
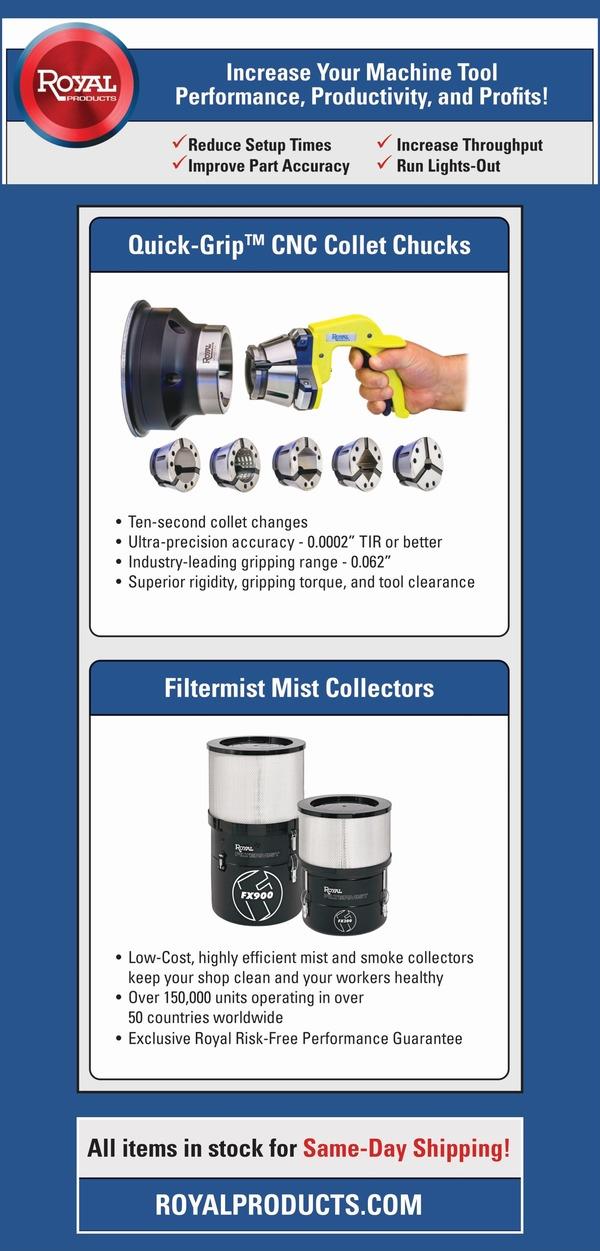
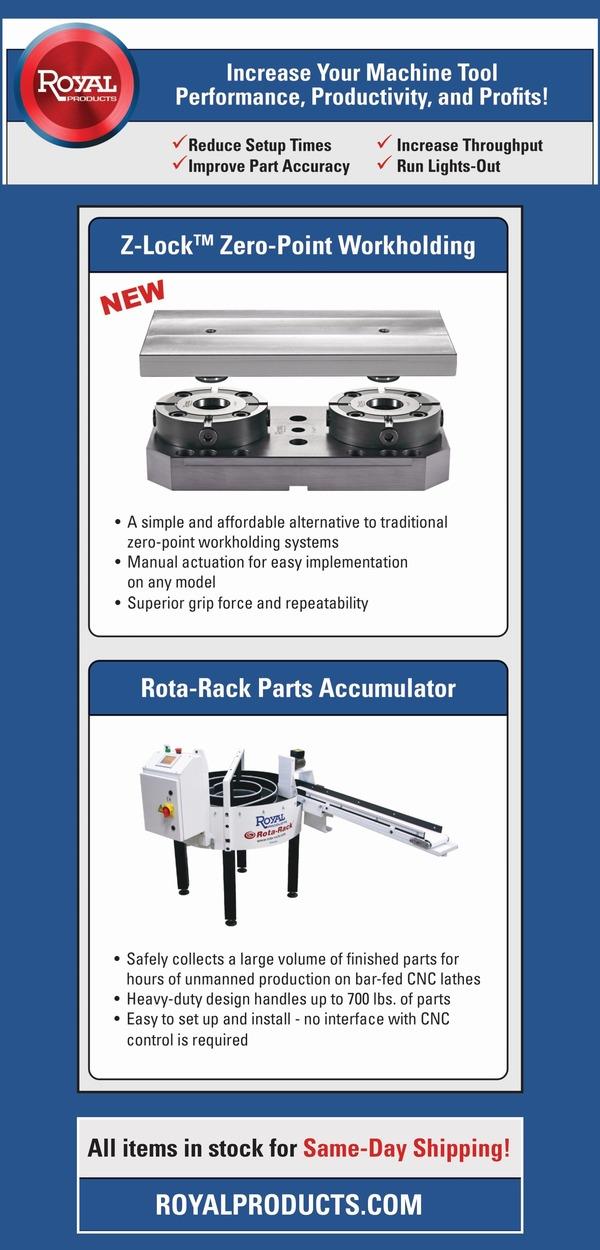

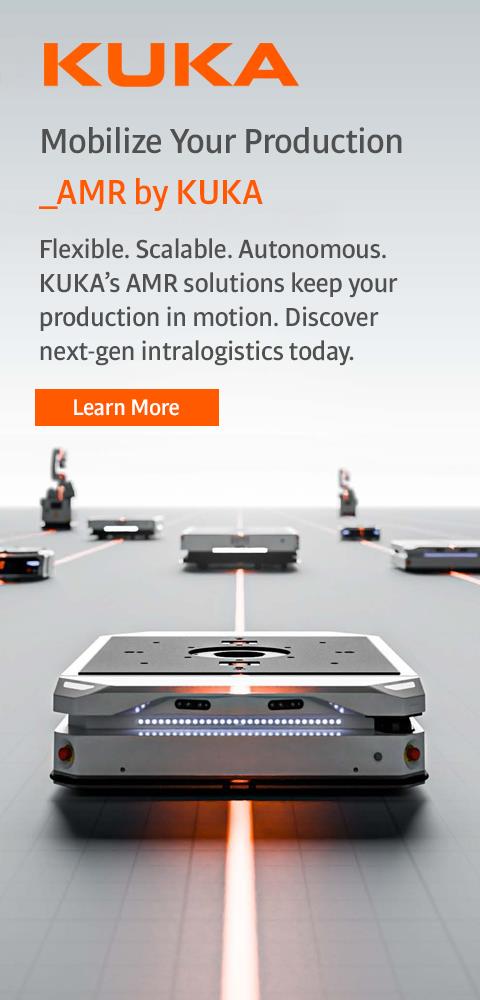
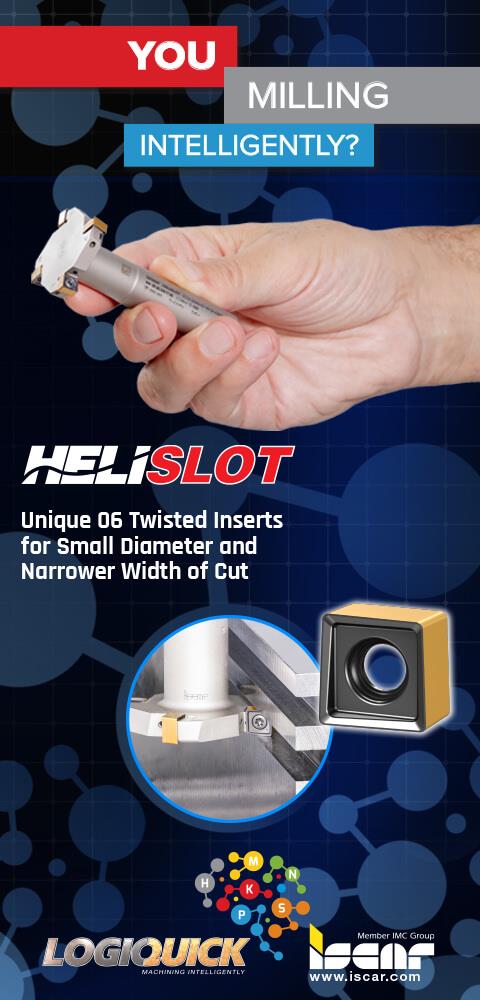
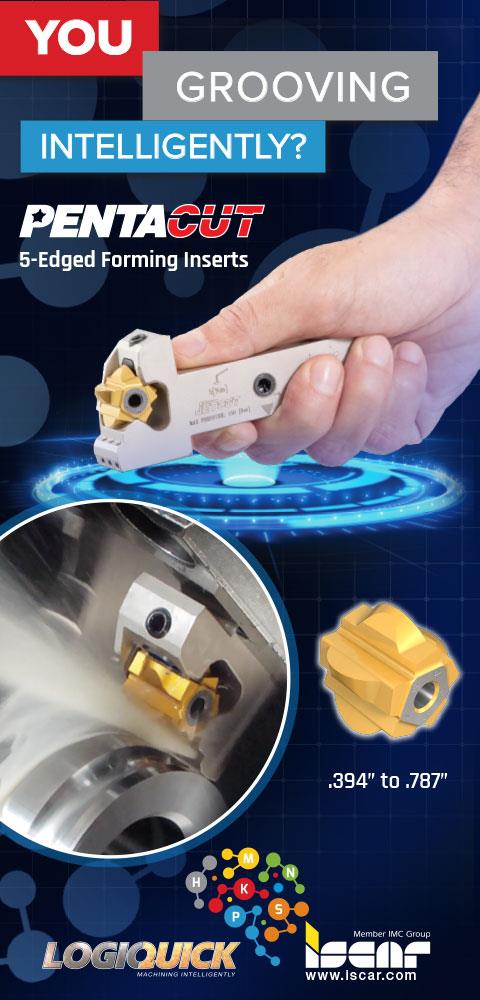
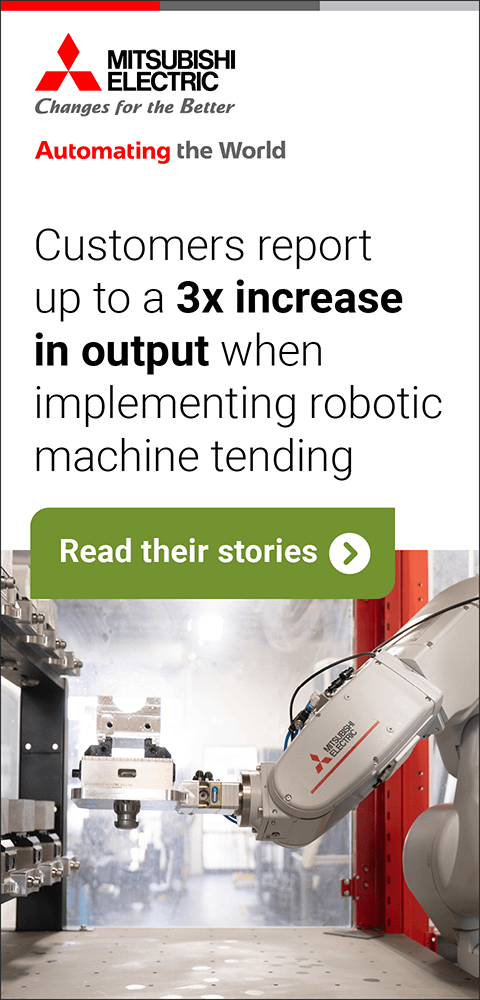
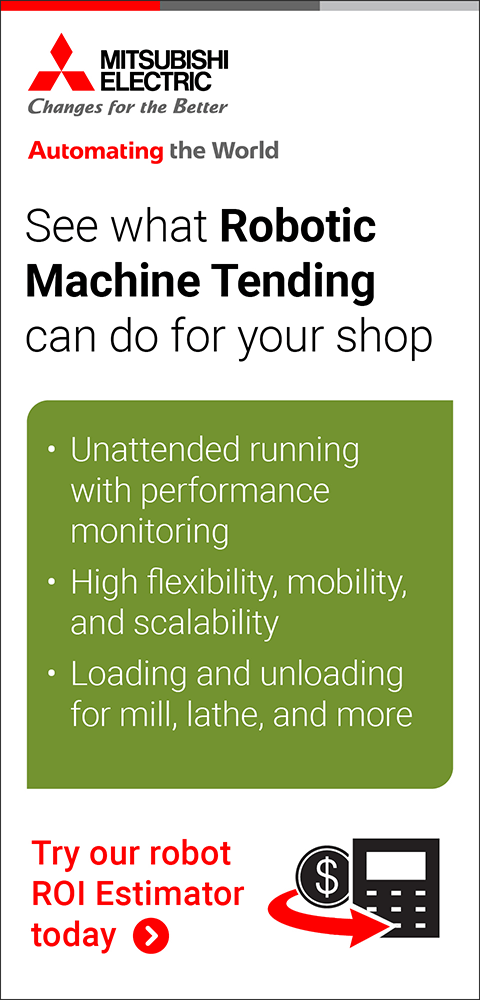
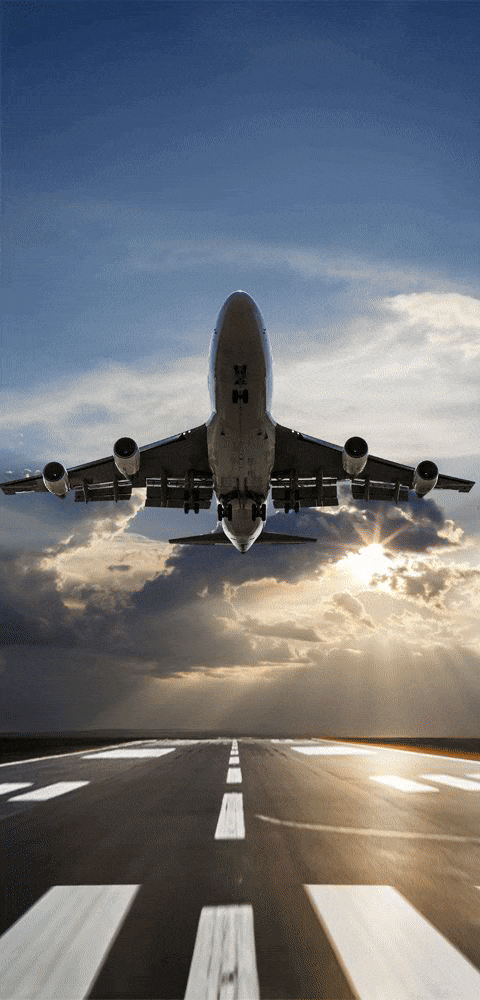
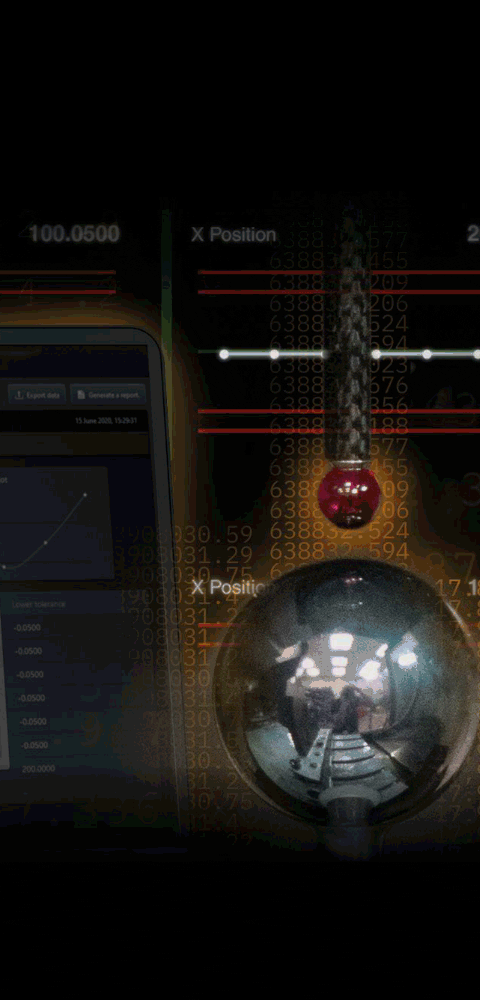
Vertical Milling Machines for Die/Mold Work
October 1, 2015
MC Machinery System's Diamond Cut milling line is comprised of five series of vertical machining centers and drilling and tapping machines, including the DM Series designed specifically for the mold and die market.
The DM Series features a rigid and accurate tooling system and is designed for close-tolerance work, making it suitable for applications in mold and die. The 32-position automatic tool changer provides better tool life management. A 20,000 RPM HSK-A63 spindle, linear scales, roller guideways, auto oil lube system, chips auger, air gun, water gun and spindle chiller are standard features of the DM Series.
The M720 Mitsubishi controller allows for easy operation. It features automatic workpiece position measurement, conversational programming and advanced graphic check capabilities.
Machine Features
- Rigid Meehanite base: wide base, box-shaped column, enhanced saddle and fully supported workpiece structure all contribute to the ability for heavy-duty machining.
- Finite Element Analysis is used to calculate the finest combination of cast iron components and rib structures of the spindle head and machine base.
- Large-span base effectively supports and evenly disperses the load force from the saddle. Short cantilever of the saddle ensures dynamic precision.
- Optimized contacting ratio between the spindle head and machine column provides spindle head rigidity during heavy cutting loads as well as ensuring the geometric precision of the spindle.
- Linear motion ways of the heavy-duty roller guide type are used on all three axes engineered to withstand heavy loading, tolerate high acceleration with rapid movement, ensure precise positioning and provide the best surface finish.
- High-performance 20,000 RPM spindle utilizes an integral motor using angular contact ceramic bearing technology which operates with an oil mist lubrication system. For continuous high speed operation, a surrounding jacket of oil, circulated through a chiller system, stabilizes spindle temperature. Thermal displacement is reduced guaranteeing spindle precision and lifespan.
- Super HSK tooling: Without well balanced, rigid and precisely made tooling, precision high-speed machining and drilling cannot be successful. The DM Series incorporates an HSK-A63 taper shank for extreme clamping force and rigidity.
- High-speed high-precision 3-axis direct drive motors eliminate backlash and achieve high-precision and provide stability during high-speed transmission.
- High rapid travel speeds of the X & Y axes are 945"/min., while the Z-axis speed is 787"/min.
- Linear glass scales are standard on all three axes to provide cutting accuracy.
- Spindle splash ring provides eight splash nozzles on a ring surrounding the spindle. The splash coolant both lubricates and cools the tool and workpiece improving tool life and part accuracy.
- Coolant through spindle prep: All the internal plumbing has been provided to easily allow for the connection of the Chip Blaster Option which provides over 1,000 PSI to greatly improve tool life and machining / deep hole drilling speed.
- Large volume coolant supply: Tank is located under the machine to conserve floor space and provides 77 gal. capacity to help remove chip heat.
- High-speed ATC system and magazine unit provides a fast tool changer system that uses a unique cam drive device which can be activated rapidly by PLC program from any tool position.
- Standard 32-position tool changer uses an arm type bi-directional tool exchange system reducing tool change cycle times. The cam driven tool magazine is designed for rotation accuracy and smooth motion even under a full load of tools.
- High-efficient chip removal system starts with complete covering of all the axis surfaces dropping the chips into the collection pan in the machine base providing a smooth flow of chips into the high capacity chip auger mechanism.
- Disc-type oil / coolant separator effectively separates the floating oil and the coolant ensuring prolonged lifespan of the coolant.
- Automatic lubrication system is a centralized oiling system providing lubrication for all drive system components, LM ways and ball screws. This energy saving system will discontinue feeding after the drives sit idle for a pre-set amount of time.
- Convenient operation is provided by a wide front door opening which simplifies the loading/unloading of fixtures and workpieces. Large side access doors/panels are also provided for ease of access for either the operator or automation. A high luminance internal explosion-proof work light is provided to aid in fixture and part set-ups.
For more information contact:
MC Machinery Systems, Inc.
1500 Michael Drive
Wood Dale, IL 60191
630-616-5920
mitsedm@mcmachinery.com
www.mitsubishi-world.com
< back