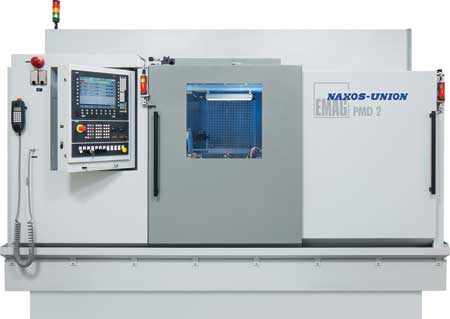
Compact design: The enclosure also contains the electrical cabinet and the energy container. Equipping the machine with an automatic loading system is an option.
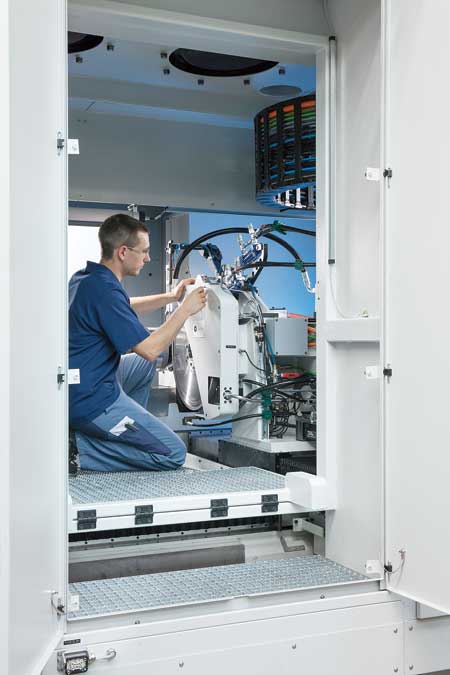
Access to the PMD 2 crankshaft grinder components is easy.
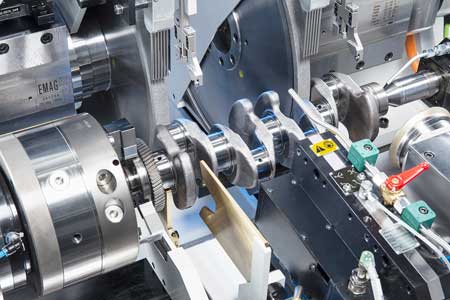
Two grinding wheels are used for the simultaneous machining of two pin bearings, reducing cycle time considerably.
Prospects for the international automotive industry are promising, with expected growth in the coming years supported by growing demand in the Asian markets. Competition continues to increase, especially from Asian companies. In addition, more rigorous national emission limits and safety requirements lead to an increase in production costs, causing planners to review their manufacturing technologies for potential savings. In the example of the crankshaft, which the engine depends on for efficiency and stability, a work-intensive grinding operation in the micrometer range is required.
EMAG has developed a tailor-made grinding solution for shaft-type components. The new PMD 2 machine is designed for the machining of passenger car crankshafts and features twin grinding heads that allow the simultaneous grinding of two pin or main bearings in a single set-up using two grinding wheels. Its capacity covers small components up to 500 mm length. "With this machine we are rounding out our range of crankshaft grinders to include the machining of smaller components," said Dr. Guido Hegener, Managing Director of EMAG Maschinenfabrik GmbH. "Up to now, our range of machines did not include a horizontal twin-head grinder for smaller crankshafts. This gap is now filled with the PMD 2."
The basis for the PMD 2 is the established "Series 2" from EMAG NAXOS-UNION and EMAG KOPP. "These machines combine high-tech grinding technology with precision, great efficiency, process integrity and simple operation," said the spokesperson. "This applies to the PMD 2 as well, where two CBN grinding wheels machine crankshafts to the highest precision."
To achieve this, the machine is equipped with a direct-driven workspindle, hydrostatic guideways and a linear motor in the X-axis, as well as an in-process measuring control that allows for roundness monitoring and correction in the machine. "The operator enters the relevant command in the control and the measuring process is carried out once the bearing has been ground. The software, developed by EMAG, then calculates the relevant correction values from the remaining roundness errors. This allows for the subsequent manufacturing processes to be successively optimized," said Hegener.
The technology also uses two grinding wheels. The twin-tool process opens up a number of possibilities for the user, depending on component and machining requirements. Two pin bearings or main and pin bearing are machined simultaneously, reducing cycle times. For instance, a four-cylinder crankshaft is machined in less than two minutes. The grinding wheels can, if required, be arranged very close together so that adjoining pin and main bearings can be machined simultaneously. Both grinding spindles and work headstock are direct-driven.
The machine also features a compact but flexible construction, for example the electrical cabinet is included in the enclosure. Connecting an automatic loading system poses no problem, and both emulsion and oil can be used as coolants. "Flexibility was of great importance in using this technology," said Hegener. "We tailor the machine exactly to the customer's requirements. Integration into an existing, complex production line is an important option, but there is the option of the machine being used as a stand-alone solution with manual loading. We expect this approach will give users a competitive edge while component quality and production costs are gaining importance world-wide."
For more information contact:
Peter Loetzner
EMAG LLC
38800 Grand River Avenue
Farmington Hills, MI 48335
248-477-7440
info@usa.emag.com
www.emag.com
Southwest
AR
David Fitzgerald
EMAG LLC
248-595-1117
www.emag.com
TX, OK, LA
Ric Lorilla
EMAG LLC
248-595-1530
rlorilla@emag.com
Southeast
VA, NC, SC, GA, FL, TN, AL, MS
David Fitzgerald
EMAG LLC
248-595-1117
www.emag.com
Northeast
PA, NY
Kirk Stewart
EMAG LLC
248-996-4703
kstewart@emag.com
ME, NH, VT, MA, RI, CT, NJ, DE, MD
Jonathan Chomicz
EMAG LLC
248-497-8526
jchomicz@emag.com
WV
David Fitzgerald
EMAG LLC
248-595-1117
www.emag.com
Midwest
IN, MI, OH
Kirk Stewart
EMAG LLC
248-996-4703
kstewart@emag.com
ND, MN, WI, SD, NE, KS, IA, MO, IL
Tod Petrik
EMAG LLC
248-470-2646
tpetrik@emag.com
KY
David Fitzgerald
EMAG LLC
248-595-1117
www.emag.com
West
Peter Loetzner
248-477-7440
info@usa.emag.com
Arnie Sugiyama
Caltec International
19801 Hamilton Ave
Torrance, CA 90502
310-527-4110
arnie@caltecusa.com