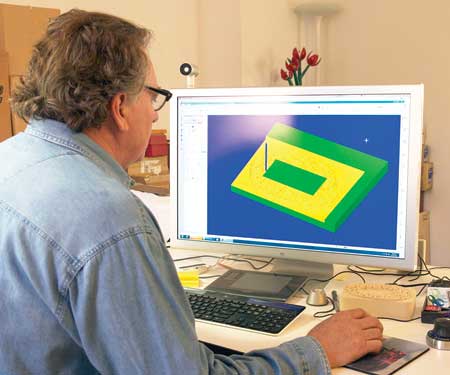
Mastercam Software (from CNC Software, Tolland, CT) is designed for use in factories and machine shops where PCs rule. As an artist, Curci is more comfortable using a Mac. So, he uses Parallels Software to create a simulated environment where Mastercam can thrive alongside his Mac-based art software tools.
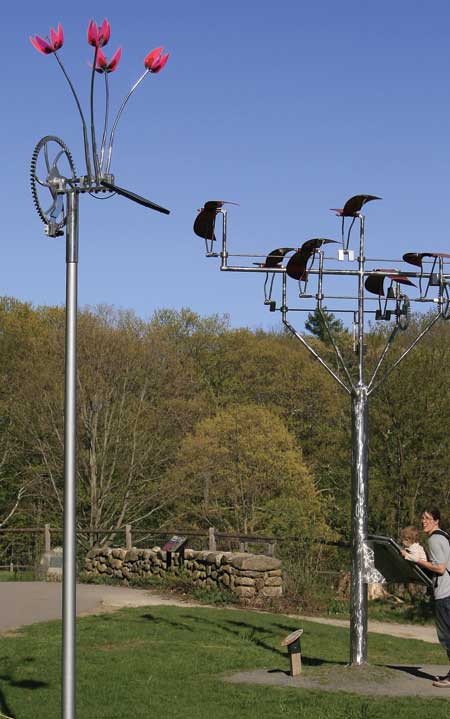
Kinetic sculptures by Gregory Curci.
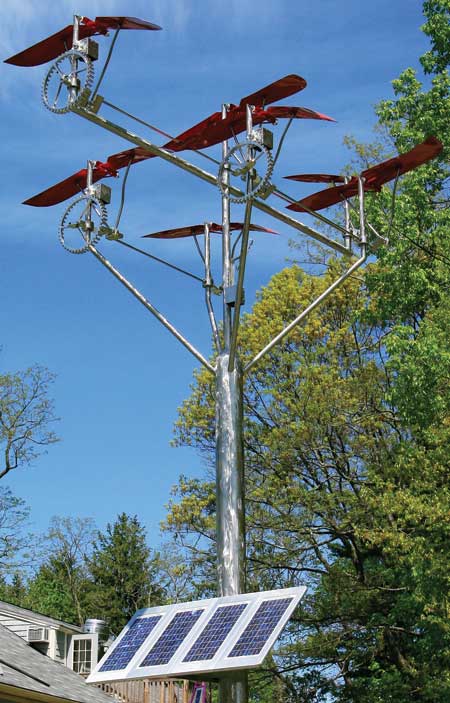
Kinetic sculptures by Gregory Curci.
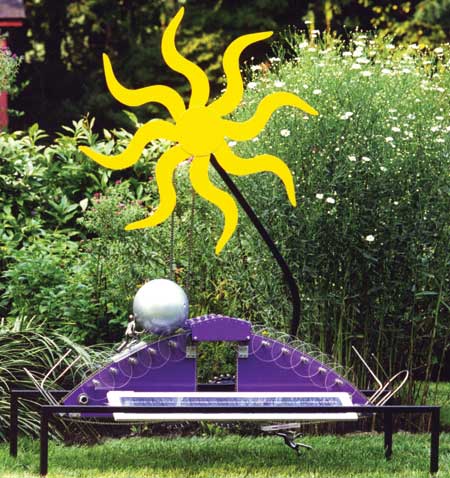
Kinetic sculptures by Gregory Curci.
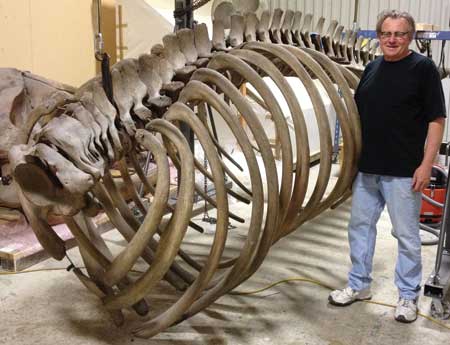
After hanging in Boston's New England Aquarium for decades, this whale skeleton was beginning to fall apart. Curci used his art skills to create new handmade connectors and put all the pieces together again. Mastercam was used on an emergency basis to create special fixtures overnight. These were used to divert the wires used for hanging the exhibit away from mischievous visitors who had discovered that they could grab them and make the beast swing.
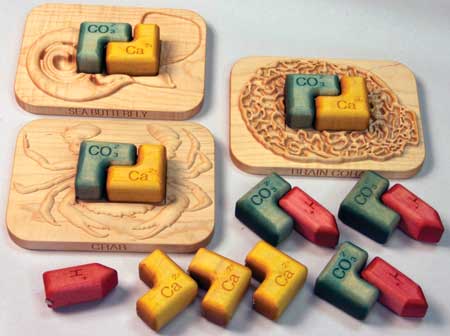
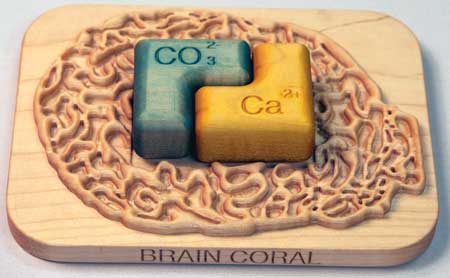
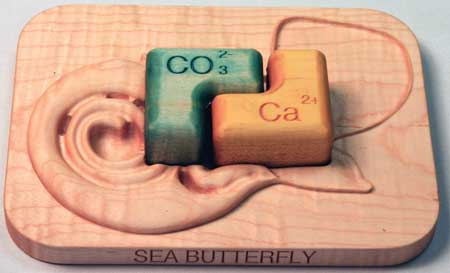
Curci used Mastercam Art software to create programs for manufacturing these puzzle pieces for a New England Aquarium educational program funded by NOAA.
If you have ever been to Audubon Society's headquarters in Lincoln, MA, and have seen the solar-powered Sunbirds sculpture, or pondered the 2,000 lb. right whale skeleton hanging from the ceiling of the New England Aquarium, or tuned into the PBS episode of "Curious George" where kids were taught how to make their own solar powered vehicles, then you have come in contact with some of the handiwork of kinetic sculptor Gregory Curci.
Curci believes there are two kinds of artists - those who aspire to make a living with their skills and creativity, and those who actually do it. He is one of the latter, supporting himself and family by nothing else but the work he loves for more than three decades.
Curci trained as a sculptor in art school, paying his way by hand lettering signs, truck panels and billboards. After graduation in 1976, he moved to Boston where he put food on the table by working as an apprentice pattern maker. This was an experience that would serve him well, because it exposed him to metallurgy and manufacturing concepts that he would later employ to sustain his career as an artist. Curci was also producing works of art on his own time, and by 1979, sales had grown to a point where he felt he could strike out on his own as an artist with a studio on Boston's Charles River. He never looked back.
Bypassing Productivity Roadblocks
"My process typically starts in my sleep," said Curci. "I dream up an idea. I am an older guy and an artist and things always begin on paper for me. I get some ideas, cut some cardboard, pound in a few nails and string up a model of my concept. Then I go into fabrication."
For a couple of decades, Curci produced his works of art entirely with manual tools and equipment, but he was becoming frustrated because his mind was capable of dreaming up creative ideas much faster than he could make all the pieces required to implement them. So 15 years ago, much to the amazement of his wife, he went out and spent $45,000 on a computer numerical control (CNC) milling machine for his studio. That expense was way out of proportion to the cost of his usual tools (e.g., a pocket knife and hammer and chisel) and there was a steep learning curve. However, that year he learned to program his mill manually and produced enough additional art to more than recover his investment.
Ten years later, the artist hit another productivity roadblock. Manual programming of his mill, particularly pieces of increasing complexity, was slowing him down. For a number of years he had considered purchasing computer aided manufacturing (CAM) software to semi-automatically generate manufacturing programs for his visions, particularly those generated with Adobe Illustrator drawings on his Macintosh computer.
When he learned that Mastercam CAD/CAM software (from CNC Software, Inc., Tolland, CT) could import Adobe Illustrator files to be used as the starting point for creating programs for his mill, he jumped in and purchased a seat of the software. This was another purchase way out of proportion with the usual artist tools. However, he once again experienced a leap in productivity comparable to the boost he got when he first started using his CNC mill.
Curci discovered that he could simulate the PC environment required for running Mastercam on his Mac using parallel software. He drags his Adobe Illustrator file from his Mac desktop into Mastercam running in parallels where he can begin generating programs for his CNC mill immediately. He said, "This process allows me to start manufacturing parts in short order. While they are running, I can be designing more parts to keep my project going. This approach transforms my mill into a non-salaried assistant and takes me to another level."
One of the first projects he created, with the help of Mastercam, was a kinetic sculpture for the Audubon Society's headquarters in Lincoln, MA. The design featured seven birds in continuous solar-powered flight. Curci had to make 14 individual wings. He designed one wing in Illustrator and imported it into Mastercam. He quickly generated the CNC toolpaths for making the wing on one side. Then, he pasted that model into another file and simply flipped it to get the toolpaths for the opposing wing. While the CNC worked tirelessly to cut all these, he turned his attention to other aspects of the project.
Buoyed in a Tanking Economy
In 2008, when the economy tanked, many of Curci's customers disappeared. However, the ones that stuck around started coming to him with projects that he could not have made without Mastercam. This allowed him to stay in the game and still make money.
An example of the type of projects, which have become an expanding facet of his business, involves restoration of artworks for museums and other public places. Mastercam gives him the tools he needs to reverse engineer and manufacture antiquated components that he needs for restoration work. He has also become involved in maintaining some of his older works that now have been located in public spaces for many years.
Mastercam gives him the ability to efficiently manufacture many of the replacement parts required for these jobs. In the future, Curci may also give his public art customers computer files for remanufacturing components of his work. If they stand the test of time and are still being enjoyed 100 years from now, maintenance engineers can have weathered components remanufactured at local machine shops, simply by giving them the computer files.
Recently, Curci was asked to restore a 2,000 lb. whale skeleton that had been hanging for decades high above spectators in a large open area at the New England Aquarium in Boston. A lot of original hand made iron mechanical elements that held the whale together were damaged when the skeleton was put in storage during a building renovation. Curci recreated these in the same fashion. There were also a great many brackets and plates that Curci machined automatically on his mill. After the riggers hung the restored skeleton from the 70' high ceiling over the penguin tank, some visitors discovered that they could grab the cable from which it was suspended and make it swing. Something had to be done quickly.
Curci was called to the scene to inspect the problem. He returned to the studio and designed a special bracket and mounting plate and programmed his mill to cut the pieces that evening. The next morning the riggers used his custom hardware to divert the wire out of harms way. Curci said the ability Mastercam gives him to respond quickly to urgent requests like these inspires the loyalty of customers who, in turn, reward him with additional projects.
Access to Complexity
The New England Aquarium recently turned to Curci to design a group of carved relief panels that could be used within the context of a traveling exhibit to schools to teach children how the rising acidity of the ocean is affecting various sea animals. The program was sponsored by the National Oceanic and Atmospheric Administration (NOAA). Curci was asked to create interlocking puzzle pieces that kids could assemble and learn about how diminished calcium carbonate is causing the shells and skeletal structures of coral, mussels, oysters and other sea animals to thin out.
The museum gave Curci black and white photos of the sea creatures that would be included in the puzzle. He scanned these photos into Adobe Illustrator to use as the basis for the puzzle's design. Then he opened the Illustrator file with the Mastercam Art module, where he programs his CNC mill to carve out accurate relief sculptures of the sea creatures on wooden puzzle pieces.
He said, "I could have easily done these by hand. But there were five different pieces in the puzzle and I had to produce five identical sets of each. This is simply a project that I could not have done without Mastercam. What is more, the Aquarium may license this program to other museums. Mastercam gives me the ability to reproduce more puzzle pieces on a fast turn basis, as they are needed."
He concluded, "Mastercam allows me access to complexity. Programming a CNC mill manually, you have to pay attention to every detail while programming. It is time-consuming and sometimes you compromise on your design to make it simpler to program. Now with Mastercam, it is so much easier to design exactly the part that I want and create CNC programs that will produce the pieces I need with great fidelity. For me it has become another tool that I use in my studio with increasing familiarity, just like I use my pocket knife."
For more information contact:
CNC Software, Inc.
671 Old Post Road
Tolland, CT 06084
860-875-5006
info@mastercam.com
www.mastercam.com