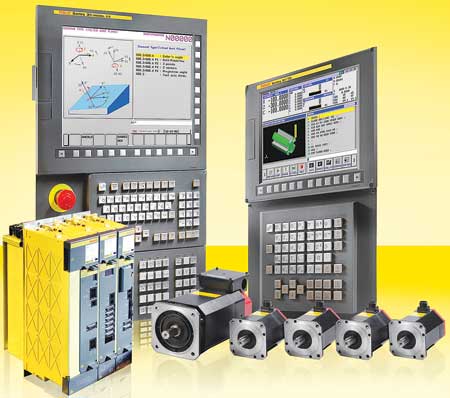
Lead
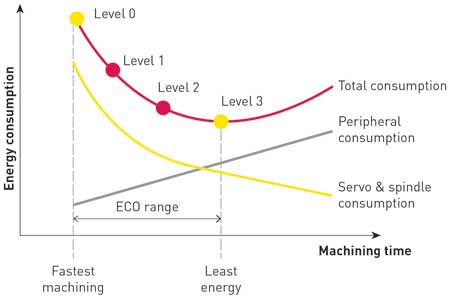
In "Benefits of a CNC Retrofit - Energy Savings" section
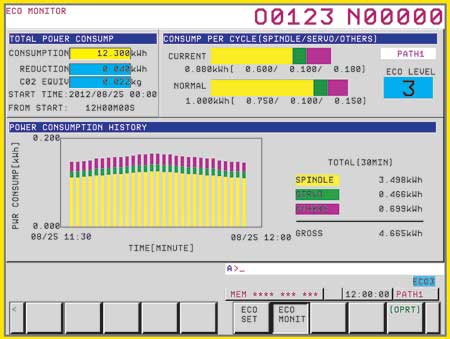
In "Benefits of a CNC Retrofit - Energy Savings" section
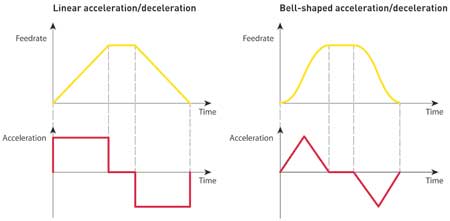
In "Benefits of a CNC Retrofit - Performance" section
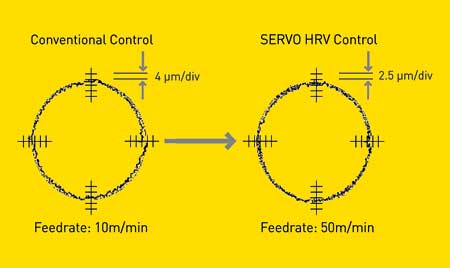
In "Benefits of a CNC Retrofit - Performance" section
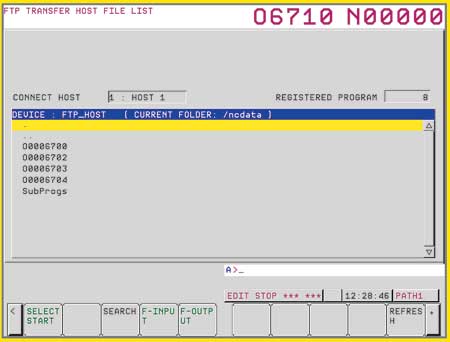
In "Benefits of a CNC Retrofit - Data Accessibility and Customization" section
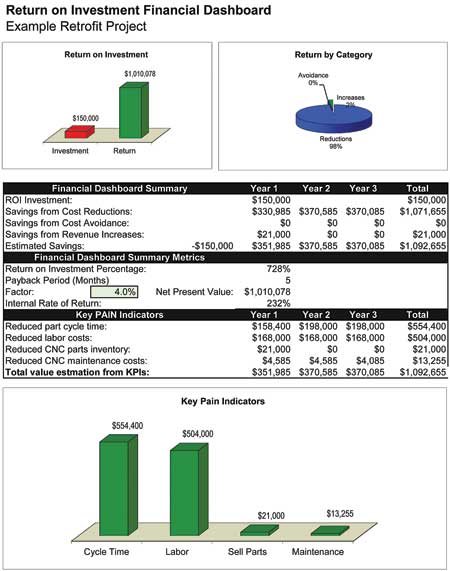
In "Justifying a Retrofit" section
Without question, machine tools are among the most vital - and costly - pieces of equipment on the plant floor. For most companies, they represent significant capital investments and therefore must maintain their viability for many years. Upgrading to the latest control technologies with a CNC retrofit is one way companies are successfully extending the productive life of their machine tools. There are key factors to consider before implementing a CNC retrofit project. Additionally, it is important to quantify the value of this important decision before moving forward.
Retrofitting is the process of replacing the CNC, servo and spindle systems on an otherwise mechanically sound machine tool to extend its useful life. Rebuilding and remanufacturing typically include a CNC retrofit. The anticipated benefits include a lower cost investment than purchasing a new machine and an improvement in uptime and availability. But there are often other unanticipated benefits to retrofitting including lower energy costs, higher performance, a new level of manufacturing data accessibility and better processes.
Manufacturing requirements have dramatically changed in the last two decades, and many new features are now available to support Lean Manufacturing. Retrofitting is a competitive business, so retrofitters will often quote a very basic control system configuration unless the customer specifies the functionality that is important to an operation.
Selecting the best retrofit partner can sometimes be confusing; it is important to make sure that the company has experience with the specific type of machine tool that is to be upgraded. It is also essential to ensure that the scope of work and feature content is clearly defined for an apples to apples comparison of competing proposals, and to establish a long-term, win-win relationship with the selected retrofit company.
Justifying the retrofit investment is similar to any other kind of investment. Considering all the financial costs and benefits allows companies to calculate a return on investment (ROI) for comparison with other investment opportunities. By considering all the financial and non-financial benefits associated with the project, companies will be able to decide if the retrofit makes sense for their business.
What is a CNC Retrofit?
A CNC retrofit typically upgrades the CNC, axes servo motors and drives, spindle motor and drives, and a portion of the associated wiring and related electromechanical components. Unlike rebuilding and remanufacturing, a CNC retrofit does not include any major repairs to the machine mechanics. (A CNC retrofit should not be confused with a CNC conversion, where a manual machine is converted into a CNC machine.)
Assuming the machine tool is in generally good shape mechanically, CNC retrofitting is typically the lowest cost solution to improve the overall performance of an older machine tool. Though some electrical subassembly is often performed at the retrofitter's business location, most of the work can be completed at the machine site - avoiding costly machine rigging and transportation costs and minimizing the time that the machine is out of commission.
Rebuilding typically includes the repair or replacement of some worn mechanical components such as ballscrews, lubrication pumps, safety interlocks, guards, hoses, belts and electrical wiring. The rebuild is typically performed at the rebuilder's facility, so there may be additional transportation and rigging costs.
Remanufacturing goes a step further to repair or replace mechanical components to the original, as-new factory specification or better. It is likely that the machine will be completely disassembled, cleaned, inspected, repaired and painted. All pneumatic, hydraulic and electrical systems will be updated. The machine may also be modified or have mechanical accessories added to re-purpose it for a new application. Practically without exception, remanufacturing will take place at the remanufacturer's site.
Deciding whether to retrofit, rebuild or remanufacture depends on the current condition of the machine and the anticipated benefits from the investment. Reviewing maintenance records and part yield statistics may help one understand the state of the machine's mechanical systems. A ballbar analysis can also be used to diagnose mechanical problems. Retrofit, rebuild and remanufacturing companies will also be able to evaluate the current condition of the machine and recommend the appropriate solution.
Benefits of a CNC Retrofit
There have been advances in machine tool and CNC technologies in the last 20 years. While not all of the technology advances will be relevant to every machine application, most businesses can take advantage of improved performance, reliability and some of the innovative features.
Not all machine tools are good candidates for a retrofit based on simple economics. Small commodity machines benefit from an economy of scale in production and in the price of the procured components. Since a retrofit can require one-time engineering charges, it is often cheaper to purchase a new replacement commodity machine. The large, more expensive machines used in the heavy construction equipment, power-generation, aerospace and defense industries are often ideal candidates for a retrofit. In some cases, these large machines are not widely manufactured today and so cannot be replaced with new assets economically. Since these machines are typically mission critical, they are well maintained mechanically. Mean time between failure (MTBF) and mean time to repair (MTTR) issues tend to be driven by their aging electronics, so a CNC retrofit can deliver significant benefits.
- Lower Cost: A retrofit, rebuild or remanufacture will cost somewhere between 1/3 to 2/3 the cost of purchasing a new machine. It is important to recognize not only the differences in purchase price, but also the additional costs of any new tooling requirements, transportation and rigging, modifications or replacement of special foundations, modification of part programs and processes, and the associated training for the operators and maintenance personnel.
At the end of a product's anticipated life span, replacement parts often become more difficult to obtain and, therefore, the law of supply and demand tends to drive up their price significantly. Parts may no longer be available locally, so the transportation costs and the total downtime associated with the failure are increased. Certain components may become obsolete, and the only choices are either to repair the original part, or to custom engineer a substitution, increasing direct and indirect costs. A machine that is mission critical or is a bottleneck process may have huge customer satisfaction and cost impacts if lost from production for any extended amount of time.
So, when compared with doing nothing and continuing to accept the current availability and performance of an older machine tool, a CNC retrofit can quickly pay for itself.
A retrofit control will significantly reduce CNC maintenance costs. Not only will the retrofit system be more reliable because it is new, but it will be built with substantially more reliable components. The new system will also be provided with a multi-year warranty for parts and perhaps labor. Advanced predictive and preventative maintenance features combined with superior troubleshooting diagnostic systems further reduce costs.
Look for a CNC and drive system that delivers the lowest total cost of over the planned life of the asset.
- Energy Savings: Studies have shown that approximately 20% of machine running costs can be attributed to electrical energy consumption, primarily for hydraulic and pneumatic pumps, and the servo and spindle drive systems.
When decelerating the axes and spindles during normal operation, older drive systems redirect energy into regeneration resistors, simply burning away expensive electricity.
Current digital drives incorporate advanced electronics that reclaim electrical energy back into the line when decelerating the servo and spindle motors. When combined with the more efficient machining processes provided by the CNC, machine electricity costs can be reduced by as much as 30% to 50%. This easily justifies the investment in the new servo and spindle drive technology during a retrofit.
With today's focus on energy conversation, an energy saving level selecting function allows the user to optimize the balance between the fastest (normal) machining speed and the lowest energy consumption. When the ECO level is set above level 0, the torque of the spindle drive is limited during acceleration to further reduce energy usage.
The CNC can display data on real-time energy usage and the data is accessible via Ethernet to record the information into a database for further analysis.
- Performance: When considering a CNC retrofit, it is important to realize that a significant portion of the benefits will actually be delivered by upgrading the servo and spindle system to a high-speed digital interface. It does not matter how fast the CNC can process blocks of part program data if the servo and spindle systems cannot keep up.
The CNC, servo and spindle systems integrated in an older machine tool typically communicate using an analog interface. The CNC commands the desired velocity of the motor with a ±10-volt signal, while low-resolution, analog or digital feedback devices tell the CNC where the axes are currently positioned. Simple I/O points are used to enable and disable the drive systems and to report on any drive or motor failures.
The coarse resolution and the noise susceptibility of the analog drive interface limit the achievable speed and accuracy of the system. Tuning traditional analog drive systems is more of an art than a science, requiring experienced engineers using specialized tools for even basic system stability.
The modern CNC and the digital servo and spindle drives are so highly integrated it is best to consider them as a single system. The subsystems communicate over high-speed fiber optic communication paths to provide the required noise-immune bandwidth for high-resolution, intelligent feedback devices and inter-process communications. Today's high-performance systems provide nanometer resolution from the initial block processing through to the 16-million count serial encoders - delivering smooth surface finish on contoured surfaces. A large proportion of the advanced capabilities of the modern CNC system are at least partially implemented in the digital servo and spindle systems processors.
The tight integration of today's CNC and digital drive systems provide advanced servo tuning applications built right into the control that makes standard servo tuning practically automatic. For advanced tuning, Ethernet communications provide engineers with frequency analysis, Bode plots and Fourier analysis tools to analyze and display the servo system response in real time. These tools are also used to tune spindle systems since they are also used as servos for rigid tapping and live tool applications.
Predictive and preventative maintenance and diagnostic systems have also advanced. Everything from motor temperature to position deviation can be displayed on the CNC. The speed of servo and spindle motor and drive fans are monitored to detect dirt ingress or potential failures. The insulation resistances of servo motors are measured to detect cutting fluid infiltration. Signal level deterioration in fiber optic communications can also be detected. Precise warning messages are displayed on the CNC for each specific potential problem prior to failure, preventing unexpected machine downtime.
Older machine tool servo systems featured limited exponential acc/dec or perhaps a simple linear acc/dec. Machine structures often reacted violently to exponential acc/dec because of inherent mechanical resonances. Linear acc/dec is more gentle on mechanical structures, but there is still a time when the axis must go from dead stop to accelerating at the start of a move, and then from decelerating to a dead stop at the end of a move.
Bell-shaped acc/dec minimizes many of the fundamental problems of machine resonances by using an S-shaped curve. During the first microseconds of a move, the acceleration of an axis is ramped very gently until the linear section is reached. The same simple, gentle ramping of acc/dec rate occurs when the axis reaches top speed, going from top speed to decelerating or decelerating to a stop. This typically allows the linear section of the acc/dec curve to be set more aggressively than is possible with standard linear acc/dec, reducing the overall cycle time.
CNC high-speed machining technology can be applied to any machine tool to speed up processing and reduce cycle time by as much as 50%. Block look-ahead, acc/dec before and after interpolation, nano-interpolation, nano-smoothing and automatic feedrate control by corner, circular radius, acceleration, cutting load torque and jerk are just some of the technologies that can be applied to make the machine more stable and accurate and therefore have the ability to go faster.
The only absolute physical limit to the productivity of a machine tool is typically the spindle horsepower available to remove material. Practically, machines are not run at maximum horsepower during finishing cuts because surface finish specifications are more important than productivity. However, even during roughing cuts a machine rarely takes a full load because of process variation concerns.
The horsepower required to cut a particular material is proportional to its hardness, the depth and width of cut and the sharpness of the cutting tool. The hardness of some materials varies from batch to batch, from piece to piece and even within a cut. The depth-of-cut of the initial passes are often lighter than the subsequent passes because the surface level is unpredictable from part to part. When contouring and facing, the width-of-cut may vary continuously. As tools wear, more horsepower is required to cut the same material. All of this potential process variation means that programmers routinely specify very conservative cutting feedrates and the machine capabilities are under-utilized.
Adaptive control specifies a target power level in the part program that is suitable for the machine and tooling. Adaptive control then automatically adjusts the feedrate to maintain a constant horsepower. As material hardness, depth-of-cut, width-of-cut and tool condition varies, adaptive control speeds up or slows down the actual feedrate as required, decreasing the overall cycle time by as much as 40%.
High Response Vector (HRV) is an advanced form of field oriented control that uses high-speed digital signal processors (DSPs) and nano-interpolation to improve surface finish, cycle times and accuracy. HRV3 closes the current loop in 62.5 µs, the velocity loop at 125 µs and the position loop at 1000 µs. Higher-speed current (torque) control can deliver higher-gain velocity control. Auto-following filters dynamically suppress mechanical resonances even when the frequency changes. The HRV features combine to allow cutting feedrates to increase while maintaining the same dynamic performance.
Since the axes drive systems have to be tuned on the new retrofit system, it is an ideal time to add some of the performance machining options and get the expert tuning needed to maximize the capabilities of the machine.
- Improved MTBF: Driven by the advances in semiconductors for consumer electronics, aerospace and military applications, today's CNCs are much more reliable than those that were produced just a few decades ago. The differences are compounded by the fact that the aged electronics integrated into older machines are now into the high-failure rate section at the end of their life cycle curve. An MTBF of 17-32 years is now being achieved.
New CNC features also provide tools to error-proof operator inputs and other process related operations. Error-proofing may prevent the downtime that results from a crash after the misapplication of tooling, materials, part programs or fixtures.
One of the most complicated and costly CNC service problems occurs when critical files are lost and there is no current backup. Some CNC files are provided by the CNC manufacturer, but the machine tool builder or retrofitter provides additional files and settings to customize the CNC to a particular machine tool. Other files are created by the end-user to implement process standards or families of parts. Files may be lost or corrupted due to an electrical component failure, a lightning strike, a flood or some other unexpected event. If these files are not backed up it could take a week or more to get the machine back into production. Modern CNCs incorporate automatic backup of files to flash memory, for one level of data security.
Machining processes often rely on the fact that a prior process was completed to specification. The classic example is when a tapping tool relies on the fact that a hole has been previously drilled. If the operator forgets to put the correct drill in the correct pocket in the tool changer, sets the wrong offset or offset value or the drill simply breaks during machining, a severe crash can occur. The Unexpected Disturbance Control feature available in today's CNCs monitors the torque generated by the axis drives and trips if it goes above a programmable threshold, protecting the machine from serious damage.
A CNC retrofit will significantly improve the MTBF of a machine tool. This is very important because many retrofit candidates are mission-critical or bottleneck machines.
- Improved MTTR: Studies have shown that, though improving MTBF is very important, there is even more of an opportunity to improve uptime by focusing on the time it takes to recover from a failure. Today's operators typically run multiple machines and assets often sit just waiting for attention.
Advances in CNC communication and mobile device technologies and their associated software applications now make it possible to alert operators and maintenance personnel to a wide range of process variances and downtime failures. Notification of symptoms can be sent before a real problem even occurs, allowing predictive and preventative actions to be taken. Features such as tool management, tool life monitoring and tool breakage detection can be combined to apply preventative and automatic recovery strategies.
If the downtime cannot be predicted or prevented, advanced diagnostic tools can be used, locally or remotely, over Ethernet to reduce MTTR. Maintenance and industrial engineers can view the CNC screens remotely to solve problems over the phone, or at least arrive at the site with the tools and parts to speed recovery.
When an accident such as a machine collision, tool breakage or component failure occurs, the machine state monitoring function saves the axis position and speed, spindle speed, program name, modal G-codes, operational history and other data to memory to allow the reconstruction of events that preceded the event. Diagnostic displays quickly communicate the CNC's general health, and the ladder and IO displays help troubleshoot the CNC-to-machine interface.
Combining the value of alarm monitoring, insightful diagnostic screens, remote access and basic troubleshooting training for operators, maintenance and process engineers, the MTTR of a machine can be dramatically reduced by a retrofit, managing the risk of excess downtime when operators manage multiple machines.
- Data Accessibility and Customization: During the 1990s the industry was focused largely on the promise of low-cost, PC-based CNC technology to provide application flexibility and data accessibility. Now, many of those systems are being replaced by traditional CNC technology because of poor reliability and the unavailability of legacy personal computer parts. The cost to use industrialized rather than commercial-grade PCs often exceed that of the traditional CNC, and the PC-based systems still have limited parts availability as their components become obsolete. IT departments also fight issues related to viruses and the misuse of company assets when PC-based CNCs are connected on company networks. Installed systems include outdated operating systems that do not support contemporary virus and security protection, and the hardware cannot be upgraded to support the newer operating systems.
Manufacturers have since determined that what they really need is robust, high-speed communications and the ability to create custom screens for specialized processes.
For the past decade, innovative CNCs have supported an optional or embedded Ethernet port that provides standard TCP/IP data transfers, and a comprehensive public API for data collection and control applications. Since the CNC does not use a public domain operating system, such as Microsoft Windows, it is less susceptible to attack by viruses and hackers.
A data server combines the features of Ethernet communications and very large part program storage location. High-speed flash memory cards can handle up to 4 GB of part programs. Part programs can be edited and executed just like internal part program memory. Extremely large part programs can be paged or streamed from a host computer using the 4 GB storage as a high-speed buffer, preventing data starvation in the drip feed mode. A data server also includes an FTP (file transfer protocol) server, so it can be accessed in Windows Explorer as just another virtual hard disk folder, providing high-speed, drag-and-drop part program downloads.
There are several choices available when implementing custom applications in a traditional CNC. A published API can be used to integrate external PC-based programs. C-Language Executor provides a, industry standard tool for creating custom displays and implementing control algorithms. Advanced proprietary HMI tools can provide an easy-to-use application development environment providing draw-and-click features similar to many common SCADA tools, and it can be integrated with C-Language Executor applications.
If the Windows development environment is preferred, Microsoft CE provides the Windows interface in an embedded operating system that eliminates virus vulnerability and the unreliable hard disk. Embedded Windows supports standard Windows applications but allows the machine tool retrofitter to select only the operating system components required to support an application. This reduces system vulnerability and gives the retrofitter the option to choose flash storage over a hard disk, thereby increasing reliability.
- Improved Support: Technical and training support may be limited on an older CNC. Even if the original manufacturer is still in business, they may not have resources available that are experienced with a particular control vintage.
However, industry leading CNC manufacturers provide 24/7 technical support on all of their CNCs, including legacy CNCs, and free technical support during normal business hours. Additionally, they provide support to help customers decide what features are most beneficial to their operations and to assist the chosen retrofit partner to implement a wide range of CNC solutions. Finally, they may also have productivity specialists that can review operations and help identify additional features that may enhance operational effectiveness, both for the retrofit machine and the other assets in customer factories.
- Standardization: Many machining operations use a wide range of machine types for a variety of applications such as turning, machining, grinding, gear cutting, punching, laser cutting and other specialized applications. There are a few machine tool builders that can offer a comprehensive line of machine tools that cover a wide range of machining applications, but typically there is a best-in-class manufacturer for many applications.
"Control standardization is an important factor to simplify operation, part programming and maintenance and allow more agility in applying labor resources," said a FANUC FA America spokesperson. "Some industries insist on their own HMI standards for machine tools. Only the leading CNCs are available on practically every type of machine tool, which can provide commonality for critical machine function. Manufacturers that might offer a less reliable, less innovative or proprietary CNC as standard will also offer the world's leading control to meet a specific customer's requirements upon request. Therefore, choosing a CNC wisely for a retrofit is an important element in standardizing manufacturing processes."
- Access to New Features: There have been many CNC technology advances in the last 20 years to support the evolution of machining processes. The CNC is now a relative super-computer when compared with the technology that is currently integrated into older machine tools.
With multiple, faster and distributed microprocessors, and with a magnitude increase in system memory, the CNC can now incorporate advanced software algorithms that can model the machine mechanics and dynamically compensate for inherent, undesirable mechanical characteristics.
Numerous features have been added to the CNC to reduce setup, minimize downtime, increase processing speeds, minimize minor stoppages and improve setup and production part yields. Many of these new features address issues that are critical success factors for lean manufacturing environments, and they typically cost less if implemented with a new CNC purchase, including during a retrofit.
Large 5-axis machines are ideal candidates for retrofit and 5-axis CNC technology has made significant advances in recent years. Until recently, 5-axis machining was mostly utilized for parts that could be manufactured in no other way. Limited CNC technology made the process inefficient so that any changes in machine, workpiece, workpiece fixtures or tooling required a round trip back to the CAM system. This sometimes required the whole process to be re-certified in compliant aerospace and medical industries. With features such as tool center point control, 3D workpiece error correction, 3D tool length and radius compensation, 5-axis workflow can now be as efficient as 3-axis. Any changes to machine, workpiece, workpiece fixtures or tooling can be adjusted right on the CNC without a round trip to the CAM system or re-certification.
How to Select a Retrofit Partner
North America has more than 250 retrofitters, ranging from one-person operations to companies with 50 employees or more. Many machine tool builders also specialize in retrofitting their own machines. There is obviously a cost impact of selecting a partner that is not local, but there could also be serious warranty issues if the company is no longer around when a customer needs assistance.
Machine tool builders and retrofitters often specialize in certain kinds of machines. So when choosing a partner, it is important to make sure that they have competencies related to a particular type and model of machine. Ask for references and confirm the quality of the work performed and determine how long the machine was out of commission during the retrofit.
It pays to get multiple quotes for any significant investment and compare them for discrepancies to uncover any lack of core competencies. Make sure to compare apples to apples on everything, including the CNC features, the work to be performed and the length and terms of the warranty. Document everything related to the scope of work to ensure a common understanding for a long term, win-win relationship.
Check the availability and quality of the documentation that will be provided with the retrofit, including wiring diagrams, and the machine, CNC, servo and spindle drive manuals. The documentation package needs to cover operation, programming and maintenance.
Look for pre-engineered kits from machine tool builders, retrofitters and control manufacturers. It is not uncommon for a company to provide kits for a high-volume machine tool with a good brand name that is common in the industry. These kits typically include everything necessary to complete the retrofit of the machine onsite, amortizing the engineering costs over multiple installations, so they should cost less than a custom retrofit.
The CNC manufacturer should be able to direct customers to a list of retrofitters with experience in their specific machine tool.
Justifying a Retrofit
Justifying a retrofit is the same as justifying any other high-value investment. A return on investment will occur when a business spends money to increase revenue and decrease or avoid costs. Performing an ROI analysis will document the value a company will lose if they decide not to invest in or defer an investment to retrofit, rebuild or remanufacture a machine tool.
First, list all the potential revenue improvements from the extra capacity and throughput from the machine. Consider all the categories of setup reduction, downtime improvement, speed improvement, minor stoppage reduction and increased setup and production part yields. Factor any savings from automation, including reduced labor, and the ability to run unmanned through breaks and additional shifts. Consider that the typical machine tool is only utilized at 30% to 40% of its capacity. Applying lean CNC technologies can significantly improve this percentage.
Secondly, list all the costs for the retrofit from the quotations received. Finally, perform the standard ROI and payback calculations. Financial analysis is at the heart of most important investment decisions, but it is also important to list any additional non-financial benefits as they can be used as tie-breakers between investments of similar value. Particularly list any benefits that support current initiatives, such as Lean Manufacturing, Total Productive Maintenance or other continuous improvement programs.
Summary
Retrofitting is typically a low-cost alternative to purchasing a new machine tool. It will improve MTBF and MTTR. Additional benefits can be realized in energy savings, performance improvement and improved access to manufacturing data.
There are many features that can be included in a new CNC to support Lean Manufacturing, reduce setup time, downtime and minor stoppages, and increase speed, setup part yields and production part yields. The downtime that is inherent when the CNC is being re-commissioned is an ideal time for training, changing processes and taking advantage of professional services that can make the project a complete success.
By selecting the right retrofit partner, a reliable and innovative CNC and by producing a credible investment justification, customers can be assured that a retrofit will deliver the promised return on investment.
Authored by: Mark Brownhill, Strategic Marketing Manager, FANUC FA America
For more information contact:
FANUC FA America
1800 Lakewood Boulevard
Hoffman Estates, IL 60192
888-FANUC-US (888-326-8287)
www.fanucfa.com