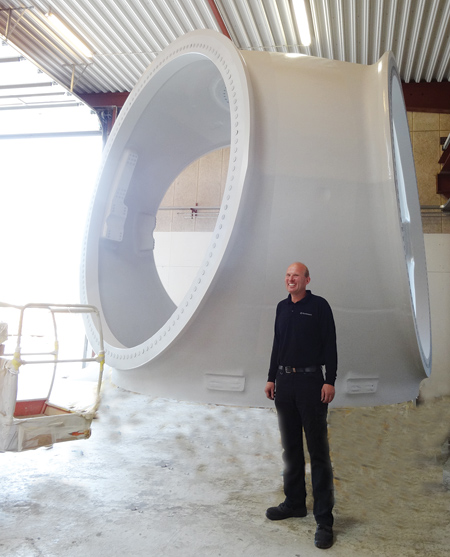
Michael Jacobsen, Owner, Nordmark Maskinfabrik A/S, with the large wind turbine hub after machining and painting.
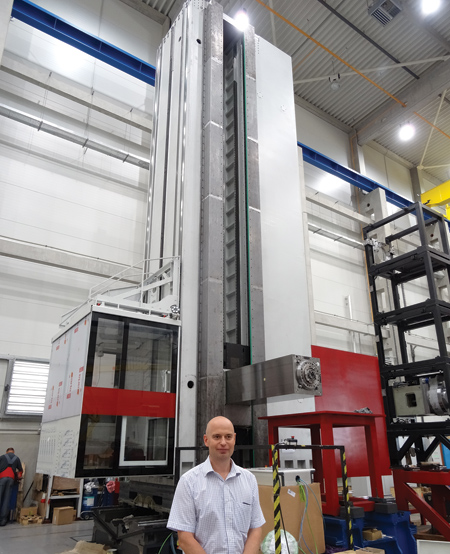
Jan Ferenc, Sales Director, Fermat Group, a.s., with one of the Fermat WRF 160 Heavy z/1600 HBMs being built in Brno, Czech Republic, for Nordmark. The headstock can travel 8 meters (26.2 ft.) on the column.
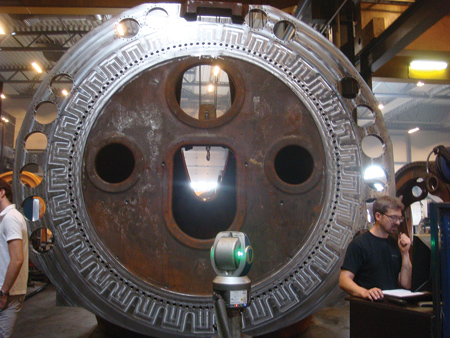
Nordmark uses the Laser Tracker for quality control of all machined components.
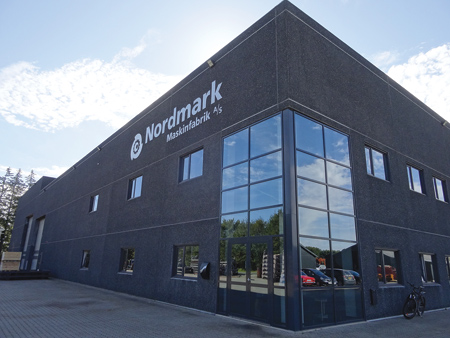
Nordmark Maskinfabrik A/S has three locations in Denmark where it machines large components, 85% of which are for the energy industry.
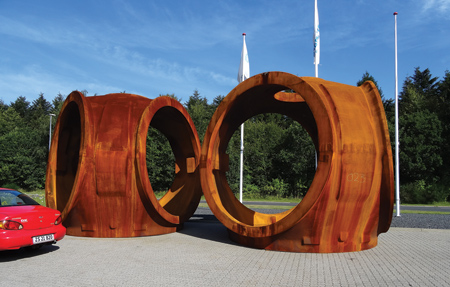
Wind turbine hub castings delivered to Nordmark for machining.
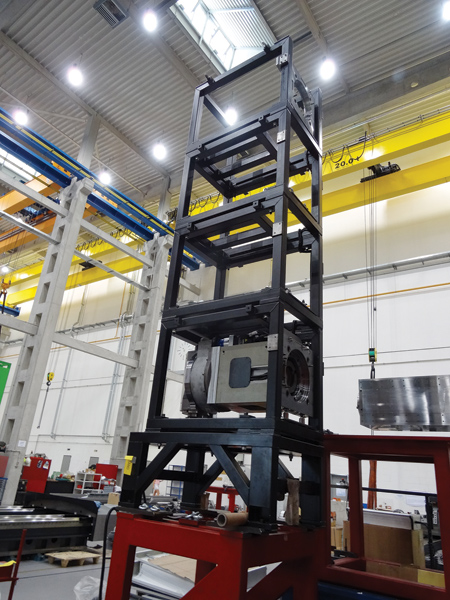
The Fermat WRF 160 Heavy z/1600 HBM pickup station for automatic heads of various types. The heads are picked up by the machine and changed as needed.
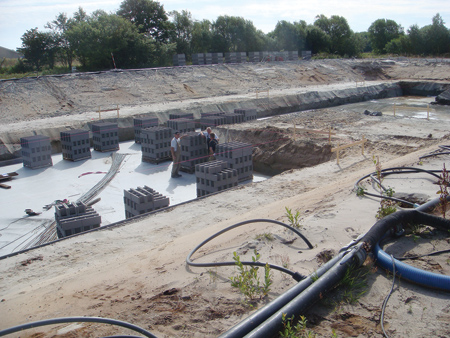
Nordmark Maskinfabrik A/S is laying the 3-meter (9.84 ft.) deep cement foundation in preparation for two Fermat WRF 160 Heavy z/1600 HBMs.
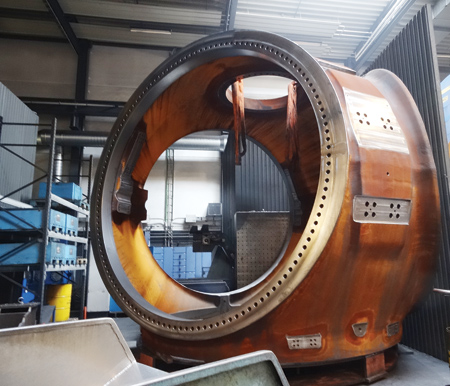
The 7-Megawatt wind turbine hub weighing 47 metric tons (51.81 U.S. tons) has been machined on a Fermat HBM.
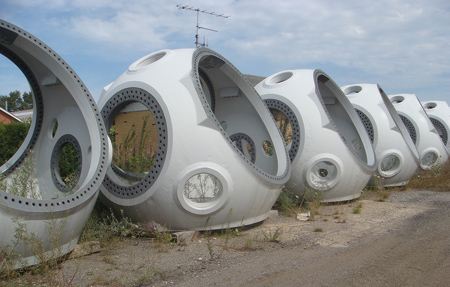
Wind Turbine hubs machined and painted, ready for shipment to wind energy fields
Nordmark Maskinfabrik A/S, Saeby, Denmark, was in need of a machine to manufacture large components for its energy customers. "I anticipate that wind energy is moving toward more offshore wind energy fields which require larger six, eight or even 10 Megawatt wind turbines, larger than land-based wind energy fields which require 5 or 7 Megawatt wind turbines. We need Nordmark to be prepared to meet our wind energy customers' needs for larger wind mill hubs and bases," said Michael Jacobsen, Owner of Nordmark. This would require a very large horizontal boring mill that Jacobsen did not find available on the machine tool market.
Nordmark Maskinfabrik A/S has three plants in Denmark focusing 85% of its machining time on wind turbine components. The company machines 500 hubs per year, producing 50 to 60 tons of metalworking chips in a week. The very large castings, weighing up to 80 metric tons (88.18 U.S. tons) and measuring up to 105' x 16.4' x 6.5', have an initial value of $28,000 - $78,000.
"We discussed with Fermat Group A/S of the Czech Republic our need to be ready for this larger wind turbine market," explained Jacobsen. Nordmark currently runs seven Fermat horizontal boring mills in its plants. "Because of our good success with our seven Fermat HBMs and having a good working relationship with Fermat, we discussed with them the development of a new larger horizontal boring mill with the milling and drilling capacity for the large wind turbine hubs. The machine would need to have an 8-meter height column (26.2 ft.), a tilting rotary table that could hold up to 80 metric tons (88.18 U.S. tons) of weight, a ram to extend both the head and spindle out to reach all areas of the large components and a robotic tool changer. The robotic tool changer frees up the area around the headstock while allowing for storage of many more tools," said Jacobsen.
To meet this need Fermat has now developed the new WRF 160 Heavy / z 1600 horizontal boring mill with a 160 mm spindle diameter that holds CAT 50 tools, spindle travel in the W-axis of 1,000 mm (3.28 ft.), ram travel in the Z-axis 1,600 mm (5.25 ft.) and a tilting table with a load capacity of 80 metric tons (88.18 U.S. tons). The longitudinal travel in the X-axis stretches up to 28,100 mm (92.19 ft.) and vertical movement of the spindle in the Y-axis is 8,000 mm (26.25 ft.). The HBM is designed with a double column for stability rather than using a single column with a counter weight. As the headstock moves up and down the column it utilizes four servomotors. The headstock is a ram-type allowing for extension of the spindle to reach all parts of large components. The columns move along the bed on four separate rolling guideways (optional hydrostatic guideways). As the headstock moves in the vertical direction, four linear optoelectronic position sensors provide feedback to the control for accurate positioning. The movement of the columns is provided by two motors with two gears and pinions and a rack positioned on the bed. The position of the columns is measured by an optical linear position sensor.
On the new WRF 160 Heavy / z 1600 the tilting rotary table is controlled by the Heidenhain control system. The rotary encoder at the center of the rotary table allows for automatic positioning of the table in increments of 0.001°. The automatic head can change positions while still spinning in order to continue machining as soon as possible. Right-angle and universal heads are available for the machine and are to be included with the Nordmark machines. From a pickup station the machine will store, pick up and automatically change the heads. An automatic chip conveyor carries chips away from the machines. The new machines will have up to 18 axes due to the multiple servomotors on each axis.
Two Fermat WRF 160 Heavy / z 1600s are being manufactured for Nordmark. Each machine will include a Robotic Tool Changer consisting of a KUKA robot with 105 tool positions running on a five-year battery all protected by a safety barrier. The machine column moves toward the robot and the robot arm moves to the spindle and replaces the tool. "This may seem counter productive but in the long run allows for much more flexibility. The standard automatic tool changer is close to the moving column, sometimes restricting areas around the machine. The robotic tool changer frees up this area for large bulky components," explained Jacobsen. "The tools on the robotic tool changer rack stay clean, well organized and allow for presetting to be done offline utilizing a small computer chip in the tool. Redundant tools can be placed on the rack so that if one tool is broken or becomes worn a new one is ready to use. In the case of a regular on-board toolchanger, the machine will look to see if the tool is on the rack and shut down if it cannot find the tool," said Jacobsen. The machine will have through-tool coolant capabilities. One of the tool positions will hold a Heidenhain probe for alignment, for finding the starting point, for high-tolerance positioning for drilling holes and for other in-process gauging for quality control purposes.
After the two new WRF 160 Heavy / z 1600s are assembled by Fermat in Brno, Czech Republic, they will be tested in multiple ways. The components and assemblies such as the headstock are tested before they are assembled into the machines. Then, when the machines are ready to ship, they will be disassembled and packed for shipment to Denmark. Nordmark is preparing a new building for the two machines. The cement floor is 3 meters deep (9.84 ft.) to support the weight of the heavy machines. The foundation will be fitted with 530 foundation bolts to hold the machines. After the machines arrive in Denmark, they will take eight to ten weeks to reassemble. To see the assembly of these two machines in progress go to: https://www.youtube.com/watch?v=B_40NoH3ZcI.
Nordmark, with a total of 120 employees, machines the wind turbine's hub, base plate and other large components. The company also does shaft rebuilding. The hubs can weigh up to 80 metric tons (88.18 U.S. tons). Large cranes carry the casting provided by Siemens Energy, Vestas or Nordex to the machine tables. Nordmark's customers send a CAD drawing that goes direct to the Heidenhain control on the machines.
The fixtures that hold the castings are custom made by Nordmark. Most of the machining is done on Fermat HBMs. Drilling of holes is done from angles using a right angle head or universal head. A tilting headstock on some of the machines also allows milling and drilling on angles. Five years ago Nordmark purchased its first Fermat HBM with a tilting headstock. The Fermat HBMs currently on the shop floor at Nordmark have 4.5-meter (14.76 ft.) up to 7.3-meter (24 ft.) columns to accommodate large hubs. The new machines will have an 8-meter (26.2 ft.) column height. It takes 72 hours to complete the machining of a hub utilizing a rotary table, an automatic right angle head and a universal head.
After the hub is milled and drilled, it is moved to another location on a trolley. The trolley moves the large hub to the paint booth, places it on a rack and then moves back out of the way. The surface is cleaned with water, sandblasted, painted and the outer surface is coated with sand to create high friction to facilitate moving the hub into place later. The hub is then wrapped in plastic to keep it dry.
Another large wind turbine component that is 7.5 meters (24.6 ft.) in diameter was being machined on the inside diameter. A ram on the Fermat HBM extended the spindle to reach all parts of the component. Due to weldments that could cause pressure build-up and cause the component to lose roundness, machining was performed from opposing sides one after the other to retain the roundness of the large wind turbine component.
"Nordmark places emphasis on quality control at all phases of the machining and finishing process," said Jacobsen. "Currently Nordmark utilizes M&H probes for in-process gauging for quality control. The new machines will have Heidenhain probes. A Faro Laser Tracker quickly measures large parts for quality control. Nordmark is able to produce components on the Fermat HBMs with 50-micron tolerance."
"Our Fermat HBMs have proved to be productive. Nordmark runs three shifts a day, seven days a week. Fermat's service department is always available and will ship replacement parts even on the weekend so we can get our machines back to cutting chips. Because Fermat uses less parts in its machines and uses well-known components such as servomotors, these types of replacement parts are readily available. Internet diagnostics are also available from Fermat. Fermat's training was all done on site for our convenience. We look forward to receiving our new large Fermat HBMs and to being prepared for the wind energy market's requirements for ever larger wind turbine hubs and components," said Jacobsen.
For more information contact:
Paul Mandelbaum
National Sales Manager
Lucas, A Fermat Group Company
13020 St. Clair Ave.
Cleveland, OH 44108-2033
216-451-5588
paulm@lucasprecision.com
www.lucasprecision.com
Petra Mrkvová, Export Department
Fermat Machinery
Prumyslova 11
102 19 Prague 10
Czech Republic
Cell: 011-420-774-339-345
petra@fermat-machinery.com
www.fermatmachinery.com