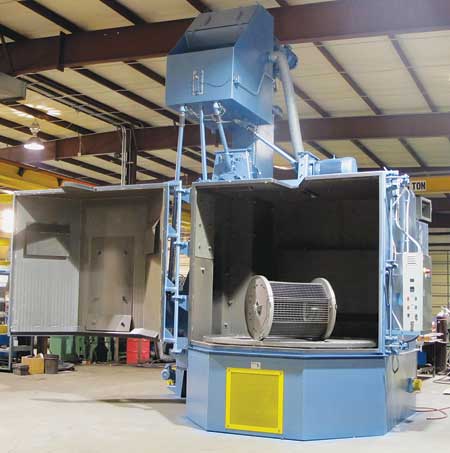
Blasting cabinet arrangement.
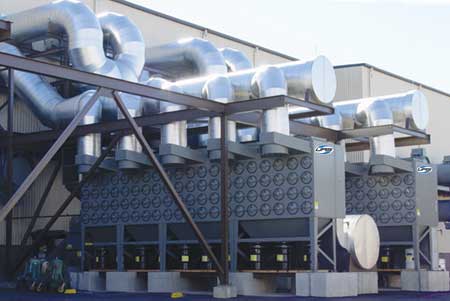
Cartridge dust collection system on abrasive blasting application.
Abrasive blasting is the operation of forcibly propelling a stream of abrasive materials against a base material surface in order to finish or prepare parts for additional processing. A significant amount of dust is generated as the stream of abrasive material displaces any surface coatings and the base material. The combination and variety of abrasive materials and base materials also generates complex emissions of various sizes, shapes and concentrations. Inhalation of these emissions poses health risks to plant personnel, and in some cases presents safety risks in the form of combustible and/or explosive dusts. Therefore, it is critical to provide an effective air pollution control system that will keep the work environment safe and employees healthy.
Abrasive blasting equipment can be categorized in two basic types: blasting cabinets and blasting rooms. In general, the type chosen depends upon the specific application, including the size of the process components, the materials being used and the volume. Blasting cabinets are an enclosure where the operator stands and controls the process from outside of the enclosure. Blasting rooms are an enclosure where the operator works and controls the process from within the enclosure. The type of enclosure being used will determine the approach necessary for proper emission control. Abrasive blasting suppliers or manufacturers can often provide recommendations associated with the emission control system to ensure that enclosures are properly ventilated. Developing an effective emission control strategy begins with a complete understanding of the process and nature of emissions.
Emission Risks and Regulations
As part of the blasting operation, abrasives, surface coatings and the base material are shattered and pulverized, creating hazardous emissions covering a wide range both in size and composition. Several governing bodies and safety organizations have developed regulations to mitigate the risks associated with abrasive blasting emissions.
A high percentage of the particulate are within what is known as the respirable range, meaning that it is small enough to penetrate the nose, upper respiratory system and lungs. The small particulate size along with the emission's chemical composition or potential toxicity poses a serious threat to worker health. As a result, the Occupational Safety and Health Administration (OSHA) and other organizations such as the National Institute of Occupational Safety and Health (NIOSH) and the Centers for Disease Control and Prevention (CDC) have established permissible exposure limits (PELs) for many of the bi-products commonly generated during blasting.
In addition to the indoor air pollution regulations, the U.S. Environmental Protection Agency (EPA) has also begun regulating processes such as abrasive blasting. The basic premise is that indoor air pollution, unless properly controlled, will result in outdoor emissions. The EPA's Metal Fabrication Hazardous Air Pollutants (MFHAP) rules include abrasive blasting as a regulated process requiring qualifying manufacturers to maintain zero percent opacity emitted from any building opening, such as an overhead door or roof exhauster.
Accumulated dust also presents a potential risk of combustion or explosion under the right conditions. The National Fire Protection Association (NFPA) publishes standards associated with specific materials and processes where combustible or explosive dusts are present. NFPA standards provide practical steps to reduce the likelihood of a fire or explosion happening and provide the necessary safety provisions should an explosion occur. Safe handling of combustible dusts is also currently an OSHA national point of emphasis with additional regulation expected.
These are several of the important safety issues and regulations to be considered and reviewed as part of implementing a successful strategy to control abrasive blasting emissions. To ensure full compliance, operators need to consult local authorities having jurisdiction (AHJ) in order to determine all applicable regulations and steps necessary to achieve compliance.
Controlling Emissions
The purpose of the emission control system is to reduce the dust to an acceptable level within the enclosure and contain the particulate that would otherwise escape. A well-designed and successful emission control system involves three primary components. The generated contaminant must be captured or contained effectively, safely conveyed or transported to equipment that is configured to efficiently collect and remove it from the airstream. If any one of these aspects is completed incorrectly, the entire system may not achieve the necessary level of safety or optimal performance.
Capturing the Contaminant
The correct method to capture or contain the particulate is dependent, in large part, on the specific design of the blasting enclosure. For blasting cabinets, internal air volume should be turned over 20 times per minute and the average inward velocity of 500 feet per minute (FPM) is recommended for all openings to keep the machine under vacuum. The extreme forces involved in the process generate particulate that possesses a large amount of momentum so impingement baffles will work with the airflow to contain the particulate within the cabinet. As part of working procedures, operators should wait to open the cabinet door until the dust-laden air has been evacuated from the volume.
Blasting rooms by design are larger volume than cabinets; however, the same principles presented for the blasting cabinet would apply to the blasting room. With the larger spaces, there is less emphasis on local capture so capture can be accomplished in a cross draft or a downdraft arrangement. The draft velocity for each arrangement is recommended to be approximately 100 FPM. Additionally, a continuous flow of clean make-up air through doorways or other openings is also recommended as the air volume is being changed over. Note that because the operator will be exposed to the emissions - in this approach an approved personal protection device will still be required.
Conveying the Collected Material
Based on recommended capture techniques, the total air volume required can be calculated and the conveying portion or duct system can be designed. The duct system needs to be designed to maintain a transport velocity of approximately 3,500 - 4,500 FPM to convey the particulate. Achieving the target velocity range will reduce dust accumulating within the duct and avoid the associated fire or structural risks. Exceeding the recommended velocities can lead to excessive wear and tear on the components as well as increased energy costs. Likewise, the number of elbows or bends should be kept to a minimum and the dust collector should be located as close as possible to the blasting operation to reduce the total system pressure loss. Inspection ports and cleanouts are also recommended to ensure the ducting remains free of product build-up.
One method of controlling the airflow and transport velocity is through the use of a variable frequency drive (VFD). Based on an input, the VFD can adjust the RPM of the blower fan to maintain the target airflow as system conditions change. Maintaining the required airflow improves system performance by maintaining the proper capture velocity at the enclosure and transport velocity through the duct while reducing potential wear and tear on duct and filters. VFDs also offer energy savings of up to 30% on the operating costs of the blower.
Contaminant Collection
Several different types of dust collection equipment can be utilized to capture the emissions from abrasive blasting operations. Baghouses and cartridge filter dust collectors are the two most common types selected to control these emissions, with cartridge collectors emerging as the preferred choice based on their high filtration efficiencies and improved installation, operation and maintenance. Cartridge collectors also offer a smaller overall footprint and lower cost of ownership.
Cartridge collectors need to be configured and sized correctly to achieve optimal performance on abrasive applications. Determining the appropriate dust collector size is based upon the filtration velocity or ratio of air volume to filter area, which is known as the air-to-media ratio (AMR). A typical AMR for a cartridge dust collector on abrasive blasting applications is around 2.5:1.0. However, additional process considerations including equipment duty cycles, loading conditions and filter life expectations will influence this process.
Proper filter media selection is very important to the overall successful operation of the exhaust ventilation system. Filters that feature surface-loading technology, such as nanofiber or ePTFE membranes, offer high filtration efficiencies with excellent dust release characteristics. Due to the abrasive nature of the particulate, spunbond polyester media is commonly used in this application to add additional filter durability. To reduce the chance of filter abrasion or damage, an abrasive inlet can be installed on the dust collector, which works to slow down the air stream and reduce particulate momentum prior to entering the dust collector.
Configuring the dust collector for specific hazards such as combustible or explosive dusts is also important. Configuration options include equipping dust collectors with explosion vents or a suppression system in accordance with NFPA regulations. When dealing with hazardous or toxic dusts, safety after-filters or HEPA filters could be incorporated.
Baselining initial performance and a successful preventative maintenance plan are important for continued performance and safe operation. Initial measurements should include the total airflow volume and the operating static pressure. Regular maintenance includes monitoring filter pressure drop, regularly emptying the collection drums and ensuring that the pulse cleaning system is operating correctly.
Summary
Abrasive blasting is a common operation that presents hazards associated with the generated process dust and emissions. Taking a systematic approach to ensure safe and proper capture, conveyance and collection of the particulate will lead to optimal performance of the dust collection equipment and a safer environment for workers. Consult a dust collection expert to review and understand the requirements of these systems and to prescribe a successful solution so that associated risks are mitigated and plant personnel are appropriately protected.
Authored by Travis Haynam, Director of Business Development and Joe Topmiller, Senior Application Engineer, United Air Specialists, Inc.
For more information contact:
United Air Specialists, Inc.
4440 Creek Rd.
Cincinnati, OH 45242
513-354-8710
www.uasinc.com