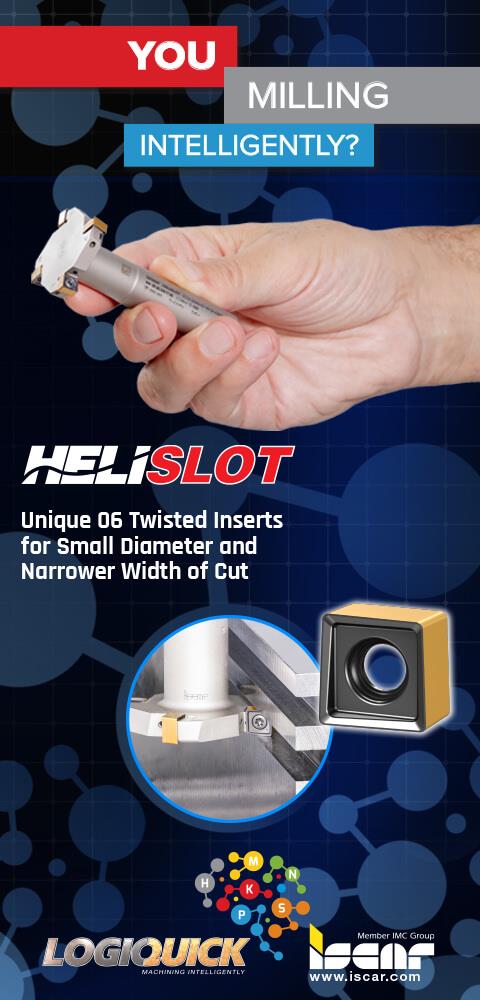
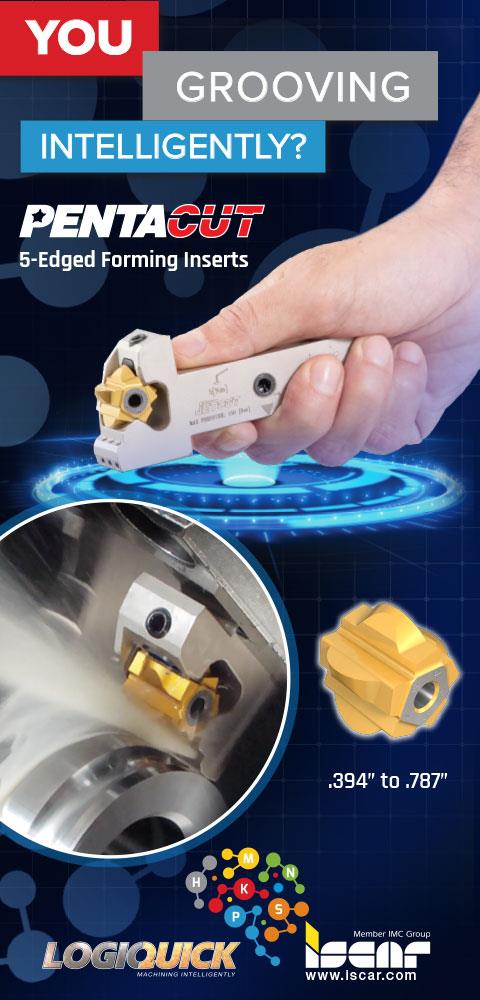
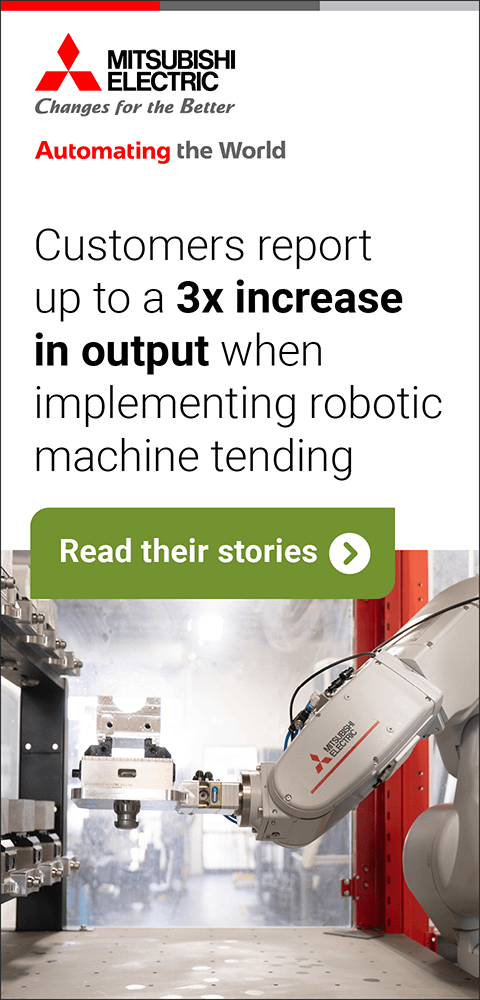
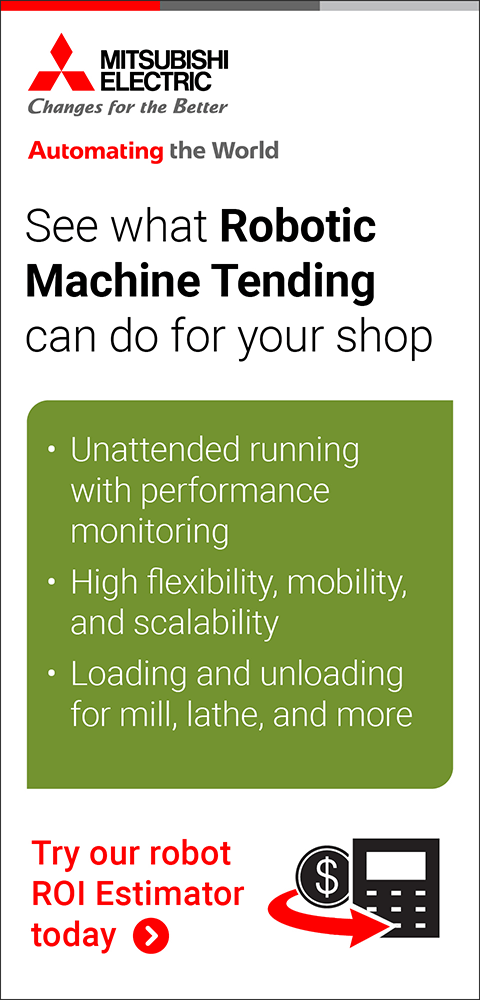
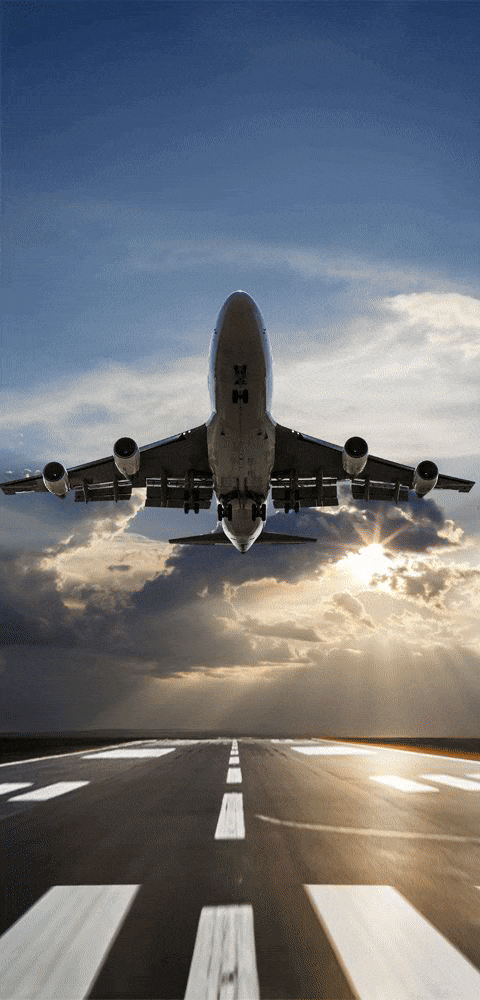
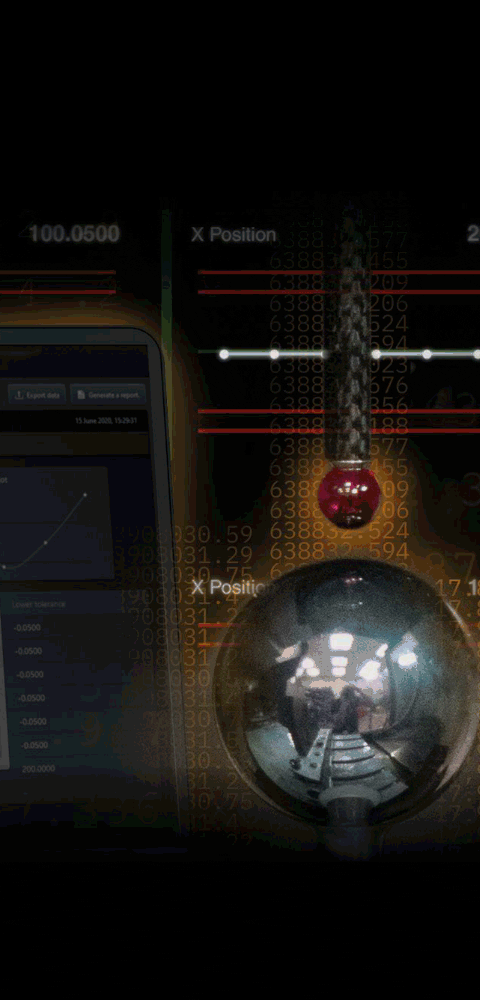
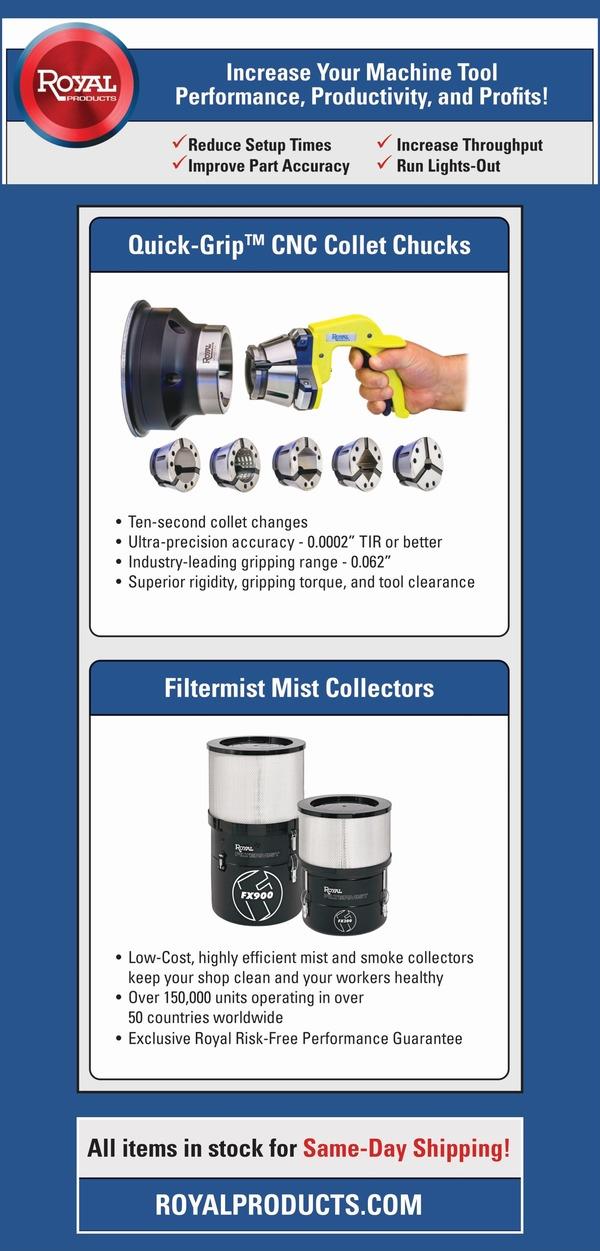
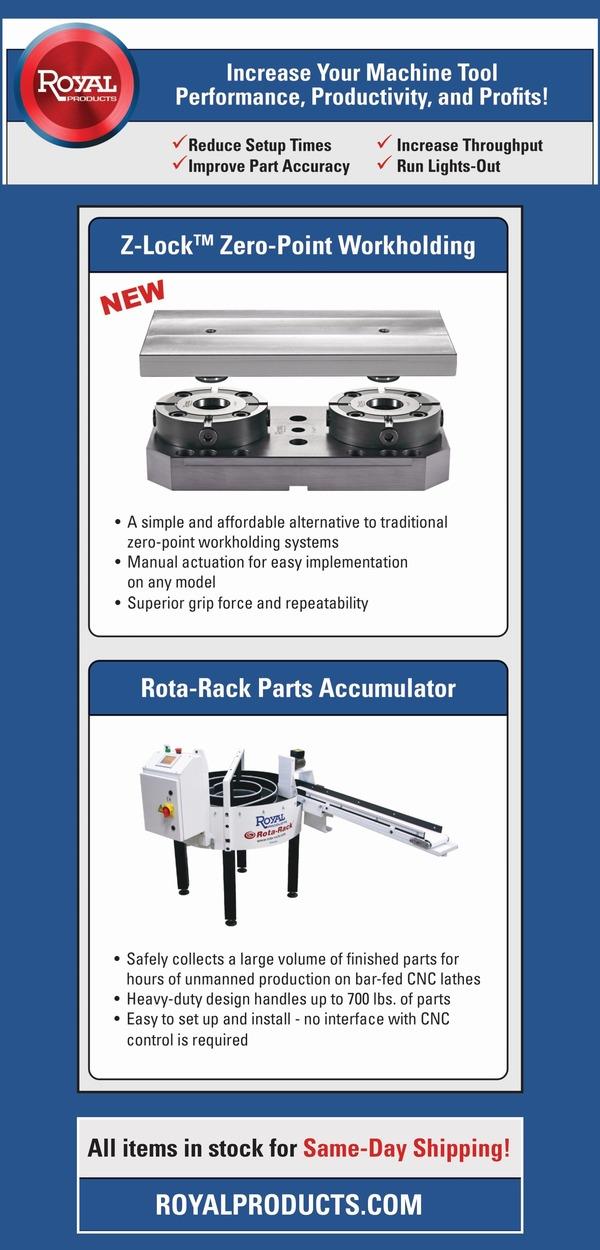
Reduce Overhead Crane Work Cycle Times with Target Positioning
November 1, 2014
Target Positioning from Konecranes allows an overhead crane load to automatically travel from a preset starting position to a destination point with just the touch of a button. It is designed to improve productivity and safety by adapting the overhead crane's working area to the physical layout of the production line.
"Often times an overhead crane moves loads from known pick-up positions to known end locations," said a company spokesperson. "Because of this, the work cycle is very predictable and repetitive. Traditionally in this pattern, the operator manually moves the loads, which is not the most effective or efficient way."
With Target Positioning from Konecranes, the operator selects the load's target address and presses the Target Positioning button on the operator interface. As long as the button is pressed, the crane drives itself to the selected target with a preconfigured travel height. The load will navigate to the selected target position (X, Y) at the predefined height (Z) and allow the operator to make the final vertical positioning manually. Manual operation can be always started by releasing the Target Positioning button on the control device.
Target Positioning from Konecranes allows the operator to define up to 120 targets and seven home positions on the crane operator interface.
Konecranes' line of SMARTON cranes is available with Smart Features, software-based intelligence that offers total control over process tasks, saving time and increasing productivity.
For more information contact:
Konecranes, Inc.
4401 Gateway Blvd.
Springfield, OH 45502
937-525-5533
www.konecranesusa.com
< back