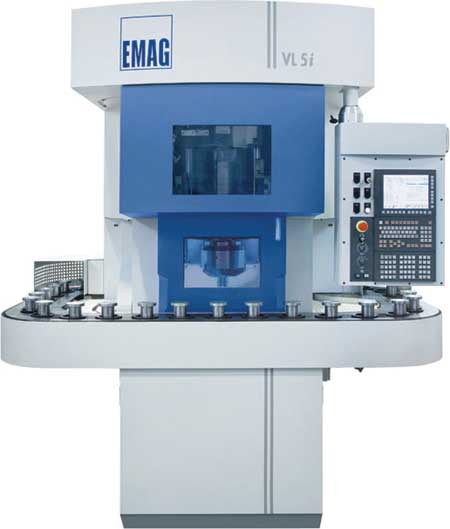
The VL 5i Vertical Turning Machine from EMAG has been designed for medium-sized businesses and subcontractors. The machine features a small footprint and automatic workhandling.
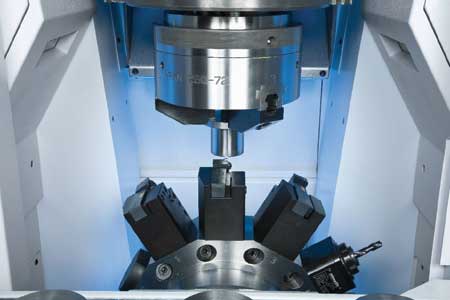
Machining area of the VL 5i: 12 turning or up to 12 driven drilling and milling tools are designed to allow users to carry out a variety of operations in a single set-up.
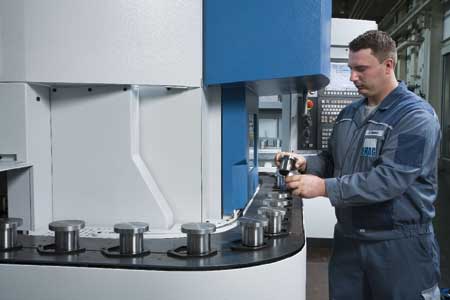
A recirculating conveyor band, with carrier prisms that do not need to be reset, takes the components to the pick-up station. Since this station lies behind the machining area, the operator is able to remove finished components and insert new raw parts at the front of the machine.
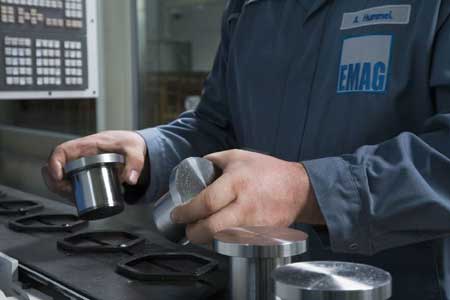
Flexible component loading: Workpieces are loaded by inserting them directly into the carrier prisms or, where necessary, into workpiece receptors that can then be inserted into the prisms.
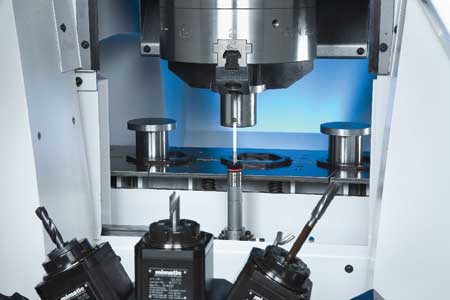
A measuring probe, located outside the machining area, is designed to bring quality assurance to the machine. In automated measuring cycles, carried out between machining process and component removal, the VL 5i logs the offset data and provides a record for quality assurance purposes.
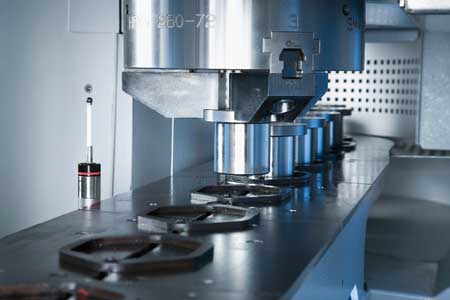
Quickly in and out: The workpieces reach the pick-up station in flexible carrier prisms mounted on the recirculating conveyor belt. The prisms' flexibility is designed to minimize the resetting effort for different workpiece diameters.
EMAG has introduced its new Platform 250 machines, which are designed to enhance configurability.
The 250 standard represents chuck size on three basic machines: the VSC 250, the VLC 250 and the VL 5i. According to the company, each of these machines has been designed with a specific set of requirements in mind: The VSC 250 is a customizable manufacturing system, the VLC 250 is a universal multi-technology machine and the VL 5i is a manufacturing system for the subcontractor.
Flexible Application
"Of the three basic machines, the VL 5i is the most standardized," said a company spokesperson. "It focuses on smaller and medium-sized production companies. The objective has been to develop a manufacturing solution that can find a use in anything from small batch to mass production. The demands are complex and a machine needed for universal use must offer short resetting times and represent a highly efficient tool in a batch production environment."
In order to meet these demands, according to the company, specific features have been incorporated in the VL. For example, the Z-axis stroke on the VL 5i has been increased by 50%, to 300 mm, expanding the range of applications. "Setting up has been further simplified by including certain pieces of software," said the spokesperson. "EMAG intended to design a machine that is fully equipped with integrated carrier prism-type automation, a fluid cooling system for spindle motor and turret, a chip conveyor, a machining area extraction system and an optional measuring probe."
Flexible Automation
According to the company, every VL features an automation system with recirculating conveyor chain into which carrier prisms that transport the workpieces to and from the pick-up station are inserted. This allows for a wide range of workpieces to be handled automatically without the need for resetting. "The automation equipment helps create a fixed production cycle, as a new raw part is available immediately after the previous workpiece has been machined," said the spokesperson. With the pick-up station located behind the machining area, the operator is able to remove the finished components and insert new raw parts at the front of the machine.
Where required, workpiece receptors and simple design pallets capable of accommodating asymmetrical and long, thin workpieces or components that must be machined in fixed alignment, can be inserted into the carrier prisms. "This allows for the fully automatic handling of a large variety of workpieces," said the spokesperson.
The VL, according to the company, is equipped with a turret to accommodate turning as well as driven tools and features indexing times of 2.2 seconds. All 12 stations can also be equipped with driven tools for drilling and milling work. "The EMAG turret drive combines high speeds with a high power rating and a minimal space requirement," said the spokesperson. "The diameter of the turret is about 360 mm, with 12 tool stations and a maximum torque of 45 Nm."
Quality Management
According to the company, the VL 5i was the first EMAG machine to feature measuring as an integrated option. A measuring station can be fitted outside the machining area, allowing a probe to measure the workpiece as it makes its way from the machining to the unloading position. "As the measuring takes place outside the machining area, the results will not be adversely affected by chips or dirt and the measurements are taken with the component still in the chuck," said the spokesperson.
Energy Efficiency
"Energy is a valuable commodity," continued the spokesperson. "The use of Mineralit polymer concrete for the machine base has made the VL so sturdy and vibration resistant that tool life is considerably higher than on machines with cast iron bases. All guideways are located above and outside the machining area, where they are well protected from chips and dirt. This results in constantly maintained accuracy and process integrity, and it also reduces maintenance.
"Telescopic covers, so susceptible to malfunctions, are no longer found on the VL 5i. From a power rating of 0.5 kW upward, EMAG uses only motors of efficiency classification eff1 with a provision for energy recovery. The electrical cabinet no longer requires air conditioning, as all amplifiers are exponents of through-hole technology and feature passive coolant systems. The valves are low-wattage and consume 70% less energy than the traditional type. The hydraulics system features an accumulator charging circuit, which provides hydraulic pressure only when required, similar to the compressed air supply where consumption is held at the lowest possible level by sealing air cycles."
The following are advantages of the VL 5i, according to the company:
- Automatic workpiece changeover in the shortest possible time
- Integrated automation, low capital outlay
- Short travels between loading and machining stations, resulting in very short cycle times
- High degree of machine availability
- Ideal chip flow conditions
- Very short chip-to-chip times
- High Z-axis stroke of 300 mm
- Small footprint
- Optional workpiece measuring, using a measuring probe located outside the machining area.
For more information contact:
Peter Loetzner
EMAG LLC
38800 Grand River Avenue
Farmington Hills, MI 48335
248-477-7440
info@usa.emag.com
www.emag.com
Southwest
AR
Ken Pope
EMAG LLC
256-642-6842
kpope@emag.com
www.emag.com
TX, OK, LA
Ric Lorilla
EMAG LLC
248-595-1530
rlorilla@emag.com
Southeast
VA, NC, SC, GA, FL
David Fitzgerald
EMAG LLC
248-595-1117
TN, AL, MS
Ken Pope
EMAG LLC
256-642-6842
kpope@emag.com
www.emag.com
Northeast
PA, NY
Kirk Stewart
EMAG LLC
248-996-4703
kstewart@emag.com
ME, NH, VT, MA, RI, CT, NJ, DE, MD
Jonathan Chomicz
EMAG LLC
248-497-8526
jchomicz@emag.com
WV
Ken Pope
EMAG LLC
256-642-6842
kpope@emag.com
www.emag.com
Midwest
IN, OH
Kirk Stewart
EMAG LLC
248-996-4703
kstewart@emag.com
MI
Geoff Fuller
EMAG LLC
248-632-2021
gfuller@emag.com
ND, MN, WI, SD, NE, KS, IA, MO, IL
Tod Petrik, Regional Sales Manager
EMAG LLC
248-470-2646
tpetrik@emag.com
KY
Ken Pope
EMAG LLC
256-642-6842
kpope@emag.com
www.emag.com
West
Arnie Sugiyama
Caltec International
19801 Hamilton Ave
Torrance, CA 90502
310-527-4110
arnie@caltecusa.com