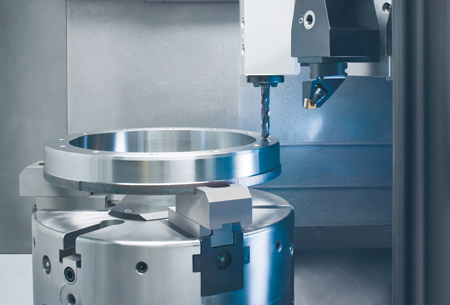
The work area of the VM 9, with a bottle spindle to hold workpieces up to 450 mm, is shown.
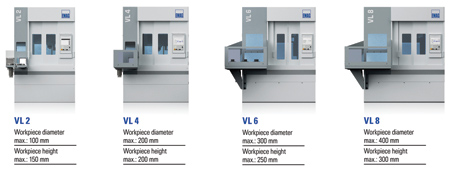
"The VL series is built for highly productive manufacturing," said a company spokesperson. "Idle times on these machines have been reduced to a minimum. For example, the chip-to-chip time on the VL 2 is just 5 seconds."
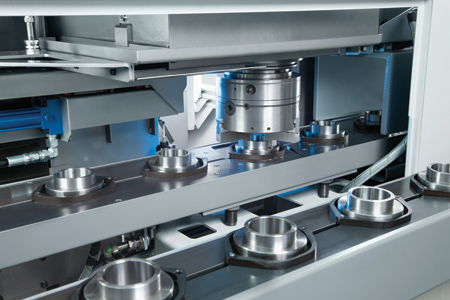
The parts are transported by an integrated O-automation system and loaded and unloaded using the pickup principle.
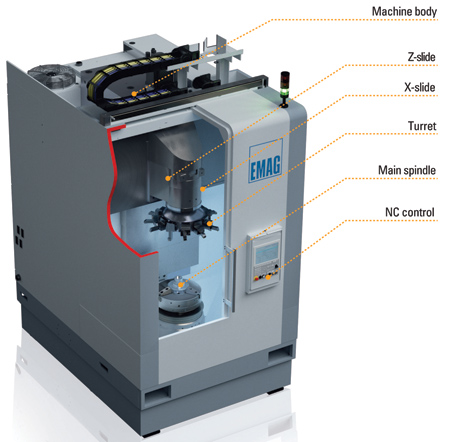
"The VM 9 spindle down turning center offers flexible, cost-effective production for small batches of chucked components," said a company spokesperson.
At WESTEC 2015, Sept. 15-17 at the Los Angeles Convention Center, EMAG will feature manufacturing systems for precision metal components with the North American premier of its new VM spindle down machine platform for production of small batches and complex geometries.
"Part of the large family of EMAG modular machines, the VM 9 vertical turning center combines a reliable platform with an extensive range of equipment," said a company spokesperson. "Designed to machine chucked components with a maximum diameter up to 450 mm, it features a tool turret which can be fitted with up to 12 tool positions and can be equipped with driven tools to carry out drilling or milling operations. An integrated probe ensures continuous quality control of the workpieces, making the VM 9 well equipped for a wide variety of production tasks." More information is available at vm-vmc.emag.com.
"The VL series will also be on display for visitors to experience the EMAG modular inverted vertical lathe design," said the spokesperson. "With the aim to develop a system of modular machines ideal for use in the manufacturing of medium and large batch runs, one common feature of all four machine sizes is the shared basic, compact design. Their small footprint means reduced floor space costs and flexibility in machine layout (for example, Chaku Chaku or closed loop arrangement). Every VL machine features an integrated O-automation system for transporting workpieces. When combined with the self-loading pickup spindles, this automation concept ensures short cycle times and high productivity. To accommodate machine operators, all the service units are easily within reach, with the various units (electrics, hydraulics, cooling system, cooling lubricant and central lubrication system) accessible at any time so that the machines can be maintained with ease." More information is available at vl-vt.emag.com.
The spokesperson stated that the technologies in the EMAG Group cover the entire spectrum of metalworking, including non-traditional processes. Electrochemical machining (ECM) is used in the aerospace sector for the manufacture of blisks, while laser welding is used in lightweighting automotive components.
"Introducing the latest addition to this technology portfolio, eldec will display a modular induction (MIND) hardening system at the show," said the spokesperson. "Featuring simultaneous dual frequency (SDF) technology, eldec hardening systems complement the workpieces machined by EMAG lathes to create efficient, complete production lines. The flexible machine concepts and complete systems from EMAG offer modular and customized solutions for the production of workpieces in nearly every industry."
For more information contact:
Peter Loetzner
EMAG LLC
38800 Grand River Avenue
Farmington Hills, MI 48335
248-477-7440
info@usa.emag.com
www.emag.com
WESTEC 2015 Booth 1523