Fast Response and Precise Accuracy Shapes Gear Tooth Cutting Service
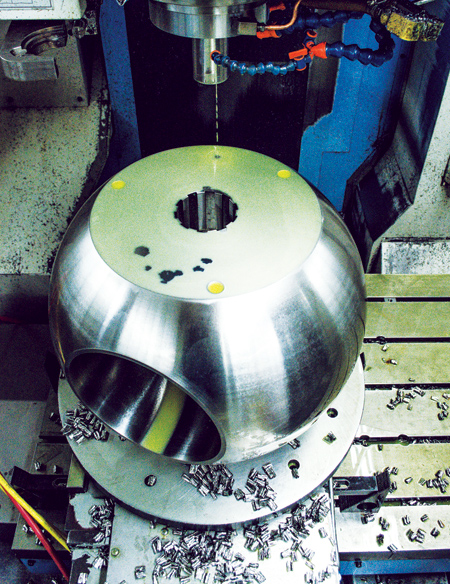
Cutting a parallel key spline on a large ball valve gear
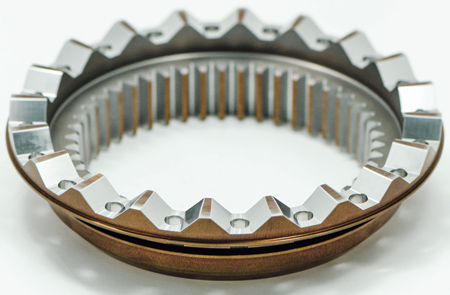
A complete face clutch gear after tooth cutting is complete
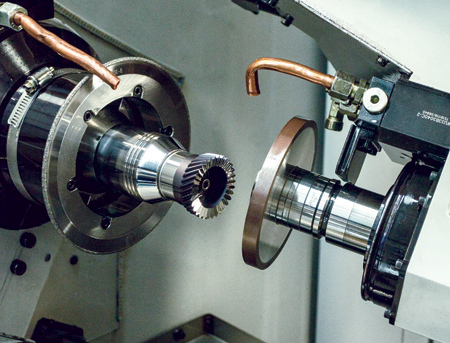
Sharpening of a helical shaper cutter on a state-of-the-art 5-axis CNC grinder
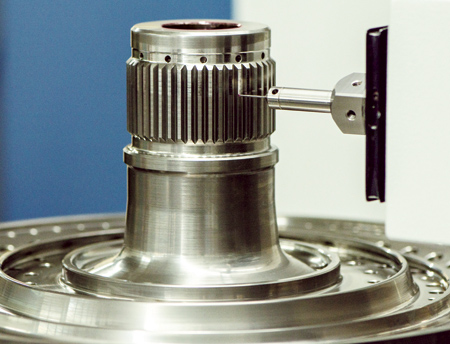
Precision inspection of tooth-to-tooth spacing on a completed gear
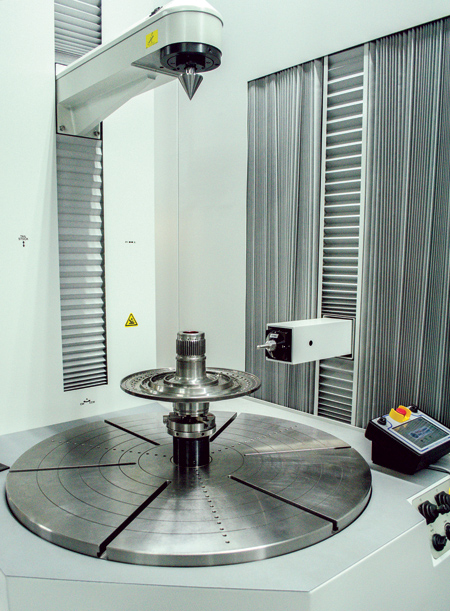
One of Perry Technology's many computerized inspection systems, performing an analysis of a completed gear
For more than half a century Perry Technology Corporation has provided gear and spline manufacturing services. From its 150,000 sq. ft. facility in New Hartford, CT, the company serves customers around the world. It is recognized as one of the Northeast's largest and most technically competent gear shops.
Perry Technology manufactures a diverse variety of custom made-to-order parts including involute spur and helical gears, worms and worm gears, bevel gears, face and tapered gears, and splined power transmission components. Perry also offers subcontract precision gear and spline tooth cutting services.
"More and more customers are coming to Perry for custom subcontract tooth cutting," said Carl Gangloff, Manufacturing Supervisor at Perry Technology Corporation. "Modern manufacturing is very complex with designs that require extreme precision, expensive materials and customization. We have built our operation here to be one of the best and most robust tooth cutting shops in all of North America."
About Tooth Cutting
Tooth cutting is the act of machining a part to remove material and create teeth. Tooth cutting at Perry Technology Corporation is accomplished by hobbing, shaping, milling, broaching or grinding. The component's design and the location of the teeth determine which process is most suitable.
It is most common for teeth to be cut or ground into hardened steel alloys. Specialized aerospace and defense components are frequently made from titanium or nickel-based superalloys such as Monel or Inconel. Perry Technology can produce gears and splines out of virtually any material.
Typically, a tooth-cutting customer will partner with Perry in a value-engineering review to confirm the manufacturability of the component. Perry engineers help identify potential issues with the design and offer advice on the customer's process sequence to assure the final product will conform to order specifications.
"Our staff is so experienced, and the equipment we have is so extensive, customers know we can get the job done no matter what material is used," continued Gangloff. "We have filled an impressive number of orders for parts that other gear manufacturers did not have the capabilities to produce. We have the equipment, skills and know-how to do it right the first time."
Perry Technology has 92 gear tooth cutting machines including an array of state-of-the-art CNC gear shapers, CNC gear hobbers and CNC gear grinders. The company's capabilities range from tiny fine pitch gears and serrations to heavy-duty coarse pitch gears that are 36" in diameter or larger. One of the longest splined shafts the company machined was over 30 feet in length. Each order is custom-produced to customer requirements.
"Perry Technology has allocated extensive machinery and personnel to service fast turnaround orders. It consistently provides same day or next day tooth cutting services to some of America's largest aerospace companies. Perry's inspectors are accredited by many of these customers and use delegated sign off authority to minimize cost and throughput time.
"I have had customers come to Perry after they tried to subcontract teeth cutting services elsewhere and it did not work," noted Gangloff. "They had an $80,000 part that was ruined because the vendor just did not have the experience."
Gear Engineering
Perry Technology has an in-house engineering department dedicated to assisting customers with their designs. Perry engineers help to determine the manufacturability of the gear - reviewing tolerance allowances, material stress limitations, teeth configurations and customer goals. They are also available to assist with prototype development, or integration of the gear into larger systems.
"One of our biggest strengths is the years of experience we bring to every job," said John Zukowski, Engineering Manager at Perry Technology Corporation. "We have been in business for almost 70 years, and many of our design personnel have decades of experience in gear engineering and manufacturing. We have the skills and equipment needed to get the job done. From one gear to hundreds or thousands, we understand how to apply our knowledge and support our customers."
Fast-Response Tooling
Perry Technology is able to produce tooling in house, including the cutters and grinding wheels needed for tooth cutting, which significantly decreases turnaround times. Typically, the company is able to create tools in days, as opposed to outsourcing the tool production to a vendor - which often requires months of lead time. The experience of the company's employees helps to ensure that the right tool is produced for the job, which maximizes machine output, improves operating efficiency and provides strict compliance to specifications.
Unrivaled Inspection
As a supplier of gear tooth cutting services for some of the world's leading aerospace companies, Perry Technology has made a significant investment in state-of-the-art computerized inspection equipment. Quality checks are integrated throughout the tooth cutting process to ensure quality and repeatability.
The company is able to check all aspects of a part with dimensional accuracy within millionths of an inch.
In addition to thousands of calibrated manual measuring tools and gauges, Perry Technology's dimensional inspection equipment includes seven large ZEISS Prismo coordinate measuring machines (CMMs) that utilize the latest Calypso and GEAR PRO software, with "program to model" capabilities. Four laser scanning measuring centers, four CNC analytical gear inspection systems, six computerized composite error measuring instruments, seven Gleason bevel gear testers, and five worm gear testers also make up Perry's Quality Control Department.
"The company's many layers of redundancy in both gear production and testing equipment is unique in the Northeast, and reflects a significant investment in the latest cutting-edge technology.
"Most companies have one or two ZEISS Prismos - we have seven," noted Zukowski. "We are always adding new technologies and redundant capabilities to improve our testing and quality. Documented test results are an essential part of our tooth cutting service offering. We understand the precision nature of our customers' components and their need for confirmation and documentation. I believe we have some of the most advanced and robust QC processes available in the industry."
If requested, Perry can conduct advanced testing on its gears and splines including documented results for runout, tooth-to-tooth spacing, index error, involute profile, tooth contact pattern, lead, fillet radii, corner radii, surface finish, tooth-to-tooth and total composite error, angular timing of teeth to other features on the part and more.
"One of the best parts of working at Perry is our reputation for quality," said Robin Centrella, Director of Sales at Perry Technology Corporation. "Our engineers, our manufacturing personnel, everyone here is dedicated to excellence."
Industry-Leading Experience
A family-run business for five generations, Perry Technology is one of the oldest and largest gear manufacturers in North America. The company has made specific efforts to retain skilled employees and provides on-going training on new technologies. The company currently has 120 employees, many of whom have worked at the company for decades.
"The combination of all our capabilities is really what sets us apart," continued Centrella. "When you combine the millions and millions of dollars we have invested in modern equipment, and the years of experience our staff brings to each job, you realize why so many companies rely on Perry Technology. Our team is incredibly skilled in gear and spline engineering and manufacturing. We solve problems that customers have had for years."
Perry's components are used in applications that are critical to system performance. While many of their customers come from the aerospace industry, they also serve a diverse market base including military and defense organizations, as well as commercial customers in the medical, power generation and machinery industries.
Perry Technology Corp. is certified to ISO-9001:2008 and AS9100C and can provide all necessary quality documentation including First Article Inspection Reports per AS9102.
For more information contact:
Robin Centrella
Director of Sales
Perry Technology Corp.
P.O. Box 21
120 Industrial Park Rd.
New Hartford, CT 06057
860-738-2525
sales@perrygear.com
www.perrygear.com