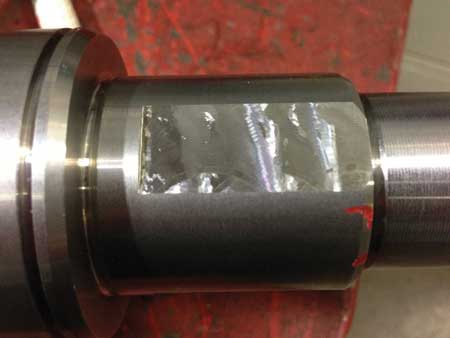
Flat surface shows finish problems from the original cutter.
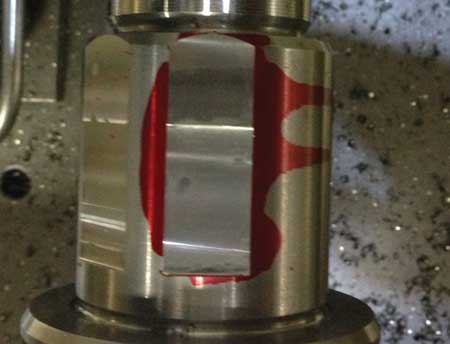
Horn USA Mini Mill produced 15-20 micro finish with no additional machining steps.
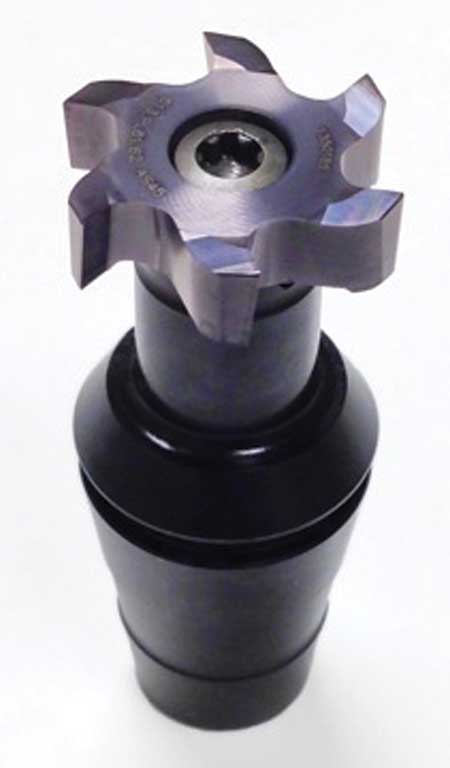
Horn USA Face Milling 613 Insert and ER Holder
Horn USA, Inc. recently worked with Machine Tool & Gear (MT&G) of Owosso, MI, to address a new truck shaft design including a flat area that must be machined at 90° from other operations. Since adding a second machine and fixtures to perform the additional process is cost-prohibitive, Machine Tool & Gear Manufacturing Engineer Jeff Ochodnicky elected to use two 90° milling heads to machine the flats. However, this created a number of problems including excessive tool wear and unacceptable surface finish. After trying various spindle speeds, feedrates, depths of cuts and inserts, Ochodnicky turned to Horn USA Applications Engineer Brett Kischnick for help.
The challenge was to mill a 1.500" long flat, 0.060" deep on a shaft using a 0.854" diameter cutter hanging more than 10" out of the spindle, while producing a 30-microinch Ra surface finish. "The cutting insert Machine Tool & Gear was using was a staggered flute design that caused pushing and pulling during the cut," said a company spokesperson. "This was replaced with a Mini Mill insert from Horn USA that applies all cutting forces downward and frees up the cut, utilizing a positive axial helix."
To achieve the desired surface finish without adding an additional step between the two passes required eliminating even more cutting pressure by reducing the teeth in cut from six to three, increasing the surface feet per minute, and making a rough cut first, leaving 0.002" for a finish pass. MT&G also moved the finish pass away from the 0.060 high side wall left from the rough pass. "Since multi-directional tool pressure causes a poor surface finish, relieving the side pressure by just a few thousandths of an inch helped produce a 15 - 20-microinch Ra surface finish without adding a step between passes," said the spokesperson.
"The final running parameters are 715 surface feet per minute, 0.058 inches depth of cut for roughing, 0.002 inches for finishing, and 0.004 inches IPT for roughing and 0.002 inches IPT for finishing," said Ochodnicky. "I was very impressed with Horn USA's knowledge and how they took the time to help solve the problem. As a result, we have saved the expense of buying another machine tool and kept additional labor costs out of our process."
For more information contact:
Jason Farthing
Technical Sales & Marketing
Horn USA, Inc.
320 Premier Ct., Suite 205
Franklin, TN 37067
888-818-4676
technicalsales@hornusa.com
www.hornusa.com