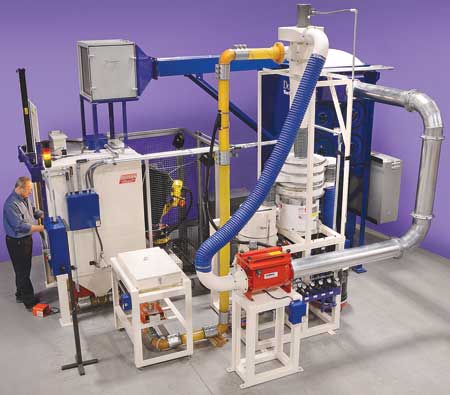
The robotic grit-blast machine is configured for surface preparation work in thermal spray coating work cells. The 7-axis Model RB-RSSA-8 uses a Fanuc M-10iA robot as a blast nozzle manipulator.
Guyson Corporation has designed and built a 7-axis robotic grit-blast machine that is configured for precision roughening of component surfaces in a production thermal spray coating cell. The Model RB-RSSA-8 has a 54" x 46" blast process chamber that is 42" in height.
A single pressure-blast nozzle is fed by a 3.5 cubic foot capacity, ASME-certified pressure vessel. Blast nozzle motion is provided by a Fanuc M-10iA robot and is coordinated with component rotation on a servomotor-driven auxiliary axis controlled by the Fanuc R-30iA robot controller. The hollow wrist of the M-10iA allows routing of the pressure-blast hose through the articulated robotic arm. A custom-tailored suit isolates the robot from the abrasive environment of the blasting enclosure and seals the back wall of the blast cabinet while accommodating the full range of motion of the nozzle manipulator.
The spindle of the RB-RSSA-8, fitted with a jawed chuck or a T-slotted turntable, can be controlled to turn clockwise and counterclockwise to orient the component throughout the blast cycle; it is capable of rotation at speeds adjustable from 0 to 300 RPM.
"During the programmed blast cycle, the robotic grit blasting system consistently maintains the correct nozzle angle, stand-off distance and surface speed to produce uniform surface roughness on target areas of the component, without under- or over-blasting and with no wasted motion," said a company spokesperson.
The robotic blast machine's media reclaimer stack-up includes a cyclone separator that removes dust and fine particles, as well as a vibratory screen classifier that feeds only grit of the specified size to the pressure pot. The blast pressure is electronically monitored and automatically regulated by closed-loop control. Blasting grit flow to the blast nozzle is also monitored. Electronic level sensors detect when the amount of blast media is beginning to get low, and new grit is automatically added before a shortage could compromise the surface preparation process.
For coating cells where the component material may raise concerns about flammable metallic dust from the grit-blasting operation, the blast system manufacturer offers special dust handling options, including an explosion-vented dust collector, metal ducting between the dust separator and the collector and an automatic isolation valve between the media reclaimer and the dust collector. Wet dust collectors and automatic fire suppression systems are also optionally available.
Prospective users of automated or robotic blasting equipment are invited to submit sample components for free laboratory testing and application engineering evaluation.
For more information contact:
John C. Carson
Guyson Corp.
13 Grande Blvd.
Saratoga Springs, NY 12866-9090
800-633-6677 / 518-587-7894
info@guyson.com
www.guyson.com