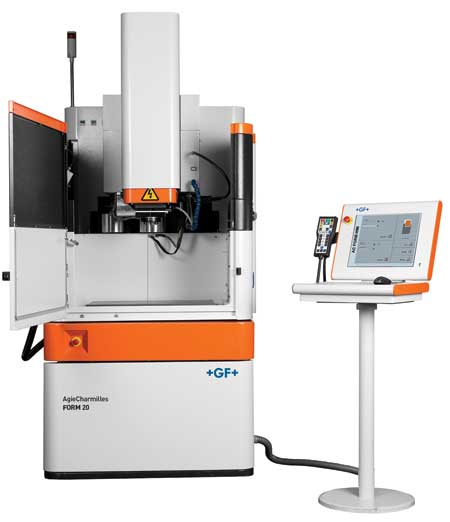
GF Machining Solutions' FORM 20 iRTC Sinker EDM sports the company's recently developed AC Form human machine interface (HMI) that allows new EDM operators to quickly learn and run the machine.
GF Machining Solutions' FORM 20iRTC sinker EDMs is one of the first machines to sport the company's recently developed AC Form human machine interface (HMI) that centers on user friendliness and intuitiveness to shorten the learning curve for beginner EDM operators. The company recently demonstrated the FORM 20 burning deep-cavity ribs into an automotive mold core to show how the system reduces overall burn time from over four hours down to a little over two hours for such parts.
The FORM 20iRTC machine features enhanced connectivity capability and performance within a compact design. It is engineered for industries such as general mold and die, aerospace, automotive and communications technology.
"Based on studies with numerous mold shops, GF Machining Solutions developed its GFAC HMI FORM CNC control, which streamlines moldmaking operations," said a company spokesperson. "As a direct result of those studies, the organization and layout of screens within the interface make it easy to use, especially for inexperienced operators. For beginners, the interface is intuitive and uncomplicated, allowing new operators to quickly learn it and confidently run the machine."
From simple Z-axis-level measuring to rotating workpieces around machine C-axes, the most common measuring cycles are also integrated into the AC Form HMI. Manual adjustments and alignments to workpieces are unnecessary, so non-burn times are reduced. According to the company, novice machine operators are able to achieve expert die-sinking EDM results.
Additionally, as a Windows-based platform, the FORM 20 seamlessly integrates into workshop management systems. Other new features, including GF Machining Solutions' eConnect, eSupervision and eTracking, are designed to further boost machine functionality for process control and outside system connectivity.
"At the heart of the FORM 20 is GF Machining Solutions' proprietary, high-end Intelligent Power Generator (IPG) with built in quality-boosting and cost-saving intelligence," said the spokesperson. "With every machine pulse, the 70-amp generator on the FORM 20 continuously optimizes the EDM process and reduces electrode wear as well as provides extremely uniform surface finishes. The machine reliably generates surface finishes of Ra 0.1 micron and radii down to 0.0007 inch."
Also embedded within the FORM 20 machine is GF Machining Solutions' TECFORM module that eliminates the need for operators to adjust the machine generator parameters. According to the company, optimized performance, efficiency and increased production time are all achieved automatically.
The FORM 20 is a compact standard die-sinking EDM that provides axis travels of 13.78" x 9.84" x 9.84" (350 mm x 250 mm x 250 mm) and includes an integrated four-position linear tool changer.
The machine incorporates rigid and compact mechanical structures for stable operation, a cast-iron, short C-frame for dynamic rigidity and a linear glass scale on its cross table positioning accuracy.
For more information contact:
Gisbert Ledvon
GF Machining Solutions
560 Bond St.
Lincolnshire, IL 60069-4224
800-CTC-1EDM
gisbert.ledvon@georgfischer.com
www.gfms.com/us