
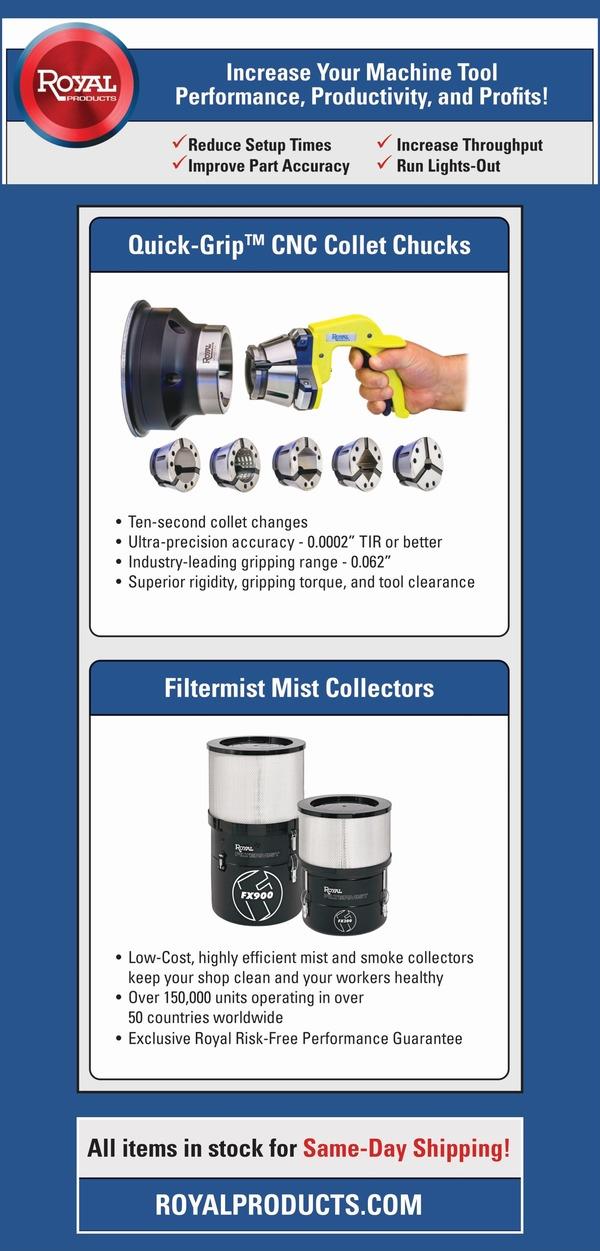
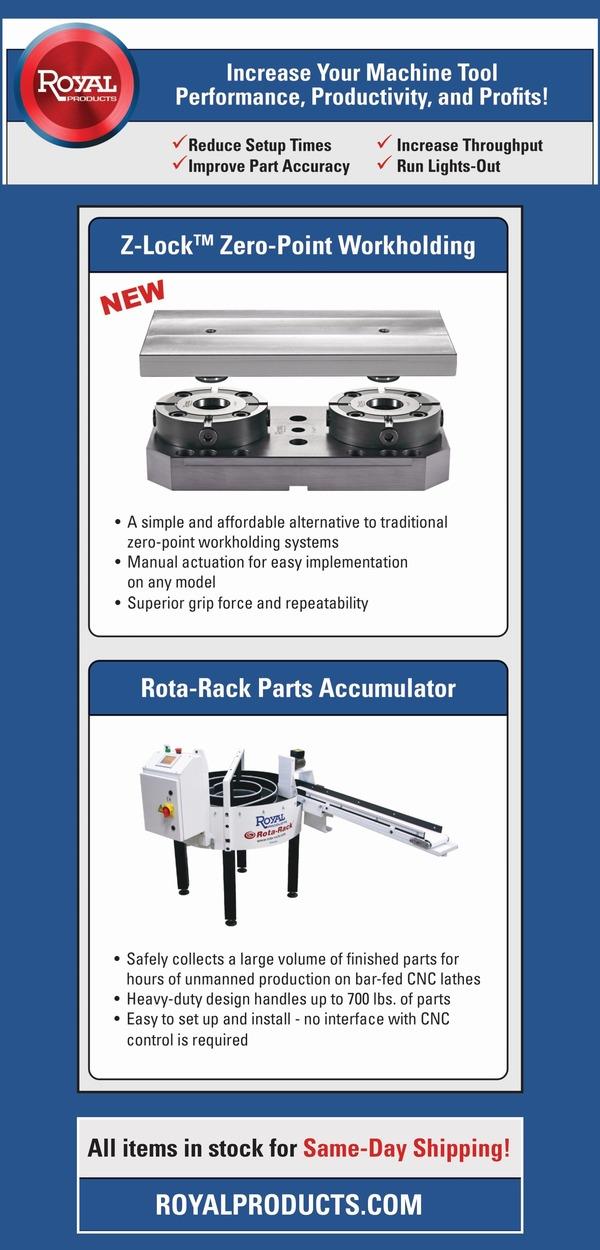

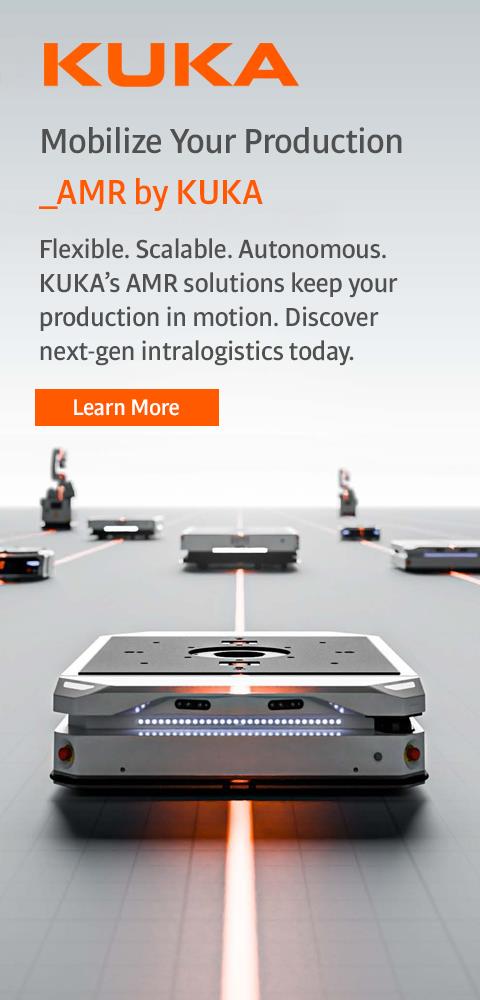
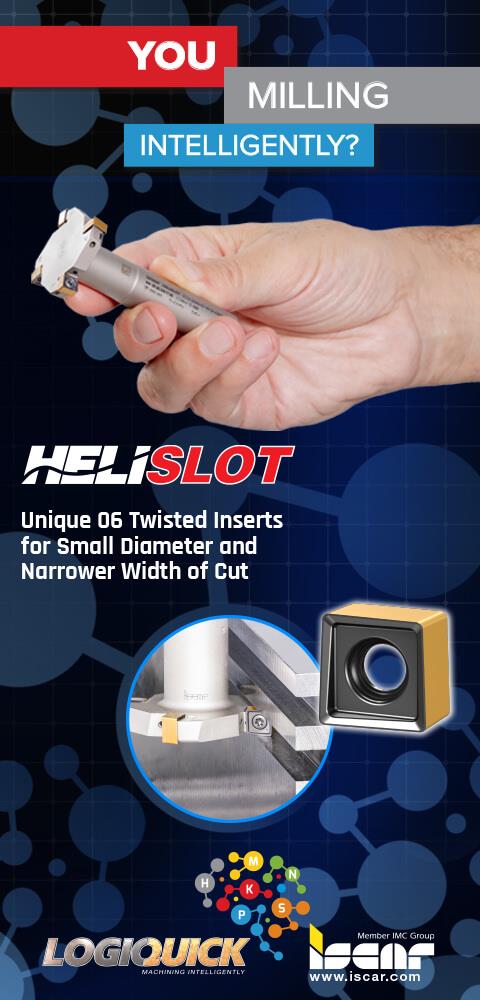
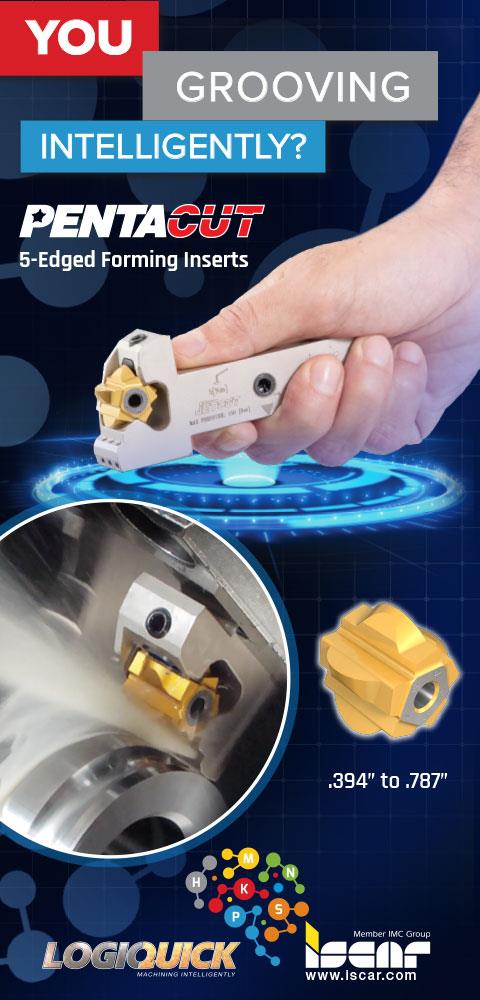
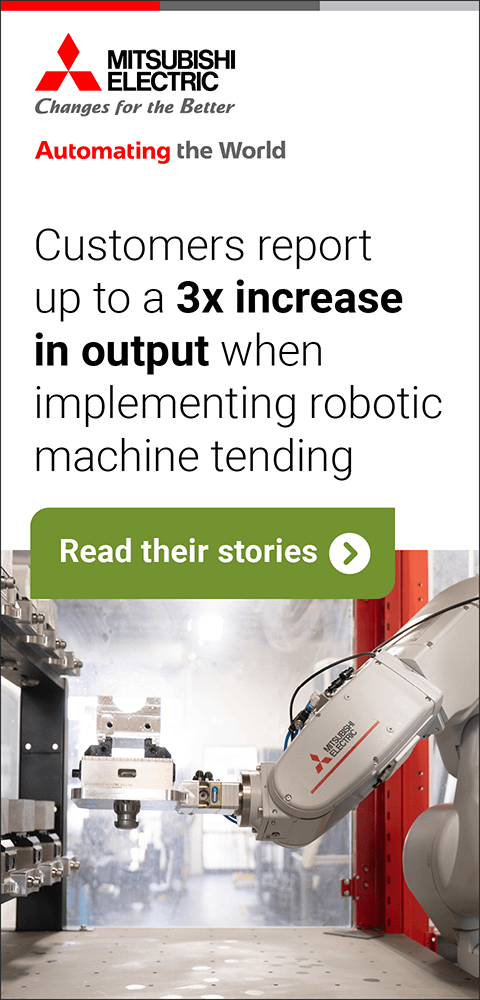
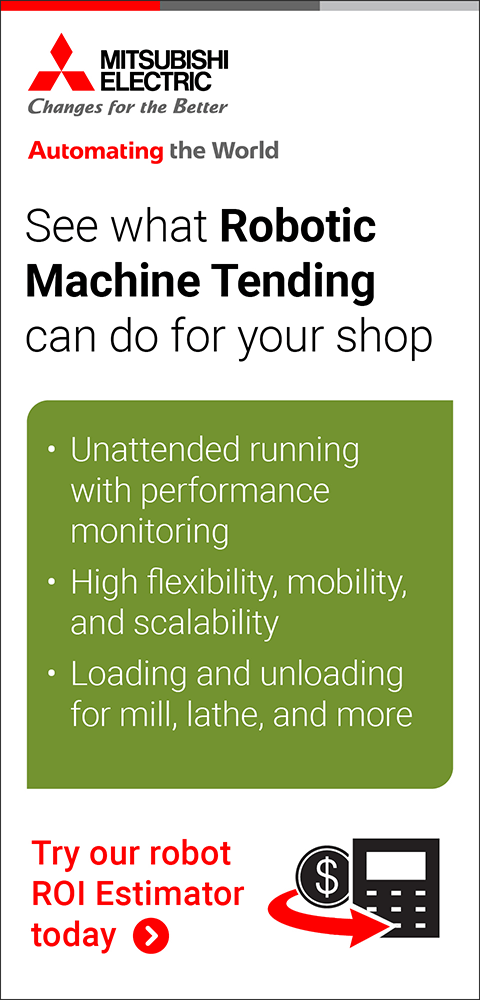
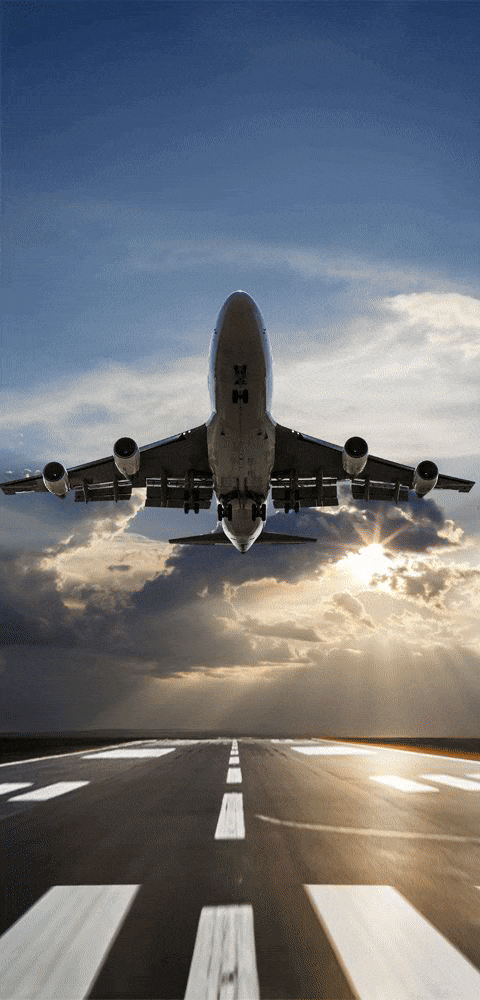
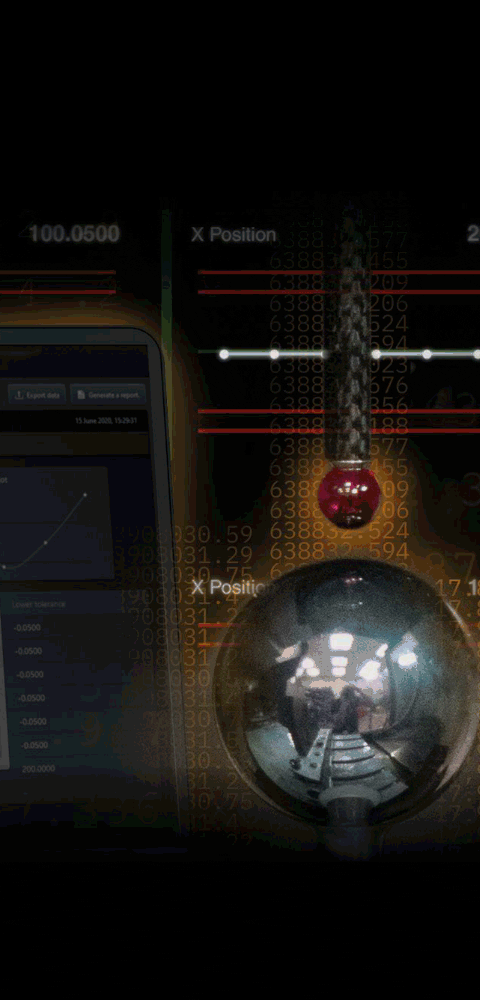
Clamping Sleeves Engineered to Support Today's Machine Tools
August 1, 2016
Euro-Tech Corporation will spotlight Kostyrka German-engineered clamping sleeves at IMTS 2016. Kostyrka slotted clamping sleeve technology is based on the idea of creating a shaft-hub joint actuated by hydraulic pressure to efficiently support the workholding function of modern machine tools.
Flexible metal plastic composite bushes in housings surround the part and clamp it by applying pressure oil to the sleeve jacket. The oil pressure is converted loss- and reaction-free into a radially acting clamping force. The sleeves spring back to their starting position after the oil pressure is removed and the clamped part is released.
"The surfaces of the clamped parts are not damaged with this adherence-actuated form of power transmission," said a company spokesperson. The part being clamped can withstand a holding force in excess of 22,000 ft-lbs. with only negligible axial movement.
The clamping sleeve's main body consists of a copper/tin, copper/tin/zinc or a copper aluminum alloy. Sleeves subjected to high stress may be made from case hardened steel or spring steel. The plastic jacket with a double-sided O-ring/back-up ring combination is manufactured from PA or POM and is resistant to mineral oils, brake fluid and low-flammability hydraulic fluids (up to 100 °C). The working pressure is 50-450 bar (700-6,500 PSI). General tolerances are: outer diameter D = g6, inner diameter d = H7, Length L = -0.1 mm (-0.004"). Seals of the sleeves are resistant in the temperature range of -30 °C to +110 °C.
Special versions are available for higher operating temperatures and working pressures outside the standard of 50-450 bar (700-6,500 PSI) range. Special tolerances are possible. For high temperature applications, sleeve seals will use VITON O-rings.
For more information contact:
Euro-Tech Corporation
N48 W14170 Hampton Avenue
Menomonee Falls, WI 53051
262-781-6777
info@eurotechcorp.com
www.eurotechcorp.com
IMTS 2016 Booth W-2453
< back