
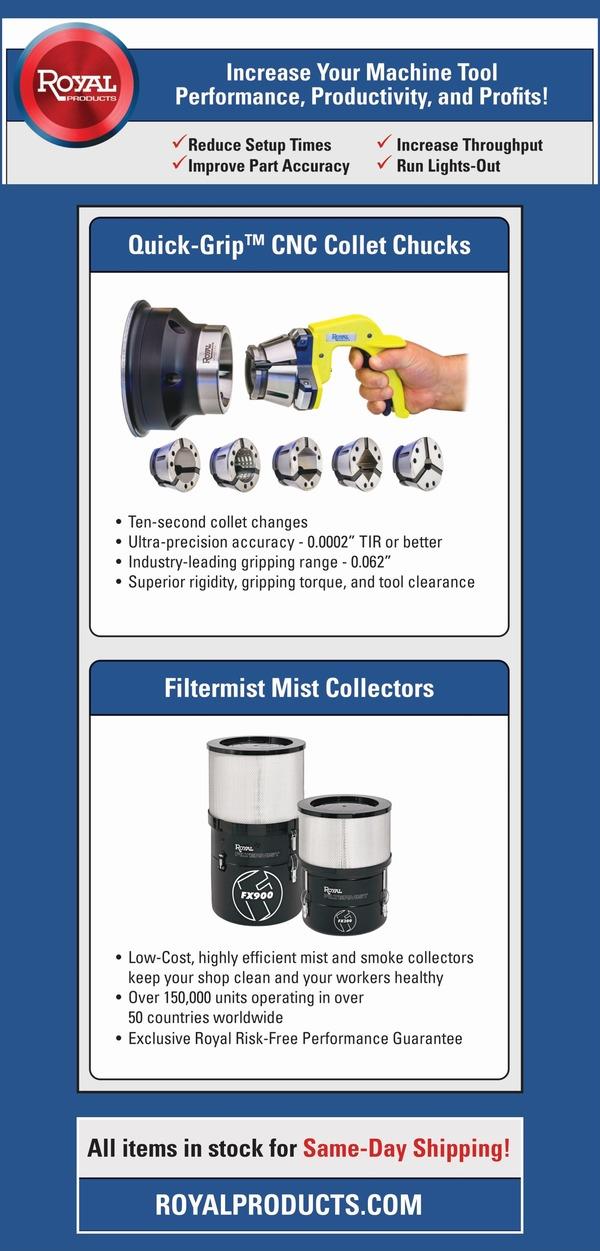
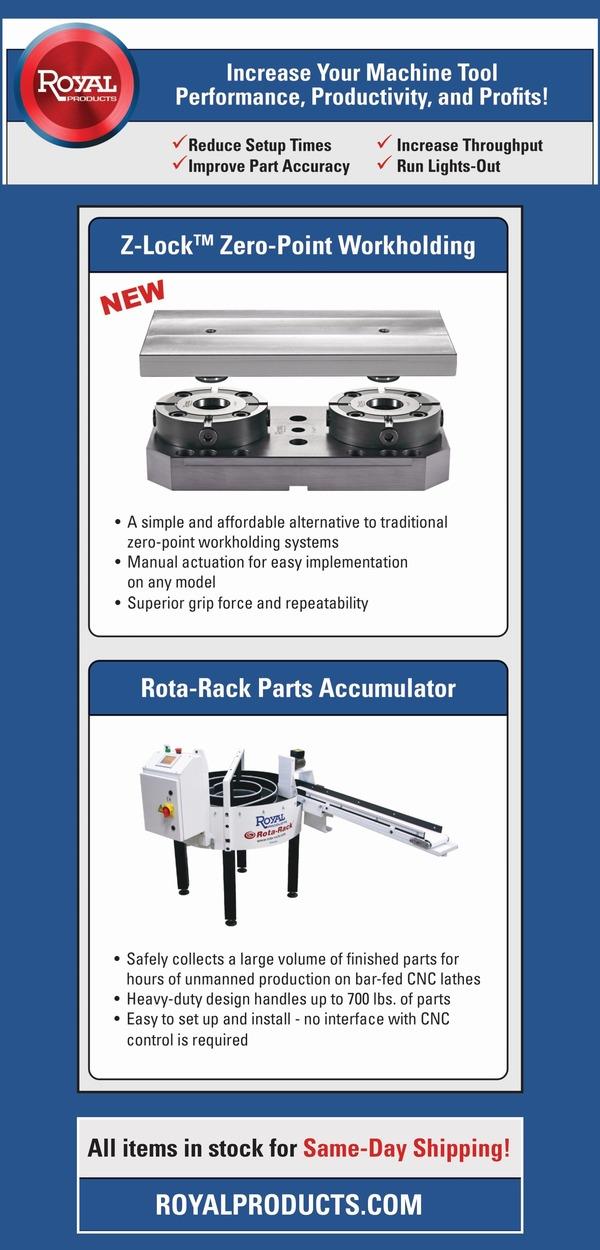

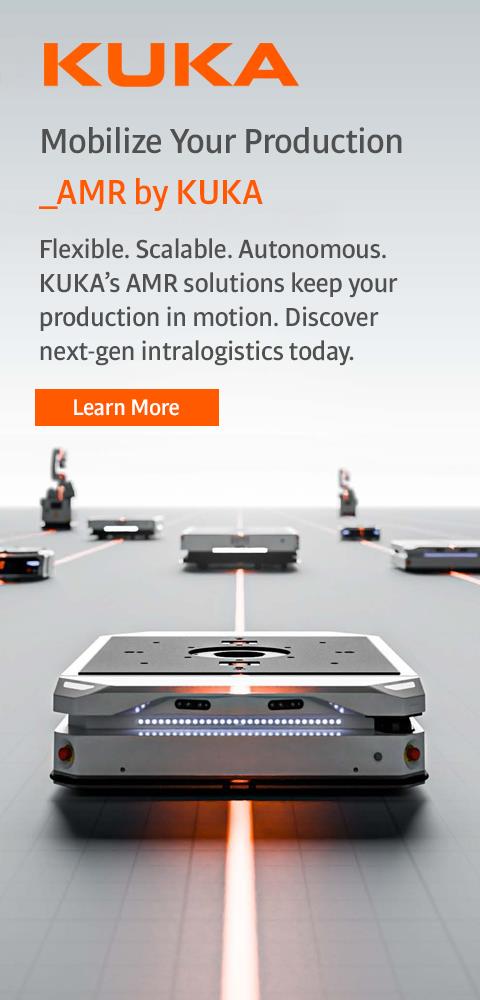
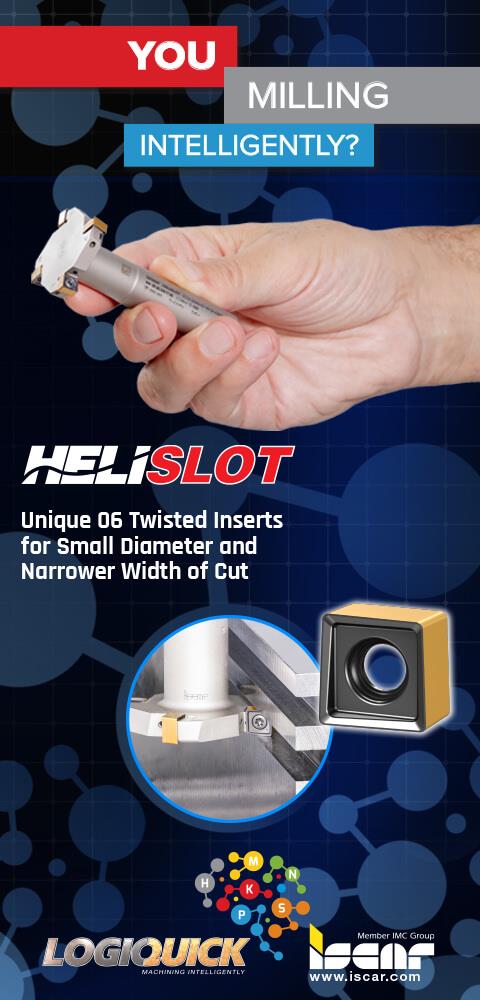
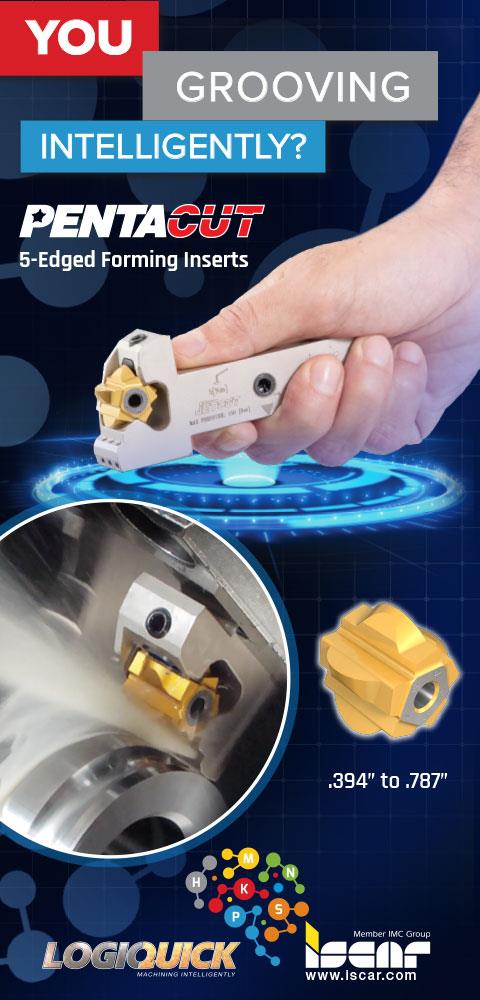
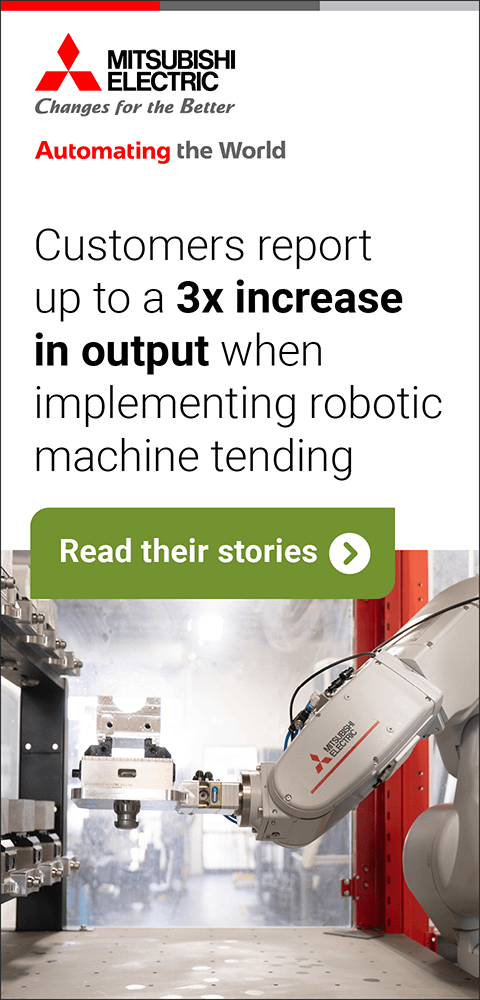
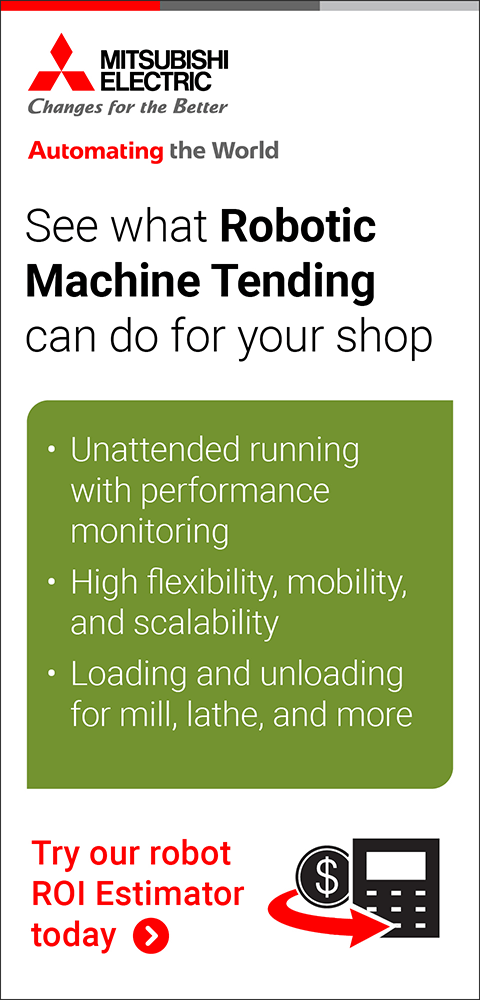
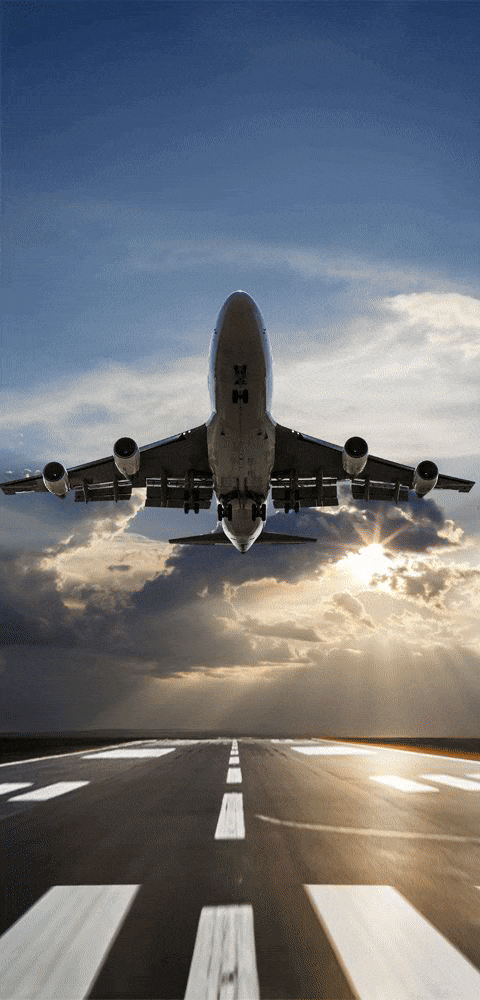
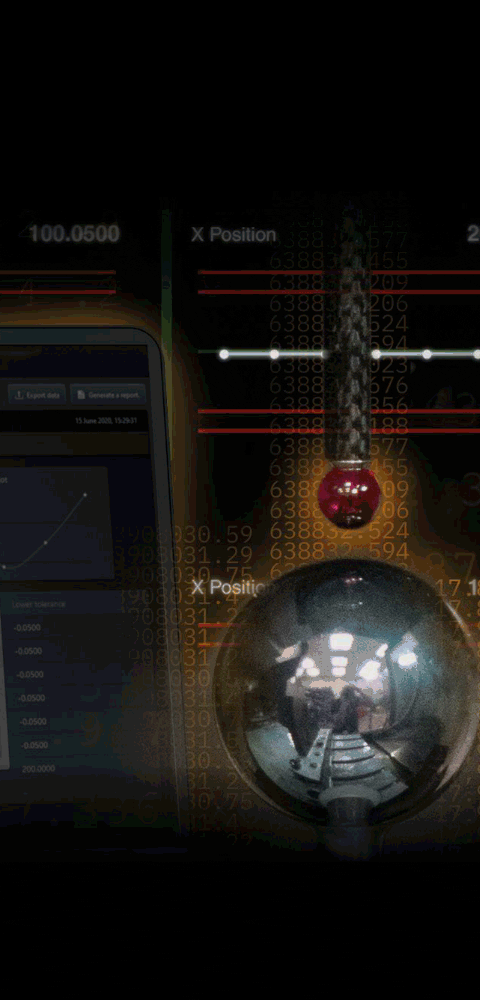
CNC for Plasma Systems
June 1, 2013
Hypertherm offers the EDGE Pro Ti, a CNC designed with integrated drives, motors and multiple torch height control interface options.
This CNC can be used for small to medium sized cutting tables and works with all plasma systems including Hypertherm's Powermax, HySpeed HSD130 and MAXPRO200. It includes features such as enhanced cutting process support for plasma, waterjet and oxyfuel cutting methods, and supports Rapid Part technology when combined with a Hypertherm Sensor Ti or ArcGlide torch height control. In addition, automatic torch height adjustments help ensure optimal consumable life and part quality without operator intervention.
The system also contains Hypernet connectivity enabling the use of True Hole technology when combined with an ArcGlide THC and HyPerformance Plasma HPRXD system. The Hypernet connectivity facilitates remote troubleshooting using a built in Remote Help function and standard wireless networking.
"The EDGE Pro Ti CNC replaces the EDGE Ti CNC in the entry to mid-range market, and does so with substantially more to offer in terms of application range and process capability for plasma, oxyfuel and waterjet cutting operations," said Bob Boyes, Product Manager for Hypertherm's automation team.
"The EDGE Pro Ti is designed for reliability and ease of use while leveraging all the benefits of Hypertherm's Phoenix Version 9 software," said a company spokesperson. "All necessary cut process parameters can be embedded within the CAM software's customer part program for reduced setup time, the elimination of common process errors and improved productivity."
For more information contact:
Hypertherm Inc.
P.O. Box 5010/21 Great Hollow Rd.
Hanover, NH 03755
603-643-3441
info@hypertherm.com
www.hypertherm.com
< back