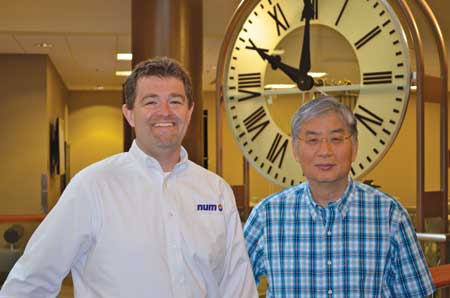
(l-r) Steven Schilling, Managing Director of NUM Corporation, and Yung C. Shin, Professor of Mechanical Engineering at Purdue University, standing in front of the university's historic Heavilon Hall clock.
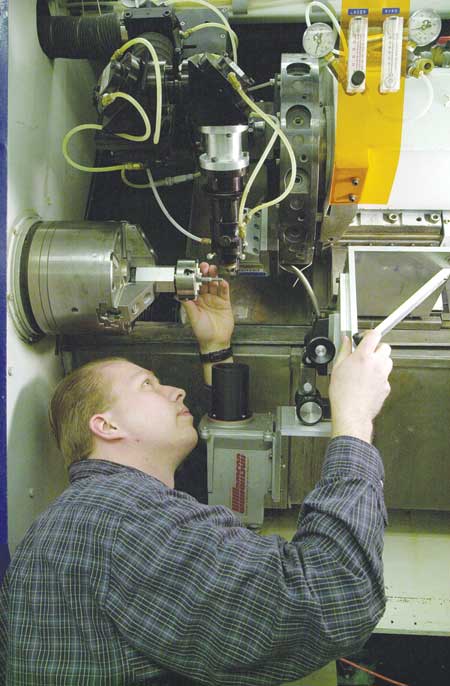
Many of the CNC machines in Purdue University's manufacturing research laboratories are based on NUM CNC systems, such as this laser-assisted machining system for ceramic materials.
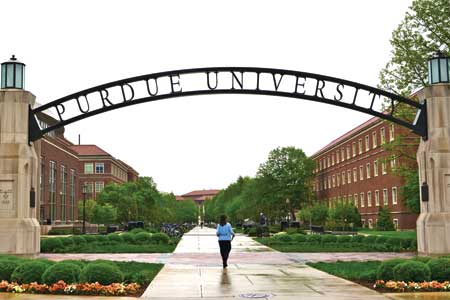
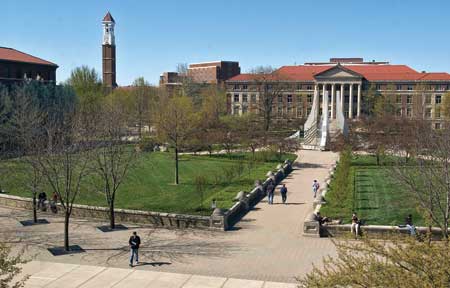
Purdue University's prestigious College of Engineering has chosen to equip one of its key educational laboratories with NUM's open-architecture CNC systems and 3D simulation software.
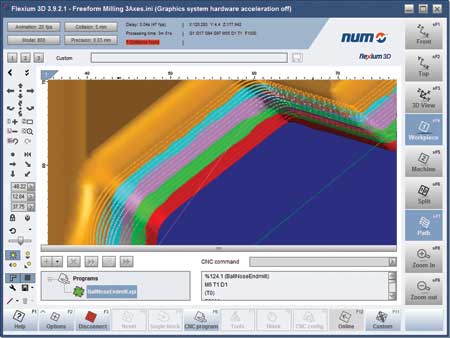
The new laboratory will have six computer workstations, each capable of true 3D workpiece simulation without needing access to a CNC system.
Purdue University's prestigious College of Engineering has chosen to equip one of its key educational laboratories with NUM's open-architecture CNC systems and 3D simulation software. The equipment will provide students with hands-on CNC programming experience and help to familiarize them with advanced CNC machine tool operation and control techniques, using a powerful combination of virtual machines and physical high performance CNC demonstrator systems.
Purdue University's College of Engineering comprises 14 schools and departments - each specializing in a particular engineering discipline - and is currently undergoing further major expansion. As part of the expansion, Purdue University is upgrading the mechanical engineering laboratory at the university's main campus. This laboratory is principally used for teaching students the basics of CNC control and programming and introducing them to machine-based manufacturing processes and techniques. It is currently equipped with several 2-axis CNC demonstrator machines based on NUM 760 and 10xx series CNC systems, together with a NUM 2D simulator.
According to Professor Yung C. Shin, who oversees all CNC-related education and research activities at the School of Mechanical Engineering, "When we set up the mechanical engineering lab in the 1990s, we looked at CNC systems from many manufacturers. However, most of the systems were like black boxes so their operation was difficult to understand, which was far from ideal when we wanted to teach the basics of CNC control. We therefore decided to base our educational platform on NUM's CNC systems, primarily because of their open architecture and the fact that the NUM was enthusiastic about helping us to use its products in this role. The openness of NUM's CNC, especially with regard to NC code and I/O facilities, enables us to clearly demonstrate the exchange of data between the PLC, CNC and drive electronics, and simplifies integration with other lab equipment. Also, many of the CNC machines that we use in our manufacturing research labs are based on NUM CNC systems, so there is a high commonality of coding."
NUM has acted as a CNC partner to the School of Mechanical Engineering for some 24 years. Steven Schilling, General Manager of NUM Corporation in Naperville, IL, points out the importance of such long-term support for educational establishments, "The staff at Purdue always have access to our technical support people and receive engineering help whenever they need to reconfigure or reprogram CNC systems for new projects. This close cooperation ensures that Purdue's laboratory CNC equipment has the latest features and tools to aide students in developing new machining technologies."
The latest upgrade to the mechanical engineering laboratory's CNC equipment is extensive. NUM has supplied two Flexium 68 CNC systems configured for milling applications, each with an NCK (Numerical Control Kernel), PLC, HMI and 3D simulator hardware and software, plus additional simulator dongles for four PCs. Flexium 68 provides a very versatile foundation for educational and research applications such as this, where the type of machine and the control approach change over time. As standard, the NCK accommodates up to 5 axes/spindles on a single channel, with full interpolation on 4 axes. Single NCK options can expand this to 32 axes/spindles in up to 8 channels, with up to 32 interpolated axes, while multi-NCK configurations can handle more than 200 axes.
To help improve ergonomics, the laboratory has installed two desktop consoles for human-machine interaction. Each console is equipped with a NUM FS152i operator panel and an MP04 machine panel, fitted with CAN interfaces. The operator panels feature 15 inch LCD screens and integral industrial PCs with solid state drives, run an embedded version of Windows and are connected to the university's Ethernet network. Each console can be used for simulation or for controlling the laboratory's CNC demonstrator machines.
NUM has also supplied all the motors, drives, power supplies and associated hardware for two additional 2-axis demonstrator machines. Both of these combine latest-generation bi-axis NUMDrive C servo drives with BPH brushless servo motors. One of these machines uses the HP version of the drive with high performance control loops, to facilitate research into applications involving very fast or precise kinematics.
Using Flexium, Purdue University's students and post-graduate researchers can now investigate CNC techniques to a very detailed level. All CNC, servodrive, I/O and PLC setup and programming is performed using a unified software toolset to help shorten the learning curve, increase productivity and work satisfaction, and encourage collaborative effort. The system's inherent open architecture has multiple advantages. Application-specific HMIs (Human-Machine Interfaces) can be easily created or modified using industry-standard editors and languages such as HTML, JavaScript, Visual Basic, Delphi, C or C++, while the PLC can be programmed using any IEC 61131-3 compliant object-oriented graphical or textual language. In addition, students who need low-level control of the NCK - for example, for real-time axis transformations - can use dynamic operators in the code, while techniques such as real-time compensation can be developed using embedded loop control macros in the servo drives.
The Flexium 3D graphical simulation capabilities that Purdue University is installing in the mechanical engineering lab will improve work flexibility significantly. Until now, the simulation software required physical connection to the CNC system - which meant that only one student at a time could use it - and was limited to basic 2D simulation of path lines. The lab now has six separate simulator stations - two on desktop consoles and four on standalone PCs - each capable of true 3D workpiece simulation in standalone mode, without needing access to a CNC system. Six more networked PCs are also being installed, allowing students to perform simulation at different locations.
Students are now able to simulate and optimize any ISO-code part program that they have written, with full visualization of the tool center point path and workpiece material removal, backed by automatic checking for collisions between machine components, the tool and the workpiece. The simulation software currently supports 3-5 axis turning and 3-axis milling/drilling, as well as waterjet and plasma contour cutting and can be transferred between applications very easily. It creates a dynamic color image, showing the workpiece as a 3D volume that can be rotated and viewed from any perspective.
Purdue University plans to make the new CNC facilities available to students in the fall, as Professor Shin explains, "We need to be able to provide more students with hands-on experience of CNC programming and visualization as soon as possible. There is now a resurgence in the domestic automation market thanks to new processes like additive manufacturing. CNC programming skills are once again in short supply. Students are excited by CNC programming when they can see the results of their efforts - whether that's on a simulator, a CNC demonstrator or machine tool - which is why our new facilities are such an important educational tool. Some 65% of our graduates go on to pursue careers in manufacturing - and many have become professors in their own right. I like to think that when they set up their own laboratories they will remember the grounding that we gave them."
For more information contact:
Steve Schilling
NUM Corporation
603 East Diehl Road, Suite 115
Naperville, IL 60563
630-505-7722
sales.us@num.com
www.num.com