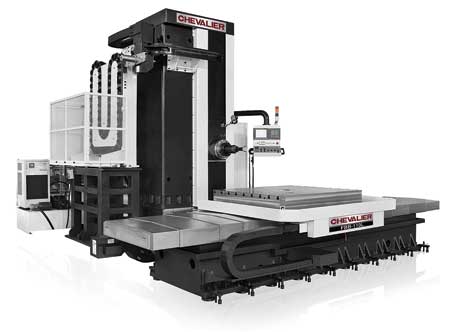
FBB-110L T-type horizontal boring mill.
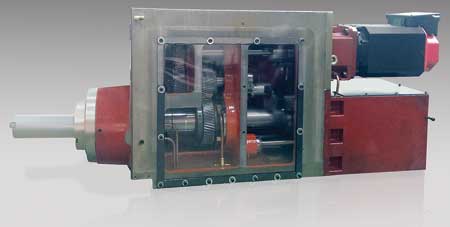
FBB-110L gear box.
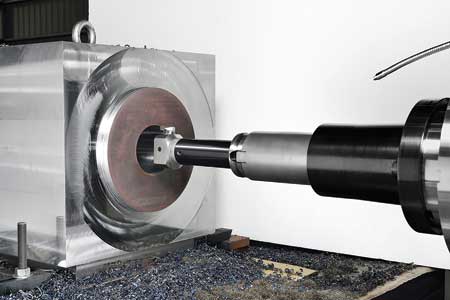
FBB-110L boring bar in the cutting process.
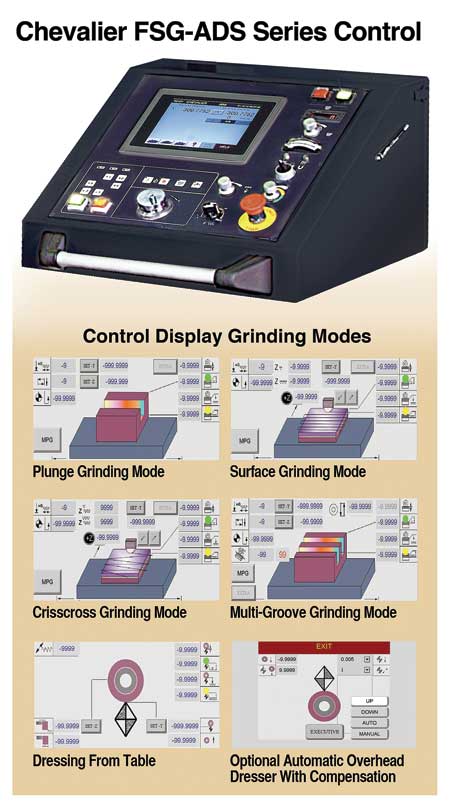
FSG-2460ADS Automatic Grinder
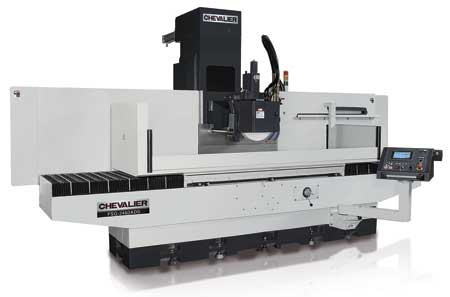
FSG-2460ADS control screens.
Chevalier plans to exhibit nine machines designed to increase production and efficiency. They will be running in a 5,000-square-foot booth on the IMTS showroom floor. Chevalier's own engineers will be on hand throughout the duration of the show to answer any questions.
Chevalier's line-up of machines include the new FSG-2440ADS automatic grinder, the new FBB-110L horizontal boring machine and the new FBL-520D heavy-duty horizontal turning lathe. Attendees will also watch a FANUC intelligent robotic team with a Chevalier heavy-duty horizontal turning lathe, demonstrating production efficiency through automation.
The FBB-110L series, a T-type horizontal boring mill, handles heavy-duty, high-precision machining with 120" x 83" x 80" machining capabilities. The extra-rigid design of the main machine body and column ensure structural stability. The fully supported base on the X- and Y-axis assures no overhang or vibration during cutting. The series features a one-piece Meehanite cast iron base with heavy-duty large box ways on X-, Y-, and Z-axes and is coated with an anti-friction Turcite material for consistent accuracy and smooth movement.
The 35 HP, 50-taper, large-diameter, cartridge-type, air-purged spindle runs with a two-speed gear head stock that generates a maximum of 1,500 nm. The spindle can be extended (W-axis) for deep-hole boring. The table features a full C-axis contouring with 0.001-degree minimum intervals. It also has a hydraulic break disk plus a locking pin every 90-degrees, designed for maximum stability. The rotary table is driven by an AC servo motor with a worm shaft and gear that provides high torque for heavy workpieces. The angular scale is built in the table to assure the accuracy of +/- 15 arc-second.
Chevalier's FVM-8088DC heavy-duty bridge machine is designed for machining large workpieces. The big size column and box-type beam construction provide support and damping. The table size is 86.6" x 70.8", for machining automotive molds. The 35 HP power spindle with a two-speed gearbox produces 700 nm of torque. The one-piece base and 70-degree cross-rail design with Meehanite casting provide rigidity and stability. The bottom column section is wider than the top to protect the machine from tilting forward. The high-pressure coolant through spindle is standard on this machine, meaning no after market engineering, enabling the end-user to connect the high-pressure coolant system quickly with less down time.
The FVL-1250VTC+C series is designed for heavy-duty turning, milling, boring, grinding, drilling and thread-cutting applications. The rotary table is driven by a spindle motor with a gearbox for low-speed high-torque machining and higher speed for fine finishing. The live tooling provides a powerful milling capability along with a standard FANUC 25 HP spindle motor that includes a two-speed gearbox, providing up to 478 nm torque. It is designed to handle up to M30 tap or 50 mm drill with tough material. The full C-axis function can be programmed in minimum 0.001 degree indexing. This rigid machine structure reduces the cutting induced vibration associated with machining hard metals.
The FBL-360B heavy-duty horizontal turning lathe team will be seen with a FANUC robot. The 45-degree slant bed lathe features a rigid box ways structure and programmable tailstock; engineered with ease of access and trouble-free maintenance in mind. The series also comes with a 15" chuck, maximum swing and maximum turning diameter of 22.4" and a maximum turning length up to 80". The lathe features up to 35 HP AC digital spindle motor with two-speed gear box, spindle bar is 4.5" in diameter and speed up to 2,500 RPM.
Chevalier's FBL-520D heavy-duty horizontal turning lathe is designed for machining heavy parts and large pipe threading.
The series features accurate machining designed to handle rough- and fine-turning operations. The gear box provides enough horsepower for heavy-duty turning.
The series structure features a 45-degree slant-bed design, comprised of single-piece Meehanite cast iron with a wide-span, ribbed box structure. For stability and support, the machine provides box guide ways that are 5.1" wide by 3.1" thick. A powerful 60 HP spindle motor, which features a three-stage gearbox and generates 3,049 ft.-lbs. of torque. The 12-station turret is 200 mm thick for deep hole boring and rough turning. The 15" through hole for pipe yard threading meets API and parameter thread standards.
"Chevalier customers like what they see in the FSG-4080DC series double-column fixed beam grinders. They say the grinders are easy to set-up, program and operate and exceed the demands for rigidity, accuracy and speed. All while providing an enormous grinding area," said a company spokesperson. "It provides an easy-to-use interface, full CNC control system, total workpiece capacity and the rigidity and accuracy of the dual column design."
The user-friendly conversational programming features:
"Smart-III CNC PC based control and Microsoft Win CE platform
"Patented designed table stroke can be adjusted from screen
"Conversational graphic program for grinding and dressing
"Standard can cycles: step surface, slice and crisscross cycles
"Switch between manual, semi-automatic, fully automatic or CNC
"Automatic wheel dressing can be done while machining or at the end of a cycle
"Simplified data transfer using Ethernet/intranet data saving and transfer, USB port and CF card port
"Grinding simulation mode executable through MPG and variable pitch/depth slicing capability.
The FSG-ADS series high-precision, fully automatic, three-axes grinder with a PLC controller provides a grind cycle with rough grinding, fine grinding, spark-out passes and an automatic over-wheel dresser with compensation, which can be added to fully automate the grind process. After the cycle is finished, the table will "park" either left or right of the saddle and at the front to facilitate unloading and loading.
According to the company, the series is well suited for mass production and easy to set-up, program and operate, it also features user-friendly conversational programming. The machine's spindle can be set to "stop running" or "continue running." The wheel head can also be set to return to the start position or to park at a reference point. Once the cycle is started, the wheel head moves rapidly to the start point and repeats the grind cycle. If material is required to be removed from both sides, "flip over" can be selected so that the wheel head position is at the finish grind height, which then starts grinding immediately without touching off.
The fully automatic grind feature consists of rough and fine grinding cycles, switching from rough grinding down-feed increments to fine grinding down-feed increments at preset points during the cycle. This crossfeed also switches from a rough to fine cross-feed increment, resulting in a finer surface finish and finer accuracy.
"The new FSG-ADIII series is an advanced, automatic-precision, surface-grinding machine that offers improved accuracy, quality and ease of operation. This series includes the new touch-screen control station that is adjustable to a comfortable position for the operator. Switches, buttons, LEDs and indicating lamps are all combined in a touch display that is ergonomically positioned to provide the best user-friendly operation," says Chevalier Vice President Johnson Lan.
The FSG-ADIII Series includes a new PLC controller that provides a grind cycle with rough grinding, fine grinding, spark-out passes and an automatic over-wheel dresser with compensation, which can be added to fully automate the grind process. After the cycle is finished, the table will "park" either left or right of the saddle and at the front to facilitate unloading and loading. The spindle can be set to "stop running" or "continue running." The wheel head can also be set to return to the start position or to park at a reference point. Once the cycle is started, the wheel head will move rapidly to the start point and repeat the grind cycle. If material is required to be removed from both sides, "flip over" can be selected, so that the wheel head position is at the finish grind height, which will start grinding immediately without touching off.
The SMART-B818III surface and high profile CNC grinder is designed to produce "mirror" surface finishes on highly accurate ground workpieces that produce microfinishes of 5 RMS. The positioning accuracy is (+/-) 0.0025 micron and the grinding accuracy is 1 micron. The SMART's movements are programmable in increments of 0.001 mm and include a table size of 8" x 8". The maximum distance from table to spindle centerline is 16" and wheel spindle is rated at 1,000-7,000 RPM and 4 HP (3 kW). The SMART's standard grinding wheel size is 8" x 1/2" x 1-1/4". The machine weighs approximately 2,665 lbs., with dimensions of 80.9" x 82.36" x 82.7".
For more information contact:
Chevalier Machinery Inc.
9925 Tabor Place
Santa Fe Springs, CA 90670
562-903-1929
info@chevalierusa.com
www.chevalierusa.com
IMTS 2014 Booth S-8987