
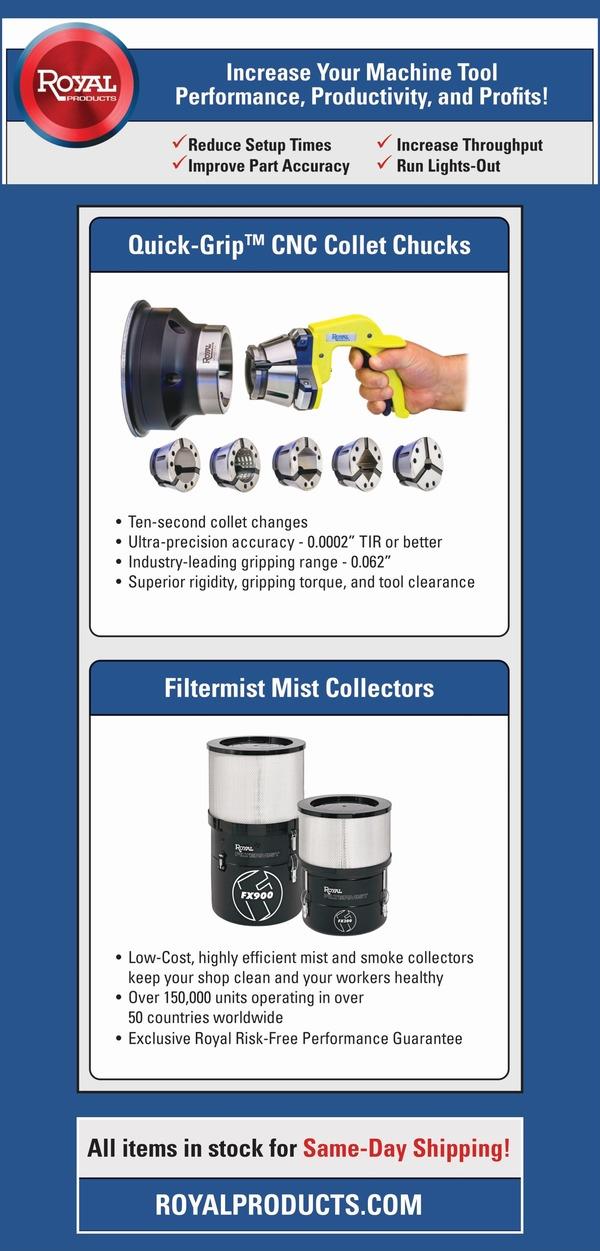
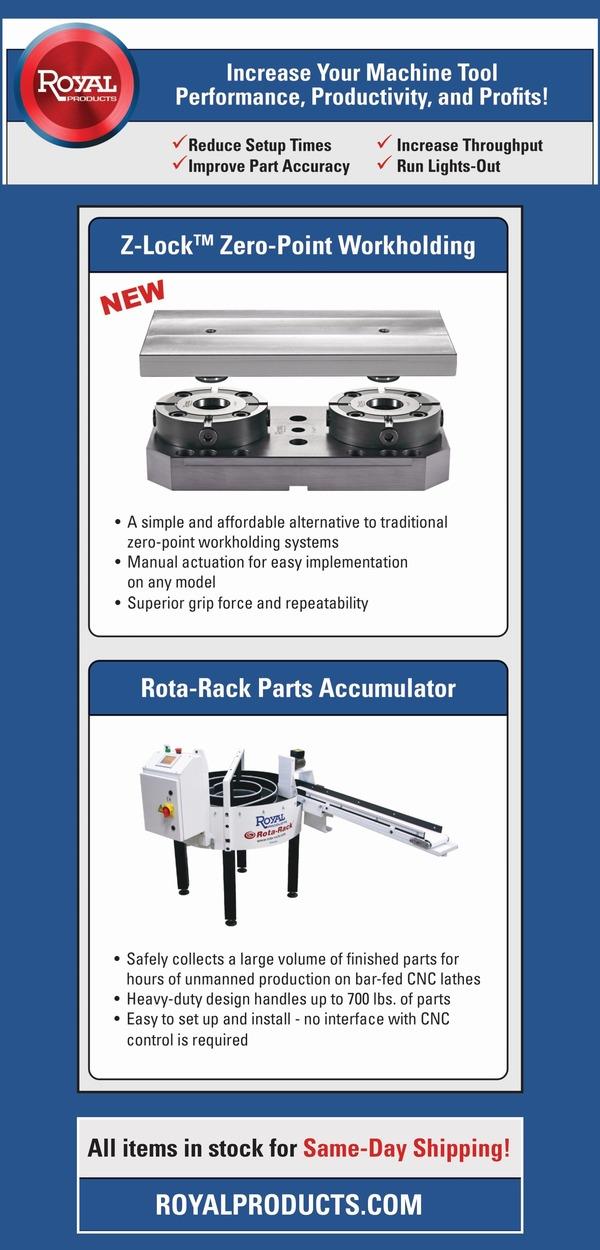

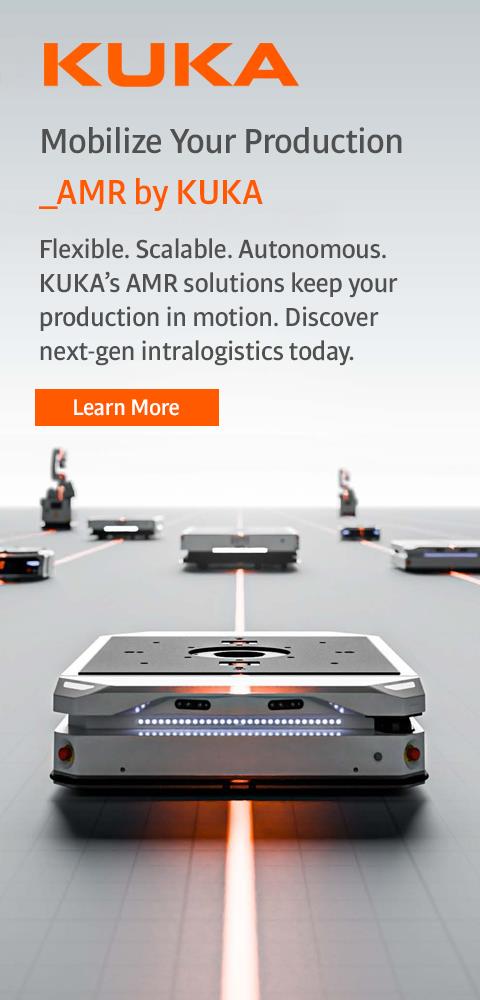
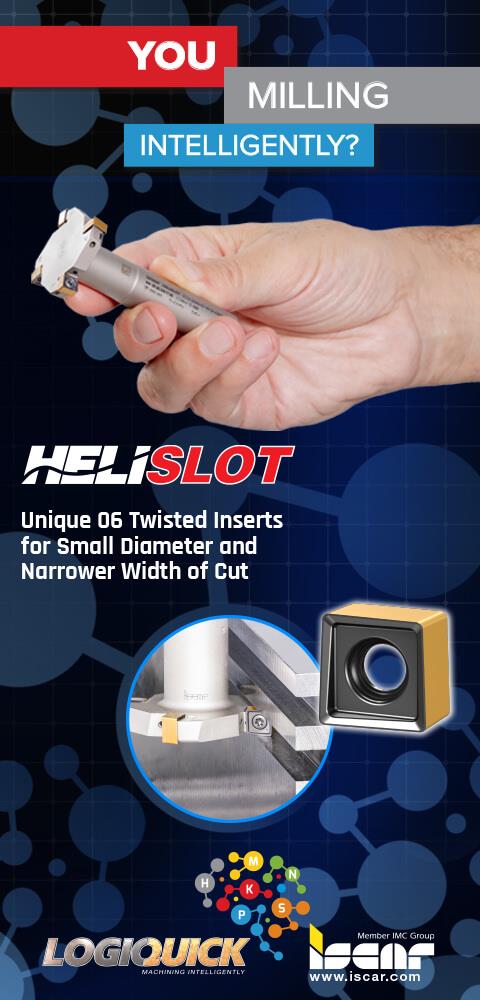
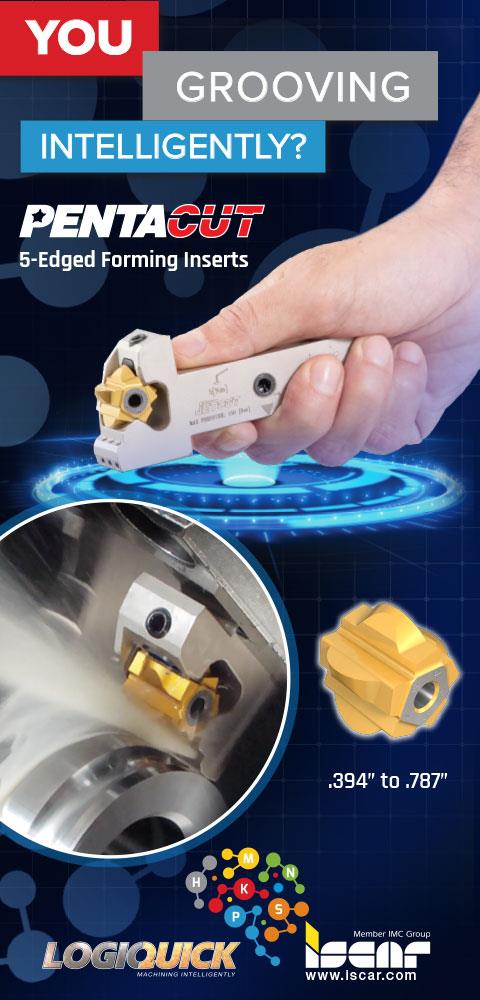
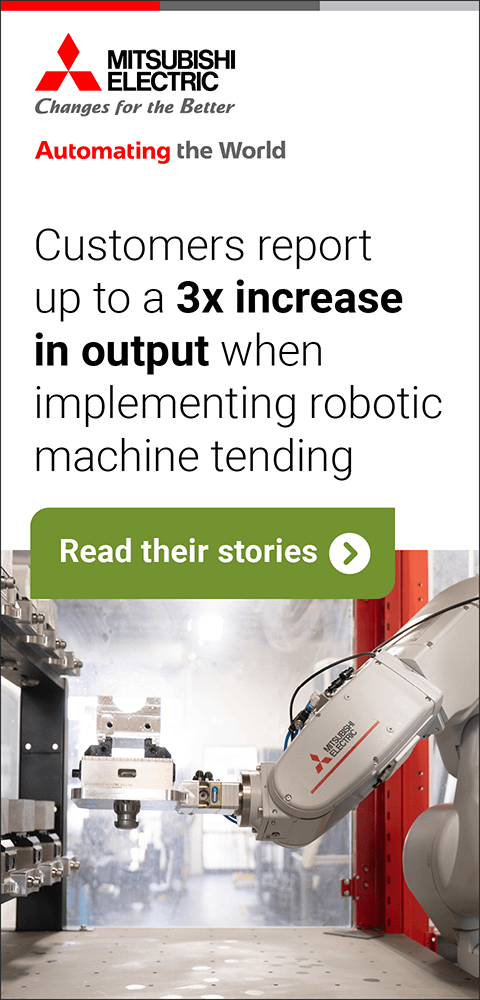
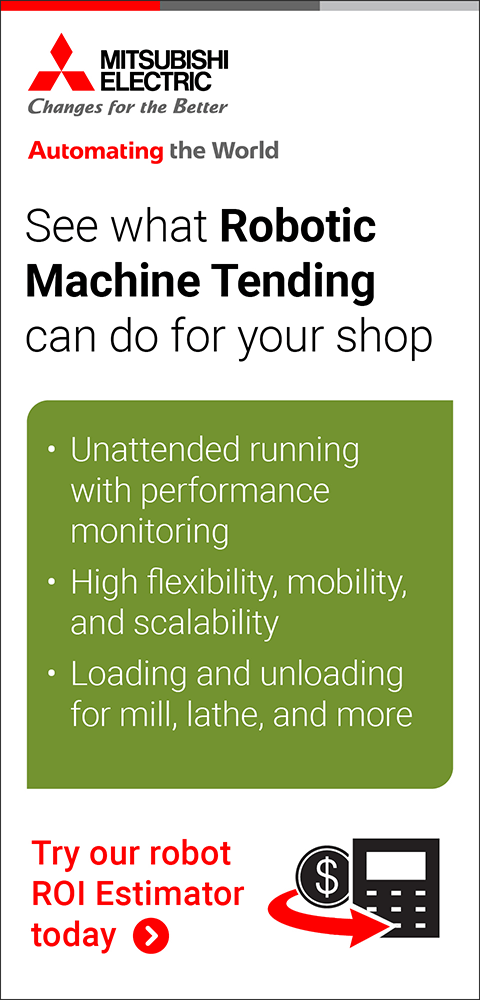
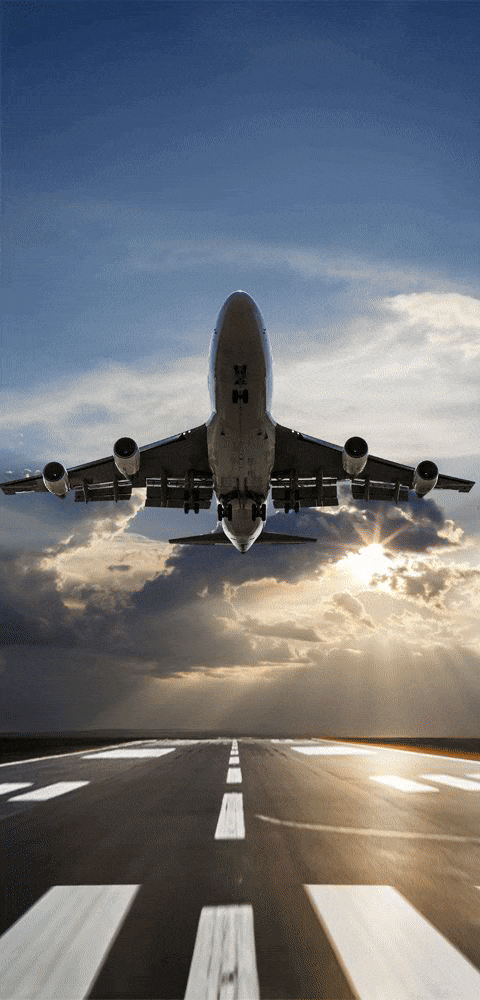
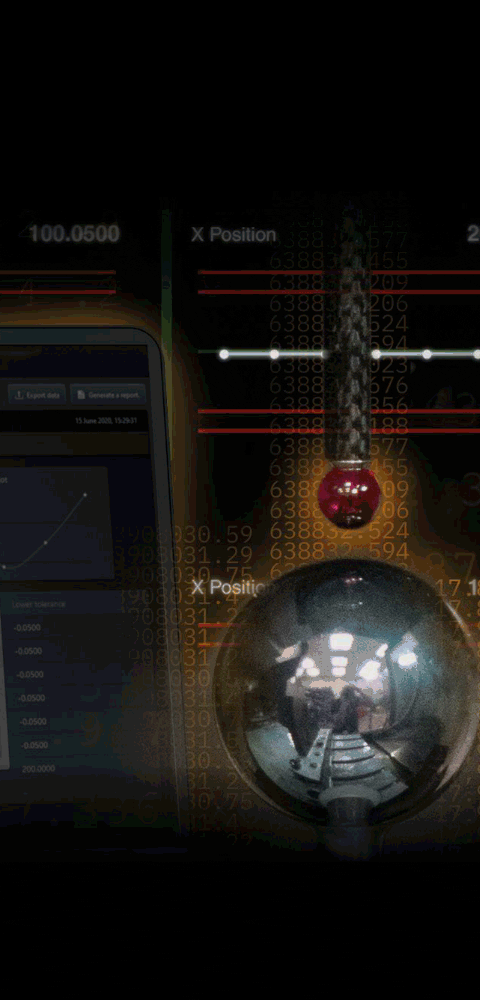
Horizontal Quench Furnace for Heat Treating Facility
May 1, 2015
Wisconsin Oven Corporation announced the shipment of a horizontal quench system used for solution heat treating of forged aluminum gun parts. The customer provides heat treating services to a large gun manufacturer, and prior to purchasing the solution heat treating system, it was outsourcing the work to a commercial heat treating company. "The yearly cost savings it realized by bringing the heat treating process in-house was well worth the investment in the equipment. Two total solution heat treating ovens were purchased along with three total aluminum aging ovens," said a company spokesperson.
The solution heat treat system has a maximum temperature rating of 1,250 °F, a work chamber of 4'W x 4'L x 4'H, and is designed to heat a 1,000 lb. load of aluminum to 950 °F. It is electrically heated with 144 kW of heat input and zero-fired SCR power control. The recirculation system utilizes a 15,000 CFM blower with combination air flow design to maximize temperature uniformity. This horizontal quench system features guaranteed temperature uniformity (+/-10 °F at 800 °F and 1,100 °F) and meets the requirements of AMS 2750E Class 2.
The quench tank is a 12 gauge 304 stainless steel construction, 304 stainless steel removable quench tank covers (utilized to minimize heat loss), and utilizes a pneumatically actuated quench elevator with 304 stainless steel wheel rollers and lift structure. The tank has a 2,400 gallon capacity and agitation pump rated for 200 gallons per minute with galvanized steel distribution piping and horizontal style water agitation design. The tank volume is designed for a 15 °F maximum water temperature rise (when load is quenched). The tank water temperature capability is rated for 140 °F to 180 °F normal use (with a 210 °F maximum temperature capability).
"A Horizontal Quench System is a great cost saving alternative to a typical Drop Bottom System. It rivals many of the typical drop bottom capabilities and features. In many instances the Horizontal Quench System will occupy less total floor space than a typical Drop Bottom System of the same chamber volume," said Doug Christiansen, Application Engineer, Wisconsin Oven Corp.
Features of this horizontal quench system include:
- As low as a seven second quench delay (load transfer time from closed door oven chamber to load submerged in quench tank); quench delay timing is variable/adjustable
- Electrically actuated vertical lift door with counterweight guided by linear rail/carriage, and variable frequency drive speed control
- Linear pusher/extractor (load pusher) with variable frequency drive speed control
- Oven relay and sequence control performed by an Allen Bradley CompactLogix PLC utilizing Integrated Motion over Ethernet/IP
- Operator interface control (for oven/quench/pusher) performed by an Allen Bradley Panelview Plus 6 10" color touchscreen HMI for manual and semi-automatic system control capability
- Nema 12 rated control panel with disconnect switch, Eurotherm 3504 recipe temperature controller (25 recipe capability), and Eurotherm 3204 process high limit controller
- Automatic solenoid actuated tank water fill capability with high/low floats, and low water level pump shut off float.
This horizontal quench system was fully factory tested and adjusted prior to shipment to help reduce installation and start-up times. A 150 point quality assurance check list was completed to ensure the equipment met all Wisconsin Oven quality standards. The heavy-duty batch oven is backed by Wisconsin Oven's 5-year warranty. This warranty covers all materials for all components (less wear items).
For more information contact:
Wisconsin Oven Corporation
2675 Main Street
East Troy, WI 53120
262-642-3938
sales@wisoven.com
www.wisoven.com
< back