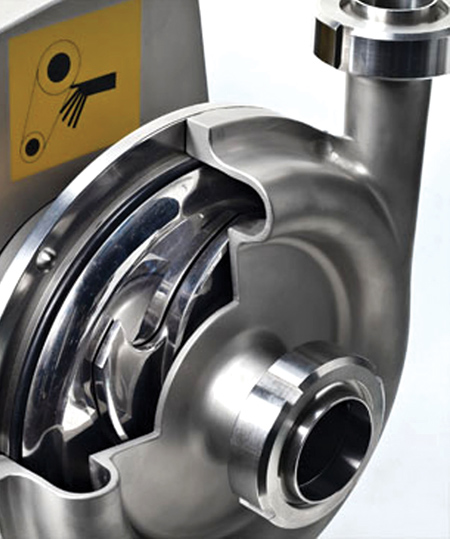
"Critical pumps with complex impellers subject to corrosion resistance are excellent candidates for significant performance improvement with Kennametal Stellite technology," said a Kennametal spokesperson.
Keeping a power grid up and running requires numerous components subject to extreme wear conditions, such as turbochargers, pumps, engines, exhaust fans and more. UltraFlex, a new wear-resistant solution from Kennametal's newest business unit, Kennametal Stellite, is designed to provide longer and more predictable service life for critical components with complex geometries in power generation, oil and gas and other industries.
UltraFlex is a coating process that bonds an appropriate Kennametal Stellite coating to metal substrates with full density. The company reported that steel parts coated with cobalt, for example, offer the same performance as fully cast cobalt components at a fraction of the lead time and cost.
"Parts with complex geometries, inner diameters and other non-line-of-sight features may encounter consistency problems with spray-on or other fused coatings," said a company spokesperson. "By comparison, Ultraflex is a slurry-based process where the appropriate coating for the component, whether titanium, carbide or other custom formulation, forms a slurry together with binders and other performance-based additives." The coating forms a metallurgical bond with part substrates dipped into it. Depending on the material system, cladding can range from 0.008 - 0.050" (0.20 - 1.27 mm) in thickness. Following the dip, the coating is air-dried to remove any water before sintering in a vacuum furnace at around 1,100 - 1,200 °C (2,012 - 2,192 °F).
Quench tests where UltraFlex components were soaked at 750 °C (1,382 °F) and immediately quenched in water at room temperature showed no coating delamination or crack formation. "Other tests comparing UltraFlex processing versus weld overlays showed the direct bonding with UltraFlex had a very small diffusion zone," said the spokesperson. "This lack of buffer layers and diffusion zones results in a distinctly 'pure' layer with minimal iron dilution and higher hot hardness compared to weld overlays."
Good base material candidates for UltraFlex include austenitic, martensitic and carbon steels, along with cobalt and nickel alloys. Titanium alloys, however, are not good candidates due to adverse chemical reactions, and some stainless steels (410) have shown increased strength but diminished ductility.
Pump Impellers
A U.S. Gulf Coast refinery recently experienced accelerated internal wear of oil pumps, often requiring entire case replacements. Compared to typical industry pump performance, run lengths were shorter, about a month, and cost per installed was higher. The application requires pumps capable of withstanding significant catalyst fines.
The refinery investigated several wear-resistant products for their pumps and found all were limited due to the nature of the technologies. Thermal spray coatings and weld overlays could be used in line of sight applications, but not for small interior surfaces. Thermal sprays also suffer from failures of the mechanical bond, they found, and there was preferential erosion of the soft matrix between the hard particles in weld overlays. Hard diffusion coatings (boronizing) are very thin and can be punctured by large abrasive particles.
Working with Kennametal, the company used infiltration brazed tungsten carbide cladding (ConformaClad) and UltraFlex to coat the inside of closed impellers unreachable by any other means. "The company was particularly impressed by the true metallurgical bond and a dense, uniform distribution of tungsten carbide particles throughout the coating, creating excellent erosion resistance and toughness in complex geometries," said the spokesperson.
"After 13 months in service, a treated oil pump showed no significant signs of internal erosion," continued the spokesperson. "This technology has also been applied to FCCU fractionator bottoms and debutanizer reboiler services, with no signs to date of increased vibration or loss of hydraulic performance."
For more information contact:
Kennametal Inc.
1600 Technology Way
P.O. Box 231
Latrobe, PA 15650
724-539-5000
www.kennametal.com
www.stellite.com