
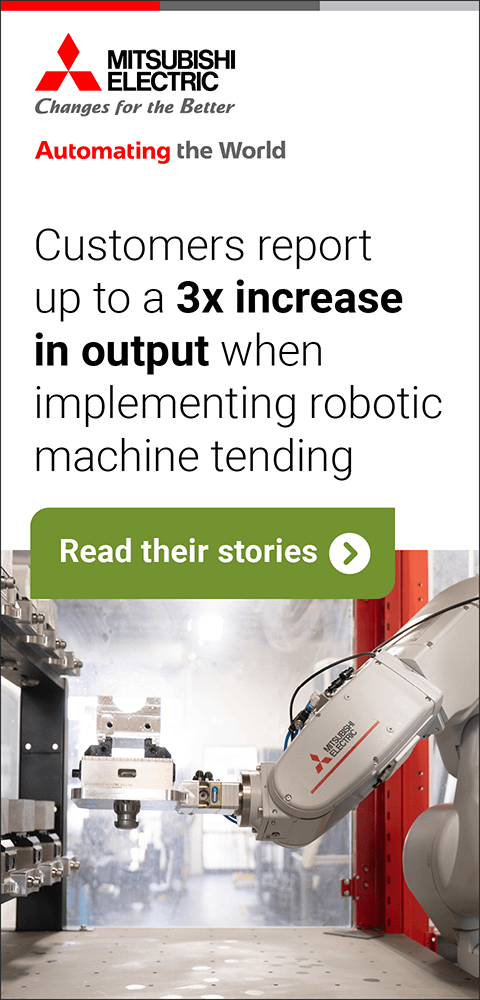
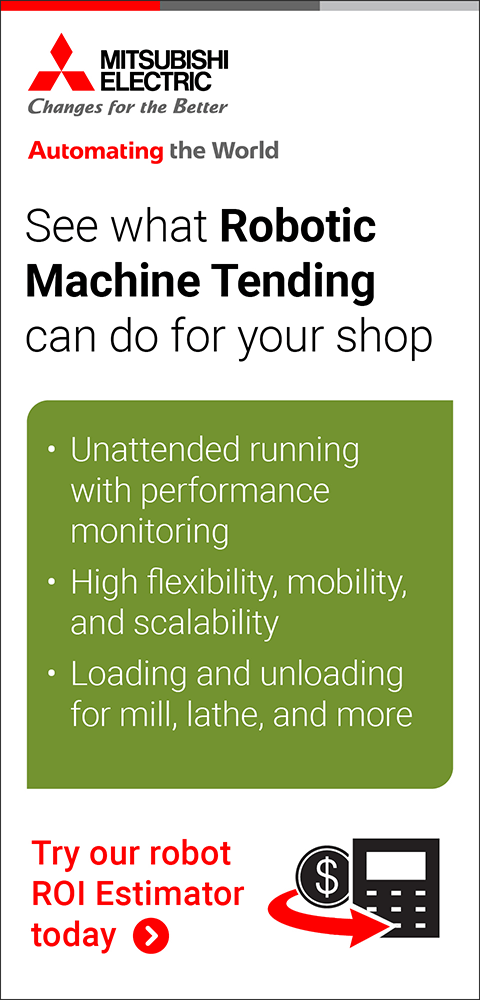
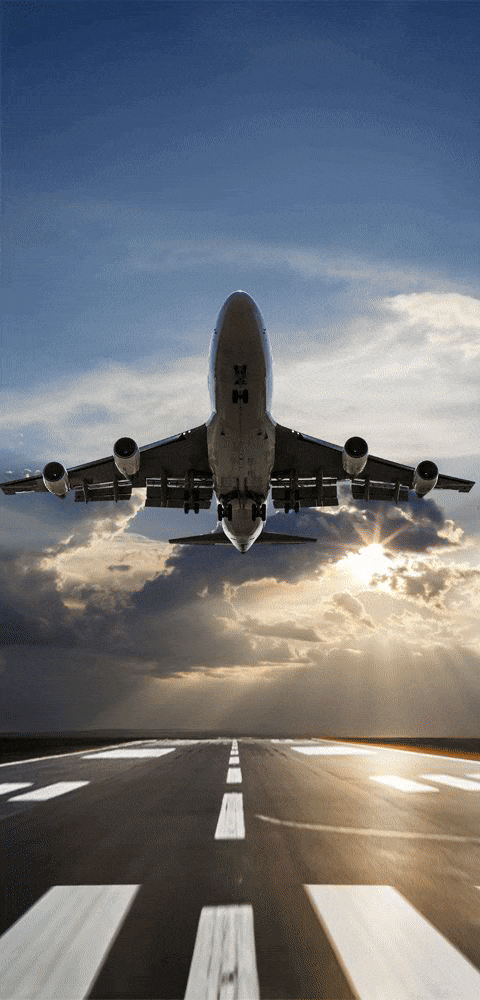
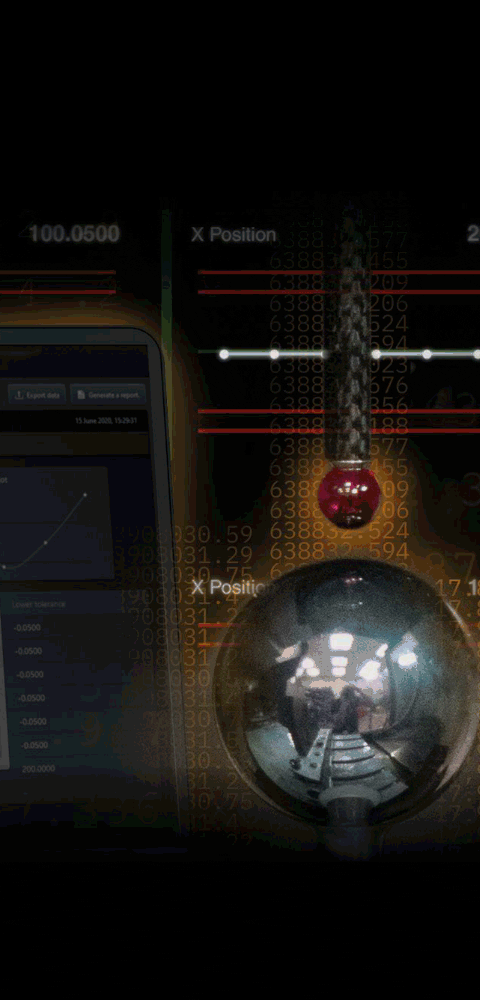
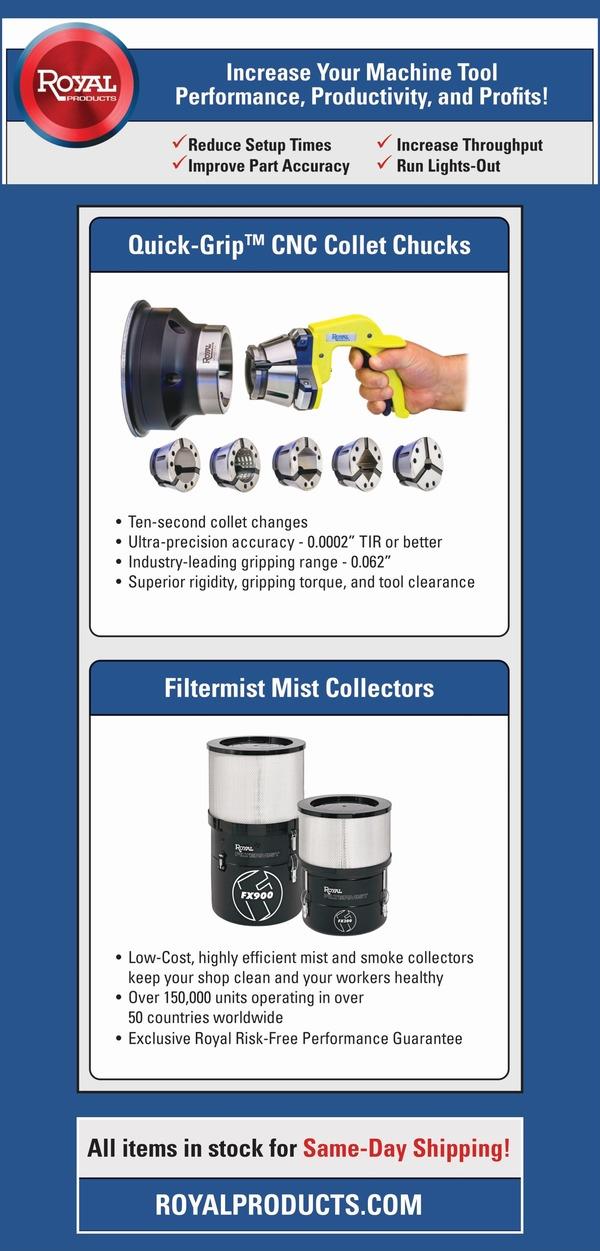
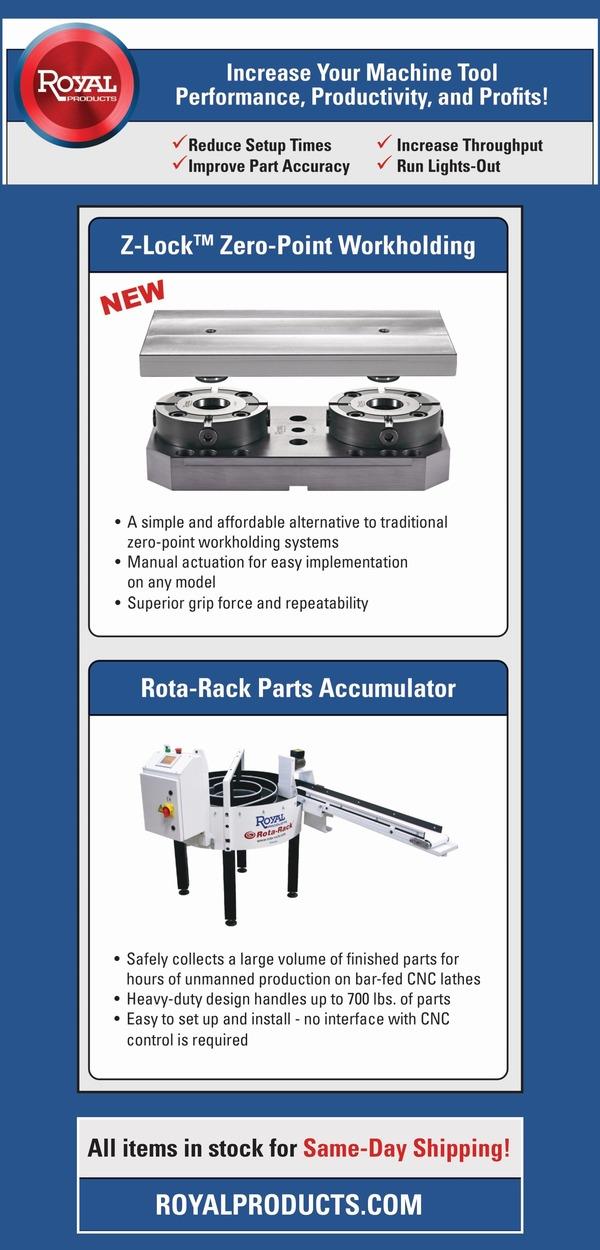

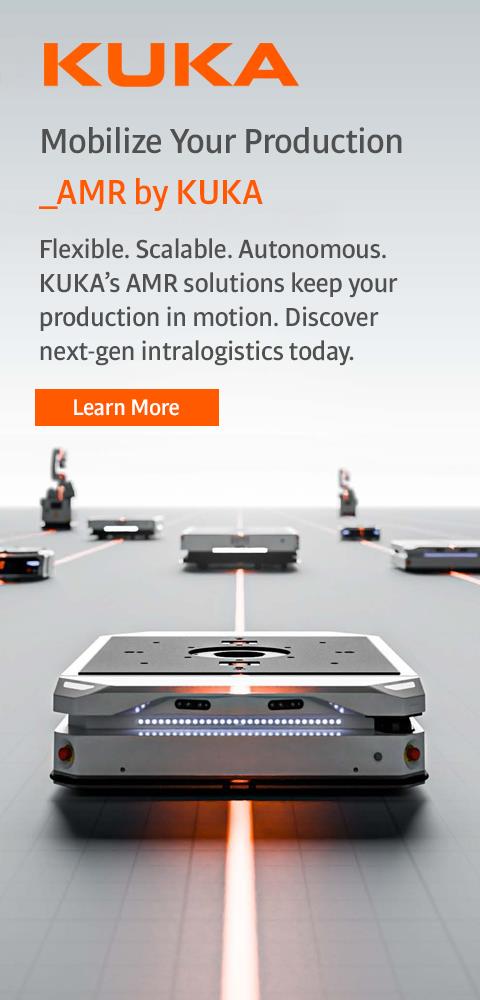
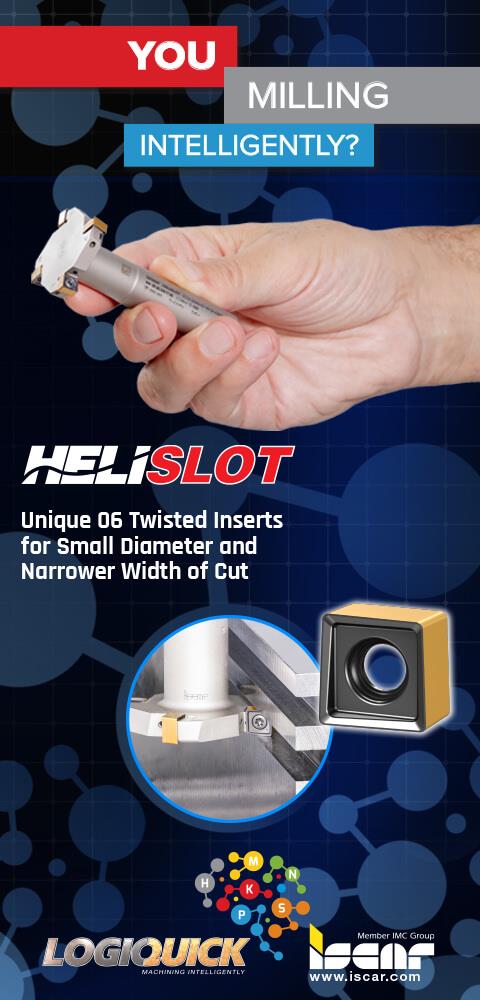
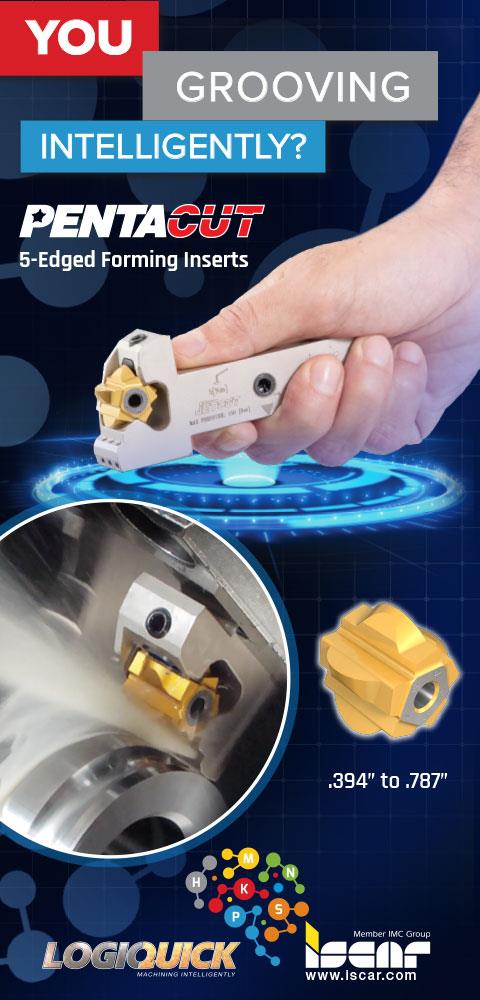
Aluminum Blackening Process
November 1, 2014
The LUMICLAD aluminum blackening process from Birchwood Technologies is designed to produce a black finish on electrical card cages and card cage components while maintaining predictable chassis grounding. It is suitable for military, commercial and industrial applications.
"The LUMICLAD finish is electrically conductive and clean to add value to all types of aluminum electrical / electronic components and assemblies," said a company spokesperson. "The LUMICLAD process forms a non-dimensional black oxide finish on all aluminum surfaces that is durable, clean and tightly adherent to the metal substrate. The LUMICLAD process develops a uniform coating thickness of .000060 inches (1.5 micron) that will not close down hole diameters or change critical part dimensions. The smooth black finish has a slightly porous crystal structure that absorbs an optional topcoat, such as a dry-to-touch sealant, light oil or clear polymer.
"Before the development of the LUMICLAD process, black anodizing had been the only viable blackening option for manufacturers of aluminum components. While the anodized finish is extremely durable, it is not practical for applications requiring electrical conductivity.
"By utilizing a conventional immersion seven-tank process line, the LUMICLAD process is easy and safe to operate so that manufacturers can operate it in-house. This process can be utilized for jobs of any size component, large or small, and for large quantities of smaller parts. Parts can be finished on racks as well as in baskets or barrels without the need to individually clamp each part.
"LUMICLAD expands a designer's options with its chassis grounding and quality black finish features. It is easy and safe to operate, streamlines workflow while providing low operating costs and high quality."
For more information contact:
Birchwood Technologies
7900 Fuller Road
Eden Prairie, MN 55344-9702
952-937-7931
info@birchwoodtechnologies.com
www.birchwoodtechnologies.com
< back