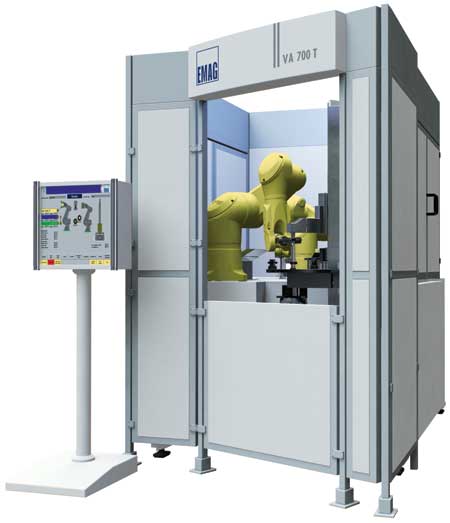
VA 700 T - Heat-shrinking assembly system for the manufacture of composite camshafts. While one cam is heat-shrunk, the next is already being preheated. According to the company, equipping the machine with a number of preheating units allows for optimal scaling of the application.
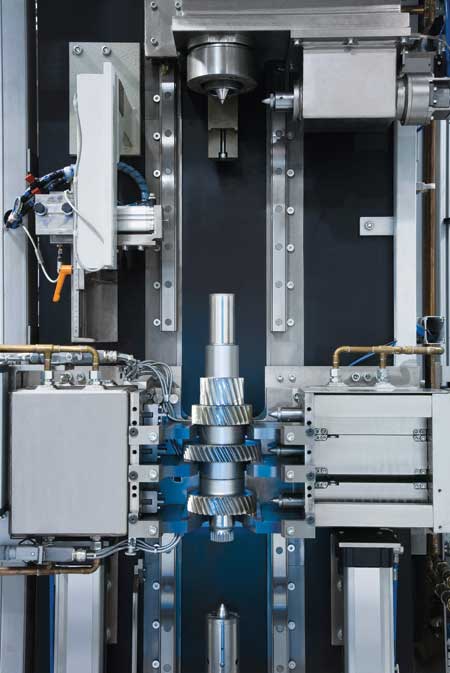
Finish assembly of a gear shaft. A combination of robots and special-design grippers technology makes it possible to heat-shrink with a joining clearance of < 15 um.
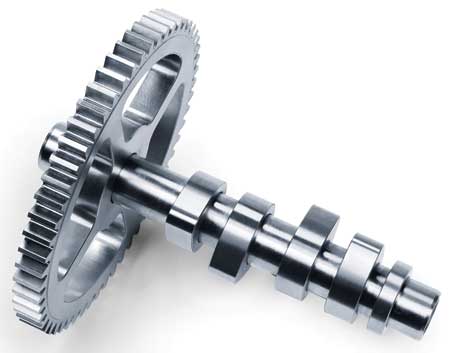
Complete, ready-to-fit, heat-shrunk camshaft. "The high degree of precision achieved on this composite shaft drastically reduces the need for a cam profile grinding operation or, if precision cams are used, avoids it altogether," said a company spokesperson.
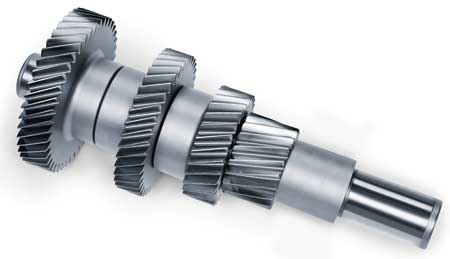
Also suitable for gear shafts. According to the company, heat-shrinking the gear shaft components makes for a compact construction and high functional density, as the gears can be brought right up to the shoulders.
EMAG offers its patented heat-shrink assembly process to manufacture precision components, in particular composite camshafts. According to the company, this process is characterized by its reaction force-free processing sequence. "In the center of the EMAG system, the component is brought up to the necessary temperature with great precision using an inductive or contact heating process," said a company spokesperson. The relevant preheating unit geometrically fits the workpiece and features an internal temperature control component.
"Powertrain production faces many challenges, including increasingly complex constituent components and decreasing batch sizes," said the spokesperson. "Heat-shrink assembly offers unique solutions for a large number of applications in this sector. Where control cams and/or gears are to be mounted on shafts, heat-shrink assembly brings about a considerable reduction in component weight while guaranteeing a high degree of functional density of the shaft. The process is also suitable for workpieces that are subject to high torque rates and great dynamic loads.
"Powertrain production calls for flexibility and effectiveness," continued the spokesperson. "Often, a diverse range of camshafts or gear shafts of complex geometry must be produced at the same location in varying batch sizes. Additionally, demands on the actual components are also increasing. High-tensile materials are being used, geometries are more complex and components are expected to become smaller and weigh less. Composite camshafts are gaining importance where individual components are made in larger quantities and then joined according to engine type requirements. This leads to a noticeable reduction in production costs while maintaining the necessary high degree of precision."
According to the company, the heated workpiece is joined with the shaft without any application of force. As the workpiece cools and contracts, it clamps firmly onto the shaft. A combination of robots, NC axes and gripper technology is designed to guarantee a process with a joining clearance of less than 15 um. "The whole process for camshafts, from pick-up of the relevant components to completion of the force fit action, takes 7 seconds," said the spokesperson. "A complete camshaft for a four-cylinder engine is therefore assembled in approximately 40 seconds. Processing speed is increased by the fact that while one component is heat-shrunk, the next one is already being preheated, all inside the EMAG system.
"Users not only benefit from the short cycle times, but the process also provides a large degree of freedom and production flexibility," continued the spokesperson. According to the company, EMAG technology allows for a multitude of materials to be heat-shrunk, such as forged or sintered cams that do not require grinding after having been shrunk onto the shaft. "Ancillary components, such as bungs or end pieces, can be made from more cost-effective materials, offering a substantial savings potential," said the spokesperson. "This approach also has a positive effect on development and functionality, as every component can be made to suit individual demands, while increasing its functional density. Where required, gears can be fitted snuggly against shoulders. This ensures that many new design variants can be implemented on the smallest possible space."
Tailor-made System Design
According to the company, the crucial point in developing machines with this specialized technology is the delicate production sequence of preheating, heat-shrinking and cooling.
"Rapidly accelerating automobile production will result in many suppliers increasing their production capacity considerably over the next few years," said the spokesperson. "EMAG's technology helps these expansion needs and provides future technological developments as well. Modern utility vehicle engines, for example, feature camshafts with integrated bearing elements. As a consequence, no downstream grinding processes can be carried out on these shafts, as the chips produced would damage the bearings. This is why composite shafts are used exclusively. This approach will gain importance when it comes to future utility vehicle designs and the expansion of the market for heat-shrink applications."
For more information contact:
Peter Loetzner
EMAG LLC
38800 Grand River Avenue
Farmington Hills, MI 48335
248-477-7440
info@usa.emag.com
www.emag.com
www.emag.com/machines/joining-machines
Southwest
AR
Ken Pope
EMAG LLC
256-642-6842
kpope@emag.com
www.emag.com
TX, OK, LA
Ric Lorilla
EMAG LLC
248-595-1530
rlorilla@emag.com
Southeast
VA, NC, SC, GA, FL
David Fitzgerald
EMAG LLC
248-595-1117
TN, AL, MS
Ken Pope
EMAG LLC
256-642-6842
kpope@emag.com
www.emag.com
Northeast
PA, NY
Kirk Stewart
EMAG LLC
248-996-4703
kstewart@emag.com
ME, NH, VT, MA, RI, CT, NJ, DE, MD
Jonathan Chomicz
EMAG LLC
248-497-8526
jchomicz@emag.com
WV
Ken Pope
EMAG LLC
256-642-6842
kpope@emag.com
www.emag.com
Midwest
IN, OH
Kirk Stewart
EMAG LLC
248-996-4703
kstewart@emag.com
MI
Geoff Fuller
EMAG LLC
248-632-2021
gfuller@emag.com
ND, MN, WI, SD, NE, KS, IA, MO, IL
Tod Petrik, Regional Sales Manager
EMAG LLC
248-470-2646
tpetrik@emag.com
KY
Ken Pope
EMAG LLC
256-642-6842
kpope@emag.com
www.emag.com
West
Arnie Sugiyama
Caltec International
19801 Hamilton Ave
Torrance, CA 90502
310-527-4110
arnie@caltecusa.com