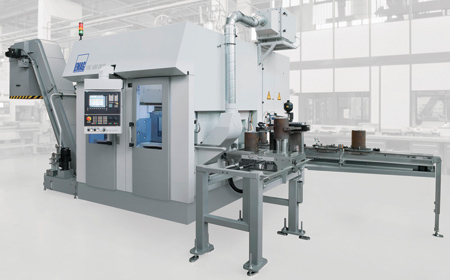
The VSC 400 DUO CM turning machine with automation is used in the production of coupling sleeves.
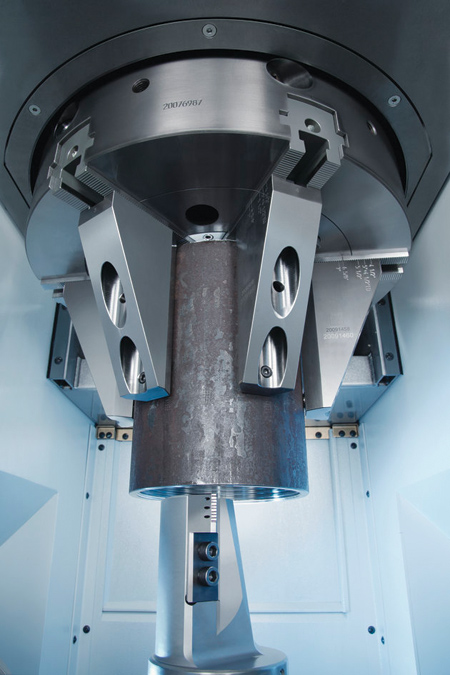
"The vertical construction of the VSC 400 DUO CM and VSC 500 CM coupling sleeve machines ensures optimal chip flow with no buildup of chips to interrupt the production process," said a company spokesperson.
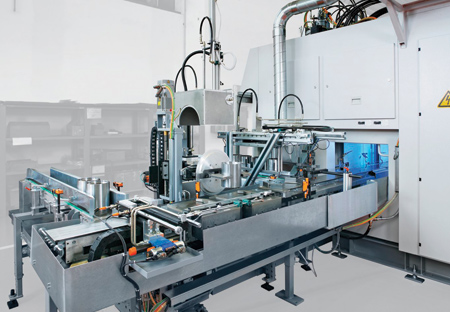
The automation system can be configured to suit customer requirements.
"Efficiency levels in the production of coupling sleeves can be raised considerably with the EMAG VLC and VSC series of machines," said a company spokesperson. "Although the coupling sleeve is a relatively small component, a great deal depends on its faultless performance. These sleeve or tool joints are used to precision-join the casings and delivery pipes with a perfect screw fit, providing an absolutely leakproof and durable connection of the highest precision while bearing the weight and considerable flexural stresses of the pipes. Production errors or large tolerances on the coupling sleeve can endanger the whole resource delivery process. Thus, the main focus is on efficient mass production techniques, with the key question being how a high quality of the production process for coupling sleeves can be guaranteed, especially when the job calls for a single production facility to manufacture millions of these components each year.
"The specialists at EMAG provide an answer to this question. For decades, the company has specialized in the machining of oilfield components such as coupling sleeves, tool joints and rock bit cones, as well as casings and delivery pipes. The production of coupling sleeves, in particular, shows how demanding this sector can be, with a multitude of processes from the actual threading operation to the cleaning process and from visual inspections to final plating. It also features a marking that details the component data (i.e., charge, material, manufacturer, machine, cycle time). This multi-layered production process benefits greatly from the intelligent EMAG machine concept, where process integrity and precision are built-in."
The spokesperson stated that coupling sleeve production lines use machines from the VSC and VLC series. They are equipped with a pickup spindle that is designed to not only collect the workpiece from the incoming conveyor belt but also to firmly hold it vertically while it is complete-machined in the tooling zone.
"This is of particular advantage where large quantities of these sleeves are to be machined," said Dieter Fischer, Managing Director. "The component can be produced in a much shorter time, as the various processes are carried out one after the other in cycle times counted in seconds. These processes do not only cover machining but also additional operations such as cleaning or measuring. When it comes to the mass production of coupling sleeves, in particular, the time savings add up to a competitive advantage for the user, as shorter machine runtimes lead to a massive reduction in component costs."
"All machining processes are fully automated, circumventing errors that occur when using an unnecessarily large number of workhandling processes," said the spokesperson. "The vertical machining concept also provides for optimal chip flow conditions, preventing the buildup of chips in the machining area, which can interrupt the production process."
The spokesperson stated that flexibility is an important focus of EMAG. The different frame sizes of the VSC and VLC series machines are designed to allow for the complete machining of coupling sleeves of a multitude of diameters; the VSC 400 has a capacity of 2" to 9" and the VLC 800 one of 7" to 24".
"Furthermore, the machines are capable of cutting all types of threads, a factor of great importance when it comes to the oilfield industry," said Fischer. "It is, of course, possible to machine coupling sleeves with threads to API and GOST standards, but proprietary threads can also be generated. Larger oilfield technology producers have their own thread standards, and we can equip our machines to suit these requirements."
For more information contact:
Peter Loetzner
EMAG LLC
38800 Grand River Ave.
Farmington Hills, MI 48335
248-477-7440
info@usa.emag.com
www.emag.com
Southwest
AR
David Fitzgerald
EMAG LLC
Charlotte, NC
248-595-1117
dfitzgerald@emag.com
www.emag.com
NM
Peter Loetzner
EMAG LLC
38800 Grand River Ave.
Farmington Hills, MI 48335
248-442-6590
info@usa.emag.com
www.emag.com
LA, OK, TX
Ric Lorilla
EMAG LLC
Houston, TX
248-595-1530
rlorilla@emag.com
www.emag.com
Southeast
AL, FL, GA, MS, NC, SC, TN, VA
David Fitzgerald
EMAG LLC
Charlotte, NC
248-595-1117
dfitzgerald@emag.com
www.emag.com
Northeast
NY, PA
James Petiprin
EMAG LLC
38800 Grand River Ave.
Farmington Hills, MI 48335
248-910-8413
jpetiprin@emag.com
www.emag.com
CT, DE, MA, MD, ME, NH, NJ, RI, VT
Jonathan Chomicz
EMAG LLC
Hartford, CT
248-497-8526
jchomicz@emag.com
www.emag.com
WV
David Fitzgerald
EMAG LLC
Charlotte, NC
248-595-1117
dfitzgerald@emag.com
www.emag.com
Midwest
MI, OH
James Petiprin
EMAG LLC
38800 Grand River Ave.
Farmington Hills, MI 48335
248-910-8413
jpetiprin@emag.com
www.emag.com
IL, IN, WI
Tod Petrik
EMAG LLC
Chicago, IL
248-470-2646
tpetrik@emag.com
www.emag.com
IA, KS, MN, MO, NE, ND, SD
Bill Konetski
EMAG LLC
Minneapolis, MN
612-804-0857
bkonetski@emag.com
www.emag.com
KY
David Fitzgerald
EMAG LLC
Charlotte, NC
248-595-1117
dfitzgerald@emag.com
www.emag.com
West
AZ, CA, CO, ID, MT, NV, OR, UT, WA, WY
Peter Loetzner
EMAG LLC
38800 Grand River Ave.
Farmington Hills, MI 48335
248-442-6590
info@usa.emag.com
www.emag.com