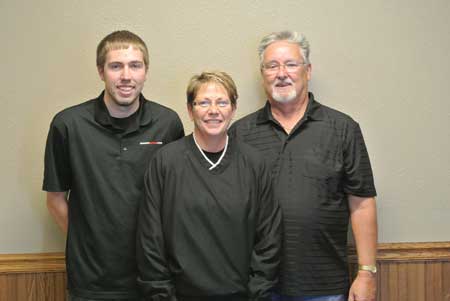
(l-r) Brock Buerger, Vicki Buerger and Dave Buerger.
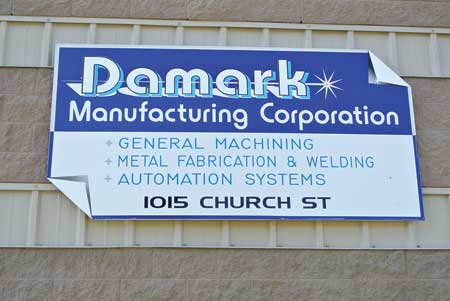
Damark Manufacturing in Lomira, WI, provides engineering services, CNC machining, CAD/CAM and 3D modeling capabilities.
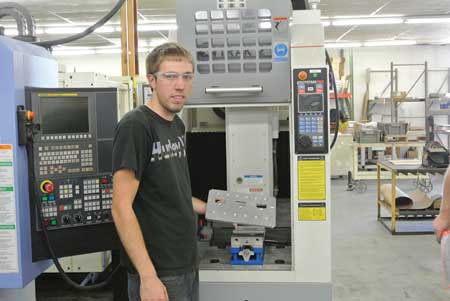
Sample part machined by a TRAK 2OP and Doosan Machining Center
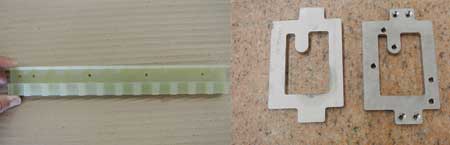
Part machined on a CNC mill (left) simultaneous with a part machined on the TRAK 2OP (right).
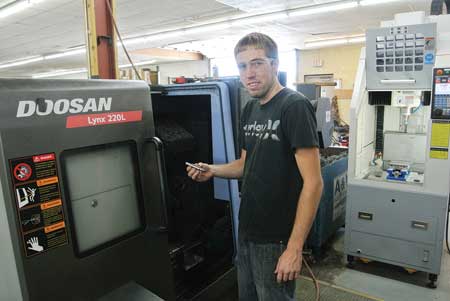
Sample part machined by a TRAK 2OP and Doosan Turning Center.
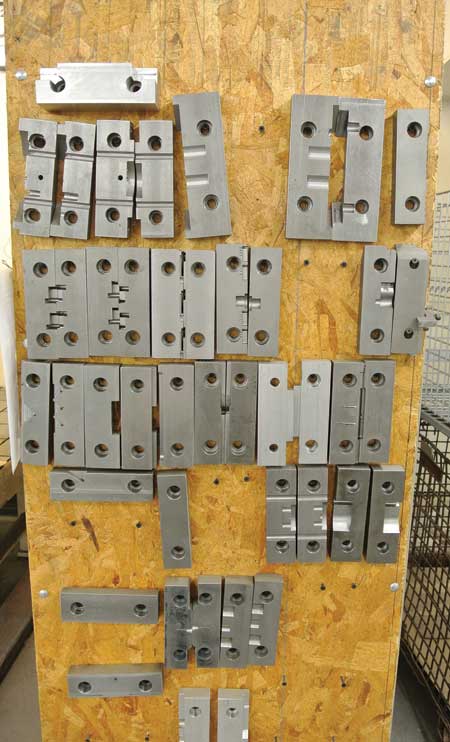
Soft jaw fixtures designed and built by Damark expedite part changeovers.
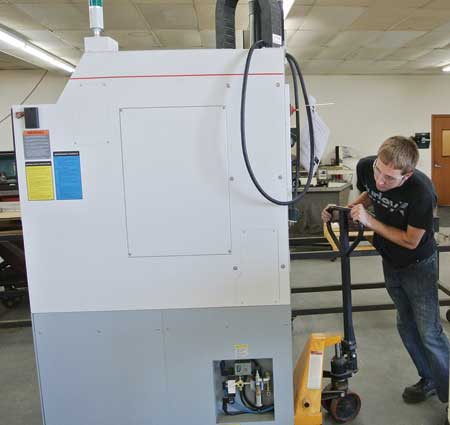
The portable TRAK 2OP comes standard with a pallet jack.
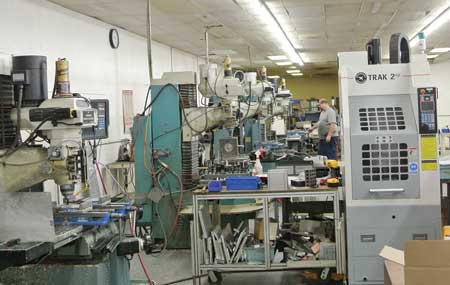
TRAK 2OP placed next to CNC mills for simultaneous machining of two different parts.
Keeping machined part work-in-process inventory levels under control is a challenge that many job shops face. Damark Manufacturing produces a large variety of low volume parts. Organizationally, the company groups similar machines together to perform batch processing - turning centers and lathes in one area and machining centers and mills in another. Over time, Damark Manufacturing observed that its work-in-process inventory levels were rising to unacceptably high levels due in large part to time consuming VMC changeovers. The company needed a solution.
The following solutions were considered:
- Changing routings from the turn and mill areas to the turn/mill machine - this solution was discarded because the company only has one turn/mill machine and its tool capacity cannot cost-effectively handle high-mix, low volume work.
- Procuring an additional turn/mill machine - this would address the issue but the implementation costs would have been prohibitive. "Not only would we have to spend at least $100,000 for a new, low-end machine (not including the cost of additional live tooling), we would have to then hire another highly skilled machinist to program and run it. Over time this additional machinist would cost more than the machine itself," said CEO Dave Buerger.
- Building quick changeover fixturing for the VMCs - although this was a viable solution, it was determined not to be optimal.
- Pooling similar jobs together in order to reduce changeover times - this idea was discarded because most of Damark Manufacturing's jobs have different due dates.
- Procuring a TRAK 2OP portable machining center - this new product from Southwestern Industries has an eight-station tool changer and runs ProtoTRAK conversational language programs and G-code. It is designed to bring an additional spindle quickly and easily to an operator idled by the cycle time of his primary machine.
Damark Manufacturing chose to acquire a TRAK 2OP portable CNC for second operations. "We placed it next to one of our turning machines and had the operator run both machines simultaneously. This enabled him to complete both the first and second operations in the same amount of time previously consumed by the first operation with no additional labor," said Buerger. "An operator can even run one part on one machine and simultaneously run a completely different part on the TRAK 2OP. Besides, the TRAK 2OP is considerably less expensive than a new VMC or turn/mill machine and it eliminated the option of providing our VMCs with quick changeover fixturing because we wanted to free up our VMCs to do higher level work."
The TRAK 2OP work table incorporates a built-in Jergens ball lock system that reduces changeover times. "Given our expertise, we will be able to design and build soft jaw/hard stop fixtures to make changeovers even more efficient," said Buerger.
Standard features of the Southwestern Industries TRAK 2OP portable VMC include:
- ProtoTRAK CNC technology with conversational language programming - also runs G-code programs. Programs can be generated either at the machine or remotely.
- 8-station automatic tool changer (BT30)
- Rigid tapping
- Coolant pump
- Pallet jack (machine can be moved by one person)
- Canned programming cycles including but not limited to pockets, profiles and bolt hole patterns.
Specifications:
- 2.5' x 4' footprint
- 3 HP, 6,000 RPM
- 18" x 15" work table with built-in Jergens ball locks
- 14" x 12" x 17" travel (x, y, z)
- 2,825 pounds
- 220 volts (3 phase)
- Minimum height to fit through doorway - 92" (Z cable carrier collapsed).
Damark Manufacturing calls the concept of placing a TRAK 2OP second operation machine next to a primary machine a "Work Cell on Demand." In six months with the TRAK 2OP, the company has moved the machine around the shop at least 15 times to create these temporary work cells. This has brought about an increase in throughput and a reduction of labor cost per part.
For a stainless steel cylindrical part with three flats, Damark used to batch process through turning (first operation) and milling/VMC (second operation) areas. After obtaining the TRAK 2OP, it was placed next to a turning center to form a Work Cell on Demand. This allowed Damark to reduce the labor required to produce 200 of these parts by six man-hours. Damark was able to reduce the milling operation set-up times by 50% via the TRAK 2OP Jergens ball lock system and its soft jaw fixturing.
Damark Manufacturing has also placed the TRAK 2OP next to the CNC mill area. "CNC mill cycle times can be as long as 10 minutes. These cycles create operator idle time which we now consume by having the operators run a completely different part, previously machined by the machining centers, on the TRAK 2OP," said Buerger. They complete two lots of two different parts in the same number of man-hours that it used to take for one lot of one part. "As an added bonus, we are able to use lower skilled labor to achieve these results because the TRAK 2OP is easier to program and run than a VMC."
Damark Manufacturing found that the quality of parts produced by the TRAK 2OP are at least as good as those obtained using previous machining methods. "In some cases, the quality obtained with a TRAK 2OP has been better than previous methods because cellular manufacturing decreases part handling," said Buerger.
Damark Manufacturing is a privately held company, founded in 1995 by Dave and Vicki Buerger. The business started out in a 1,700 square foot facility specializing in fabrication and repair. In 2003, it relocated to its current location in Lomira, WI. Through the years the company has added engineering services, CNC machining, CAD/CAM, 3D modeling capabilities and new equipment. It now operates in a 22,100 square foot building. Damark is capable of machining a wide range of materials including: steel, aluminum, phenolics, copper, brass, Inconel and titanium.
Damark began with Dave Buerger's belief that through honest practices, it could simplify business processes and create an innovative approach that would save customers money and offer responsive personalized care. The company is founded on the following principles:
- Provide innovative solutions that solve customers' problems.
- Be a responsive and trusted resource for our customers throughout the manufacturing process.
- Provide quality products through precision machining execution.
- Provide all team members an opportunity for growth.
According to the company, Damark Manufacturing refines the manufacturing processes it uses on a continuous basis. The result is a low risk source with controlled costs and high quality manufactured parts. "Damark is a valued source to manufacturing engineers and part procurement specialists because we pay close attention to details throughout the procurement process," said Buerger. "Quality is stressed to all our employees, who are some of the best in the business. Damark supports their efforts by providing the necessary tools and training to perform first piece and spot production inspections as well as statistical control techniques."
For more information contact:
Damark Manufacturing
1015 Church St.
Lomira, WI 53048
920-269-7825
www.damarkmfg.com
Bruce Meredith, Marketing
Southwestern Industries, Inc.
2615 Homestead Place
Rancho Dominguez, CA 90220
310-608-4422
info@southwesternindustries.com
www.southwesternindustries.com