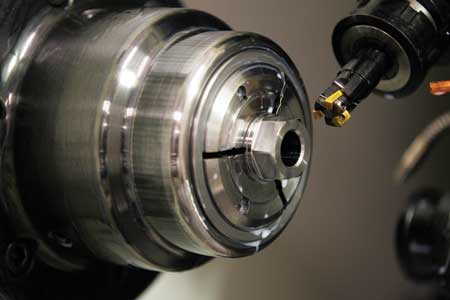
Penske Engine shop's Mazaks include a QUICK TURN NEXUS (QTN) 200MY multitasking machine with turning, milling and Y-axis capabilities. The machine eliminates the need to move parts from one machine to the next for their various operations.
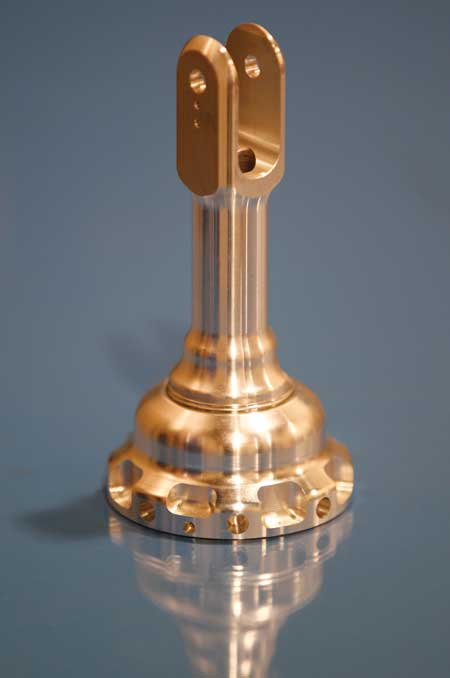
An INDYCAR two-part suspension component done on the Mazak QTN 250 MSY multitasking machine. The challenges are the component's five different features requiring the use of five different extended-length live tools in the machine's turret. Between the two parts of the component Penske uses every axis available on the QTN 250 MSY.
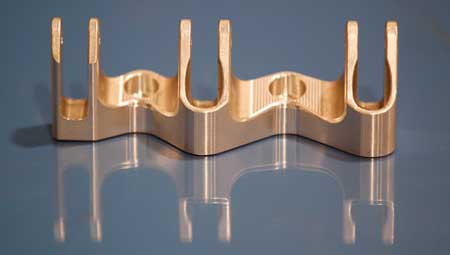
According to Matt Gimbel, Production Manager at Penske Racing, weight reduction usually transforms simple parts into complex ones in terms of features and geometries. "While radiusing a part's corners and edges or machining out pockets where possible may reduce weight, doing so means multiple operations and more often than not requires 5-axis machining. Plus, combining multiple parts that were once individual components assembled together into one machined block also increases part complexity."
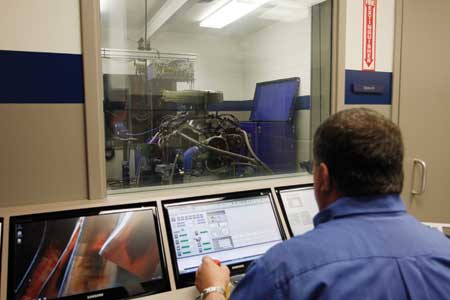
A race car's engine is tested at Penske Engines Co. This facility in Concord, NC, is one of the two Penske Racing Team shops using machines tools from its technology partner Mazak.
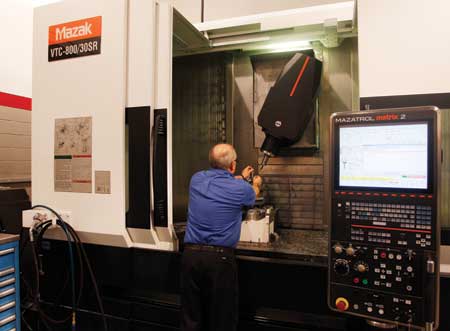
One of the largest Mazak machines at Penske's Mooresville facility is a 5-axis Vertical Traveling Column (VTC) 800/30SR VMC with swiveling B-axis spindle, full traveling column and a 5,500-lb. maximum table load. As parts designs become more complex, the machine allows the team to access all of a part's features in one set-up.
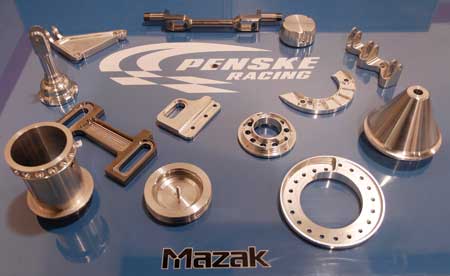
Penske machines many chassis parts on its Mazaks, including front spindles, front and rear hubs, idler arms, pitman arms, steering shafts, various mounting brackets (both engine and transmission) and various other components. Half of these components are aluminum, while the remaining are made from particular alloys or stainless steels with tolerances that range from +/-0.002" to those that must be held to within 0.0002".
Two races happen every week for Penske Racing in Mooresville, NC, and the team strives to win both. One is the race at the actual track, while the other is what Penske refers to as the "manufacturing race." According to the company, this is the crucial race where highly engineered components that will give the team a competitive advantage must go from design to reality and get to the racetrack as quickly as possible.
Every racing season, Penske's two machine shops - one in Mooresville and another, the Penske Engines Co., in Concord, NC - support all the Penske racing teams. "The shops produce components for 65 NASCAR chassis and eight INDYCAR team chassis and pump out about 45,000 race car parts per year," said a company spokesperson.
In its part manufacturing operations, Penske continuously drives to shorten leadtimes as well as contend with frequent race-day component emergencies as quickly as possible. These are the instances where crew chiefs at the track will relay necessary component design changes or tweaks according to that week's particular track or racing conditions. The Penske machine shops must then interrupt current operations and produce the emergency parts within hours for shipment to the track that same day.
"Whether under typical or emergency production conditions, Penske is in a constant state of redesign because its philosophy is that parts can always be improved upon," said the spokesperson. "Inventory is basically non-existent at Penske because part designs can be outdated after a week to a month."
Matt Gimbel, Production Manager at Penske Racing, likens the team's machining operations to those of a high-mix/low-volume job shop. "Like those shops, Penske tries to retain all its processes in-house," he said. "As do those job shops, the team also relies heavily on the latest, most advanced machine tool technology for the speed, precision and processing flexibility needed to keep pace within such a hectic production environment."
For more than 20 years, Penske has been partners with Mazak for not only the team's machine tool technology but also training and application support. The team's Concord shop has six Mazaks, and the Mooresville shop has five. Penske's driver racing suits sport the Mazak logo, as do the team's race cars.
"We do not just partner with any organization," said Gimbel. "They must be industry leaders that can get the job done and work with us in a win-win situation. The technology of our cars and components continue to progress in precision and complexity, which, in turn, makes them tougher to manufacture. To stay ahead, we rely on Mazak machines with multitasking, 5-axis and Done-In-One capabilities as well as large tool storage capacities, pallet changers and easy programming for even our most complex of parts."
The recently added Mazaks at Penske's Engine shop include a QUICK TURN NEXUS (QTN) 200MY multitasking machine with turning, milling and Y-axis capabilities; VERTICAL CENTER NEXUS (VCN) 510C/50 (50-taper spindle) and VCN 410B Vertical Machining Centers (VMCs); and an INTEGREX e-410H 5-axis multitasking machine with C-axis turning spindle and B-axis milling spindle.
The seven-person shop machines many chassis parts, front spindles, front and rear hubs, idler arms, pitman arms, steering shafts, various mounting brackets (both engine and transmission) and various other components. Half of these components are aluminum, while the remaining are made from particular alloys or stainless steels with tolerances that range from +/-0.002" to those that must be held to within 0.0002".
Penske builds its cars at the Mooresville location, and five Mazaks reside at that facility's seven-person machine shop. The largest machine is a 5-axis Vertical Traveling Column (VTC) 800/30SR VMC with swiveling B-axis spindle, full traveling column and a 5,500-lb. maximum table load. The others are a VCN 510C-II with a two-pallet changer and a VCN 410B-II; a QUICK TURN SMART (QTS) 250 Turning Center; and a QUICK TURN NEXUS (QTN) 250-II MSY multitasking machine with twin turning spindles together with milling and Y-axis capabilities.
"Part designs originate at the Mooresville facility, and several factors can trigger either the redesign of an existing part or the development of an entirely new component," said the spokesperson. "These include an official racing rule change; new information about a specific track (loads, aerodynamics, etc.); a previously supplied component now being produced in-house; and opportunities to simply improve a component in terms of performance, weight reduction or fit and finish."
"There are components that we have improved upon as much as possible," said Gimbel. "But then a rule change occurs, and it creates a ripple effect throughout the car's parts, opening up whole new opportunities for further improvements. Most often, weight reduction is the catalyst for part changes. We constantly work to reduce overall car weight or to transfer it from locations higher on the car to those lower on the car, known as ballast areas, that are closer to the track surface. On race cars, low weight is good, and high weight is bad."
However, according to Gimbel, weight reduction usually transforms what were once simple parts into those that are quite complex in terms of features and geometries. "While radiusing a part's corners and edges or machining out pockets where possible may reduce weight, doing so means multiple operations and more often than not requires 5-axis machining capability. Plus, combining multiple parts that were once individual components assembled together into one machined block also increases our part complexity."
On the Cup Series side, Penske tries to make as many parts as it can in-house. In addition to providing a competitive advantage - running stronger, lighter parts than the competition - in-house production gives the team more control over quality and helps increase its manufacturing speed and flexibility.
"Without our Mazak machines, we would be really hard pressed to truly benefit from producing a part in-house," said Rick Huneycutt, Machine Shop Manager at Penske Engines Co. "Fortunately, we have the advanced machining capability needed to produce parts better and faster than our suppliers, which makes bringing parts in-house well worth our the efforts."
Huneycutt attributes much of Penske's part processing ease and flexibility to the Mazak machine CNCs. The team can seamlessly switch part production from one Mazak to another if needed because the machines are basically the same in terms of a programming platform as well as other components such as standard spindle sizes and types. "The Mazak controls contribute significantly to shortening part changeover times," said Huneycutt.
At Penske, job changeovers can happen two or three times a day on certain machines because lot sizes are often well under 50 parts. On its QTN 200MY, for instance, Huneycutt and his crew change over from one job to the next as many as six times in the course of a day, depending on part prototyping and production needs.
"We often use dovetail fixturing, quick-change chucks and other special techniques to also help shorten set-up times and speed job changeovers," said Huneycutt. "And with the large 40- to 80-tool storage capacities on several of our Mazaks, we eliminate the time wasted loading the various tools for each particular job. The more tools in the carousel, the faster we go from one job to the next, the quicker we get back in the cut once a part is fixtured in the machine and the more uninterrupted production we gain."
Some of Penske's parts require as much as 95 percent material removal while others only 35 percent. Machining cycle times can range anywhere from one minute for simple parts to 12 hours for those with multiple contoured surfaces and requiring as many as 30 tool changes per part.
"Because jobs and parts change constantly, Penske lacks the luxury of time necessary to run test parts in efforts to fine-tune cutting speeds and feeds," said the spokesperson. "Instead, the team relies on graphics simulations within the Mazak controls to determine exactly where speeds and feeds can be optimized even before a part is actually loaded onto a machine."
Penske will also batch run jobs together on its Mazaks whenever possible to not only shorten cycle times but to also gain unattended production. Instead of running one part at a time, the team sets up machines with multiple-part fixturing and loads two parts - each with somewhat longer cycle times - or as many as eight shorter-cycle time parts for long hours of lights-out production.
"On our Mazak VCN 410B-II, we may, for instance, machine four brake caliper mounts at once in a solid 14 hours of unattended in-the-cut time," said Jeffery Baker, Machine Shop Manager at Penske's Mooresville facility. "Or we have the option to use our VCN 510C-II with the two-pallet changer and run the machine unmanned. This frees up the machinist to potentially man a second machine. Initially, we would only use the pallet-changing capability for larger lot size jobs, but now we will also set up each of the machine's pallets with completely different smaller lot size jobs to run them unattended as well. In fact, we often mount a fourth axis on one of the pallets to expand our part processing options even further.
According to Baker, Huneycutt and Gimbel, Penske's machining needs continue to change. All agree that parts are becoming larger and even more complex as separate part assemblies are combined and machined from single solid pieces of raw material. For this reason, the team has set its sights on larger platform machine tools from Mazak that will provide the necessary work envelope sizes together with multitasking and 5-axis machining capabilities.
"It is a much more level playing field in racing these days," said Gimbel. "All the cars are basically equal in performance, so any little improvement or advantage could put a team over the finish line first."
For more information contact:
Tasha Riddell
Mazak Corporation
P.O. Box 970
Florence, KY 41022-0970
859-342-1700
triddell@mazakcorp.com
www.mazakusa.com