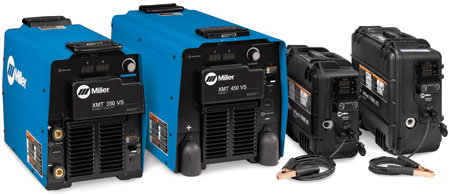
"The new multiprocess XMT ArcReach systems from Miller Electric Mfg. Co. have been designed to reduce downtime, costs and safety hazards by allowing welding operators to set the power source voltage at the weld joint without the use of control cables, minimizing unnecessary trips to the machine," said a company spokesperson.
"The new multiprocess XMT ArcReach systems from Miller Electric Mfg. Co. have been designed to reduce downtime, costs and exposure to safety hazards by allowing welding operators to set voltage at the weld joint without the use of control cables," said a company spokesperson. "This capability minimizes unnecessary trips to the power source, allowing for more arc-on time and greater productivity. By providing control of voltage at the weld joint, the new systems also reduce the opportunity for trips, slips or falls on the jobsite; encourage best-practice weld settings and weld techniques; and lessen operator fatigue associated with excessive walking to and from the power source."
The XMT 350 VS ArcReach (for 3- or 1-phase power) and XMT 450 VS ArcReach (for 3-phase power) are both suitable for industries such as shipbuilding and construction in which welding operators work at significant distances from the power source. Both systems are compatible with Miller SuitCase X-TREME 12 VS or 8 VS ArcReach feeders and provide multiprocess welding capabilities including MIG (GMAW), Stick (SMAW), TIG (GMAW) and Flux-Cored (FCAW) and Air Carbon Arc Gouging (CAC-A).
"In addition to generating more arc-on time by reducing trips to the power source, the XMT ArcReach systems help reduce downtime to address operator fatigue so welding operators are able to spend more time welding - enhancing productivity," said the spokesperson. "The XMT ArcReach systems also reduce downtime for troubleshooting welding system problems resulting from damaged control cables, as well as the expense of purchasing, maintaining, repairing and replacing control cables.
"The XMT ArcReach systems save time by eliminating the need to access and reconfigure power source settings after use. When a welding operator connects the ArcReach-equipped feeder to the XMT power source, the panel setting automatically converts to MIG/FCAW (with gas) if it detects an electrode positive connection or FCAW (no gas) if it detects an electrode negative connection. Disconnecting the feeder restores the power source's original panel settings, making it easy for the welding operator to switch processes right at the weld joint.
"The ArcReach systems provide remote override of weld process and arc voltage at the power supply, which prevents other welding operators from making setting changes. The welding operator can precisely set arc voltage at the feeder and monitor the actual arc voltage and current delivered to the weld using the digital meters on the feeder. Having this control at the weld joint makes it easier to adhere to weld procedures and prevents welding operators from settling for less than optimal settings, resulting in more consistent and higher weld quality."
For more information contact:
Miller Electric Mfg. Co.
P.O. Box 100
Lithonia, GA 30058
800-426-4553
info@millerwelds.com
www.millerwelds.com