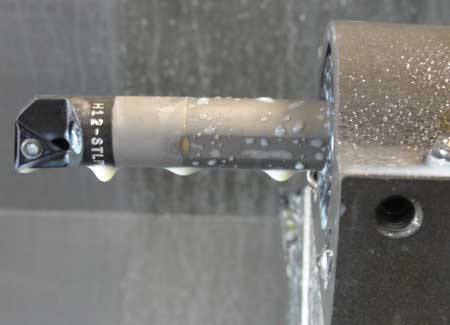
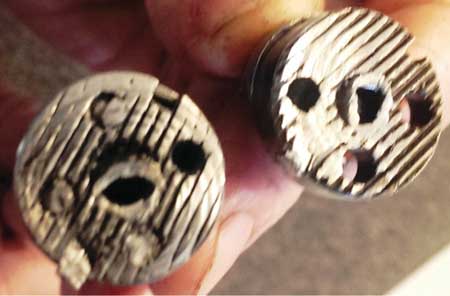
Catastrophic failure of serrated connection
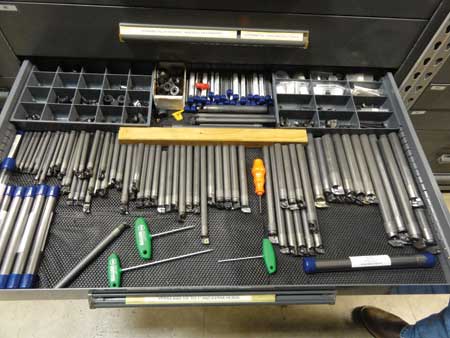
End user retrofitted more than 100 worn and broken carbide shanks to Versabar
"Versabar Tools, LLC is introducing its high performance Versabar Modular Boring Bar System. The system provides ultimate versatility and affordability. Modular bars range in size from .375" - 1.500" and are available in 4xD and 8xD lengths, both steel and carbide shanks. The system features 38 modular head options (RH+LH) suitable for boring, profiling, threading, grooving and back facing. Pockets accept standard ISO/ANSI inserts, and right and left-hand head versions mount to the same bar. Reduction adapters facilitate utilizing smaller diameter heads on a larger diameter bar," said Roger Little, Versabar Tools, LLC.
Versabar System Benefits
Unlike fixed-pocket bars, Versabar is multipurpose, adaptable for a variety of machining applications. Versabar heads are quick-change (using only one screw) and the uniquely designed socket connection is strong and reliable. Inter-changeability saves time, especially in the event of a pocket crash or when part changeover requires using a different insert configuration. The bar remains in the turret and the alternate Versabar head can be mounted in about a minute, without sacrificing program offsets. Faster changeover times allow for a reduction in batch sizes, work-in-process, inventory and even lead times.
An exclusive feature of Versabar is the 4xD stub carbide shanks. The carbide shank is nearly 3x more rigid than the traditional steel counterpart (Young's modulus), which makes it superb for those challenging applications where steel shanks produce chatter. The added rigidity also allows for program modifications that can optimize cycle time, especially when machining difficult materials and when threading (fewer passes). With bar deflection eliminated, the following benefits can be realized:
- Increased dimensional accuracy
- Enhanced surface finish
- Elimination of chatter (critical when threading)
- Extended insert edge life
- Reduced scrap.
Increased rigidity may also facilitate utilizing a reduced bar diameter (possibly two sizes smaller) to machine inside a given bore. The smaller shank can enter a smaller bore; therefore machine a broader range of parts. Furthermore, increased bar rigidity enhances the performance of aging equipment, especially noteworthy machining internal applications.
Why Replace Fixed-Pocket Bars?
Integral steel shank bars are limited to one type of machining operation. Pocket crashes require removing the shank from the turret (sacrificing offsets) that can involve up to 30 minutes of downtime. Savings from the modular feature, and enhanced performance credited to rigidity, are considerations that offset the cost of the 4xD shank.
Integral carbide shank bars have (by necessity) brazed heads, adding the unwelcome variable of inconsistent pocket hardness. Pocket hardness is a function of (i) the type of steel the head is produced from, and (ii) the method and duration of the cooling process. Sophisticated manufacturers may (or may not) employ techniques that encourage hardness retention, however, net hardness remains a variable. Low cost manufacturers (including the typical repair shop) typically employ the most expedient process. This process involves producing the head from typical alloy steel, heating the assembly to slightly above silver-solder melt point (1,300 °F), then slow cooling the assembly to avoid braze strains (stress cracks) from forming in the shank. Unfortunately, slow cooling anneals the head resulting in net hardness as minimal as 200-240 (BHN). Experienced machinists may realize this when they test pocket hardness with a file, but the results remain subjective. At the end of the day, inconsistent pocket hardness is an unwelcome variable with integral carbide bars, negatively impacting their useful life.
Soft Pockets Are Problematic
A soft pocket is susceptible to deformation from the forces of insert corner snaps. Tiny gaps soon develop between the insert and pocket wall, reducing insert stability, allowing insert shifting and vibration. This phenomenon encourages further (and more dramatic) insert corner snaps. Experienced operators insert shims into the gaps of soft pockets (out of desperation) to extend the life of the high cost bar. This can be problematic, as shifting of the insert in the cut can result in scrapped parts, and render the pocket unusable. Soft pocket threads stretch and tear from the demands of hardened insert screws. Shavings from certain hard materials may create erosion around the pocket area. In that Versabar heads bolt on, the variable of pocket hardness is eliminated; the heads provide improved performance throughout their useful life.
Modular Systems Comparison
The most popular modular system utilizes a serrated connection; the smallest diameter available is .625" (16 mm). The Versabar connection design allows for diameters as small as .375" (10 mm). The serrated connection works well, however should the serrations of either the head or bar get damaged (nicked, bumped) misalignment can occur. The misalignment may go unnoticed by operators. This can allow vibration, which may contribute to holding screws loosening when in the cut. Should this happen, it can cascade into a catastrophic event for both the head and bar (see picture of catastrophic failure). Also noteworthy is that capscrews attaching the head are by necessity small (in sizes 1.00" and smaller) with hex sockets that are prone to strip out, contributing to downtime (removal of the bar from the turret to drill out the screws). Instead of serrations to position the head, the Versabar connection utilizes a rectangular drive key and socket, with a more robust singular torx screw, mounted axially at an angle along the centerline of the bar.
The now generic, boss/bore interchangeable head system remains the standard on many CNC turning centers in the U.S. The connection utilizes a boss (head) and bore (bar) with a bolt pattern of three attaching capscrews, with a drive pin. The connection is not suitable for sizes below 1.00" diameter. Positioning of the head depends upon the drive pin, which is inherently small. Forces from a typical pocket crash can shear the drive pin, making the head unusable. In extreme cases capscrews shear, allowing the head to rotate, damaging the bar connection. Again, the Versabar key and socket design does not depend upon the limitations of a drive pin to position the head, and it incorporates a more robust holding screw.
Versabar Retrofit Program
Shops with a collection of worn, broken or seldom used (outdated pocket) carbide bars ranging in size from .375" - 1.50" can place these expensive tools back in service, for a fraction of replacement cost. Once retrofitted with the Versabar connector, the shanks become modular, accepting the full array of Versabar heads. Over time, the only maintenance may involve the occasional re-placement of the Versabar connector. The shank itself has an unlimited life. Should it break, it can become a stub length bar.
The Versabar Retrofit Program provides three major benefits for end users:
- Savings of up to 65% compared to purchasing new bars
- Value is restored to existing bars, maximizing investment
- Versabar new shank purchases are reduced.
Authored By Roger Little, Versabar Tools, LLC
For more information contact:
Roger Little
Versabar Tools, LLC
P.0. Box F
1227 FM 646 N
Dickinson, TX 77539
409-440-8106
rlittle@versabartools.com
www.toolsaverinc.com