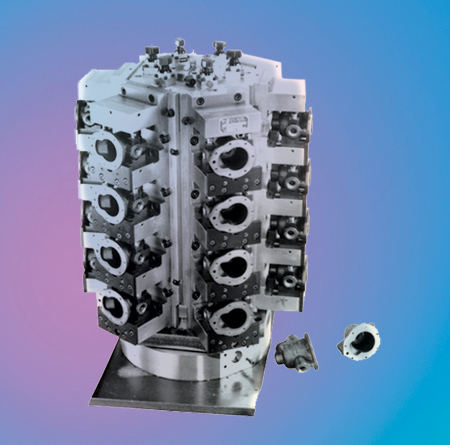
Special Double Hexagon Hydraulic Fixture, allowing continuous production by reducing load/unload and handling operations, is designed for high-volume production applications.
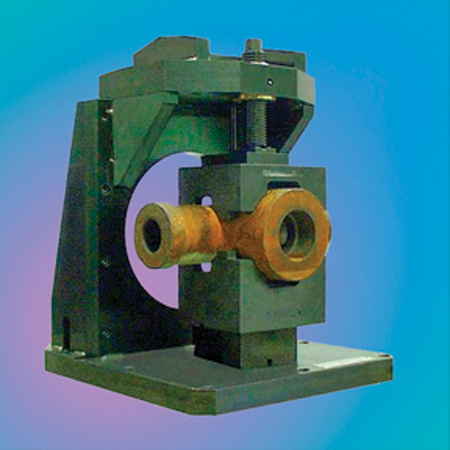
Royal "C" Frame Fixture is designed to hold large valve bodies by allowing flange diameter and its back face to be finish-machined in a single operation.
When a customer requests a "special" workholding fixture, meaning a fixture for a particular part or family of similar parts, corporate personnel take on a concentrated, unique teamwork attitude. Workholding specialists in sales, engineering, manufacturing and quality control begin working closely together as a project team from the onset of the request to ensure meeting the customer's requirements.
Initial customer communication is vital to the success of the entire project. First, the customer is asked to supply sample parts, part prints, machine tool information and the tooling package to be used to manufacture the parts in the facility. In addition, the customer can then communicate any concerns they may have regarding the project. For instance, concerns may be schedule or budget constraints, previous manufacturing difficulties they may have encountered or, if this is a new part for the company, possible future difficulties they feel may occur.
Specific questions need be answered at this point in the process. How many parts can fit in the machine tool's envelope? Does the machine have a pallet system? How can the project be made ergonomically safe? Now it can be determined whether to use a sophisticated hydraulic fixture or a manually operated fixture.
Hydraulic fixtures are normally used with higher volumes of parts when shorter cycle times and fast load/unload times are required. Manually operated fixtures normally are used with lower volumes and longer cycle times.
A concept design is then presented to the project team for review. If necessary, any changes are made to facilitate manufacturing and assembling of the fixture. Careful consideration of a customer's needs is always of utmost consideration and importance. The design approval prints are then sent to the customer for review and approval.
When the customer agrees to the design concept, final drawings are produced, and a meeting is called with process engineering, manufacturing, quality control and assembly technicians. Any further changes to facilitate manufacturing are made, and engineering specialists make a final review of the drawings, and then they are released for manufacturing.
Production Control now plays an important role from the ordering of material to the preparing of schedule charts. Depending on the complexity of the fixture design, process engineers now begin to process - from a few details to as many as several hundred. In turn, all of these details need to be juggled throughout various manufacturing and inspection operations. The end result is that all the components must arrive at the proper time for final fit.
Usually, after several weeks of manufacturing and many hours of careful planning, the new special workholding fixture has reached final assembly, and the project nears its completion. Assembly technicians, project engineers and quality control specialists assemble, test and measure all of the critical aspects of the specially designed fixture to insure its integrity and workmanship. Sample parts are loaded/unloaded and checked for repeatability and proper grip.
The final step in the process is to check tool clearances against the tooling package provided by the customer. Once this has been completed, the project is ready for final review. The special project team then invites its customer to its facilities for a complete review of the newly completed fixture. Once the customer is completely satisfied and final approval is given, the custom-built, American-made fixture is shipped.
Authored by Guy Byrne, Senior Vice President/General Manager, Royal Machine & Tool Corp.
For more information contact:
Bernie McAloon, Sales Manager
Royal Machine & Tool Corp.
P.O. Box Y
4 Willow Brook Drive
Berlin, CT 06037
860-828-6555
royal@royalworkholding.com
www.royalworkholding.com