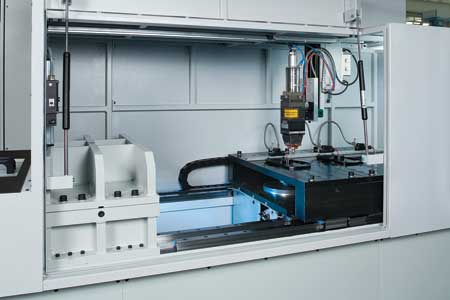
Machining area of the ELC 160 Laser Welding Machine for the welding of gearwheels. On its three stations the wheel assembly is pre-heated, joined and laser welded.
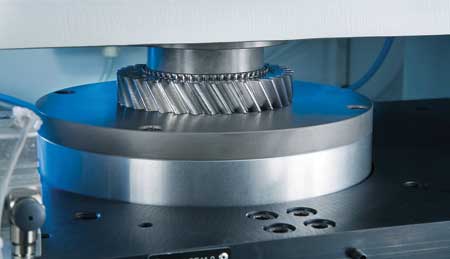
Joining a gear and a synchronous ring on the ELC 160.
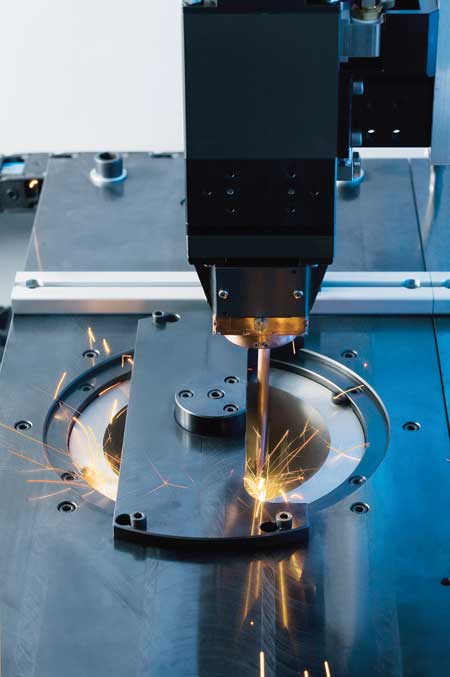
Laser welding a synchronous wheel onto a gear. The solid-state laser on the ELC 160 halves operating costs.
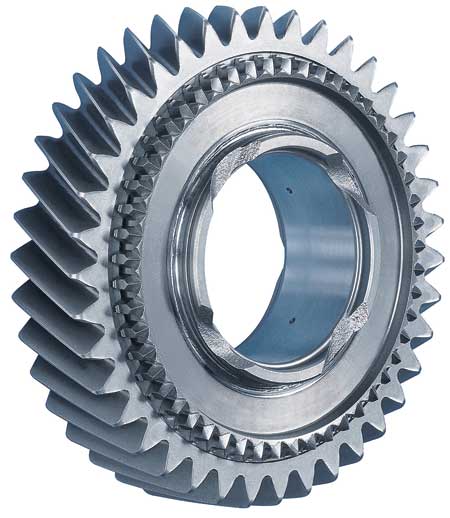
Laser-welded gearwheel.
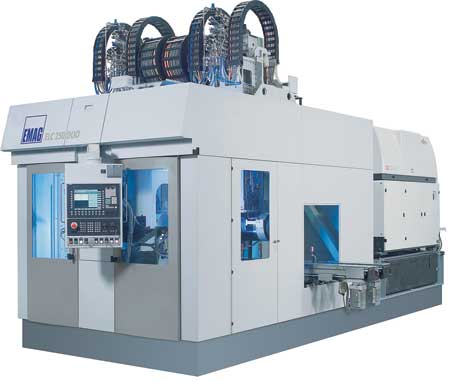
The ELC 250 DUO - a compact laser welding cell for the machining of differential housings. The DUO variant features two spindles. The twin-station operation allows for cycle time-concurrent loading and unloading of the work spindles.
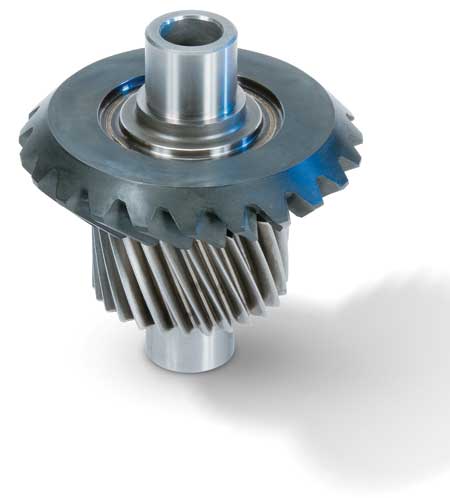
Laser welding the differential housing and the crown gear reduces weight by 1.2 kg compared to traditional assembly, according to the company.
From dual-clutch transmissions to the classic differential, modern transmission technology is a pivotal research sector in the automotive industry where designers optimize the functionality of gearwheels with new materials and altered geometries. These gearwheels are also required in ever larger quantities as the number of speed gears in many passenger cars continues to increase. "Laser welding is one innovation promoting effective processes and EMAG capitalizes on its knowledge in the production of transmission components with ELC series of laser welding machines that offer integrated solutions for processes with high output rates," said a company spokesperson.
A typical transmission component presents many challenges. Even a small wheel with an integrated synchronous gear represents a relatively complex design. To manufacture it efficiently and at the highest precision calls for two different parts to be produced separately and subsequently joined in a welding and joining process. "It is at this point in modern transmission manufacturing that laser welding comes into play," said Dr. Andreas Mootz, Managing Director of EMAG Automation. "The process allows manufacturers to concentrate a carefully dosed amount of the energy emitted by a laser beam on the welding point, minimizing possible warping yet still achieving high welding speeds. The EMAG welding process uses solid-state lasers. Whereas a classic carbon dioxide laser achieves an efficiency factor of just eight percent, EMAG laser welding technology has an efficiency factor of approximately 20 percent. Noticeably less power is used to achieve the same optical performance with solid-state lasers, reducing energy costs in production."
Single setup welding
Production sequences are integrated on the ELC system, beginning with a work spindle that uses the pick-up principle to load itself. Components are then clamped and pressed together in the joining press. According to the company, the clamping technology used ensures accurate positioning of the components, providing ideal conditions for the welding process. The stationary optic is designed to ensure operating safety and stability of both the machine and welding process. Depending on workpiece or material, the components can be induction-preheated prior to the welding process and brushed thereafter. Regardless of what is required, the process is completed in a single set up. The complete joining and welding process for a gearwheel takes 12 seconds, while the components for a differential are finish-welded within 40 seconds.
Laser welding advances light-weight construction
Differential housings show the possibilities laser welding technology opens in vehicle production. For some time now automotive companies have been replacing the screw-type connection between the differential housing and crown gear with a welding seam, resulting in a reduced material cost while the weight of the assembly falls by approximately 1.2 kg. "These kinds of savings are a significant advancement in light-weight construction within the automotive industry," said Dr. Mootz.
For more information contact:
Peter Loetzner
EMAG LLC
38800 Grand River Avenue
Farmington Hills, MI 48335
248-477-7440
info@usa.emag.com
www.emag.com
Southwest
AR
Ken Pope
EMAG LLC
256-642-6842
kpope@emag.com
www.emag.com
TX, OK, LA
Ric Lorilla
EMAG LLC
248-595-1530
rlorilla@emag.com
Southeast
VA, NC, SC, GA, FL
David Fitzgerald
EMAG LLC
248-595-1117
TN, AL, MS
Ken Pope
EMAG LLC
256-642-6842
kpope@emag.com
www.emag.com
Northeast
PA, NY
Kirk Stewart
EMAG LLC
248-996-4703
kstewart@emag.com
ME, NH, VT, MA, RI, CT, NJ, DE, MD
Jonathan Chomicz
EMAG LLC
248-497-8526
jchomicz@emag.com
WV
Ken Pope
EMAG LLC
256-642-6842
kpope@emag.com
www.emag.com
Midwest
IN, OH
Kirk Stewart
EMAG LLC
248-996-4703
kstewart@emag.com
MI
Geoff Fuller
EMAG LLC
248-632-2021
gfuller@emag.com
ND, MN, WI, SD, NE, KS, IA, MO, IL
Bill Konetski
EMAG LLC
612-804-0857
bkonetski@emag.com
KY
Ken Pope
EMAG LLC
256-642-6842
kpope@emag.com
www.emag.com
West
Arnie Sugiyama
Caltec International
19801 Hamilton Ave
Torrance, CA 90502
310-527-4110
arnie@caltecusa.com