
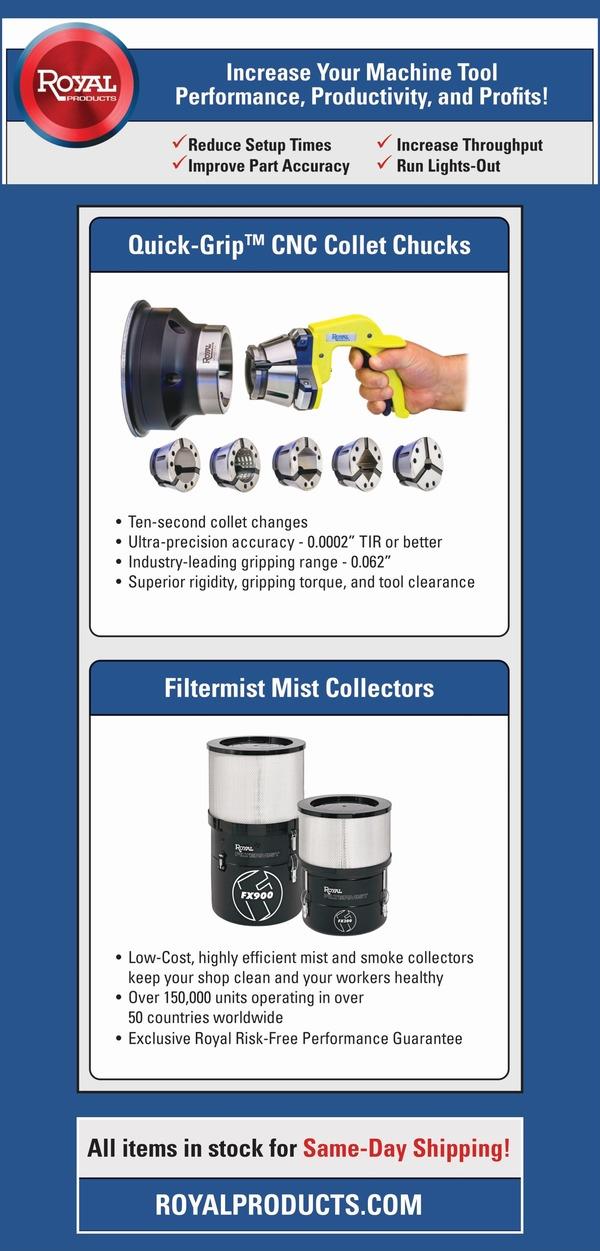
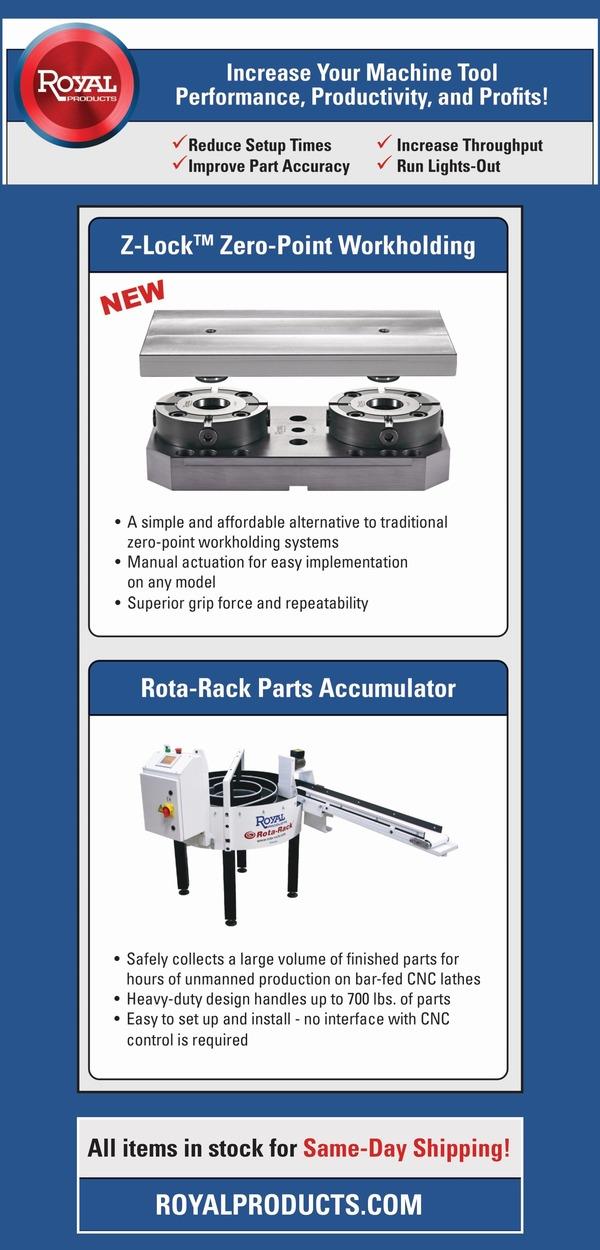

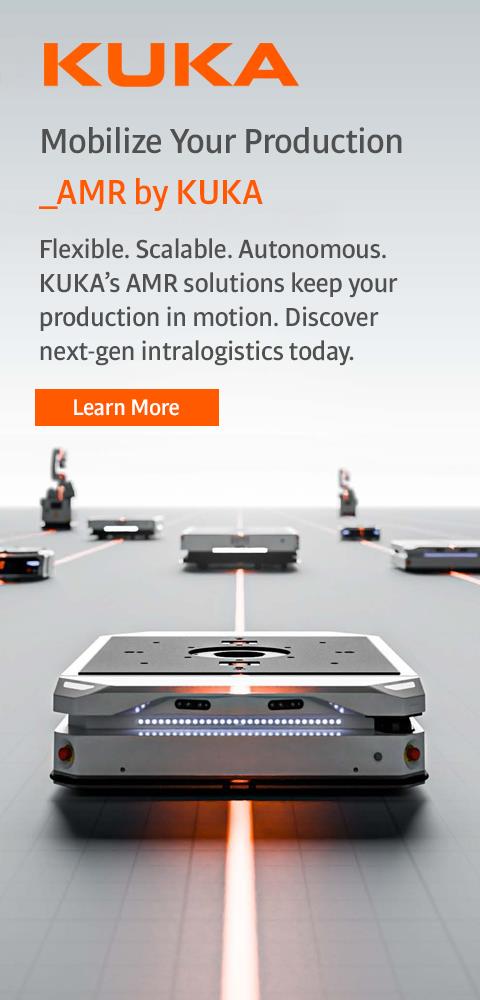
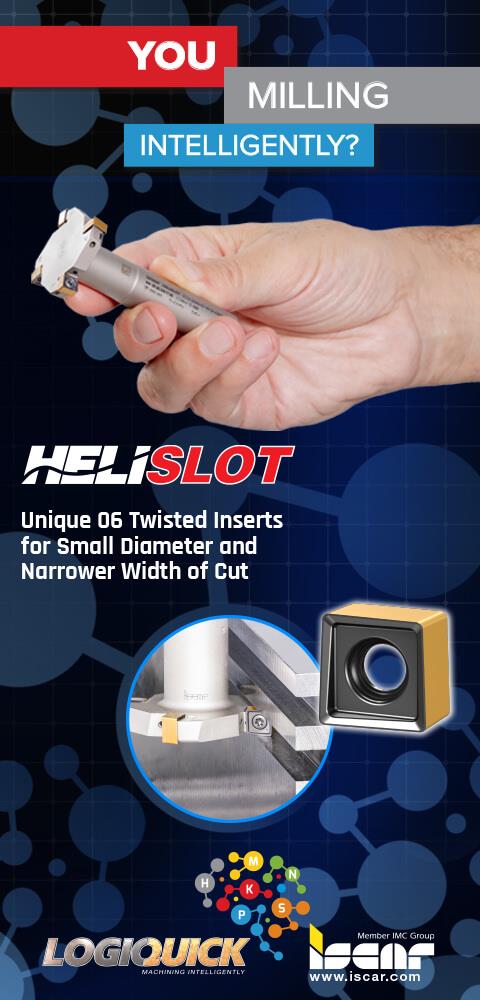
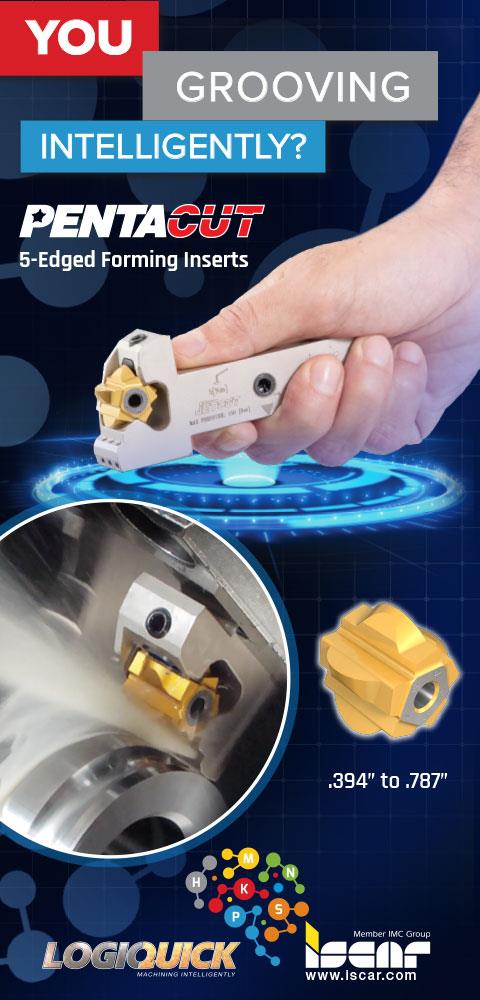
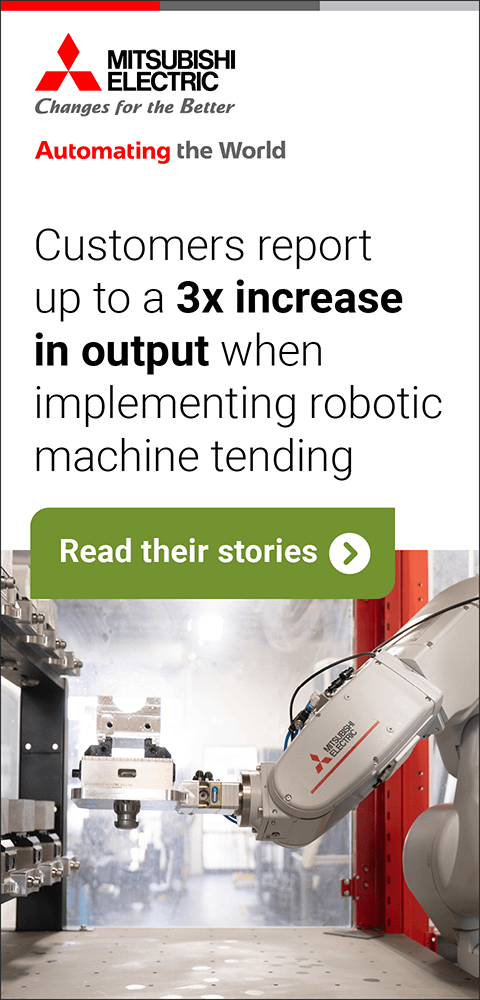
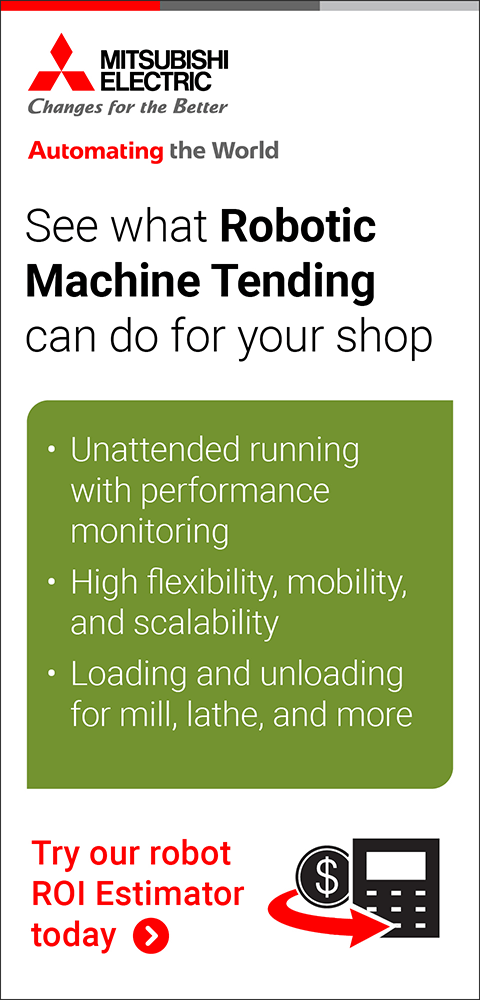
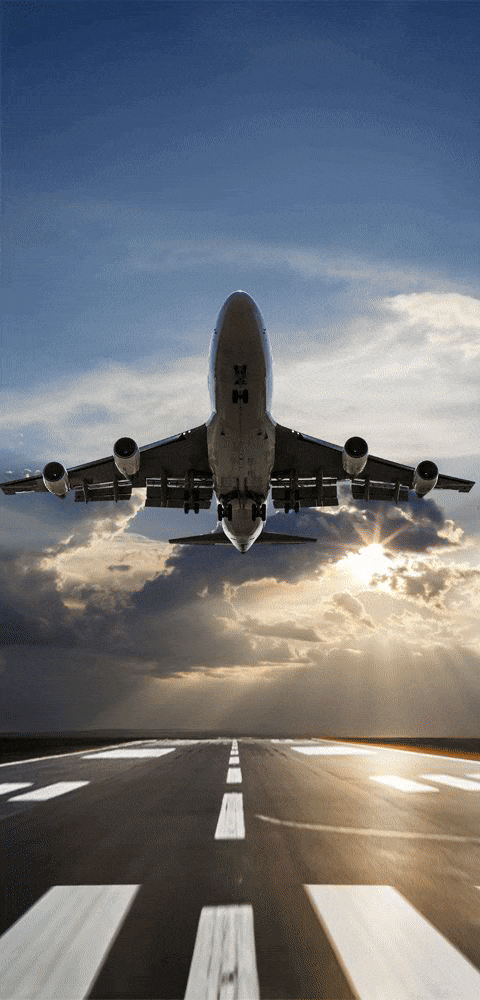
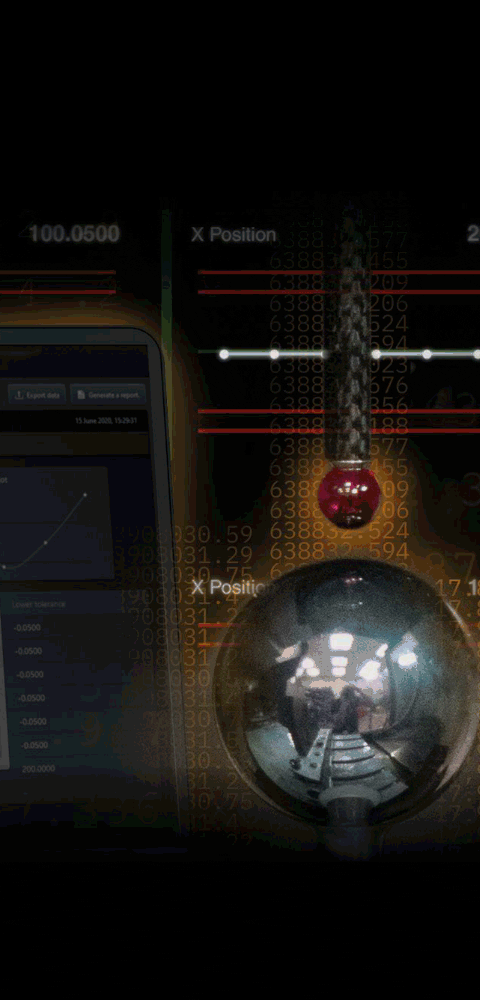
New Inspection Software to be Demonstrated
October 27, 2015The latest version of Delcam’s PowerINSPECT inspection software will be demonstrated in booth 1032 at the Quality Show being held in Rosemont, IL, October 27 - 29. The 2015 R2 release of this hardware-independent metrology software is designed to make it easier to complete fast and accurate inspection of complex assemblies. It includes more options for automation of inspection sequences, including automated probe changes, automatic feature extraction for point cloud batch inspection, and greater control over collision checking.
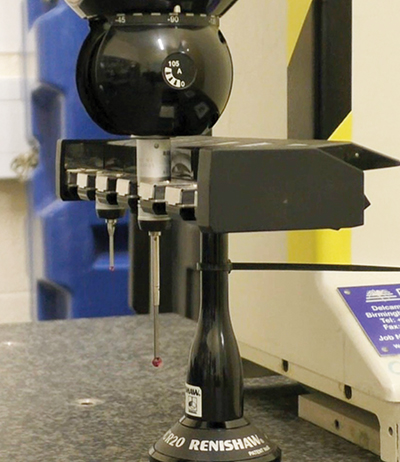
PowerINSPECT 2015 R2 can incorporate probe changes from racks into fully automated measurement sequences
The main improvement for users of CNC CMMs is the addition of support for MCR20 and FCR25 probe change racks. PowerINSPECT can now incorporate probe changes into fully automated measurement sequences. Enhancements to the probe database allow the user to define probe tools in terms of sub-assemblies, which can be docked in the rack ports. A typical example of a sub-assembly is the combination of a probe module and a stylus.
Once created, the sub-assemblies are allocated to specific ports in the probe change rack, and the user defines the physical location of the rack on the CMM by measurement. PowerINSPECT carries out probe changes as required by the measurement sequence and keeps track of the sub-assemblies as they move between the probe head and probe rack.
A new zoom-to-fit option is available that shows, in the CAD view, groups or individual items that have been selected in the sequence tree. This option is designed to save time, especially when locating specific features in large, complex CAD models or long measurement sequences.
It is also easier to navigate between the graphical display of the CAD model and the CAD file manager history tree. Selecting a CAD level or individual surface in the graphical CAD display highlights the corresponding item in the CAD file manager history tree. Similarly, selecting an item in the history tree highlights the corresponding surfaces in the graphical CAD display.
PowerINSPECT 2015 R2 includes a new way of evaluating features from point-cloud data that makes batch inspection easier. Geometric point-cloud features can now be evaluated from suitable scan data that exists anywhere in the PowerINSPECT document. The features are created in the usual way, either from the geometric toolbar or by using the wireframe checker. The entire sequence can be created in advance and then PowerINSPECT will evaluate the results automatically as soon as the scan data is available. Operators measuring subsequent, similar parts just have to perform the scan and the sequence of features is evaluated automatically. Once the scan is complete, all specified features are calculated and the report is updated automatically.
With PowerINSPECT 2015 R2, users have better control over RPS alignments due to a new option to define which features are used for any best-fit calculations, rather than calculating the best fit across all of the features selected for the alignment. It is also now possible to apply an offset to an RPS alignment, if required.
Improvements to the graphical display have made programming of CNC edge points easier and more intuitive. When creating edge points, PowerINSPECT displays a live preview of the edge point based on the current cursor position. When editing edge points, the point pairs and probe paths update simultaneously as the point is dragged along the edge.
Finally, a new option has been added to measure waviness or small fluctuations in surface smoothness that can result from cutting tool wear or worn machine components causing vibrations during machining. Waviness defines the allowable variation within a localized region. This allows simultaneous control of very tight tolerances inside small, localized regions and looser tolerances over larger areas. For surface inspection and point cloud inspection, PowerINSPECT can now produce a waviness evaluation based on the differences between a point and its neighbors. Each point passes the waviness test if its variation relative to neighbors in the specified zone is within the tolerance limit. An overall value for the part is expressed as a ratio of the number of points passing the test to the total number of points measured.
For more information contact:
Delcam
877-335-2261
marketing@delcam.com
www.delcam.com
Quality Show 2015 Booth 1032
< back