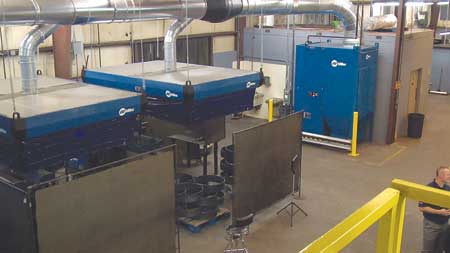
Chandler has complemented its manual weld cell fume extraction systems with specific hoods and a centralized collection point for its automated applications.
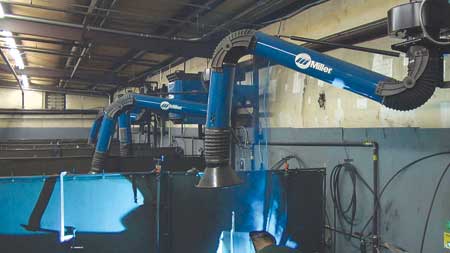
Fume extraction in manual welding cells at Chandler is achieved through wall-mounted fume extraction systems.
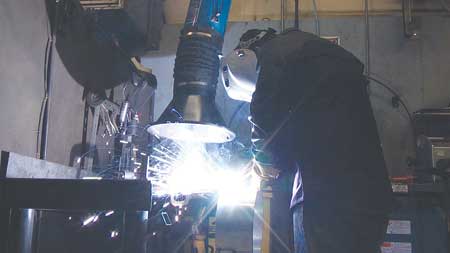
Weld fume extraction through source capture is consistently one of the most effective methods of removing weld fume from the work environment.
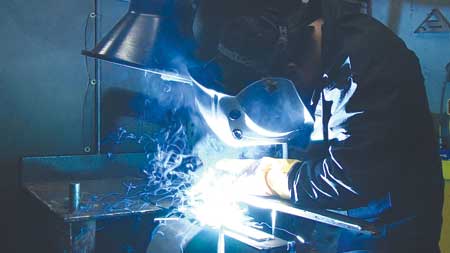
Source capture proved more effective than ambient exhaust and ventilation fans.
Chandler Equipment started out as a farm equipment business 30 years ago. The company then expanded into industrial waste-hauling tanks. Today the company manufactures hatches and ports for tank vessels in Springdale, AR. The company supplies large oil and gas companies with the parts they need for waste tanks used in North America's current oil and gas boom. Chandler fabricates the accessories for the tanks - tank hatches, valving and the fittings for the tanks are the company's sweet spot.
Chandler's welding takes place in a combination of automated and manual welding cells. Material thickness ranges in size from 14 gauge up to 1/2", all typically welded with short-circuit and spray-transfer MIG welding processes. On both the manual and automated side of the Chandler welding business, the vast majority of the work is mild steel. As aluminum and stainless steel became a growing presence in the shop, however, the need to rid the building of fume and smoke became even more critical (hexavalent chromium, for instance, can be produced in some applications when welding with stainless steel filler metals).
Weld fume particulate is among the smallest encountered in work environments. Most weld fume particles are less than 1 micron in size - airborne dust is large in comparison at 1 micron and larger. Chandler worked with Miller and his local Airgas distributor to determine a system that was capable of removing this microscopic weld particulate, improving the overall air quality in the shop and not limiting the shop's future growth capabilities by taking up too much space. The final choice: a combination of wall-mounted fume extraction systems and a centralized fume extraction system.
Cleaning the Air
Jeff Chandler got his start in the family business as a welder. Today he runs the company, but the daily grind of welding fume and dust particles he experienced on the job remains fresh in his mind. He wanted to give his employees the highest quality work environment possible through filtration. This effort started out with ambient solutions such as exhaust and ventilation fans. It did not take long to realize that these fans would not work.
"We had been using ventilation fans and exhaust fans over a period of time," said Chandler. "It just did not work. There was always a cloud around during the workday. And in the winter the cold air we brought in through the ventilation meant we were spending a fortune trying to heat the place. We needed to do better to clean the air."
Chandler contacted Steve Jones, an account manager with Airgas Mid South in Springdale for direction. Knowing that source capture would provide a more optimal solution for capturing weld fume and particulate by removing it before it ever had a chance to enter the work environment, Jones suggested the FILTAIR SWX wall mounted dual-arm fume extraction system from Miller.
"Jeff started out with the purchase of the two dual-arm wall mount systems for the operators in those stations and was very happy, very satisfied," said Jones. "The two systems were working out so well for them, the shop started cleaning up immediately. Jeff gave us a purchase order for three additional units."
While the success in the manual welding cell was phenomenal, there remained a haze in the larger automated portion of the facility.
"Once Jeff made the decision that they needed to continue to move forward pulling the welding fumes out of their shop, they sat down and started researching the automated side of their business," said Jones.
Finding the Right Filtration System
Chandler spent months investigating suitable options to capture the weld fume from the automated cells. There were systems incapable of capturing the submicron weld particulate. There were cross-air systems that exchanged outside air with the inside air - harsh on the heating bill in the winter months as it would pump in cold air from the outside. There were bulky systems that did not seem to be the right fit for the building, and systems that would require the building and welding cell design to be reconfigured. It came down to three systems - one of which was the FILTAIR Industrial Centralized System matched with FILTAIR Automation Hoods designed specifically for automated weld cells. Chandler ultimately selected a FILTAIR 12000 system with 12 filter packs (the system comes in options of either 2, 4, 6, 8 or 12 packs).
"When we came across Miller and the FILTAIR system, we found that everything was pretty much confined to the robot, and the particles could be taken off right when it was welded," said Chandler. "When I found out the footprint of the machines was 65% smaller than the average centralized collector, we took an even closer look."
That smaller footprint gives Chandler significant flexibility for future growth.
"We are a little confined for space in some places and we were looking for something that would fit in those spaces that we had," said Chandler. "As the years go by you want room for growth, like we have some more spots to put more robots later on, so robotic welding, as we get bigger, we are able to add on to this system and still be able to use it and not have it be in the way. So I think probably one of the most important things was the confinement of space and it not taking up more room, because in a building like we have, every square foot is essential in the day-to-day operations."
Unlike some of the more rigid systems, which require traditional ductwork that would need to be torn out if expansion were necessary, the FILTAIR system was installed with a unique snap-tight interlocking ductwork system. When assembled, the design ensures a sealed system that can also be easily changed as the business grows. New cells can be added without tearing out the system.
"The ductwork is a whole lot smaller than what a lot of the other people bid out. We were bidding out some huge ductwork and I did not know how we were even going to put it in this building," said Chandler. "The adjustable part is absolutely important. For future use we will be able to expand in areas and add on when we need to. Everything is flexible where we can hook right on to it or 'T' into the group that is existing today. No other system could offer that feature."
Another advantage to the system is sound quality. The FILTAIR is also one of the quietest fume capturing systems on the market. The noise level is so low that Chandler employees can carry on normal conversations while right next to collectors.
"You can just barely hear it. You can talk being up next to it. That is very important, especially when you are giving instructions on things that need to be done," said Donnie Moore, Shop Foreman, Chandler Equipment.
The maintenance of the system has been simple, according to Moore, and has been successful at its most important task: removing weld fume particulate. At a Minimal Efficiency Rating Value (MERV) rating of 15, the FILTAIR is efficient at removing 99% of weld fume. A Linear Jet Automatic Cleaning System works within the system to keep the particle surface loading FilTek filters efficient at capturing weld fume longer than other filters. When it does become time for maintenance, the filters' surface-loading capture of fume particles allows for easy cleaning.
"With the centralized system, the benefits are a lot less maintenance, a lot less cleaning for our part. It does it all itself," said Moore. "It is user-friendly."
Reduced Energy Consumption
One surprise with the installation of the FILTAIR system was the consistent temperature of the building. Before, when pulling cool or hot air from the outside with the ambient system, the thermostat would spike one way or the other. Today the centralized system provides a consistent environment that has kept the thermostat and the resulting heating or cooling bill in check.
"We always had a problem with the flow of air because, on different days, the air outside was different," said Moore. "Now we are not even turning the heat on in here, and the system itself is keeping it warmer and we have lowered our heating bill. With it taking the fume out of the air, we do not have to clean as much as we used to."
Change in the Air
The effect on the atmosphere at Chandler was immediate. Within a few hours of flipping the switch on the newly installed FILTAIR centralized system, the building cleared and the air quality improved. Gone was the smoky haze hanging above the manufacturing floor.
"I was amazed," said Moore. "The clean air, it was just like it cleared up in a second."
The newfound clarity inspired Chandler to spend a day cleaning the entire facility from the factory floor to the rafters above. A cleansing that remains today, thanks to the fume extraction systems quietly hard at work.
"We cleaned the whole building, all the beams throughout, so everything would stay clean from now on - so we would not have any weld fume problems or particles in the building," said Chandler. "I want this facility to be how I would want it if I were welding. The well being of my employees is very important."
Authored by: Al Hilbert, Product Manager, Miller Electric Mfg. Co.
For more information contact:
Miller Electric Mfg. Co.
P.O. Box 100
Lithonia, GA 30058
800-426-4553
info@millerwelds.com
www.millerwelds.com