
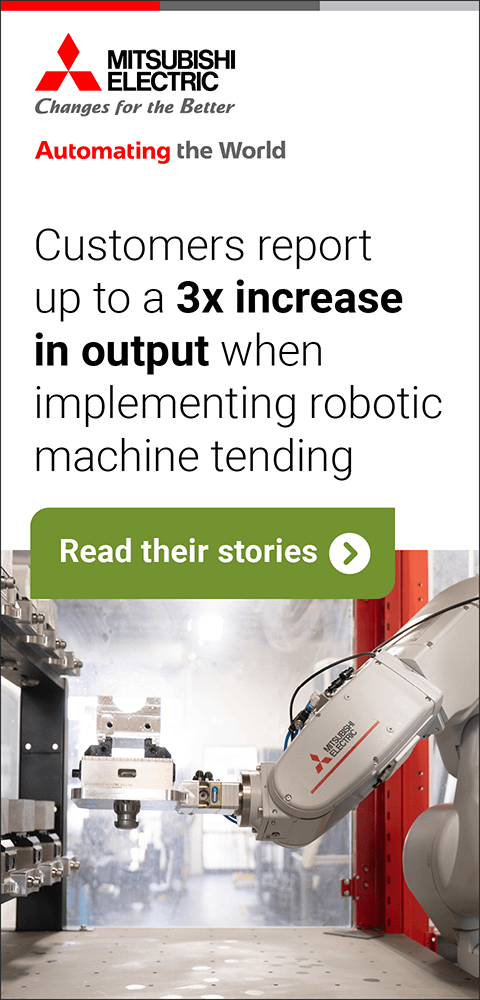
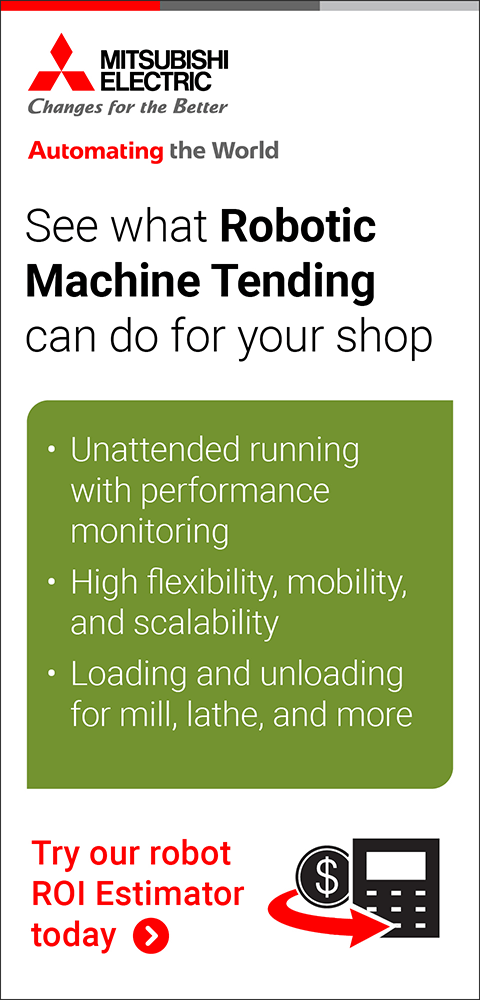
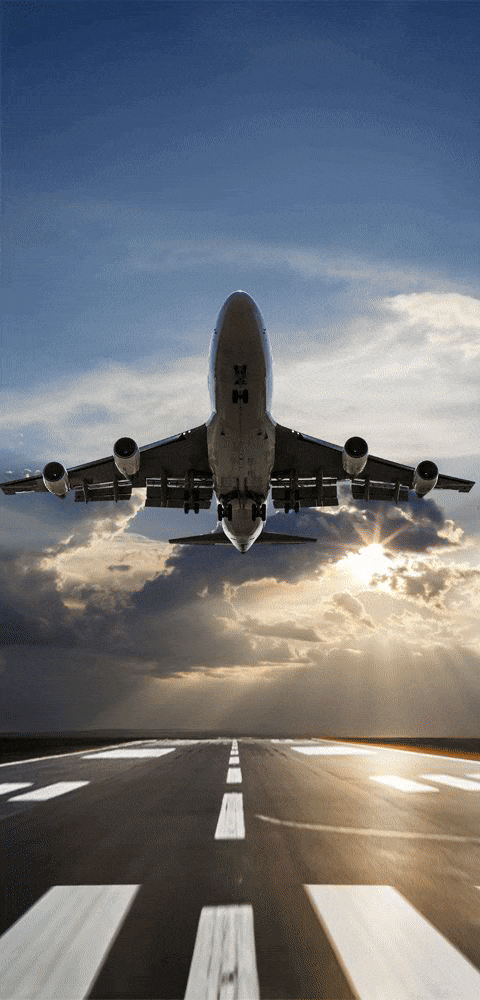
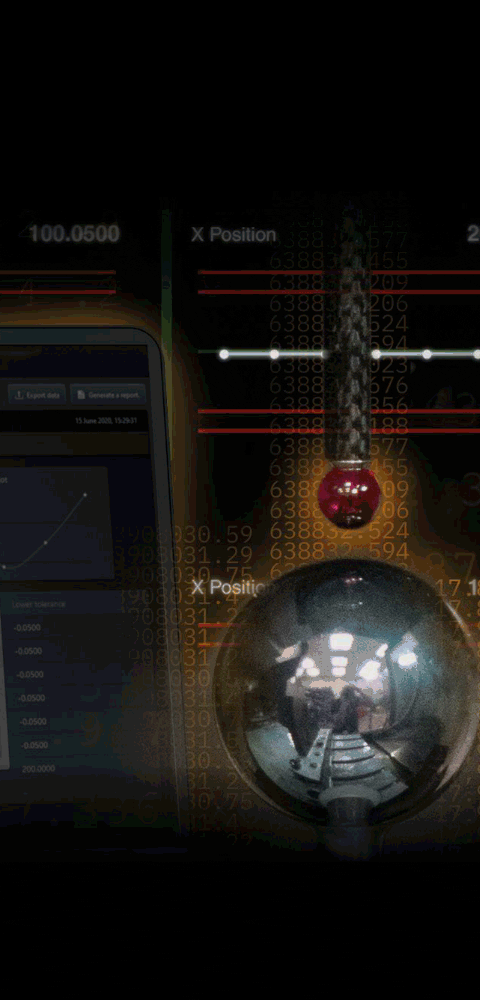
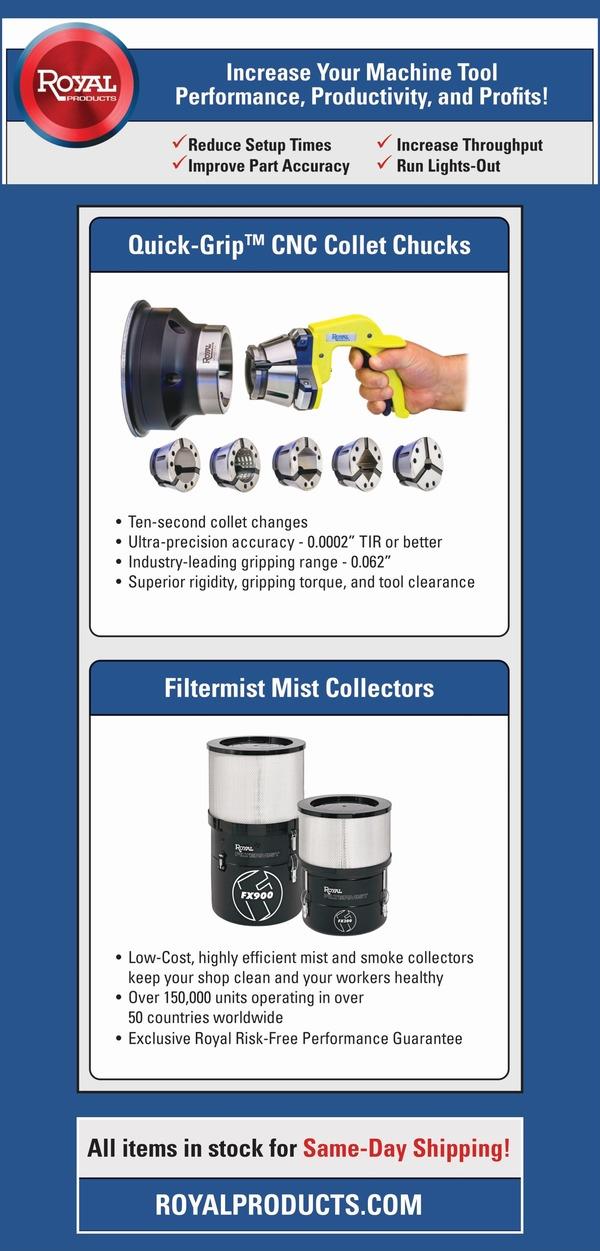
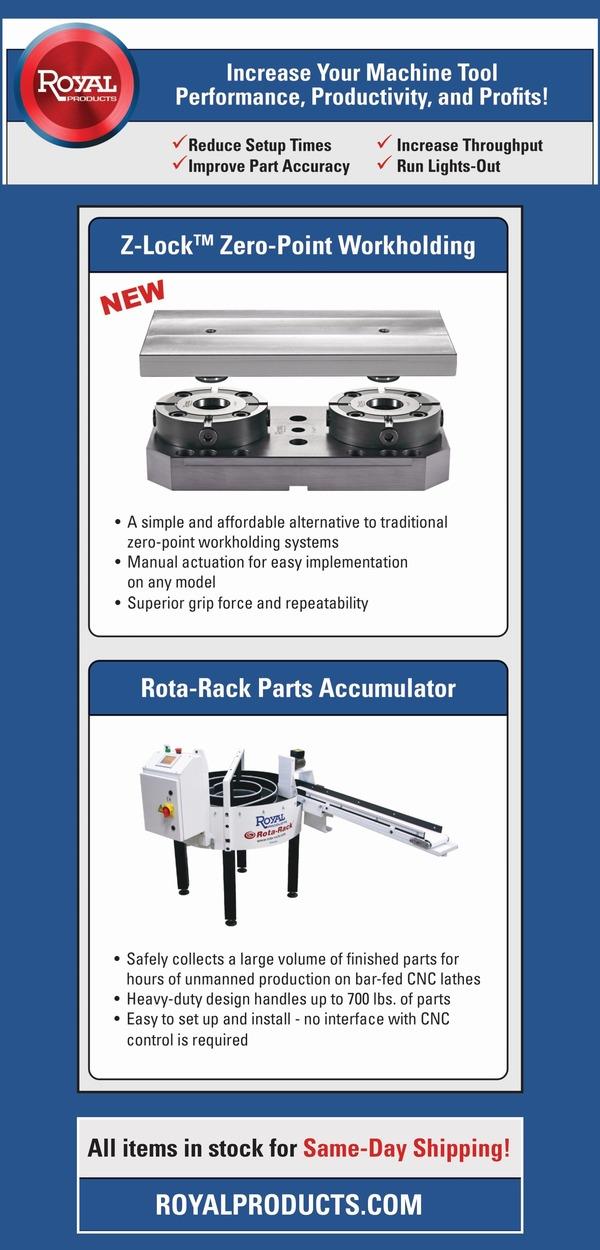

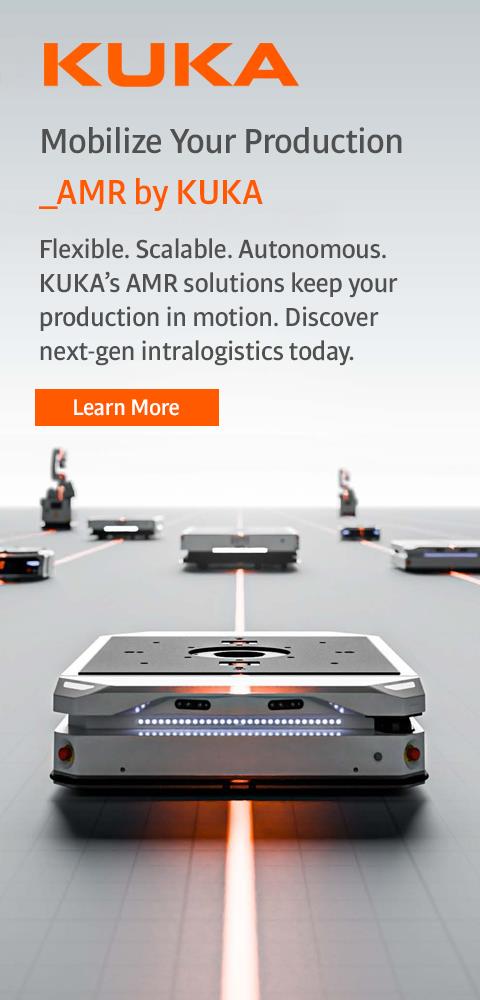
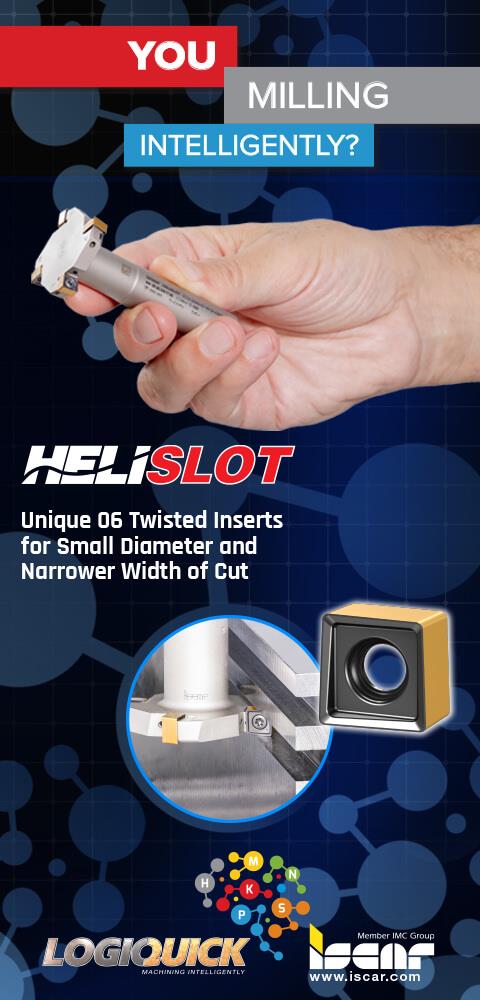
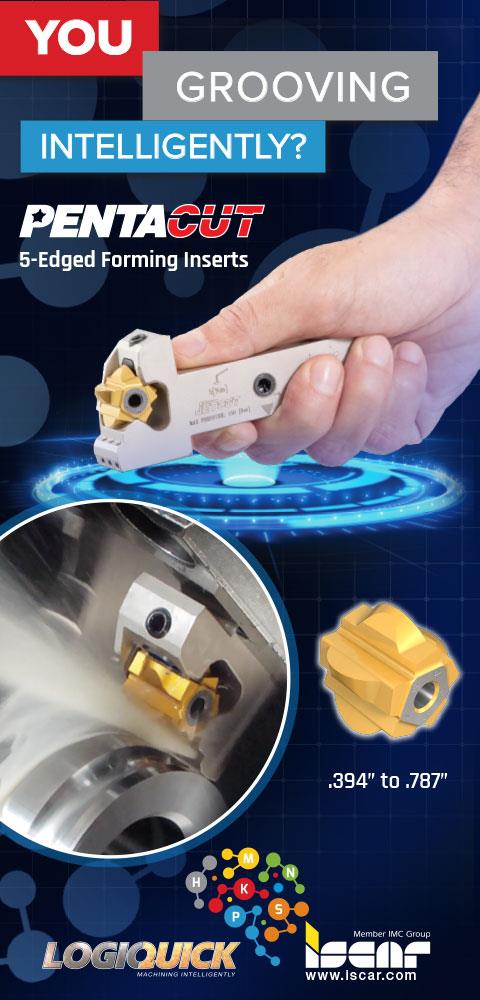
Renishaw Seminar Aims to Transform Your Manufacturing with the Power of Process Control
May 16, 2013MAY 2013 - On June 6, 2013 Renishaw will present a manufacturing process control seminar on metrology solutions to improve machining performance and increase manufacturing process capability. The event is presented in conjunction with Okuma and software providers Prolink and Applied Automation Technologies (AAT) at Okuma's THINC facility in Charlotte, NC. Content will focus on Renishaw's Productive Process Pyramid, a systematic approach to reducing waste and variation in manufacturing processes through a variety of innovative technologies, proven software and expert support. The seminar will be offered twice - a morning session beginning at 9:00 a.m. and an afternoon session at 1:30 p.m. Both morning and afternoon attendees are invited to a hot lunch served between sessions (12:00 p.m. to 1:30 p.m.) and each session will include product demonstrations in Okuma's showroom. The event is free though participants must register at renishaw.com/usroadshow and select which session they plan to attend.
The Renishaw Productive Process Pyramid provides a building-block approach to eliminating variation at its source, controlling it from the bottom up in four steps: establish stable machine operating conditions; address predictable sources of variation, such as location of the part, size of tools and offsets; deliver intelligent in-process feedback; and ensure the process and the part are checked against specifications via post-process monitoring.
Prolink offers an entire suite of software solutions to automate data collection and quality analysis information and share it organization-wide. The company's QC-CALC statistical process control (SPC) program is compatible with Renishaw's most advanced metrology hardware. It automatically collects data, creates a database, and displays the collected information in graph form with easy filtering for detection of negative trends and generation of exception reports.
AAT's Computer Aided Part Programming System (CAPPS) software includes a machine tool metrology program, CAPPS-NC, and brings the measurement capabilities of CMMs to CNC machines. CAPPS-NC interfaces with multi-axis machining centers and multi-styli probe configurations, and is used for on-machine, in-process metrology applications to provide closed-loop feedback to the manufacturing process. Other CAPPS software includes CAPPS-OFFLINE, a full-featured offline CMM programming package that simulates the total inspection process, and CAPPS-DMIS, the first CAD-based CMM metrology software for the retrofit and OEM markets. CAPPS-DMIS runs the latest probe technology from Renishaw, such as the PH20 and REVO.
For more information about Renishaw's Manufacturing Process Control seminar, or to register for the event, visit www.renishaw.com/usroadshow.
< back