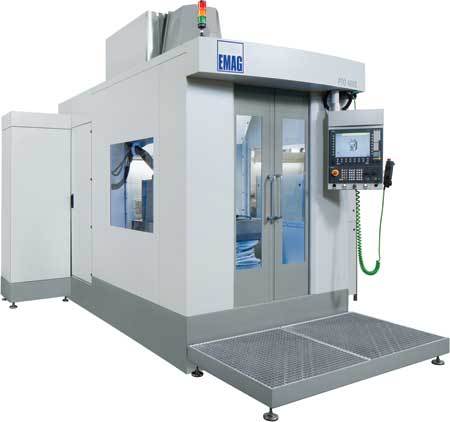
The EMAG PT is designed to guarantee maximal process integrity during multi-axis production.
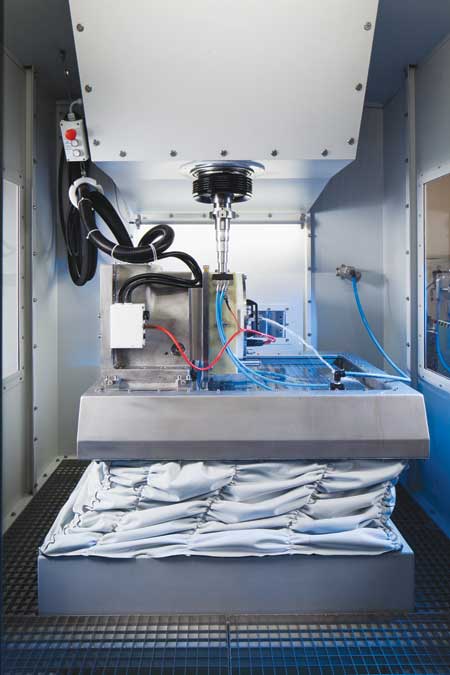
Machining area of the PT 4000: precise electrochemical machining of rotary components
EMAG has introduced its 4-axis precision electrochemical machining (PECM) PT machine. "This innovative, non-cutting answer to 3D challenges often presented in the medical industry offers a competitive advantage in the machining of demanding geometries," said a company spokesperson.
"The phrase 'Freedom of Design' describes a large number of production solutions offered by various industries and often means that installed machines are expected to produce all future component geometries required by innovation," continued the spokesperson. "This is significant in die and moldmaking, where it is an essential feature in the batch production of many products. Dies literally mirror the demanding designs of the end product. In toolmaking, 'Freedom of Design' means that a multitude of complex geometrical details must be machined into a piece of hardened, often high tensile material, often resulting in a time-consuming milling process. Thus, cycle times and tooling costs on multi-axis machining centers often rise dramatically. Process integrity is another factor of focus, as the smallest surface quality error can compromise the overall quality of the component."
According to the company, the PECM process is ideal for such tasks. During the electrochemical process, the material is removed without causing a heat affected zone and without the known negative effects of a cutting process. "There is also as good as no tool wear to contend with," said the spokesperson. "The non-contact machining process achieves top surface finishes, up to Ra 0.05 depending on the material." The process can also be employed to machine hardened materials, as the technology makes an anode of the workpiece and cathode of the tool. Between the two flows an electrolyte solution, which carries the charge that removes the metal ions from the workpiece.
New PT Series
PECM machines from EMAG are currently in use in the automotive, aerospace and energy industries. According to the company, PT machines offer the first multi-axis PECM machines with EMAG quality to ensure top metalworking performance in the manufacture of complex components. "With a total of four axes, the range of process applications has been enhanced considerably," said Jochen Laun, Managing Director, EMAG ECM GmbH. "Even demanding 3D structures can be machined."
The PT series is designed with the following features for process integrity and efficiency:
- PT machines rely on a machine base of the polymer concrete MINERALIT, which is built to guarantee precision kinematics and a vibration-resistant operation, both preconditions for precision machining.
- The contour of the tool cathode is tailor-made by EMAG to suit the job at hand. "The electrochemical machining process can be spread over a large surface, resulting in a naturally high degree of parallelization," said the spokesperson. "Even 3D geometries can be reproduced with great precision."
- The machining process employs axes Z (with 250 mm travel), X and Y (with 400 mm travel) and C (the rotary table with a 360° rotation). Where desired, machining can be interpolated and carried out in all axes simultaneously.
- The generator technology allows for the scaling of the processing current to a 20,000 A maximum and is tailored to suit the application.
- With filtration quality and consumption levels that can vary between 40 and 600 l/min, the electrolyte supply system can also be configured modularly.
- An ergonomic user interface, which includes graphic visualization, is designed to simplify operation and improve safety levels and transparency of the production process.
The machine is built to handle a large amount of parts with recurring contours with a diameter of up to 500 mm. "With the PT series it is possible to achieve rough machining feedrates of up to 5 mm/min," said the spokesperson. "This reduces to 0.1 to 0.2 mm/min for finish machining. The possibility to machine large surfaces of 20 to 30 components simultaneously makes this an economically viable proposition for medium and large component batches. Tolerances achieved in this kind of production can be under 20 um."
Component Sturdiness
For example, a customer's steel workpiece may require the inclusion of a large number of 3D contours, which are machined in an unattended process controlled by an automatic NC program that generates the necessary rotary and transitory movements. "The PT machine used has a fully fledged NC control and four axes," said the spokesperson. "It not only processes the workpiece with great efficiency, but it also emphasizes its advantage with the gentle machining of the material used. The PECM process does not heat the material and thus alter its microstructure. There will be no micro-fissures in the material that have a negative influence on component stability, as experienced when the erosion process is used. This is an important factor, especially when it comes to high-performance components.
"Some advantages of the new PT series from EMAG include multi-axis production of complex 3D geometries and a gentle, fast and precise process. The series can be employed by medium-sized sub-suppliers for various industries, in a general mechanical or medical engineering environment and in die making."
"Customers who have a requirement for recurrent precision 3D geometries will be able to gain in component quality and sink production costs," said Laun.
For more information contact:
Peter Loetzner
EMAG LLC
38800 Grand River Avenue
Farmington Hills, MI 48335
248-477-7440
info@usa.emag.com
www.emag.com
Southwest
AR
David Fitzgerald
EMAG LLC
248-595-1117
www.emag.com
TX, OK, LA
Ric Lorilla
EMAG LLC
248-595-1530
rlorilla@emag.com
Southeast
VA, NC, SC, GA, FL, TN, AL, MS
David Fitzgerald
EMAG LLC
248-595-1117
www.emag.com
Northeast
PA, NY
Kirk Stewart
EMAG LLC
248-996-4703
kstewart@emag.com
ME, NH, VT, MA, RI, CT, NJ, DE, MD
Jonathan Chomicz
EMAG LLC
248-497-8526
jchomicz@emag.com
WV
David Fitzgerald
EMAG LLC
248-595-1117
www.emag.com
Midwest
IN, MI, OH
Kirk Stewart
EMAG LLC
248-996-4703
kstewart@emag.com
ND, MN, WI, SD, NE, KS, IA, MO, IL
Tod Petrik
EMAG LLC
248-470-2646
tpetrik@emag.com
KY
David Fitzgerald
EMAG LLC
248-595-1117
www.emag.com
West
Peter Loetzner
248-477-7440
info@usa.emag.com
Arnie Sugiyama
Caltec International
19801 Hamilton Ave
Torrance, CA 90502
310-527-4110
arnie@caltecusa.com