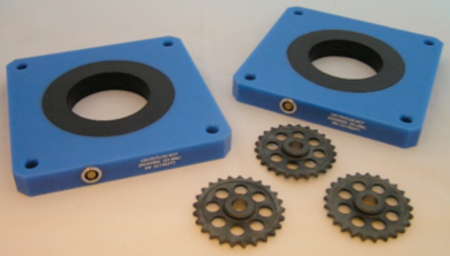
Eddy current encircling coils are shown. During eddy current testing, the part under test will be placed in the middle of the coil.
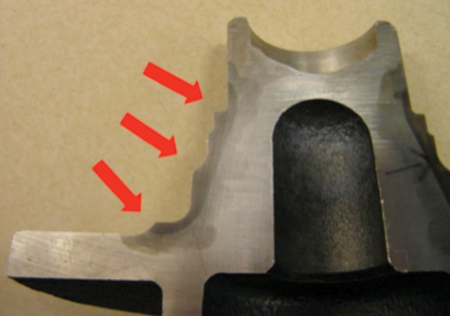
A cutaway is shown of a wheel bearing with a complex heat-treat pattern generated by localized induction heating.
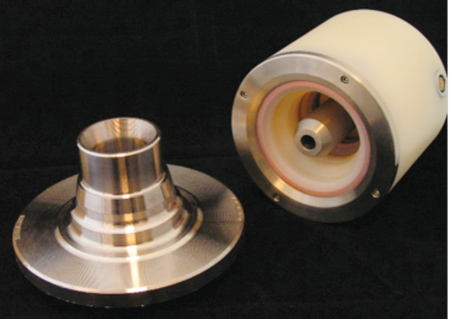
An eddy current heat-treatment validation probe is used to test a wheel bearing in three places and can detect improper heat treating due to induction heating element damage or failure, misplacement of the heating elements, improper quenching or other heat-treat process cycle issues.
"Eddy current testing systems have been used extensively to determine whether metal parts have been properly heat-treated," said Joe Jessop, Senior Applications Engineer and CEO, Criterion NDT, Inc. "These systems work on both powder metal and forged parts such as gears, bearings, shafts, tubing and pins, to name a few. Eddy current systems can easily be integrated into high-speed production lines and interfaced with production systems to reject parts that fail an inspection criterion."
Jessop reported that non-heat-treated gears can get mixed up with properly heat-treated parts. He stated that the difference in these parts cannot be seen visually. "A reliable, fast method is needed to find these bad parts," he said.
Eddy current testing uses electromagnetics to determine the proper internal structure of a part without the need for invasive, destructive measures. "It is a comparative test, where a part-under-test is compared to a known good part," said Jessop. "Differences in conductivity and permeability will change how the electromagnetic fields will flow in a part, so parts that are heat-treated differently will test differently."
Jessop stated that eddy current test systems consist of an eddy current instrument and test coil or probe. Modern eddy current instruments use multiple frequencies for testing and contain industrial I.O. that interfaces to production line PLCs and robotics. Eddy current probes can be designed to validate the overall heat treatment of a part or specific locations of heat treatment such as a bearing race on a part. The part under test is placed in the middle of the coil. "The actual test takes only a few hundred milliseconds so it can easily keep up with production line speeds," said Jessop.
For more information contact:
Joe Jessop
Senior Applications Engineer, CEO
Criterion NDT, Inc.
3702 West Valley Highway North
Suite 202
Auburn, WA 98001
253-929-8800
joe.jessop@criterionndt.com
www.criterionndt.com