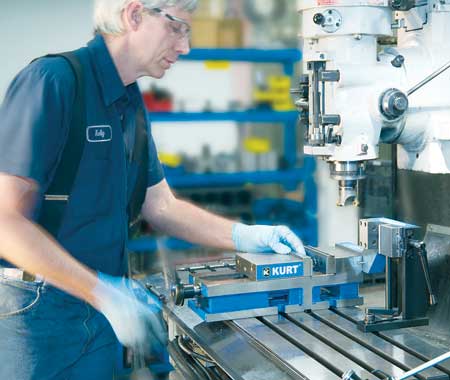
Operator is shown inserting a part into a standard 6" Kurt vise mounted on a milling machine. Mounted adjacent to the 6" vise is the Kurt SideWinder vise ready to receive the part for second.
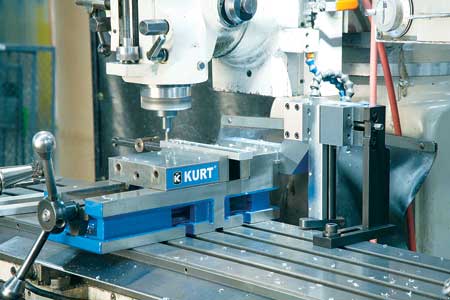
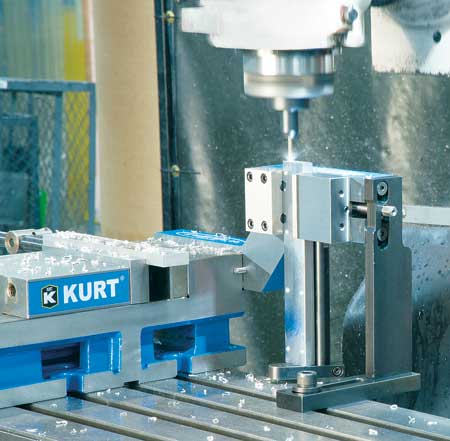
Horizontal drilling (left) in a standard 6" Kurt vise. Second operation vertical drilling (right) on the attached Kurt SideWinder vise.
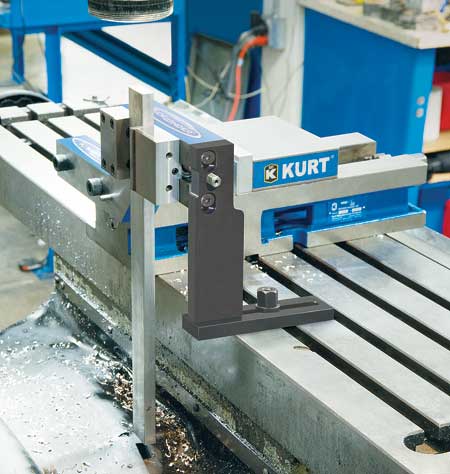
For handling long piece parts, the SideWinder vise is mounted facing away from the machine table as pictured. Note that spindle travel from part-to-part is minimal when using the Kurt SideWinder vise in both setup positions. The SideWinder has a jaw width of 2.500" and jaw height of 1.063". It has a maximum clamping force of 2,450 lbs.
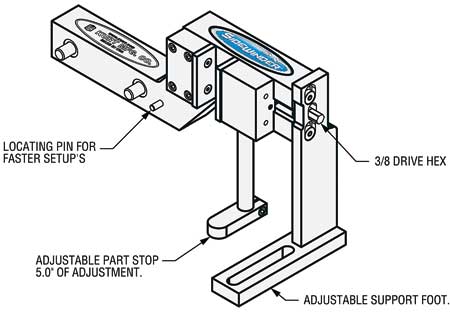
The Kurt SideWinder aligns parallel to the host 6" vise and aligns with the XYZ axes of the machine tool.
"Getting the most productivity out of every machine setup is an ongoing machinist's goal," said a Kurt spokesperson. "Second operations using a vise for the workholding on a VMC or a knee-type mill usually requires mounting a second vise or custom fixture to do the secondary machining operation on the ends of longer parts.
"Consider the time required to make a second operation setup, which is about a half hour (table cleanup, find and attach clamps, risers, etc.), plus all the effort needed to mount a second 70 lb vise or similar custom fixture. That process is an ideal target for improvement but the change could not be accomplished easily until now with a SideWinder vise."
The SideWinder vise from Kurt mounts to any existing Kurt 6" industry standard single station or similar model vise and provides vertical workholding for second operation machining. According to Kurt, the Sidewinder takes less effort and less set up time compared to using a second vise or custom fixture.
It is designed so that when mounted to the host 6" vise, the SideWinder vise is parallel and aligns correctly with the XYZ axes of the machine tool for quick and accurate positioning of the part for secondary operations.
The SideWinder vise is designed with integral mounting that is part of the SideWinder vise body. Two through holes in the body align with the boltholes on the backside of every industry standard 6" single station vise so that when screwed together with two cap screws, it aligns in all three axes for consistent 3D locating, according to Kurt. The SideWinder mounting bracket has a stabilization leg at the movable jaw end. It mounts to the machine table to help reduce vibration that could occur during machining. An integral workstop in the SideWinder can be adjusted to position the height of the part.
Once affixed to the vise and the machine table, insert and clamp the part in the main 6" vise for first operation machining. Remove it and re-insert and clamp the part in the SideWinder vise for second operation machining.
"What is really unique is the SideWinder does not interfere, in most cases, with the working envelope of the main vise," said the spokesperson. "Another benefit is that because the SideWinder is mounted 8 inches above the machine worktable, it is more conducive to longer reach machining operations.
"The SideWinder makes end-work machining on a longer piece part simple and less costly than a custom fixture. In the past, second operations requiring a custom fixture would work well enough for one part application but not for a variety of parts. Using vises with precision-machined sides also worked well, however, this requires more time to mount and they are heavy to manipulate."
SideWinder mounting can be varied two ways on knee mills based on the length of the part to be machined. The typical mounting position is facing toward the operator and over the top of the machine table for shorter parts. For longer parts, the SideWinder can be mounted facing away from the operator toward the left side of the vise. This position locates the piece part out and beyond the machine table.
The SideWinder vise is designed for a variety of machining operations including precision boring, tapping, drilling and finishing. Tolerances are relative to the cutter choice and the feeds and speeds of the tooling used.
In an example application using a 3/8" end mill on cold-rolled steel, Kurt reported that the SideWinder provided accurate and secure workholding on a Bridgeport CNC milling machine with a new spindle. Operations included circular interpolating milling of 0.300" depth of cut with 0.180" radial engagement at a feed rate of 30 IPM.
"Based on an average shop rate of $70 an hour, the SideWinder vise is a very good investment even when used only twice a month," said the spokesperson. "By using it twice a month, users can conservatively save about a half hour of setup time for each use. That amounts to $840 savings based on the $70 shop rate over the course of a year, easily recovering the investment for the vise. For shops where secondary operations are more frequent, the SideWinder pays for itself even faster. Another big bonus is the reduced physical wear-and-tear on the operator of not having to move a second vise or custom fixture on and off the machine. The SideWinder weights only 19 lbs."
The SideWinder vise incorporates the Kurt AngLock concept in the movable jaw, which is intended for rigid part clamping while decreasing jaw deflection. According to Kurt, the AngLock design distributes clamping force evenly across the full jaw surface. The SideWinder is precision machined of porosity-free 80,000 PSI ductile iron and has been cycle tested a minimum of 50,000 cycles at the maximum clamping force.
The SideWinder vise has a recommended maximum clamping force of 2,500 lbs using input torque of 12 ft-lbs. It has a maximum jaw opening of 2.500", jaw width 2.500", jaw height 1.063" and workstop adjustment range from 0 to 5.000". Screw hex size is 0.375", hex length: 0.453. Overall bracket width is 14".
For more information contact:
Kurt Manufacturing Company
Industrial Products Division
9445 East River Road NW
Minneapolis, MN 55432
877-226-7823
workholding@kurt.com
www.kurtworkholding.com