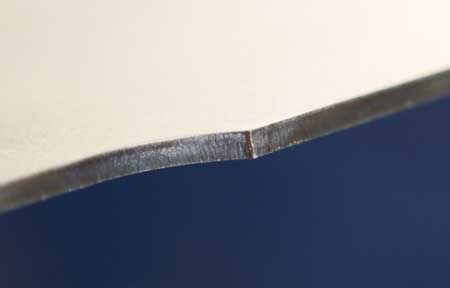
LaserCoil Technologies is now offering short-run production and prototyping coil-fed blanking services, producing clean-edge parts ready for additional laser welding or stamping processes without requiring reshearing.
LaserCoil Technologies LLC, specializing in technologies for laser cutting blanks from coil, is now providing pre-production, prototype and low volume production part runs at its technical headquarters in Perrsyburg, OH. The patented LaserCoil system can process up to 20,000 pieces/run from a variety of coil material including aluminum, mild steel, advanced high-strength steels (AHSS) and more, producing surface sensitive panels as well as structural components in thicknesses from 0.5 to 3.5 mm (0.02" - 0.14") and up to 1.9 m (75.00") wide coil at any length. Additionally, the system can achieve complex curvilinear shapes for near-immediate 'idea to net shape' components.
"We are experiencing especially high interest in coil-fed laser blanking of the new AHSS materials and aluminum," said Jay Finn, LaserCoil Chief Technical Officer. "We are also seeing high interest in AHSS and aluminum. We can achieve high yield rates and better quality than traditional stamping as our laser cutting process eliminates edge micro-fracturing problems that can lead to splits during the drawing of a blank."
The LaserCoil fiber laser and proprietary optics process achieves near-zero dross with a minimal heat-affected zone. "This provides consistent edge quality to deliver components that are laser welding-ready, eliminating the need for a reshearing process. This cleaner edge also leads to improved formability," said Finn.
"The flexibility of the LaserCoil system can also help companies facing potential die repair or late die delivery issues, as well as material shortages. Since there is no need for traditional press dies, set-up simply requires programming for the new component. This allows for the same part to be cut from a wide range of different coil widths. The company also offers feasibility studies on new components or prototype parts to help ensure that design, materials and processes are optimal for a given part," said Finn.
For more information contact:
Kim Beck, President
Jay Finn, LaserCoil Chief Technical Officer
LaserCoil Technologies LLC
7401 Ponderosa Road
Perryburg, OH 43551
419-591-7012
finnj@lasercoil.com
www.lasercoil.com