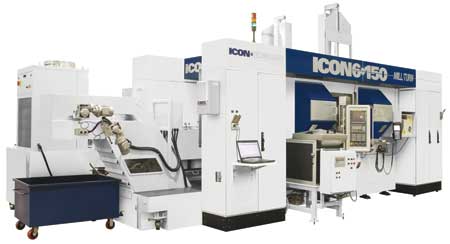
ICON Technologies, a division of Hydromat Inc., introduces the ICON 6-150 mill/turn center, a precision metalcutting machine that combines flexible lean principles with a pallet transfer system for increased production.
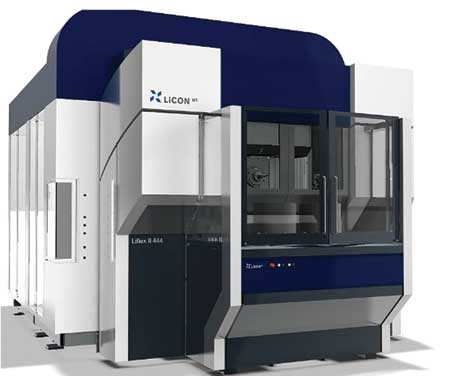
Hydromat will feature the Licon LiFLEX 444 II. With this twin-spindle machining center, German machine manufacturer Licon mt is appealing to new markets and target groups for the processing of small and medium-sized workpieces.
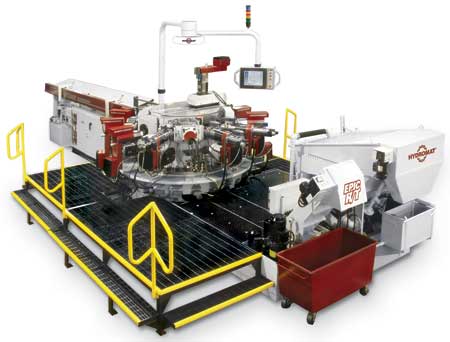
The Hydromat EPIC R/T 45-12 rotary transfer machine produces precision metalcutting for bar-fed applications. This machine utilizes 12 horizontal tool spindles and the capacity of up to six vertical tool spindles, featuring up to 18 tools in the cut at once.
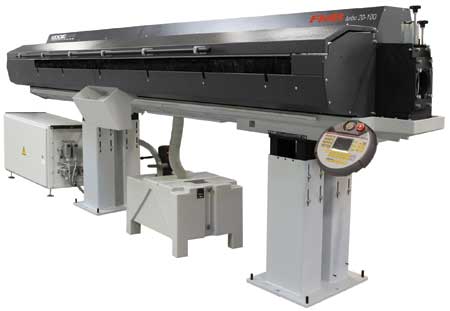
Edge Technologies introduces the new FMB 20-100 bar feeder. This feeder is compatible with all types of sliding or fixed CNC or cam operated lathes with spindle bores up to 102 mm.
Hydromat will feature a variety of productivity enhancing machines for precision metalcutting and automation, including the ICON 6-150 mill/turn center, Licon LiFLEX 444 II twin-spindle machining center, Hydromat EPIC R/T 45-12 rotary transfer machine and Edge Technologies FMB 20-100 bar feeder.
ICON 6-150 Mill/Turn Machining Center
ICON Technologies, a division of Hydromat, presents a multi-station mill/turn center, the ICON 6-150. Designed with four machining stations and two dedicated loading/unloading stations, the ICON was developed around flexible machining principles. Equipped with a six-position table, it is designed to shuttle pallets to four machining modules for fast, ultra-precision cutting.
Each of these four machining modules is equipped with one cartridge style motor spindle. Each spindle type is selected based on the type of cutting to be performed at that station. ICON offers high torque spindles in the following configurations; 10,000 RPM, 20,000 PRM, 42,000 RPM and 60,000 RPM. According to the company, these spindles are air-purged and liquid cooled, or permanently grease lubricated, and therefore are virtually maintenance free.
The machine is equipped with four servo driven, direct drive B-axis motors. These B-axis motors are installed on stations two, three, five and six and have a position accuracy of +/- 4 seconds. Each table is equipped with a zero point clamping system, made by EROWA in Switzerland, to securely and accurately clamp the base pallet to the B-axis motors. The positional repeatability of these pallets is 0.002 mm. An optional 350 Nm disc brake can be added for precise positioning during heavy cutting at an elevated level of force. Stations one and four are for loading, unloading, gauging, A/B loading and inverting for sixth side machining.
These four cutting stations produce 5-sided machining with 4-axis interpolation; six sides if the idle station is used for workpiece inversion. Each machining unit is equipped with its own HSK E40 size, 12-tool changer allowing for maximum tooling flexibility. HSK E32 size is available as an option.
An additional heavy cutting B-axis motor type is also offered for profile machining utilizing the 4th axis. With a more stout design, the company reported that it has a more rigid profiling capability with increased torque. Power is driven through a zero backlash worm drive gear box rather than the direct drive of the standard B-axis motor.
The ICON 6-150 can also come equipped with a 5th axis machining unit that features a high-speed integrated direct-drive motor spindle, one created by the designers at ICON Technologies in conjunction with the Fischer Precise spindle company. "Available with this optional 5th axis, the ICON 6-150 mill/turn center is perfect for medical applications and the production of aerospace, hydraulic, automotive and other precision machined parts," said a company spokesperson.
Workpieces are mounted by hand or by robotics on pallets that are transferred to each station by the rotary table. At each of the four machining stations the B-axis motors engage with the pallets for indexing or turning of the workpieces. The part sizes can range up to 150 mm in diameter and the height is dependent on part configuration, workholding and cutting force requirements.
The machine frame is designed as a sturdy, welded, steel construction. It supports the indexing table and the four machining units. According to the company, the openings below the machining stations are designed to assure an optimal evacuation of coolant and chips from the working area. Individually arranged and controllable coolant nozzles are installed inside of the machine frame for the purpose of providing coolant to the cutting tools and preventing chip accumulation inside the machining area.
"This multi-station transfer technology enables simultaneous machining on all four stations, making the machine ideal for medium to high production of complex workpieces requiring multiple operations, complex cuts and where tight tolerances are critical," said the spokesperson.
Licon mt Twin-Spindle Machine
Hydromat will feature the Licon LiFLEX II 444. "With this twin-spindle machining center, German machine manufacturer Licon mt is appealing to new markets and target groups for the processing of small and medium-sized workpieces, a perfect fit for expanding upon the Hydromat machine platforms at IMTS," said the spokesperson.
Licon mt's product portfolio includes a range of model types that meet different requirements for machining workpieces of different material types, workpiece sizes and varying degrees of flexibility and productivity. The LiFLEX II 444 was added to the line last year and represents a new machine model for processing smaller and medium-sized components up to 445 mm in size. "This machine is perfectly suited for heavy machining due to the rigid and compact design in combination with the high power/torque available," said the spokesperson. "By expanding its product portfolio with the new LiFLEX II 444, Licon mt is consistently pursuing its strategy for 5-axis complete machining on complex workpieces in a single clamping."
The integration of a pallet changer facilitates simultaneous loading and unloading of workpieces. Options include spindle compensation for the Z-axis and broken tool detection. The zero point clamping system is designed to ensure a quick changeover to other workpieces. Chip removal is optimized through suspended fixtures. "LiFLEX II 444 is smaller and more compact when compared with other LiFLEX machining centers," said the spokesperson. "The good price-performance ratio is very attractive to the market."
Winfried Benz, Managing Director of Licon mt, explains its market orientation: "With our small twin-spindle machine, LiFLEX II 444, we are able to offer companies around the world a viable alternative for machining medium-sized parts in small or medium volumes. We aim to continually optimize the process of complex workpiece machining with the goal of minimizing costs for scrap as well as additional quality controls. To this end, complete machining is an essential element. The price-performance ratio of LiFLEX II 444 makes a further contribution to ensuring that unit costs are reduced to the bare minimum."
EPIC R/T 45-12 Rotary Transfer Machine with Updated Features
The Hydromat EPIC R/T 45-12 is a collet style rotary transfer machine for precision metalcutting of stock sizes up to 1.75" round, 1.5" hex and 1.25" square and a length up to 6". This machine utilizes 12 horizontal tool spindles and has the capacity of up to six vertical tool spindles, featuring up to 18 tools in the cut at once. It also has the rigidity to handle all components and all material types within its work envelope. According to the company, Hydromat's non-rotating bar stock design provides quiet, vibration free operation.
All Hydromat Rotary Transfer machines are built as modular systems consisting of horizontal and vertical tool spindles rigidly mounted around a cast base with high-precision machining of all critical surfaces. According to the company, this arrangement is designed to provide tremendous versatility and flexibility in a turnkey machining system. This current version of the EPIC R/T 45-12 machine features the new Bar Change Stop, an automatic hard stop built into the bar feeder that further refines bar position by giving accurate position reference for the end of the new bar. It then begins the countdown for the remnant based on a known and fixed distance.
Hydromat's updated 2-axis programmable flange offers up to +/- 30mm of extended travel for offset features, rotary O.D. and I.D. recessing, thread milling, chamfering and in-process de-burring. "This innovation eliminates costly secondary operations while adding value to the manufacturing processes," said the spokesperson.
The new overhead cut-off saw is now utilized on many Hydromats on short part applications, or in a chuck machine where the clearance below the blade is constrained. It also offers easier access to the saw for easier blade changes. According to the company, the overhead saw configuration eliminates the possibility of chipping a saw tooth on the blade from a falling remnant during the bar change sequence.
"Another Hydromat innovation has streamlined the coolant plumbing by creating a high/low coolant ring positioned above the table," said the spokesperson. "This allows for unlimited options for both high and low coolant pressures where they are required most, while doing away with excess plumbing."
The EPIC R/T control gets updates for 2014 that include new programming features. While navigating from the main menu there is now an integrated Coolant Temperature Sensor read-out that gets its data from probes in the machine. This allows the operator to pre-set a certain temperature that the machine must reach before allowing it to go into automatic cycles.
The new Advanced Parts Counter screen features production status for the export breakdown of data for Production Count, Warm-up, Starved, Blocked, In Fault, Pending Action and Calculate Total Production Efficiency. With the optional Quality Control software system, based on an advanced product quality plan with scheduled inspection intervals, the operator sees an alarm right on the EPIC interface screen advising an inspection of the next part. The EPIC control will search for the latest CMM report based on a time code stamp. The operator is able to see trends, and pull quality inspection reports from the interface screen, knowing when to make offsets based on the data. The QA department can actually stop the machine from the lab if problems are detected.
"The EPIC R/T 45-12 possesses the characteristics of more conventional Hydromats - maintaining the integrity, reliability and flexibility of its predecessors - while featuring the latest in CNC rotary transfer technology - Embedded Motion Control (EMC), a special plug & play control architecture embedded into each toolspindle unit, offering fully independent functionality for each axis motion," said the spokesperson. "A modular tool spindle system with quick-change pre-settable heads helps the EPIC R/T offer quick and easy changeovers - typically one to three hours. The EPIC R/T 32/45-16, as with all Hydromat machines, supports lean manufacturing principles and competitive manufacturing at small, medium and large production quantities.
"A wide variety of rotary transfer machines offered by Hydromat give the manufacturing professional the right tool for the right job. The Hydromat machine is the solution for the elimination of secondary operations by producing parts complete from barstock, castings, forgings or cold formed blanks. The Hydromat machining platform eliminates secondary operations and reduces work in progress. Additional cost reduction occurs due to extremely short remnants and thin cutoff for significant material saving. Also increased productivity is partially due to modular tool spindle system with quick-change pre-settable tool heads for easy changeover."
Typical components suited for machining on Hydromats include automotive ABS and brake systems, fuel, electrical, engine and steering components; plumbing and HVAC valve castings, faucet bodies and gas valves and connectors; hardware power tool and appliance housings; electrical wire connectors and switch bodies; defense and aerospace fuse bodies and instrument housings.
Edge Technologies FMB Turbo 20-100 Bar Feeder
Edge Technologies' new FMB 20-100 bar feeder expands on the Turbo "Heavy Metal" line of hydrodynamic 12' through 24' bar loading magazine feeders. Quick-change polyurethane guide channels allow for quiet operation at high RPM while feeding round, square or hex bar stock. This unit also offers a one-size channel set that automatically adjusts for all material sizes. This feeder is compatible with all types of sliding or fixed, CNC or cam operated lathes with spindle bores up to 102 mm.
"The robust design of the Turbo 20-100's cast iron base and support stands are resistant to flexing," said the spokesperson. "With the unit weighing over 8,200 pounds, this keeps vibration from bent bars to a minimum, so a smooth operation is guaranteed. The double-pusher space-saving design is 4 feet shorter than single pusher bar feeders."
The Turbo 20-100 features a Bosch IndraDrive controller with a servo motor drive to the feed mechanism. Flexible control of bar length and rate of feed is designed to provide optimum practical and economic use of the bar feeder. Easy options on the operator control panel offer proper interaction between the bar feeder and the CNC lathe, with parameters clearly shown on the text display.
The polyurethane guide channels can be changed in about 10 minutes to accommodate multiple bar stock diameters. Oil filled guide channels envelope the stock, providing a guiding system for high RPM turning operations. During this process the rotation of the bar creates a hydrodynamic effect, centering the bar stock in the channel and reducing noise and vibration. The guide channel is securely closed with a toggle lever system while machining bars.
A roller steady device on the Turbo guides the bar stock between the bar feeder and lathe. Rollers or blocks provide feeding of round or profiled material. The rollers are quickly adjusted to the bar diameter.
Bars are placed in the storage magazine at the side of the guide channel. This area features a loading capacity of 11". The new bar is automatically positioned in the lathe ready for facing before the first component is produced. Loading time for a 12' bar is 30 seconds. Maximum adjustable feeding speed is 700 mm per second and maximum adjustable return speed is 1,000 mm per second.
The bar remnants are withdrawn to the back end of the magazine and a gripper extracts it out of the collet and deposits it into a remnant basket. The gripping device is used to both insert the new bar into the bar stock collet and to extract the remnant. It is not necessary to chamfer the bar if it is cleanly cut. No adjustment for bar size is necessary and it is completely self-centering. Bar pusher collet changes can be done less than one minute.
For more information contact:
Kevin Shults
Hydromat, Inc.
11600 Adie Road
St. Louis, MO 63043
314-432-0700 Ext. 4252
kshults@hydromat.com
www.hydromat.com
IMTS 2014 Booth S-8348